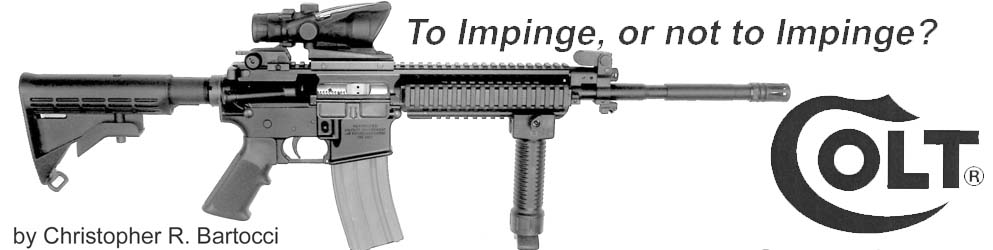
By Christopher R. Bartocci
The Retro Piston Operating Mechanism and Colt’s Advanced Law Enforcement Piston Driven Carbine
SAR gets the first look at Colt’s new Advanced Law Enforcement Carbine (LE1020) piston operated carbine and the controversy of the direct gas versus piston driven mechanism. This is an inside look at the evolution of the Colt Type C SCAR weapon to the new LE1020 family of weapons.
Since the introduction of self-loading long guns at the turn of the century, there has been one primary operating mechanism employed in particular on service weapons: the gas operated piston mechanism. The two main types are the shortstroke tappet where a two piece piston/ operating rod strikes the face of the bolt carrier group driving it rearward and the piston rod returns to its forward position by a spring (SKS, AR18 and FAL), and the other would be the piston rod which is connected to the bolt carrier (AK47). Both systems work well and are very reliable.
In the 1950s the military was looking for a lighter alternative to the current weapon systems. ArmaLite, a division of Fairchild Engine & Aircraft was working on advanced firearms designs with just that in mind. With their aircraft background, it was only logical for ArmaLite to take full advantage of the advanced aluminums to decrease weight.
Their first successful design was the 7.62x51mm AR-10. This rifle had two receivers manufactured of aircraft aluminum and made use of advanced polymer stock, pistol grip and handguards. It was very advanced for its time and for many back in those days, way too new.
The AR10 design made use of a different operating mechanism that went right along with the lightweight theme that the military was looking for. This system was called gas impingement or direct gas operation. There was no heavy piston rod which obviously decreased weight. A stainless steel gas tube ran from the front sight assembly to the bolt carrier. Gas was bled from a gas port in the barrel under the front sight assembly and directed through the gas tube into the bolt carrier group. An expansion chamber was created between the back of the bolt and the rear of the inside of the bolt carrier. The bolt would be driven rearward unlocking a multi-lug bolt from the barrel extension. Excess gas was bled out through vent holes in the carrier.
There were many benefits to this system. This included a decrease in weight, less parts and no maintenance of the gas system. Another major benefit was the increase in accuracy from the piston guns. Due to no heavy piston and gas block mounted to the barrel, the barrel was free to vibrate with little disruption from the operating mechanism. Also due to the design, the entire operating system was inline with the shooter’s shoulder which decreases recoil.
There were some trade offs as well. Due to no heavy piston, the cyclic rate was increased. Owing to the expansion chamber being inside the bolt carrier, carbon and fouling would be deposited in the bolt carrier, which would require more maintenance than the older piston gun.
The AR-10 would evolve into the 5.56x45mm AR-15, which would in turn developed into the M16 family of weapons (M16, M16A1, M16A2, M16A3 and M16A4) and the M4 carbine family of weapons. Problems arose early in the Vietnam War due to improper development of the family of weapons and lack of training and cleaning equipment. The M16 rifles did require more maintenance than the piston operated AK47. Due to the direct gas operation, the bolt assembly would require disassembly and cleaning but this was on the user level. After the troops were properly trained the majority of the malfunctions went away. Other complications that arose with the M16 in Vietnam were due to changing propellants without qualification and the rifles malfunctioning due to excessive cyclic rate/parts breakage and high amounts of fouling due to the use of ball powder.
The clean up began after a Congressional hearing. Rifles were being modified with chrome plated chambers, bolts and disconnectors were modified to cope with higher cyclic rate caused by ball powder as well as cleaning kits and proper training in maintenance. Chemical make up of the ball propellant was changed to significantly decrease the carbon deposits in the bolt assembly decreasing the fouling.
Colt’s First Look at a Piston Operated M16
With the success of the AK47 in Vietnam and the early problems the AR-15/ M16 encountered, Colt experimented with a piston driven version of their M16A1 rifle in the late 1960s. The Model Colt 703 design had a piston rod that connected to a modified bolt carrier. This system virtually duplicated that of the proven AK47.After the refinements were made to the M16A1 and the 5.56x45mm ammunition, the piston system was deemed unnecessary by the U.S. Government and abandoned. The government found no advantage to the use of the piston system in reliability compared to the finalized direct gas M16A1 rifle.
Old Technology Becomes New Again
Recently, much publicity has been made about the inadequacy of the gas impingement system in favor of the traditional piston system. This drive has come mainly through the efforts of different manufacturing firms trying to answer the issues presented from customers and end users. Applying the short-stroke tappet gas system had also been looked at in the mid- 1980s: the RHINO system, as well as various parallel developments in the 1960s such as the AR-18.
Throughout SOCOM, there had been many reported issues with the M4A1 carbines in respect to durability and reliability. The issues ranged from failures to extract, broken bolts as well as blown barrels. The SOCOM consensus was that the M4A1 carbines were not durable or reliable due to their use of the “flawed” direct gas system, which deposits fouling into the bolt carrier group inducing eventual failures. The interesting part was that SOCOM was the only group to find the M4 to be officially flawed, hence the birth of the SCAR program.
What is the Reliability Standard?
According to the mil-specs, the M16 and M4 series weapons exceed by more than 3 times what is required. Independent testing of two M16A1 rifles by then Captain Mark Westrom in 1984, then Ordnance Officer with 205th Military Intelligence group in Frankfurt, Germany, showed that the two rifles will fire 2,000 rounds (each) without cleaning and no malfunctions.
Manufacturers who make piston driven rifles claim them to be more reliable. Before you have a comparison there must be a standard requirement. The firearm must fire X amount of rounds in Y amount of time with no more than Z amount of failures. Much thought must be given to X, Y and Z. For instance, what is a reasonable round count of consecutive fire before the weapon should fail (lightweight carbine, light support weapon or heavy machine gun)? A lightweight small arm should not be expected to do the job of a general purpose belt fed machine gun. What is the maximum number of rounds one can reasonably be able to expect to be fired before the soldier cleans his weapon? Say the weapon must fire 1,000 rounds without cleaning and no malfunctions. Both an impingement gun as well as the piston gun can meet that requirement. Military issue weapons requirements must state what it must do to pass quality control and be entered into government inventory.
Both types of weapons are battle proven. Both have advantages and disadvantages. The main benefits of the direct gas are its light weight and lack of the weight of a heavy operating rod. Additionally, the M16 series of firearms has an inline operating system which aids in controllability on automatic fire and a significant increase in accuracy due to no piston being attached to the barrel, particularly with the advances in rail systems such as the A.R.M.S. SIR system, which leaves the barrel completely free-floating. This gives the weapon more accuracy and assists in cooling down a hot barrel. The main disadvantage is the weapon directs hot gas into the bolt carrier group to cycle the weapon and fouling is deposited on the back of the bolt and rear of the carrier. With neglect and lack of maintenance, this can lead to malfunctions. The system is maintained with standard cleaning equipment and brushes. No special tools are required for maintenance. There is also the sensitivity of “time under pressure” with a direct gas system, which has been the root of many problems in barrel length changes and similar attempts to change the balance of the system without adding the “time” component into the equation.
The advantage of the piston mechanism is that all hot gasses remain in between the piston and the gas block. No fouling gets into the bolt. However, the walls of the chamber will still become fouled regardless of the operating mechanism. This is a reliability advantage in severe conditions. Traditionally, there will be a lower cyclic rate with a piston driven system. The disadvantages are the increase of weight caused by the operating rod, additional parts such as piston return springs as well as the fact the piston rod impedes on the harmonics of the barrel when fired decreasing potential accuracy.
Colt’s Advanced Law Enforcement Carbine (LE1020)
The LE1020 is a direct descendent/product improvement of the Type C SCAR. Both designs stemmed from a gas piston design concept by Colt Engineers that has roots that go back to the Colt 703 of the late 1960s. Once the decision was made that it was not necessary, the idea lay dormant until a few years ago.
As recalled by Colt engineers who attended the SCAR Bidders Conference in Tampa, Florida, all the manufacturers gave independent presentations in front of about 40 SOCOM representatives on what they were thinking of for the program. After the presentation, the manufacturers were asked questions by the representatives such as, “Do you have a piston gun?” and “Would you consider making a piston gun?” It was clear SOCOM wanted the piston system for their own reasons, so Colt built one. The Colt SCAR Type C would compete in the SCAR trials and be rated “acceptable,” along with the other two Colt entries. For more details on the Colt SCAR Type C, see Small Arm Review, Vol. 10, No. 1, October 2006.
Colt Defense was not the first on the market to produce a piston driven M16 platform weapon. Colt chose to take an incremental approach to the development of their final piston system to be sure their customers got the finest product the first time they offered it. As of this writing, Colt Defense has two different piston designs under consideration, which were developed by their engineering team of Paul Hochstrate, Art Daigle, Kevin Kaminski, Greg Rozum, Mike Josey, Greg Kuczynko and Bob Habernern. Before Colt goes into production, they want one piston operated rifle. Both piston systems have design benefits. The Colt piston system is also the only piston driven M16/AR platform to have completed and passed an Official U.S. Govt/SOCOM trial. However, the Type C SCAR would go through several evolutionary changes before it would be sellable as per Colt’s standards. Colt will combine the best features of both systems to their final design. Delay in the debut of the piston operated carbines has also been primarily due to Colt’s wartime production of M4 and M4A1 carbines to the U.S. Government and allies.
The Colt type C SCAR and LE1020 utilize a proprietary monolithic upper receiver that is machined from a solid aluminum forge (7075 T6 aircraft aluminum). There is a major advantage to having a free floated barrel, both for accuracy and sustained fully-automatic fire. By going with the monolithic onepiece upper receiver, Type C SCAR and the LE1020 did not require any add on rail systems to add weight or unnecessary parts. There is a continuous milstd- 1913 rail from the charging assembly to the front sight/gas block. Additional rails were at 3, 6 and 9 o’clock positions for mounting a variety of accessories. Also, by having the monolithic rail, there are no issues relating to point of aim being affected by removing and re-installing optics. Also, with the use of the piston system, the conventional M4/M16 rail systems would not fit. On the face of the rail behind the front sight base, are two sling attachment points, one at 3 and the other at 9 o’clock for attaching a sling swivel. The bottom portion of the handguard is removable by pressing a tab in with a tip of a 5.56mm cartridge and sliding it forward and pulling downward. The LE1020 has retained the forward assist assembly, fired cartridge case deflector as well as the ejection port dust cover. The LE1020 prototypes have all been equipped with the military issue MaTech back-up iron sight.
The barrels have been produced in lengths of 10.5, 14.5, 16 and 18.5 inches in length. Both standard and heavy barrels have been produced. They are manufactured per mil-spec including a 1 turn in 7 inch twist to stabilize the 77-grain MK262 Mod 1 ammunition in use by SOCOM. The bore and chamber are chrome plated. As with all Colt barrels and bolts, they are tested with a 70,000 p.s.i. proof cartridge and then magnetic particle inspected to be sure there are no defects in the structure of the metal. The barrel comes standard with the A2-style muzzle brake. The LE1020 features M4 extended feed ramps in the barrel extension as well as upper receiver. The barrel profile has the M4 contour with the step for mounting an M203 grenade launcher.
The gas block utilizes a Colt designed folding front sight assembly as well as the locking mechanism for the piston assembly. The front sight is the mil-spec square front sight post. Also a bayonet lug is present. The cyclic rate on the SCAR Type C/LE1020 can be increased or decreased as desired by modifications to the gas port.
The piston assembly on the original Type C SCAR carbine was inserted from the front of the front sight assembly along with a return spring. The expansion chamber cap was placed in last and held in place by a large roll pin. This was the one criticism of the design by SOCOM. Colt testing had shown the carbine could fire at least 18,000 rounds without cleaning. However, SOCOM wanted an easier way to remove the piston assembly for cleaning. The LE1020 piston assembly is held in place by a push pin similar to the rear and front takedown pins on the lower receiver. This gave easy access for cleaning in the field without tools and made it so the locking pin would not be lost during cleaning. The operating rod is made up of the rod, return spring and return spring stop. The end of the return spring snaps over an edge on the operating rod to lock into place. This is similar to the way the buffer spring locks to the buffer. The stop is placed on the rear of the return spring.
The bolt carrier was heavily modified for the use of a piston rod. The early bolt carriers are modified selective fire bolt carriers. The carbine examined for this article is a pre-production model. The finalized bolt carriers will omit all of the gas exhaust ports on the carrier. They are not needed and serve no purpose on the piston gun. The carrier key was replaced with a shorter solid carrier key that is also pinned in place for added stability to take the impact of the piston rod. Two “skis” were placed on the bottom rear of the bolt carrier to keep the carrier in line with the buffer extension. As this weapon was designed by Stoner, it was as an in line construction.The bolt carrier group would move straight back into the buffer extension. Using a piston system changes this some. Due to the piston rod striking the carrier key, the force directs the carrier out of alignment with the buffer extension driving it on an angle. The edge of the bottom of the bolt carrier can damage the buffer extension tube. The “skis” put the carrier back in alignment preventing damage to the buffer extension tube and receiver. Currently, there is a government funded operational evaluation being conducted for SOCOM by Colt and UCT Defense for greaseless operating parts on the M4 to improve maintenance, functioning and the wear of select parts of the weapon. This will greatly aid in maintenance in the desert environment.
As previously stated, the LE1020 is a direct descendant from the SCAR Type C. The lower receiver will remain the same as the standard semiautomatic only LE6920. The LE1020 has a 16 inch LE6920 barrel for law enforcement, but the piston system can be produced in other barrel lengths. Numerous configurations of selective fire weapons using the piston system have been made using standard M4 lower receiver groups. The only difference is the piston operating system requires an H2 buffer when firing in automatic. This is one steel weight and two tungsten weights inside the buffer increasing significantly the mass of the buffer. This prevents light strikes due to bolt carrier bounce due to the high cyclic rate of fire. Colt Defense also intends to manufacture the piston rifle/carbine with standard M4 handguards and a new universal handguard.
What is the benefit of the LE1020 over the LE6920? The real benefits of the LE1020 system are the extended rail system, which is built into the weapon at the factory, and the free floating barrel. The barrel is also exposed for better cooling and maintenance. Is the future of the M4/ M16-type weapons going to be piston operated systems rather than direct gas? Perhaps some elements of SOCOM will go with piston operated carbines. Many in the industry believe the standard will remain with the direct gas guns. Indications from the Army state that the current M16A2/A4 and M4/M4A1 carbines are doing the job and they continue to order M4 carbines. But only time will tell.
This article first appeared in Small Arms Review V10N10 (July 2007) |