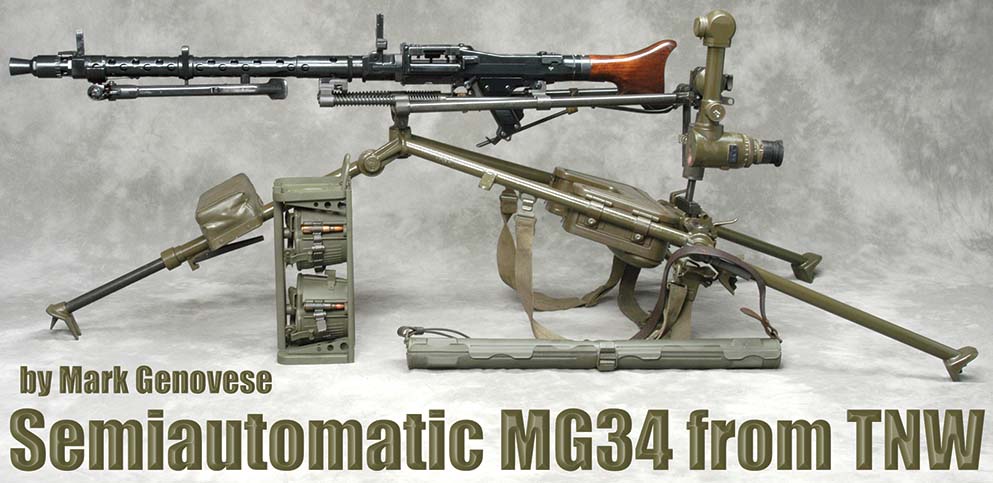
By Mark Genovese
The MG34 German universal machine gun would emerge from the ashes of World War II to stand proudly in the annals of historical firearms. Its superb craftsmanship, technological brilliance and manufactured competence would become the light saber of the National Socialist juggernaut. The universal machine gun concept would be unique in its day, in that it would have to fulfill a difficult three fold task: heavy machine gun, light machine gun and in the anti-aircraft role. Further refinements demanded of the MG34 by the Reichsministerium would be simple operation, quick change barrel, light weight, selective fire and high and low cyclic rates, to name just a few. All this development and manufacture was accomplished in secrecy to avoid the restrictions of the treaties of Versailles signed after World War I. When one considers the heavy water-cooled Maxim and Schwarzlose machine guns the Wehrmacht had within its arsenal prior to the adoption of the MG34, 26 pounds would seem exceedingly light. Field stripping the MG34, with its then modern bayonet style catches, compared to the Maxim or Schwarzlose method, was far simpler for the machine gunner and his crew. Barrel change, a necessity after 250 rounds of rapid fire is exceedingly easy as well by first locking back the bolt, pressing in the receiver latch, swinging away the receiver with the muzzle somewhat lifted so the free barrel slides out and to the rear. The select fire trigger is complicated mechanically but a pleasure for the gunner. The upper part of the trigger when pulled will fire semiautomatic while the lower part of the trigger will fire fully automatic. The complex adjustable cyclic rate (600 rpm or 1000 rpm) selector incorporated into the pistol grip was discontinued early on because the troops preferred the high rate of fire. It appears aside from the standard issue MG34, two others were fielded: the MG34 tanker with its Panzermantle heavy barrel jacket made from hardened steel and few vent holes to protect it from infantry fire plus shrapnel, and the mysterious and rare MG34/41. Louis Stange, the inventor of the MG34, continued throughout the war years to improve and increase the rate of fire for his 34/41 “schnell” or “fast” machine gun. Herr Stange was able to achieve 1,200 rpm with a shorter barrel, bigger muzzle area, smaller booster hole and a more powerful recoil spring to name just a few of the changes. The light machine gun or heavy machine gun role was not determined by an internal change of caliber or parts but rather a peripheral change in the way the weapon was/is fired from its mount. In the light machine gun single soldier role, the attached bipod would be appropriate to engage static and/or moving targets at relatively close ranges. One will encounter two types of bipods. On the early MG34, the MG13 type bipod can be found with its simpler manufacture and unfortunate ability to spin freely around its attachment point, and the later standard reinforced type with its superior height adjustment screw. It was in the heavy machine gun role that the Heereswaffenamt (Army Ordnance Office) made its most profound and remarkable advancements; specifically the MG Lafette 34 machine gun soft mount and its phenomenal optical sight. The first reciprocating spring mount to attract the attention of the Ordnance Office was the Danish Madsen mount in early 1930.
The theory of having a spring absorbing mount system as opposed to weight alone to steady the weapon was very attractive to the Wehrmacht and their concept of the universal machine gun. The issue of searching fire was addressed with a unique elaborate mechanical device. When on, as the weapon recoiled, it would index up and down automatically. This mount was capable of anti-aircraft fire as well with its issued extension tube. The commercially made MG Z optical sights were complex, extremely robust in manufacture used for direct or indirect fire and could engage their targets from up to 2½ miles away, an astronomical feat in the 1930’s. The MG34 was used extensively in the Westwall and the Siegfried line fortress system of armored pillboxes used by the Wehrmacht to defend German interests.
Specifications of the MG34 are: weapon length – 48 inches; barrel length – 24 inches; caliber – 7.92mm; weight – 26 pounds; barrel weight – 4-1/2 pounds; ammunition can with 300 rounds – 22 pounds. Basic field stripping is straight forward and simple. Open the top cover, push the cover hinge pin from the right and lift off the cover. The spring held feed block may be lifted off as well. The butt catch is on the underside of the butt itself. Press the catch in and a quarter turning the buttstock right or left frees it from the receiver. With the bolt in the forward position and just behind the pistol grip mounted to the bottom of the receiver is the buffer latch. Push it in and twist the buffer right or left a quarter turn to remove the recoil spring. Carefully pull the cocking handle rearward to free the bolt through the rear of the receiver. Press the latch on the left side of the barrel jacket trunion, swivel the receiver down, tip the jacket up and allow the barrel to slide back and out. Push the button on the right bottom of the trunion, twist and pull to free the barrel jacket from the receiver. Lift the catch in front of the foresight to unscrew the flash hider/recoil cone. The trigger assembly is secured to the receiver with two split pins and removal is not recommended. Before the end of World War II, 450,000 MG34’s were produced by five firms; Berliner Suhler Waffen, Steyr Daimler Puch, Waffenwerke Brunn, Mauser Werke and Rheinmetall.
THE TNW SEMIAUTOMATIC CONVERSION
It is generally regarded that the reason a semiautomatic MG34 was not attempted in the past was for the same reasons Savage Arms, back in 1943 after a thorough examination, found the weapon would require the use of considerable numbers of machine tools and highly skilled personnel to manufacture just the 109 parts made directly from bar stock. This monumental semiautomatic project would require a person or persons with a sincere heartfelt love for this historic firearm, endless patience, phenomenal skill, an extremely well equipped machine shop, time and no financial challenges. Mr. Tim Bero and Mr. Lance Witham of TNW Firearms Inc. decided to take the project on. The receiver, starting life at forty pounds of carbon steel, would require over three hundred machining steps alone and several years to develop and manufacture the specialized broaching tools necessary for the 11-1/2 inch long bolt and cocking channels deep within the receiver. The only difference between the TNW semiautomatic receiver and the fully automatic receiver is the interior cavity has been machined with no channel for the sear lug found on the standard MG34 machine gun bolt; consequently one cannot be introduced per BATF regulations. The opening machined in the bottom of the receiver is designed to permit only the installation of the unique TNW spring loaded, pivoting, disconnecting semiautomatic sear and in no way can an original fully automatic sear be substituted. If one were to try, the grip assembly containing the selective fire sear assembly cannot be physically attached to the receiver. For them to successfully assemble an original sixty five year old barrel jacket and its trunion to the new receiver and have the closest tolerance and lock up possible, the new receiver is manufactured without the 2 inch long by 3/4 inch OD interrupted thread stud that locks the barrel jacket to the receiver. They first cut the original stud free from the front quarter of the demilled fully automatic receiver, then chucks it in a lathe and turns it to the proper outside diameter. Next, a corresponding hole is centered and milled in the receiver to accept a press fit of the turned down stud. The barrel jacket/trunion is fitted to the new receiver and stud, held in place by a special jig as tightly as possible, then welded. The remaining hole is filled and the outside surface machined smooth. From the front of the demilled receiver, the upper and lower unlocking cams, made of CrNi alloyed steel and surface hardened, must have their four rivets carefully milled away to allow for their removal and reinstallation within the new semiautomatic receiver. The extremely difficult part of this operation is not installing the new rivets, but machining flush the remaining stepped upper rivet heads within the receiver itself. This very time consuming, methodical and systematic assembly is the only acceptable method for this historical precision-made firearm. The original MG34 bolt has been redesigned to fire from the BATF mandated closed position by eliminating the sear lug. The firing lever located on the bolt head has been removed as well and its space hard fusion welded over and its release cam surface used to trip the firing lever located on the bolt carrier has been milled completely away. The rear underside of the bolt carrier has been machined to accommodate the newly designed spring loaded firing lever, which slides over the original rear part of the firing pin. The firing pin retaining nut and rear part of the bolt carrier has had a corresponding amount of material removed to allow for the new firing lever.
This lever contacts the new firing pin retainer designed to hold the striker and its new extremely stiff flat wound return spring in the cocked position. When the trigger is pulled rearward a new roller cam within the grip interfaces with the progressively angled bottom surface of the new pivoting sear located in the lower receiver. As the sear rises and makes contact with the new firing lever, it pivots off its firing pin retainer releasing the cocked striker allowing primer ignition. As the bolt recoils rearward the pivoting sear is forced to rotate to the rear and thus acts as a positive semiautomatic disconnector. The hard trigger pull of this weapon is a direct result of the necessarily stiff flat-wound firing pin spring. This challenge can be overcome by polishing all corresponding trigger parts to a mirror smooth finish and after one thousand rounds fired, reduced the initial pull by about thirty per cent. This situation can be eliminated completely with the purchase of the inexpensive and readily available MG3 Bundeswehr tripod with its remote trigger linkage that converts the trigger pull to a compound mechanical leverage push. It is easily installed with just a screwdriver adapter available through TNW.
I considered this project for quite a while but it did not become a reality until Mr. Mike Remo of Anzio Iron Works Corp. returned from Europe with a handful of reasonably priced, matching serial numbered, excellent condition DOT 1944 Waffenwerk Brunn AG, Werk Brunn part kits. Coincidentally, Tim Bero was for the first time offering his semiautomatic MG34 as a receiver in kit form. This allowed me to request a specific serial number thus fulfilling my long sought after desire for an authentic World War II matching German MG34. While waiting for TNW to make and number my receiver, I had plenty of time to gather the necessary peripheral accoutrements for this project. My old friend Dave Michels of Sarco Inc. provided brand new unnumbered chrome lined barrels and their proper carriers, original ammunition cans with five belts and one starter tab each, two Gurttrommel 34 (belt drums) and their Gurttrommeltrager (carrying frame), an outstanding example of the four tin set Petroleumskasten (kerosene and oil) used to hold liquids for cleaning and maintenance of the MG34 and all 1944 dated to match the weapon. The good folks over at Allegheny Arsenal, Inc supplied me with an extra bolt that was reconfigured to semiautomatic as a spare, a Gurtfuller 34 (belt filling machine) and many other small parts. Test firing was at Ukumehame Range on the Lahaina (translates to “unforgiving sun”) side of the beautiful island of Maui. The MG3 Bundeswehr Feldlafette MG tripod with its outstanding Hensoldt Wetzlar periscope were used throughout the test. Five hundred rounds of 1955 dated Czechoslovakian ammunition, with its notorious deep set rock hard primers, and five hundred rounds of the fantastic and inexpensive steel cased 1972 dated Romanian ammunition were fired at 24 inch square steel targets from 235 yards away. After sand bagging the mount and the initial sighting in, all one thousand rounds impacted center target a spot the size of a silver dollar, with no failure to feed or failure to eject. With cleaning, proper maintenance and liberal use of the TNW recommended TW25B high temperature synthetic lubricant protectant, sold through Mil-Comm (reviewed in SAR September 2004, Vol.7, No.12, page 92 by Timothy Kast); this phenomenal semiautomatic conversion will deliver years of trouble free range time.
Contacts:
TNW Firearms, Inc.
P.O. Box 311
Veronia, OR 97664
(503) 429-5001
Mr. Tim Bero and Mr. Lance Witham
Anzio Iron Works Corp.
1905 16th Street North
St. PetersburFL 33704
(727) 895-2019
Mr. Mike Remo
Sarco Inc.
P.O. Box 98
Stirling, NJ 07980
(908) 647-3800
Mr. Dave Michels
Allegheny Arsenal, Inc.
Box 161
Custer City, PA 16725
(814) 362-2642
Mr. Greg Souchik
Mil-Comm
2 Carlton Ave.
East Rutherford, NJ 07073
(888) 947-3273
This article first appeared in Small Arms Review V8N8 (May 2005) |