By Christopher R. Bartocci
For more than 40 years now, M16 series firearms have been the American military’s weapon of choice. It is fair to say that few small arms have created such a history of controversy, which still persists to this day. What actually happened early in the Vietnam War forms the basis of ongoing misinformation and misconceptions about the M16 & M16A1 rifles. These weapons unfairly “earned” a reputation for malfunctioning when they were “dirty” and for being a lightweight piece of junk to many. The truth, however, is much more complex than the standard line that the gun did not work due to fouling. The M16’s initial reliability issues should not have fallen on the Black Rifle itself, but on the U.S. Army Ordnance Corps which was ultimately responsible for developing and fielding weapons used by U.S. soldiers.

The new lightweight rifle was adopted in 1964 based on its “superior performance” over the heavier M14 with its 7.62x51mm NATO cartridge designed for longer range engagements. The M16 was seen by many, including Special Forces advisors, as a good infantry weapon “nearly perfect” for combat conditions in Vietnam. With a larger “basic load of ammunition,” these small caliber, lightweight, low recoil weapons proved ideal for rapid multiple target engagements and close quarter fighting often encountered in Southeast Asia. Without digging into the early history of the U.S Air Force AR-15’s & M16’s, we will look at what went wrong “in the jungles of Vietnam.”

Soon after the new black rifles were deployed into ground combat with front line Army and Marine units, reports of significant malfunctions began to circulate across Vietnam and back to the States. Many of these problems stemmed from U.S. Ordnance Corps’ defiance, prejudices and outright negligence, which proved serious enough by 1967 to warrant a Special Subcommittee on the M16 Rifle Program in the U.S. House of Representatives. These proceedings within the Armed Services Committee are now known as the Ichord Hearings, after the chairman, Rep. Richard Ichord. The details of the entire M16 program brought out during these hearings showed incredible mismanagement and gross negligence which directly caused weapons to malfunction in the jungles of Southeast Asia. After the real problems were brought to the surface, corrective action was finally taken to develop a weapon system that would function properly with its ammunition and could be deployed reliably in extended combat operations for decades to follow. We will now take a hard look at the errors, oversights, and solutions which lead to the combat proven M16A1.

Fateful Selection of Ball Powder
Most problems encountered with the rifle would be based on the Ordnance Corps’ decision to load 5.56mm ammunition with Ball powder instead of the IMR powder it was designed for. The decision was made carelessly and without testing to see if the Ball powder would have any adverse effects on the rifle. This was a grave error, one that the government would be warned about both by Gene Stoner and by Colt’s.
So what difference does the powder make? All the difference in the world. Auto loading firearms are by far one of the most complex of all machines. The tolerances and manufacturing processes are very unforgiving. A military rifle is a weapon system. That system is made up of a weapon, cartridge, propellant, primer and bullet. Any time one is changed, it must be tested and qualified before a change is implemented to insure the integrity of the weapon is not compromised. It was not.
Ball powder caused a series of malfunctions due to its different burning properties from the IMR powder the rifle was designed around. Keep in mind that the gun and ammunition were designed together. Ball powder has a much sharper pressure curve (burns faster) and increased the port pressure of the rifle. This increases the cyclic rate of the firearm by more than 200 rounds per minute. What this means is the timing of cycling of the firearm was dramatically sped up. The rifle was designed to fire at a rate of 700 to 800 rounds per minute, with ball powder it was increased to nearly 1,000 rounds per minute. This alteration of operation caused numerous problems including exceeding the cyclic rate maximum. It was so bad that Colt (by instruction of the Army) performed acceptance testing with older lots of cartridges loaded with IMR powder so that they would meet the lower cyclic rate as specified in the contract with the Army so the rifles could be delivered to the Army. Ball powder has been used going back to World War II. Large stocks remained from that time period that could be converted into rifle powder. This significantly decreased the cost in comparison to IMR powder. The main problem with IMR propellant was the inability for DuPont to manufacture the quantities needed to the specifications required. The actual decision to use ball propellant for this rifle system was not a bad decision, the problem came into how they implemented it. The rifle/ammunition were not tested and qualified before ammunition with Ball propellant made its way to the jungles of Southeast Asia.
Failure to Chrome Plate the Chamber
The principal and most serious cause of the malfunctions of the AR-15/M16 rifle in Vietnam was the failure to chrome plate the chamber. From experience gained in the Pacific Theater during World War II, it was found that chrome plating a chamber of a firearm would prevent many serious failures to extract. This military requirement was set forth by Ordnance Technical committee since 1957. Corrosion causes pitting in the chamber. When the cartridge is fired, it expands to the walls of the chamber. The cartridge would stick in these pits causing the extractor to tear the rim off the cartridge cases and the only way to remove it was to hammer it out with a cleaning rod. If the chamber was corroded and pitted, no cleaning would make it function properly. The question is, if we learned this lesson in World War II and made it a military specification on all U.S. small arms, why did the AR-15/M16 rifle not have it? The blame here goes not to Ordnance Corp but to the “Wiz Kids” on Secretary of Defence McNamara’s staff who made all the decisions. This micromanagement of money in resources and decisions was made by people who had not the slightest clue about small arms. As stated by William Davis, Jr. about the decision to not chrome plate the chamber, “If the rifle needed a chrome chamber Stoner would have designed it that way. So it did not have one therefore it did not need one.” Despite that fact, the rifle that Stoner and Colt showed the government was not a finalized weapon. It would need development to get ready for the troops to use at large.
This problem was simply corrected. First to appear were barrels with chrome plated chambers only. The barrels were marked “CMPC”(Colt magnetic particle inspected and proof tested). Barrels were also sent to Rock Island to have the chambers modified and chrome plated. This prevented the serious failures to extract and made the chamber easier to clean. Later in the war, the barrels were chrome plated in both the bore and chamber. These barrels were marked “CMPB” or “ CMP Chrome Bore.” With this modification the failures to extract became a thing of the past in the rifle.
Additionally the original gas tube was made from AISI 4130 steel. Due to corrosion issues that came up in the jungles of Vietnam the gas tube material was changed to stainless steel. This was implemented in the 1966 to 1967 time frame. This change eliminated the corrosion issues.

(Photo courtesy of Collector Grade Publications)
Failure to Extract
Failure to extract problems were due to the bolt unlocking sooner due to the change-over from IMR to Ball powder. There was still high residual pressure in the chamber and the cartridge cases did not have sufficient time to contract to be easily removed from the chamber. Thus, the extractor would slip off the rim or shear part of the rim off leaving the fired cartridge case in the chamber. To clear this malfunction, often the bolt would be closed again and the cartridge would come out of the chamber. If you compounded this malfunction with a corroded and pitted chamber, the cartridge case would become lodged in the chamber and have to be pounded out with a cleaning rod. This was by far the most serious of any malfunctions of the M16 in Vietnam. Chrome plating the chamber cured the extraction ill. The next major improvement to extraction took place in the 1970s with the addition of the rubber extractor spring buffer, which greatly increased extractor force. This particularly helped carbines that had a much higher cyclic rate.
Fouling
Fouling has been played up by many as the main cause of the failures in Vietnam. Many claimed that the gun would malfunction and the only way to get it working again was to tear it down and clean it on the battlefield. This was not the case. The main malfunctions were caused by corroded chambers causing failures to extract. No matter how clean the rifle was, it would not function reliably with a corroded chamber. Cleaning will not increase bolt and fire control group strength to prevent parts breakage due to the significant increase in cyclic rate. However, Ball powder did cause more fouling in the firearm, particularly in the chamber and inside the bolt carrier in between the back of the bolt carrier and the rear of the bolt. Simple maintenance took care of this, but maintenance became a problem of its own. It should be noted that to this very day the military M855 Ball cartridge uses Ball powder and the M16A2 and later generation rifles work very well.
Correcting Slam Fire Issue
One of the earliest problems to surface was slam fire. Slam fire occurs when the bolt is released and the firing pin strikes the primer and that inertia is enough to set the cartridge off. The principal culprit was the inconsistency in the manufacturing of the primers. When soft batches of primers were loaded this was more evident. To cope with this problem, the weight of the firing pin was decreased thus correcting the problem. There was a complete retrofit of all the old firing pins with the new ones service wide. Based on my research, the old firing pins were destroyed to keep them from surfacing at a later date and causing slam fire problems.
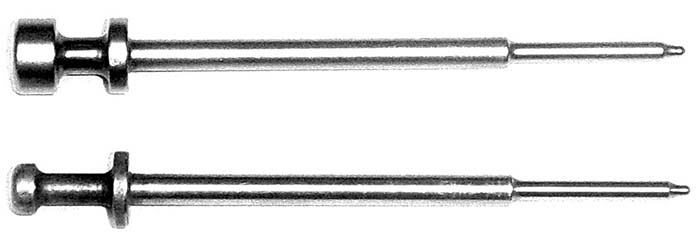
The “Light Strike” Problem and Newly Designed Buffer to Cope
The “light strike” was consequence of the higher cyclic rate. This malfunction was only found on fully automatic fire. When the cartridge is fired, the bolt carrier moves to the rear and the hammer is held by the automatic sear. The bolt carrier moves forward by action of the buffer spring, strips a cartridge off the magazine, chambers it, and as the bolt moves into the locked position, the sear trip area on the back of the bolt carrier tips the auto sear releasing the hammer to fire. But when the bolt carrier slammed into the barrel extension, it would momentarily bounce off the barrel extension and when the hammer would strike the bolt carrier, it would not be completely closed. The hammer would ride the firing pin/bolt carrier group forward and by the time it would lock there would be insufficient energy left to fire the cartridge. Thus, there would be a light dent on the primer but the round would not fire.
This problem would be corrected by the redesign of the buffer/spring guide. The original buffer, which utilized the “Edgewater ring springs,” was basically a spring guide that worked well with IMR propellant. For use with ball powder, five sliding steel weights were inserted inside the buffer and in- between them are small rubber disks. The weights would be able to move freely inside the buffer. This accomplished a couple things. First, it slightly decreased the cyclic rate on the closing stroke. Secondly, it prevented the bolt carrier bounce. As the buffer moved rearward when fired, inertia kept all the weights to the rear and when the bolt carrier would move into the locked position the weights would move forward absorbing the energy preventing the bolt carrier bounce.


Excessive Parts Wear and Breakages
The bolt itself would crack and break from the higher velocity and impact caused by the higher cyclic rate. The rear of the disconnector would break as well. These components worked properly at their design parameters but the increase in cyclic rate caused them to be overworked and eventually fail. The bolt catch was found to break with extended use due to the higher cyclic rate. It certainly was not that the rifle would not work with ball powder, it would have to be modified to do so. That was the job of the Ordnance Corps as per directions given by Secretary of Defense McNamara: they failed to do that.
Refining some manufacturing processes and redesigning some components solved these problems. The bolt was shot peened to increase its strength to deal with the higher cyclic rate. The disconnector was redesigned and made stronger to deal with the harder impact. The bolt catch was strengthened to halt the bolt carrier group of the higher velocity caused by the use of Ball propellant.
Other Modifications and improvements
As the war progressed, the rifle was further modified and improved. After first fielding, it was clear that these rifles were corroding. This is called “Intergrandular Exfoliation.” This is a chemical reaction in the aluminum caused by a combination of humidity, body perspiration and other chemicals that caused the receivers to flake off in layers and had a white corrosive substance appearance. This was primarily due to the receivers being made of the lower quality 6061 T6 aluminum forgings. Eugene Stoner himself had pled with Ordnance Corps to use 7075 T6 aluminum and was shot down until 1968 when production changed to the desirable 7075 T6 aluminum, which is used to this very day.
The lower receivers went through three generations as well. The original utilized a removable front pivot pin. The second introduced the captive front pivot pin, which visibly showed a raised area/rib that went straight back behind the front pivot pin and ended near the rear of the ejection port. The third was the addition of the magazine release button fence, which prevented accidental release of the magazine by dropping or dragging.
The bolt and bolt carrier had gone through some changes as well. The original AR-15 had a chrome plated bolt and bolt carrier. The XM16E1 used the same with the addition of the forward assist notches. This was a proprietary “hard” chrome plating process that was quite expensive. It was found that the chrome did wear off and chip and eventually corroded. It had also prematurely worn the internal dry film lube inside the upper receiver. The original purpose of chrome plating was to make it easier to clean. This it did, but there was a better way to go about this.

There are no remaining records that state the exact time when the chrome plating process ceased, but it is safe to say in the 1967 time period the chrome plating was dropped in favor a more durable and cheaper manganese phosphate which was black in color. The inside of the bolt carrier and carrier key remain chrome plated. Both the smooth side as well as the forward assist notched versions of the bolt carrier was produced in chrome plating and eventually both changed to the new finish. In 1966 Colt stopped manufacturing the smooth sided carriers due to lack of interchangeability with the XM16E1/M16A1 rifles.
Additionally, a new firing pin retaining pin was introduced. The original part was a machined retaining pin that came in chrome plated and manganese phosphate finish. A much cheaper cotter-type pin replaced this. The original was a much better component but there was another more inexpensive way to do the same job.
The Self-Cleaning Gun
With the purchase and distribution of more than 85,000 AR-15 rifles in Vietnam, there was not a single .22 caliber cleaning kit, operator’s manual or chamber or bore cleaning brush available. As recalled by Gene Stoner, the Army had no intention of buying the rifle so the government did not want to waste money on cleaning kits and manuals. The AR-15 was supposed to be an “interim” solution until they could get the SPIW (Special Purpose Individual Weapon) finalized and fielded. Therefore, the gun was touted as being self-cleaning. Troops were instructed that it was not necessary to perform any cleaning or maintenance on their weapons prior to going out on patrol or on a mission. Due to lack of reasonable maintenance guns would be fouled, firing thousands of rounds without cleaning. By not cleaning, the humidity and other environmental factors, the gun was even more prone to corrosion in the barrel and chamber. With the lack of availability of cleaning supplies, operator manuals and maintenance training, rifles were found to be in unserviceable condition in the hands of infantry soldiers. Many soldiers in the early part of the Vietnam War received training on the M14 rifle in basic training and when they arrived in Vietnam they were issued an M16. They received no instruction on operation and maintenance. With the introduction of Ball propellant, the fouling became more of a problem without maintenance

(Photo by Jim Wesley)
It was not until late 1966 that the Army began distribution (small) of the newly designed chamber brush which cleaned fouling out of the chamber as well as the locking recesses in the barrel extension. It was not until 1967 that large scale distribution of manuals, cleaning rods, bore and chamber brushes and lubricant were issued to the troops in the field.
Many have seen pictures, video coverage or heard stories of the flimsy M16 that was so fragile to dirt that condoms were placed over the muzzle to prevent dust from entering the barrel. Once again, a half-truth. The reason for covering the muzzle was to prevent water from entering the barrel. Due to the smaller bore, water enters by capillary action and is retained by surface tension. The gravity overcomes the surface tension in a larger .30 caliber bore and it will run out more easily. This was to protect more so from walking thorough streams and rivers and large amounts of water entering the barrel rather than a few drops of rain. This is a characteristic of a .22 caliber high power rifle. The best way to improve the barrel strength is to massively overbuild it to take severe pressures but the weight would become unacceptable. It should be noted that M1 rifles during World War II also had condoms placed over the muzzle during landings on beaches to keep water out of the muzzle.
The Forward Bolt Assist

Many believe to this day that the forward assist was an improvement to the rifle. The designers contested that it was in fact not an improvement but rather a detriment. Testing performed at Rock Island Arsenal proved this. They were able to demonstrate the detriment of forcing a cartridge into a chamber, and in particular a dirty chamber that can cause serious failures to extract and to open the bolt under adverse conditions. The forward assist was added by the request of the Army so the soldier would have some external link to the bolt carrier to manually close it. Odd, since even the M14 manuals say that you never force a round into the chamber. If it will not chamber, eject it out and load another. As Stoner designed the AR-10 as well as the AR-15, this external link was found not necessary. The forward assist was added to fill a psychological need, not a mechanical one. Eventually, it was added to all production rifles and is still in use today. It is an expensive addition to the rifle that has no practical purpose. Under extreme conditions such as being heavily corroded (not seen since they became chrome plated), or with heavily fowled chambers, the forward bolt assist will aid in chambering the round but will not affect the inevitable failure to extract. In firing hundreds of thousands of rounds out of M16-type weapons, this author has never had a malfunction that the forward assist would have cleared.
The Final M16A1

(Photo courtesy of Frank Iannamico)
On February 13, 1967 the XM16E1 rifle was type-classified the M16A1 rifle. The final version would carry this weapon system for the next 18 years until the adoption of the M16A2. The final “A1” would have the enhancements including the magazine fence for preventing the magazine from being accidentally released, the forward assist, the 7075 T6 aluminum receivers, chrome plated bore and chamber as well as the new butt stock with the trap door to hold cleaning equipment. With the development of this rifle in full swing after the hearings, troops who entered into service in late 1968 encountered little trouble and the weapon went on to become one of the most successful small arms the world has even known.
The Carbine
With the introduction of the short barreled XM177 and XM177E2 carbines, a new realm of problems were found. The U.S. Government never officially adopted any 5.56mm carbine until the Colt M4. So, all the carbines used were small runs of guns not fully developed and no final Technical Data Package, and therefore; no true mil-spec like the standard rifle. Due to the shorter distance from the gas port to the bolt carrier, significantly more pressure is created in the carbine increasing the cyclic rate even more than the standard rifle. Multiply this with the use of ball powder. Major problems were more frequent failures to extract and bolt carrier bounce. With refinements such as the new M4 “H” buffer, the bolt carrier bounce problem has been solved and with enhancements to the extractor (stiffer spring and stronger buffer) and the use of the new “O” ring have brought the failures to extract problem to a halt.
Conclusions
Reputation is a funny thing. It is developed by many factors, rarely are they based on fact. It is subjective based on the individual’s perception of the weapon and subjected by prejudices. The AR-15 as introduced by ArmaLite/Colt was an excellent firearm but needed to be put through a proper development program before it was issued to the troops. Through this process, issues such as chrome plated chambers, cleaning equipment and modifications to use the alternate Ball powder would have been addressed. The political infighting between the Ordnance Corps, the U.S. military and congress caused many U.S. servicemen their lives by putting a weapon in their hands that was not properly developed, which Ordnance Corps was responsible for. Development of a weapon should never be conducted in the field. This agenda was for one purpose only, to protect their inferior M14 because it was home grown. Regardless that the M16 was ideal for the combat conditions in Vietnam, it was clear that the increased hit probability due to lightweight and low recoil, controllability on full automatic and ability to carry significantly more ammunition over the M14 were a clear advantage. High volume of fire was required in the dense jungles where clearly defined targets were rare. History has a funny way of repeating itself – One has to wonder what the M4 will compete against.
Acknowledgements
I would like to thank to Ken Elmore, President of Specialized Armament Warehouse for his contributions of both intelligence and materials for photography. An avid Colt AR-15/M16 enthusiast and collector, Mr. Elmore is also an instructor for Colt Defence LLC Law Enforcement Training Division. Specialized Armament Warehouse is one of the largest Colt parts dealers in the World located in Chandler, Arizona.
This article first appeared in Small Arms Review V9N5 (February 2006) |