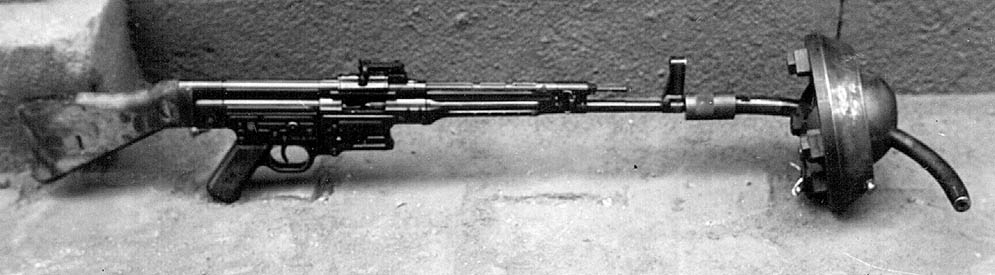
By Frank Iannamico
During World War II, the Germans came up with many innovative small arms and ancillary equipment. One piece of German ingenuity that captured the attention of the United Statesโ Ordnance Department was the Krummerlauf or โcurved barrelโ concept.
The earliest German development program for curved barrels was based on the need for an improved method of proof-firing machine gun mounts installed in aircraft. By diverting the projectile downward immediately after leaving the muzzle, the kinetic energy of the projectile was reduced; therefore the test range could be considerably shortened. In August 1941, Reinmetall-Borsig engineers at the German proving ground in Guben originated a high-angle firing device for machine guns, in which a curved barrel served as a diverting channel. This device was first considered as a โdivertingโ unit rather than a โdirectingโ device. As previously stated, the diverting action was required to upset and slow down the projectile for convenient test purposes on airfields with limited space.
Actual research to develop a curved barrel for combat purposes began in 1943 at the Unterluss Laboratory of Reinmetall-Borsig, with Dr. Herfurtner supervising. The first research in directed, rather than diverted projectiles began with trough or gutter barrels of half-round cross-section. The first unit was a 15-degree trough bent around a radius of 250 mm and fastened to a specially machined barrel mounted on a standard K98k German service rifle. This unit was attached as a rigid assembly to the barrel. Attachment of the device was accomplished by a three set-screw, spring-loaded clamp. Performance was considered satisfactory using standard 7.92x57mm rifle ammunition. The angle of direction, however, was considered too small to be effective. During the course of the experiments many unusual characteristics of both bullet and barrel troughs were observed. Among these was a thrusting effect caused by the rapid change in bullet direction. A major problem was the troughโs lack of rigidity, which caused excessive barrel whip. Since it was planned to proceed on to barrels with greater directing angles, no effort was made to correct these factors on the 15-degree device.
Later experiments were undertaken with an open sided 30-degree unit that had reinforcing ribs placed along the outer closed surface of the trough. The K98k rifle continued to be the basic weapon of the testing, and standard SS-type 7.92x57mm service ammunition remained as the projectile type. With the introduction of the reinforcing rib, the whipping of the barrel diminished. However, new difficulties soon arose. The fired projectiles had a tendency to skid, shred, split and yaw very badly. This condition led to the development of an all-steel, jacketed 7.92x57mm projectile with greater rigidity that reduced the possibility of shredding. The experimental steel ammunition gave improved results. However, further work with special ammunition was canceled when the General Staff would not consider the introduction of a new type of service ammunition for such a highly specialized purpose. As an alternative, work continued with standard mild-steel core S.m.K. ammunition. The problem of bullet shredding, splitting and yawing was never completely solved.
The trough barrel design continually failed to meet the designated 200-meter accuracy requirement. Work on the trough configuration was abandoned in favor of a closed-barrel design with a 30-degree deflection. The first โclosed tubeโ barrel was not rifled, the projectiles, however, continued to break apart and deform during firing. A new problem also emerged, after a few hundred rounds the projectiles would break through or seriously deform the curved portion of the barrel. Undeterred, the General Staff ordered research to continue.
Eventually it was discovered that rifling the curved barrel device proved to provide better performance. Finally, by producing a specially made, close-tolerance curved barrel extension with full-depth rifling, satisfactory results were achieved. There was no effort made to index the rifling of the curved barrel attachment to the host barrel. Testing had proven that matching the rifling of the barrel and curved extension did not affect accuracy.
As a consequence of good performance with the directing barrels and tubes on the 7.92x57mm bolt-action K98k rifle, engineers were encouraged to develop a device for weapons capable of automatic fire. Experimentation in this field was undertaken using the 7.92x57mm MG34 machine gun. Due to the high rate of fire of the MG34, the results were not satisfactory. The thrust resulting from the rapid and continued passage of projectiles through the curved barrel was so great, that the operating system of the weapon jammed continually. Deemed impractical, the curved barrel project for the MG34 was abandoned.
In 1943, the MP43 machine carbine and its new mid range 7.92x33mm Kurz cartridge was adopted into German Army service. By 1944, the weapon, with slight modifications was re-designated as the StG44. The midrange weapon was capable of both semiautomatic and full-automatic fire. With a less powerful cartridge, and at a lower cyclic rate of fire than the MG34, the MP43/StG44 was considered as an ideal host weapon for the curved barrel attachment. The Tank Corps originated a requirement for such a device to increase the close-in protection of combat vehicles against infantry attacks. This new requirement raised the need for a barrel with increased angular direction. Both a 60-degree and 75-degree barrel were ultimately developed, but the 90-degree was eventually selected as the most suitable angle for complete vehicle defense. Two distinct barrel types were eventually adopted, one with a 30-degree bend and another with a 90-degree curve. The 30-degree design designated as Versatz J was to be issued to infantrymen that were issued the StG44 weapon. Using the special prism rear sight giving 30 degrees visual deflection and the curved barrel the infantryman could fire his weapon from trenches or similar cover without exposing himself to hostile fire. The curved barrel attachment for the StG44 was 14 inches long. The barrel of the StG44 was 16.5 inches long. With the curved barrel attachment the total bullet travel was 29 inches. On the barrel attachment the first four inches were straight, the 30-degree curved section was 5.5 inches long and the muzzle section 4.5 inches in length. The curved extension was rifled similarly to the StG44โs barrel with four right-hand grooves. The extension was attached to the StG44โs barrel by means of a clamp. The curved extension with a rear diameter of 10 millimeters was coned to a depth of 9 millimeters; this was to permit the projectile to align itself when exiting the StG44โs barrel into the curved extension. No attempt was made to match the rifling of the host StG44โs barrel to the rifling in the barrel extension. The outside diameter of the StG44โs barrel was 14 mm while the Krummerlauf barrel had an outside diameter of 20 mm. At a point 58 millimeters from the breech of the attachment there were an inline series of five 4 mm holes drilled through the top of the barrel to relieve the propelling gas pressure, allowing the projectile to โcoastโ through the curved part of the barrel extension. (Note there were several variations of the pressure relief holes noted, including a design with an elongated slot). During U.S. testing of the 30-degree Krummerlauf device it was discovered that muzzle climb was accelerated when the exiting projectile changed direction in the barrel. The weapon was not however, uncomfortable to fire.
While being interrogated by U.S. Ordnance personnel after his capture, Colonel Hans Schaode claimed credit for the Krummerlauf โbent barrelโ concept. Colonel Schaode was an assistant to Dr. Speer in the research division of Rheinmetall-Borsig at Sommerada. Colonel Schaode said that he began experimenting with the bent barrel concept in the fall of 1943. A year later he received the official approval of the German high command. Rheinmetall-Borsig was given a contract for 20,000 units per month.
Original German projections of barrel life of the curved extension were 6,000 rounds. Colonel Schaode stated the muzzle velocity was increased by 10% when the curved barrel attachment was used. Both of the aforementioned German theories were disproved when the U.S. Ordnance Department tested the device at the Aberdeen Proving Ground.
The 90-degree Krummerlauf device was designed primarily for use with tanks to clear unauthorized โridersโ off of the vehicle. The 90-degree unit was designated as the Versatz P. There were two methods used for attaching the 90-degree device to the StG44 weapon. One method used was the clamp similar to the one used with the 30-degree Krummerlauf; the other method was special interrupted threads for fast attachment or removal of the weapon from the curved barrel. The barrel of the 90-degree Krummerlauf was slightly thicker than the 30-degree model with an outside diameter of 25 millimeters. The barrel was 18.75 inches long, and except for a 1.625-inch section for attachment to the adapter, the entire barrel was curved. The device was rigidly mounted in a tank or vehicle by a special ball and cup mount. The ball freely floated in the cup, and had two eccentric holes in it. One hole was for the curved barrel that was pinned and bolted into place, the other hole was for the periscope sight making it parallel to the axis of the weaponโs bore. The mirror-prism sights reportedly designed by Bush-Rathenow were to be manufactured by Zeiss. During 1945 the first units were completed, the scope had 1.5 magnification and 12-degree field of vision.
The U.S testing of an StG44 weapon fitted with the 90-degree barrel extension revealed that the weapon was very difficult to control. When the host weapon was manually held horizontally the barrel was pointed to the right. The test weapon was fired in both full-automatic and semiautomatic modes of fire. When the fired projectile entered the curve of the barrel a violent reaction occurred in the opposite direction. The combination of recoil and torque of the projectile made control of the weapon impossible. Several attempts by a number of shooters failed to hold the weapon rigidly while firing from the hip. When attempting automatic fire, the shooter would be spun almost 90 degrees after only three rounds.
Firing projectiles into sawdust had shown that many of the projectiles were twisted into two pieces. Those projectiles that remained intact, keyholed when striking a target placed 8 inches from the muzzle. When fired at a dirt bank at a distance of 50 yards single shots would produce two to three strikes six to twenty feet apart from disintegrating projectiles.
Examination of the German 90-degree barrel after firing 150 rounds showed no distortion at the curved part of the barrel, but there was damage to the rifling. The throat of the curved barrel was torn and stretched. The throat damage was caused by the bullet leaving the host barrel. This was believed to have been caused by the excessive weight of the barrel extension causing abnormal barrel vibrations resulting in momentary bending of the host barrel.
The U.S. Ordnance Department testing also concluded that the German 30-degree curved barrel concept using the 7.92x33mm Kurz cartridge was practical, but the 90-degree barrel was not. While being interrogated after the war Colonel Schaode revealed that Rheinmetall had conducted experiments with curved barrels in various calibers up to 75 millimeters.
German Major Hertmann who was formally with the German Ministry of Armament, Division of Infantry Units, was also interrogated. Major Hertmann was supervising small arms development in Berlin, Kummersdorff, and the proving ground at Hillersleben. The Major stated that the curved barrel had proven successful. The 30-degree barrel was for issue to foot soldiers while the 90-degree model was to be fitted into a ball-socket joint to protect tanks from attack by enemy infantry.
The U.S. Ordnance engineers who evaluated the various German barrel devices concluded that the idea of a curved barrel was worthy of further research and development. They felt that the low velocity U.S. .45 caliber cartridge with its large bearing surface would be well suited for such a device. Several U.S. designs emerged for the U.S. M3 .45 ACP caliber submachine gun.
This article first appeared in Small Arms Review V6N10 (July 2003) |