By George E. Kontis, PE
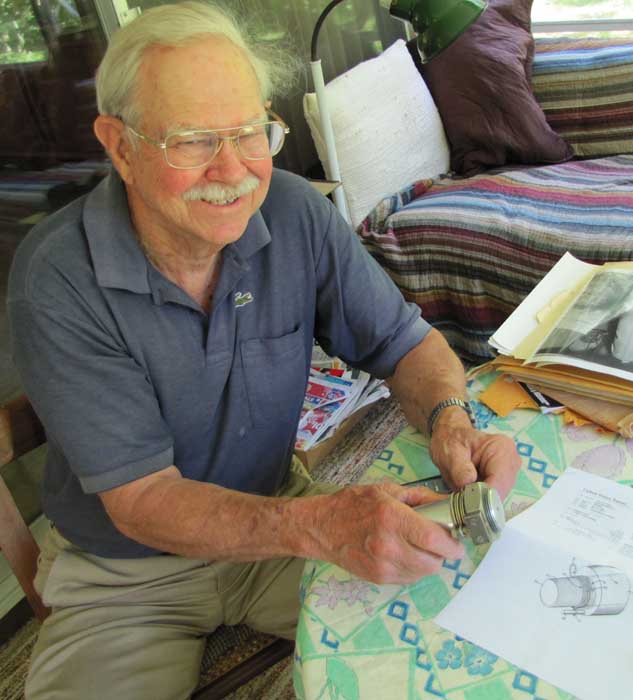
During the 60s, 70s, and 80s, the General Electric Armament Systems department employed several hundred top notch engineers charged with the development of Gatling guns, single barrel cannons, and both linked and linkless ammunition handling systems. These highly effective and reliable weapons were widely acclaimed during the Vietnam War, Gulf War, and conflicts in between. GE was never a company to single out any of their employees as a standout in the field, yet a select few of their engineers had talents to rival John M Browning. Lewis K. (Lew) Wetzel was one of those engineers. His first project at GE was to put the M61 Gatling gun into production, and from that point on, was a major contributor to nearly all of GE’s gun and feed system designs.
Lew used what might be considered as 360° thinking in his designs, considering every aspect including accuracy, durability, production, reliability, maintainability, and quality. His designs controlled the round, fired case, link (if there was one), at all times in the weapon cycle. This discipline and through minimizing the number of components, propelled the reliability of the GE systems far above what John Browning ever achieved, and maybe even envisioned. Lew kept a careful eye on his design teams, insisting that if they were to use threaded fasteners (bolts) or pins, he would allow them to select two of each – one long, one short, to be used in the design. As neither was of the same diameter, there was no guessing for the maintainer and spares were minimized. Later in his career Lew developed a 30mm cannon that required no threaded fasteners at all.
We ended Part I of the interview with George asking if the 25mm Caseless Gatling cannon design project was the one to be used on the F15 fighter jet.
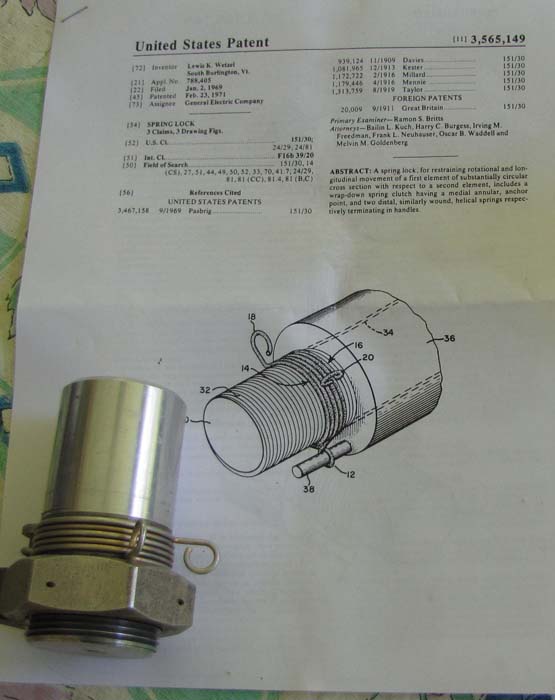
Lew: That’s right. We set up a separate unit that I headed up.
There were two 25mm caseless guns in competition. Ford Aerospace and GE had parallel contracts, and each of us used different ammo contractors. We farmed out the ammo to Hercules and had a shoot off. We both had problems. You know that ammo is uncased and it can just go up in flames. They had a special water deluge system to douse the fires. I know both GE and Ford had fires. We might have had one more than Ford, but in the end, the Air Force decided Ford was the winner.
During final negotiations, the Air Force decided the contractors should respond with a Firm Fixed Price contract with guaranteed performance. You know, this is kind of dumb for a high risk program. Not only was it risky, but they tried to get me to agree to their technical requirements too. I said, “These requirements are mutually exclusive. We can’t meet the recoil requirements and at the same time use the energy to drive the gun. You have to back up the recoil with something!” In the end, I priced it accordingly and Ford won. Ford ended up investing about $20 million of their own money and finally the program was cancelled. You know that’s really sad because caseless is still a good idea.
George: We’re still trying to get into case telescoped and caseless. AAI’s new machine gun works just like our old 25mm.
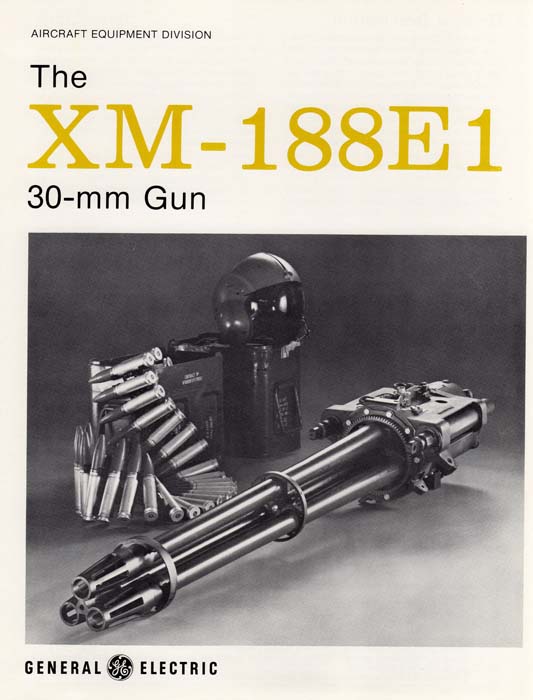
Lew: Well of course, how else are you going to do it? You know the real problem was that if you have a misfire you have to eject it. It might just be a hangfire and that gets really hairy. They had some interesting concepts on coating the round – like using intubescent paint as a fire retardant. This gun system was going to be the primary armament of the F15. The whole system could be jettisoned so in case you had a fire you’d push a button and the whole thing would eject. It was part of the original design.
After the caseless program was lost, I designed the XM188 30mm cannon. It used the WECOM 30mm round designed by the Army. My proudest accomplishment was that you could disassemble the whole gun with your bare hands. I remember going into the Pentagon one time to give a presentation. Dick Bruce was the marketing manager at the time. He and I drove up with the gun in our trunk and parked at the bottom of the stairway at one of the entrances. The gun had a belt of dummy ammunition hanging out of it. We found a guy with a push cart and we asked him if he’d mind taking the gun up to the conference room on the fourth floor. He said, “Sure. I’ll do that for you.” You know, the guy took us right past Robert McNamara’s office (who was then Secretary of Defense,) with what was obviously a gun – no IDs, no badges, no nothing! I got into conference room and told the general I was surprised at the lack of security here. We walked right in with a gun and nobody challenged us. He answered, “We are our own worst enemy. If anybody ever tried to attack us, only then would we get organized.”
George: Lew, you and I worked on the XM188 together. I designed an adjustable gas deflector that was supposed to improve accuracy. I remember that really neat spring you designed that required no tools to disassemble the recoil adapters. Remember it? It was a spring that two ends you squeezed with your thumb and forefinger.
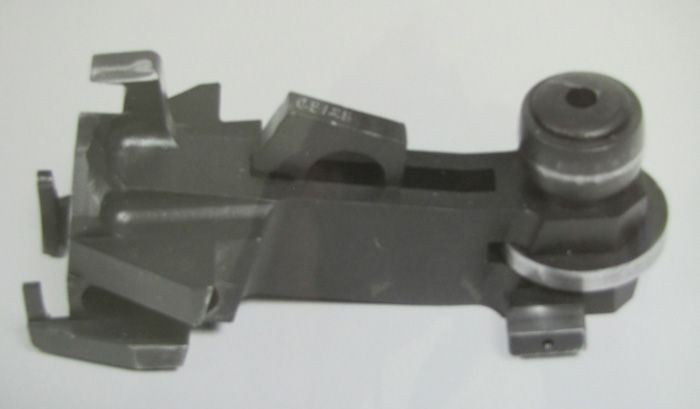
Lew: You want to see it? I have the prototype.
(Lew disappears and returns momentarily with the prototype. A spring wound in opposite directions wraps around threads on a shaft, preventing rotation of the shaft in either direction. Lew brings out the patent too.)
George: I remember you always said to make a simple prototype and then keep refining and refining it until all the bugs are worked out?
Lew: Yeah, I remember that. I keep this stuff handy to remind me I did some simple things. It’s pretty slick. After I left the XM188 gun program, they turned it over to the Production Engineering group. The first thing they did was to take off all of the no tools features.
George: I’ll get a photo of you and with the patent too.
Lew: Nobody will recognize me without glasses. I don’t need them anymore, but I’m so use to wearing safety glasses, having worn them my whole life, I appreciate how important they are. Oh yeah, there was another project we worked on together; putting our single barrel GE120 single barrel cannon into the Marine Corps’ LVTP-7 amphibious tracked vehicle.
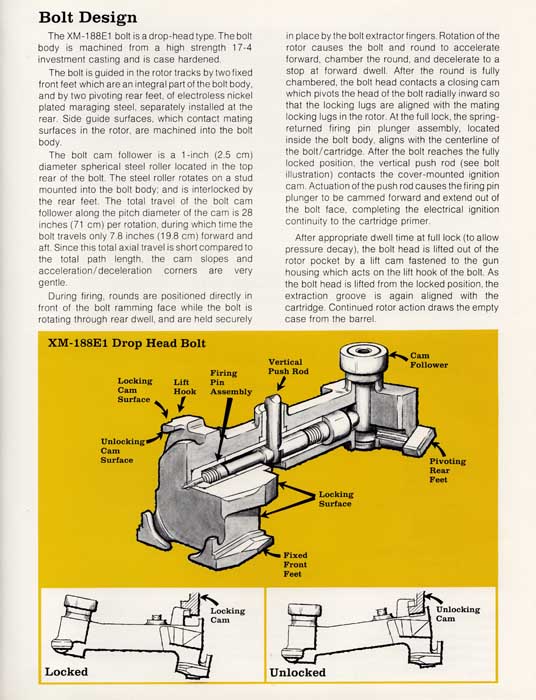
George: We had some problems with that one. We had some technical problems and I couldn’t figure out what went wrong. You figured it out and saved my butt. I love to tell the story about the FMC turret technician who was about to check the electrical continuity of an electrically primed 20mm round that had misfired. He was going to use an ohm meter. He was getting ready to touch the primer with one of the ohm meter probes (which would have sent a low voltage current through the round) when you stopped him.
Lew: Yeah, I knocked it out of his hand. It saved his life. He was holding it right in his crotch too. I took the round away from him and chambered it back in the gun. I said, “If you want to test it, let’s do it while it’s in the gun.” I connected his ohm meter to the firing circuit to test it – and it fired! His face turned absolutely white, and you should have seen the faces on all of the Marines! (Lew brings out a picture of him standing next to the LVTP-7 with a bent barrel.” I can’t imagine what happened to the gun barrel in that picture.
George: After that, I recall we worked together on the 30mm GPU 5/A gun pod, but I don’t recall how that project got started.
Lew: After the 25mm caseless program, I worked on a few small jobs but I didn’t have a major program. Management decided they’d give me an Independent Research and Development Project to get me back to work. You remember those? We’d come up with advanced concepts and Corporate would fund the ones they thought had the best chance for adoption.
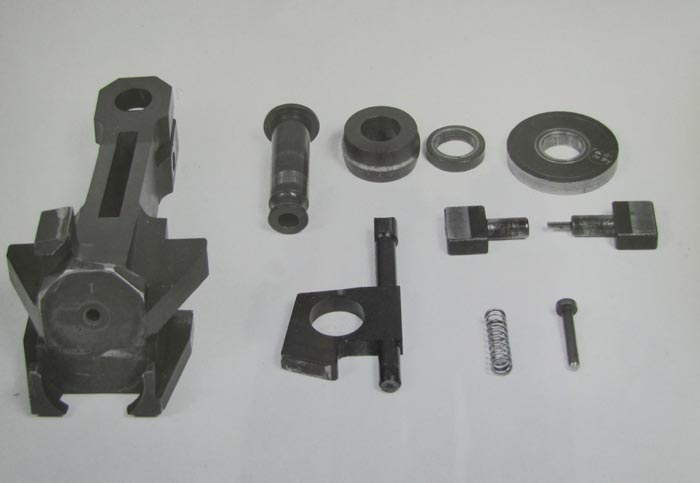
GE had already scored high marks for the design of the A10 gun system that involved a whole new airplane build around the 30mm GAU-8 guns system. It was a very effective system, and I got to thinking it would be a good idea to give this same armament capability to a lot of other jet aircraft. I started fooling around with the idea and came up with the feed system concept. I built a simple prototype of it, and it kept growing from there.
One of the most significant things in the design of the Pod was the muzzle blast deflector. The way the gun is mounted, recoil tends to make it deflect downwards during firing. But with the blast deflector it completely counteracted the downward force. The pod was super accurate as a result. A lot pilots who fired the pod told me they were very surprised at how accurate it was. The last blast deflector was probably not patented, but it should have been.
George: You know, there are two slots left un-machined on the M16 rifle flash suppressor that do the same thing – in this case it’s controlling muzzle climb.
Lew: That’s probably why we didn’t succeed in getting a patent for it. I remember you designed the feeder, remind me what other parts you designed?
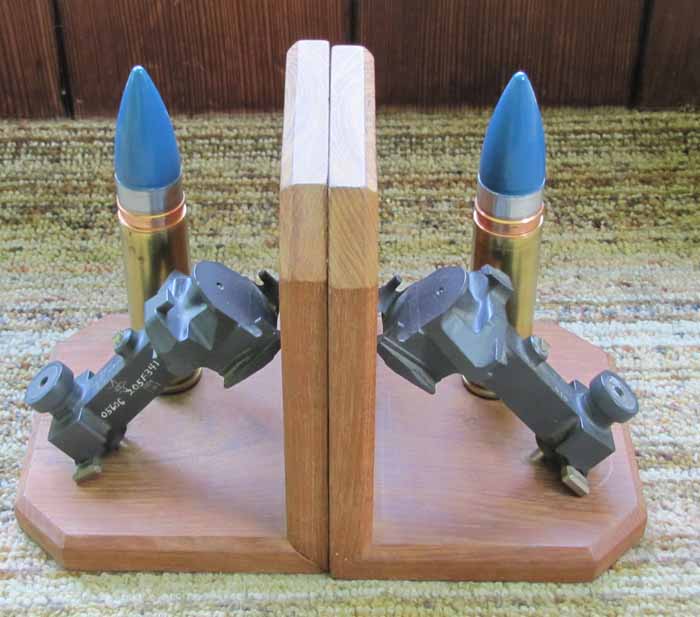
George: I also designed the turnaround sprockets – there were about five of them that kept the conveyor buckets transporting the ammunition. I also designed the recoil adapters and got a patent on that design. I made the first feed system prototype that we test fired. I worked with a talented designer named Woody Evans and the designer you worked with was Ed Proulx. I learned from you how important it is to test increasingly more complex prototypes. When these were tested out and de-bugged, there were few, if any, major problems left.
Lew: There was one more thing that really made the Pod program work. When we were putting our project plans together in order to get corporate approval, I remember I asked for $1.5 million to finish the design. Then I put an Appendix on the Program Plan. This was a cost breakdown to complete the prototypes, and that would take another year and $6 million. Upper management was mad at me. None of the other engineers were giving out the follow-on cost information, and I wasn’t supposed to either.
I told them, “When I submit a project to corporate; I want them to know the whole story. No surprise for later.” So, I refused to take it out. Wouldn’t you know it, the whole program was funded! Corporate locked the program in, so it was guaranteed for completion. This also enabled us to make long-term commitments to Northrup and General Dynamics and we were able to flight test it on the F5.
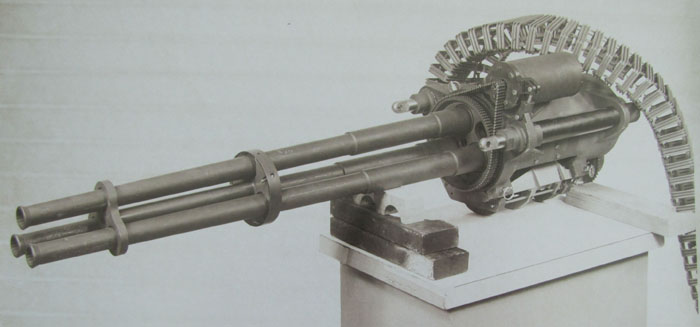
George: I always thought that was clever when you decided to power the whole pod off of compressed air.
Lew: Sure, they always have air compressors at Air Force bases. You don’t need anything special for a compressor. The other neat thing was a built-in test. This was long before they had built-in testing for anything. During the development, our instrumentation group designed a fault code that would let you know where the problem was if anything had gone wrong. And I said “This would be handy to have on the production model” so they did it so the whole test unit could interrogate. They do this now in automobiles, but remember this was 40 years ago. By the way, did you get involved in any of the flight testing?
George: No, by then I had taken over as project engineer on the 7.62mm Armor Machine Gun.
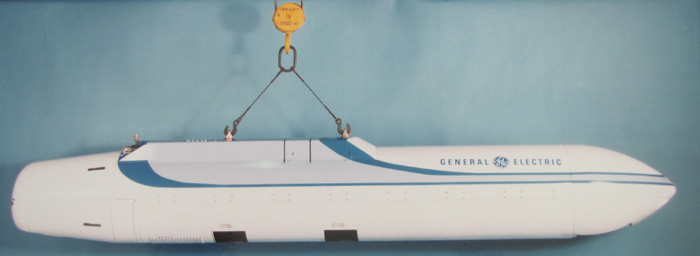
Lew: Well, you missed some fun. We had it on the A7 and the F5. One of our young engineers, Charlie Hillman, went over to Korea for the F5 testing. Pilots really liked it. I’m sure the blast deflector played a major part. Everybody was happy and we got the production contract. Strangely enough, the production contract was through the National Guard. They did all of the testing. I remember we went out to Tucson, Arizona and did some firing out there. It scared the hell out of me when I was leaving. As we were leaving the Tucson airport, I recognized the bunker we were firing in to. It was right next to the main runway! What if you got a stray round or ricochet?
George: How many 30mm gun pods were built?
Lew: Hundreds of them went into production. We got the production contract in 1980 and they had a big party out there in Colchester. I was sure our Foreign Military Sales of the Pod would be big. I wanted to make sure that the pod would fit on the French Mirage jet. That’s what the Egyptians were flying and they were on our side. We wanted to make sure our pods were compatible. There was plenty of clearance for the pod, all we had to do was to make a special electrical cable – the bomb racks were already compatible. Our marketing just didn’t push it hard enough. We missed this one and a lot of other marketing opportunities.
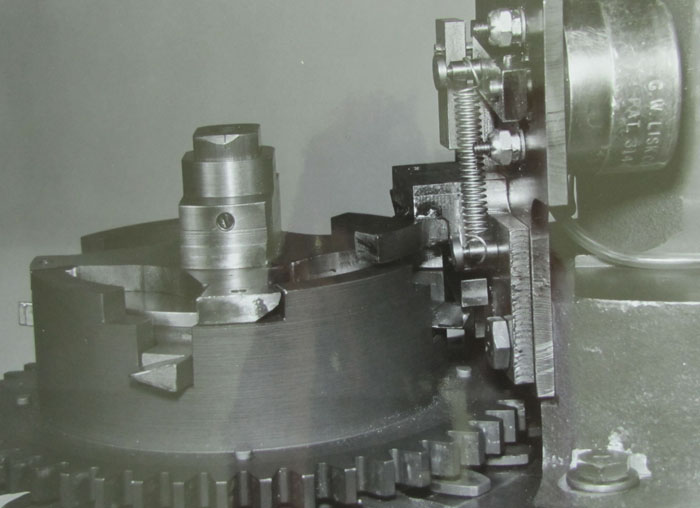
We got the production contract $275 million worth of contracts. We made a good profit on the pods because our contracts people had negotiated a lot of incentive fees. These were for weight, mean time to repair, reliability, on time delivery, etc. We met all the goals and got the maximum incentive fee. It all added up. Our manufacturing department did a fantastic job of building it.
The next project that my engineering unit developed was a .50 caliber Gatling gun. Quent Sawyer was the project engineer.
George: I remember it. I started the concept and got the money allocated for it. The idea was to size it for a 6 barrel gun but we’d do it first in 3 barrels. They assigned me a designer to work with and we were scheduled to start it in the fall of 1981. That’s when I left to go to work for FN and Quent Sawyer ended up designing it.
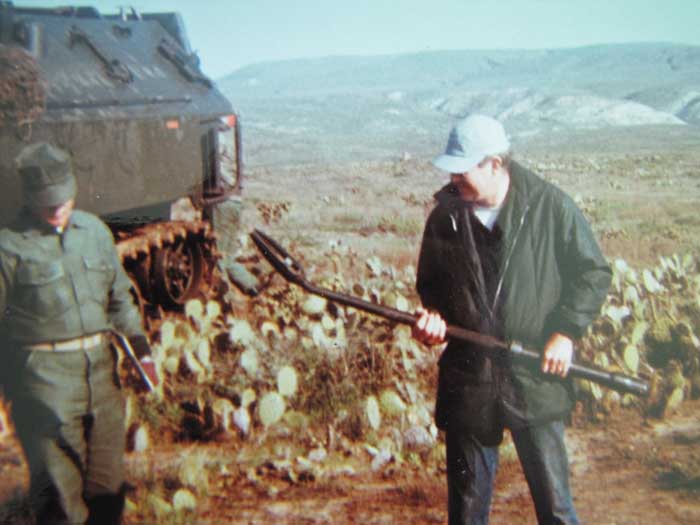
Lew: That gun had some pretty rough political problems. We got the prototype working and it was fantastic. We had it set up on a pintle mount and we got word that after all our testing we were still trying to find a place for it in the military. We were in negotiation with the Air Force to get it on the V-22 Osprey. We heard the commandant of the USMC would be in Burlington, Vermont and would be in after the commencement exercise at Norwich University. We invited him for a firing demo so I said, “We’re going to demonstrate it and let’s let him shoot it.” I had it all arranged – even the offer to let him fire it. All of a sudden, they decided not to let me go. “No, they said, we have to keep the number of people down to a minimum.” So I wasn’t there. Then came the edict that we were not going to let the general shoot. My technician was told not to let the General shoot under any circumstances. After the technician fired a few bursts, the General went up to him and asked: “Do you need any help with it?” The technician said he was tempted to let him shoot it anyway. But he didn’t. He was told they were worried about the General’s safety.
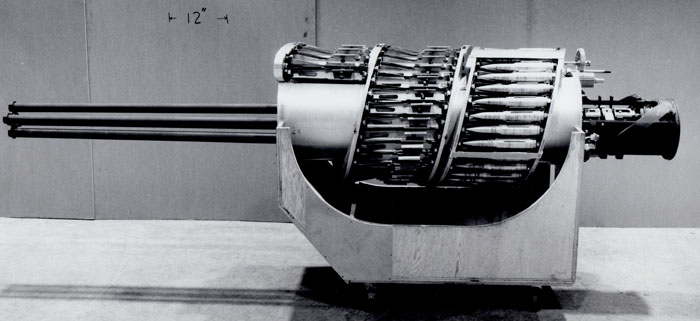
I said, “What the heck! There is no safety problem. Heck, I wouldn’t let my technician fire it if there was any danger. So guess where the General went? The next week he attended the rollout ceremony for the new V-22 Osprey. He’d have probably would have said he wanted that gun on the Osprey. Just about the time I was leaving they wanted to sell a license to Royal Ordnance. They were all set to buy the license but Royal Ordnance closed its doors.
George: What was your position at that time?
Lew: I was manager of Advanced Weapons Engineering. The pod was split off into a separate unit. Newt Garland had managed that group, and when he retired, I took over. We were getting into liquid propellant, and I was also responsible for barrel development. Dave Perrin was the main barrel guy; He did some real pioneering barrel work before they closed down the barrel shop. I retired in 1988.

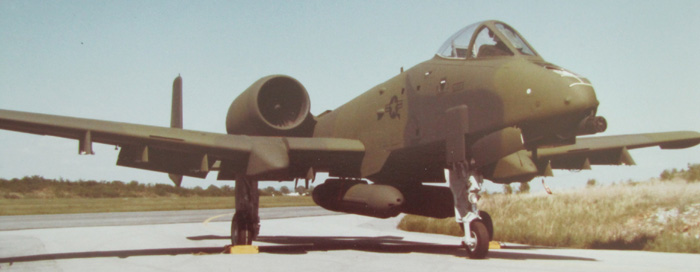
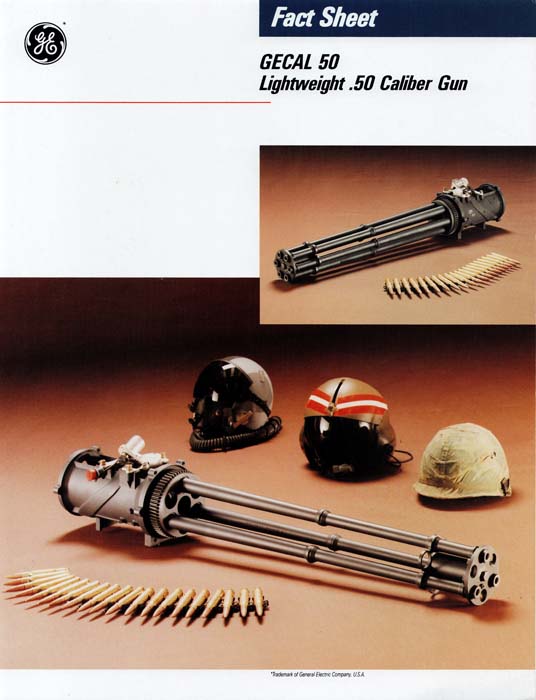
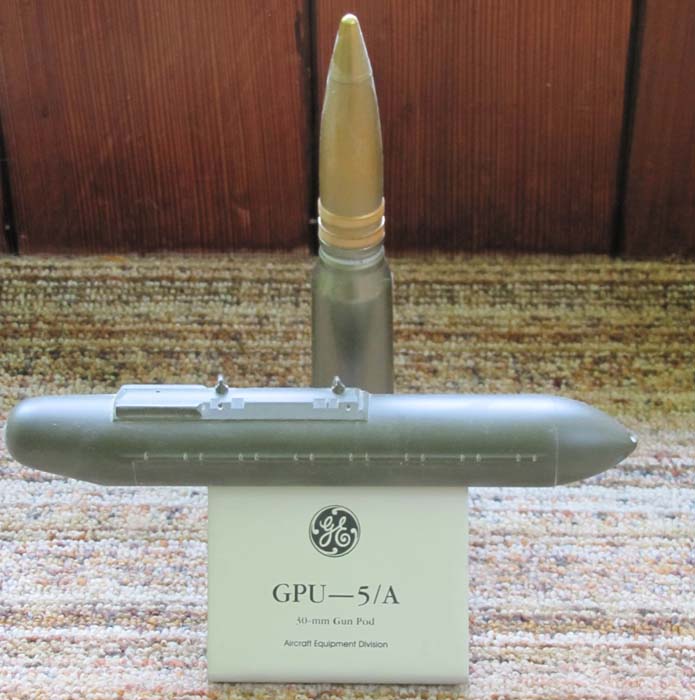
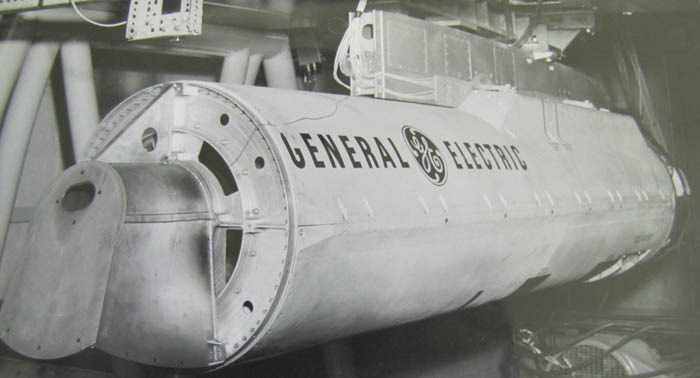
This article first appeared in Small Arms Review V16N3 (September 2012) |