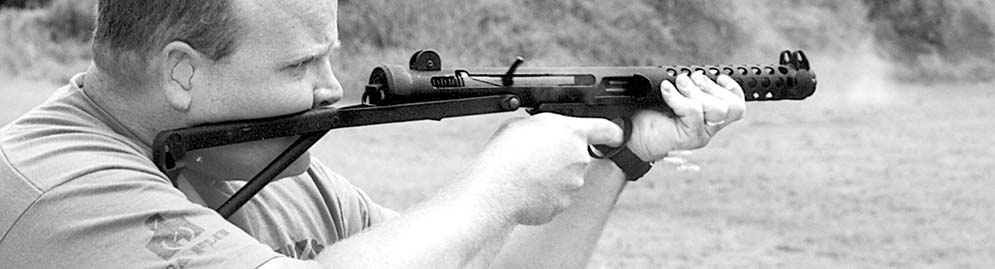
By William R. “Bob” Bishop
In 1986 I attended a well known military school at Ft. Bragg, NC, which allowed me to become familiar with foreign weapons. One of the weapons which really caught my interest was the Sterling SMG. The direct replacement to the world famous Sten gun, it had a construction and balance second to no other. All these years and several MP5’s, Uzi’s, etc. later, that memory of a fine weapon remains vivid in my mind. Unfortunately, the few fully transferable Sterling SMG’s are so rare they are essentially unheard of – until now.
Two nationally-known Class 2’s are now manufacturing “new” fully transferable Sterling SMG’s here in America. Interested? Then let’s move on as SAR takes you through this fully detailed creation of the rare Sterling SMG. The starting point for this project is its godfather, the Sten. The end result is one of the most classic open bolt SMG’s – the Sterling.
History
The history of the Sterling begins with the Lanchester SMG. This well built (and heavy) weapon was manufactured from 1941-43 and was somewhat of a clone of the German MP28(II) SMG. The Brits replicated the MP28(II) as they had no experience with SMG production and were desperate for weaponry during the early days of the war.
As the Lanchester was very expensive to produce it was decided by its maker – Sterling Engineering Co. Ltd. – to replace it with something requiring far less resources. Also, this new product would have to successfully compete against the then-new Sten SMG. George Patchett had just started working for Sterling and in the period 1942-43 produced 24 prototype Patchett MkI machine carbines. These shared the 9mm caliber, .065 wall thickness, 1.5” tube diameter and 50 degree cocking slot with the Sten. Everything else was an improvement.
The Patchett MkI machine carbine was improved with the newer MkII version: 82 degree mag well to accept the new curved 34-round magazine, a radiused chamber feed lip and improved folding buttstock. This competed in numerous arms trials and finally was selected by the UK government as the Patchett MkII (“L2A1” in MoD nomenclature) in 1953 to replace the Sten MkV. A total of 6,536 were built. In 1955 the MkII/L2A1 was replaced by the evolutionary MkIII/L2A2 which dropped the Patchett name and was officially known as the “Sterling SMG”. A total of 4,449 were built. Finally, the end product as we know it – the Sterling Mk4/L2A3 SMG – was adopted by the UK military in September, 1955 and soldiered until 1994 when totally replaced by the SA80 rifle.
During this time 374,369 SMG’s were built by Sterling and also Royal Ordnance Factory (ROF) Fazakerley. Of this, Commonwealth military units received 15,250 from Sterling and 163,475 from ROF Fazakerley. The remainder of 195,644 SMG’s were Sterling-manufactured Mk4’s for commercial/export use. Production came to a halt in 1988 when Sterling Engineering Co. Ltd. ended its business life, and in 1989 was absorbed by British Aerospace. What started with the Lanchester in 1941 ended with one of the finest open-bolt SMG’s ever built – the Sterling Mk4/L2A3.
Conversion
The basic idea behind the conversion is exactly the same thought process the Sterling inventor, George Patchett, followed: start with a tube which is dimensionally the same as the proven Sten and then migrate it to Sterling specifications. In this case, start with a registered Sten tube, acquire a Sterling SMG parts kit and then have a very skilled C2 manufacturer integrate them.
Stan Andrewski of Stan’s Custom Gunsmithing and Don Quinnell of Don’s Gun Shop are currently the only two this author is aware of who do this conversion. Stan originated the Sterling concept after six months of correspondence with BATF’s Technology Branch. The proposed conversion was so close to the original Sterling that BATF went to extra lengths to make sure its agents could still identify the Sten tube. He finally received BATF permission in 1997 and has been at it since, while Don started in 1998. Both perform their work to the highest standards.
The remainder of this article will provide an overview from Don’s standpoint on how a fully transferable Sterling SMG is built to “factory” standard. While both Stan and Don have the same general process, each has their own proprietary differences. After all, you’ve got to keep your trade secrets! In each case the end result is fully equivalent in quality and function to that of the original Sterling Mk4/L2A3.
Parts Kit and Inspection
Stan and Don are adamant about the starting point for this Sterling project: get the parts kit first! Although the Brits manufactured 374,369 L2A3/Mk4’s very few – or their parts – actually got to America. This is because many are still in active service or military storage depots. International Military Antiques (IMA) has been importing Sterling parts kits since late 1994 and has brought in 500 kits during this period. Based on the unknown future of parts kit importation you should order one now for a very reasonable $250 and store it away while you locate the registered Sten tube.
The kit arrives with all parts as taken from active service Sterlings. Per BATF guidance it is cut into three sections: barrel jacket, mag well/handgrip and rear casing assembly. The bolt, trigger mechanism, barrel, stock, etc. remain untouched along with the factory 34-round magazine.
When the kit is received it must be checked for mechanical condition. The trigger assembly lock screw hole in the handgrip frame should be round and not oblong because of excessive bolt cyclings. Closely examine the forward edge of the hole for roundness. Within the trigger assembly the guide rod and axis pins must be checked. On early production ROF Fazakerley SMG’s these were phosphated and prone to rusting. Later production guns and all Sterling-manufactured units used stainless steel pins – make sure you have these. Also, check the sear nose and trip ledge on the bottom of the bolt as they must not be rounded in order to assure proper bolt release.
A final “must” purchase item is a superb book which gives the complete history and layout of the Sterling SMG. It is called “The Guns of Dagenham” by Laidler and Howroyd. With 310 pages and 371 illustrations it is worth every cent of the delivered $43.95 cost. Call C&S Metall-Werkes or Long Mountain Outfitters for ordering information.
Registered Tube
Registered Sten tubes are not too difficult to find; unfortunately, they are usually attached to a Sten parts kit and now comprise a complete SMG. No problem – those parts will soon be coming off and converted back into a Sten parts kit. But there are differences among the registered Sten tubes out there and could affect the fidelity and longevity of the newly-created Sterling.
Some general observations on several typical registered Sten tubes:
Erb: This is the highest quality registered Sten tube available. These were manufactured to the strictest standards from 4130 chromoly steel with the correct DOM .065” wall thickness. Dimensions are exact and about 500 tubes were registered before May, 1986.
Wilson: Wilson’s tube is also of very high quality with dimensions held to the tightest tolerances. An issue with this tube is its serial number is usually marked under the mag well where the Sterling sear hole must be milled. This requires extra C2 work so as to not obliterate/remove this number.
DLO: This tube is manufactured of harder steel than other tubes and consequently more difficult to machine. But, as the dimensions are different in the front/rear receiver areas to accommodate the method in which DLO parts kits were cut from the original Sten, it converts to a dimensionally accurate Sterling in overall length.
CatCo: This tube adheres to Sten specifications quite well and is built from 4130 chromoly steel with a DOM .049” wall thickness. While this is thinner than desired, it remains somewhat usable for a Sterling conversion. CatCo registered about 70-80 fully transferable tubes before the May, 1986 ban went into effect.
Conversion Process
The first order of business is to create the basic “Sterling” receiver. This is initiated by bolting the barrel into the severed barrel jacket via its 1/4×5/8” socket head screws and then sliding the barrel’s circular rear flange into the front of the receiver tube. Precise measurements of the barrel’s chamber face are then made in relation to the mag well/ejection port areas. This will determine where the barrel must be positioned, and in doing so establish the overall length of the combined jacket/Sten tube. Tolerances for this are + 1/8” to assure reliable functioning. Once this overall length is calculated, the barrel is removed from the jacket and welding begins.
A precision-turned and tightly fitted bronze mandrel is then tapped into the Sten tube with a rubber mallet. Meanwhile, the jacket has been shortened (usually about 1/4”) to yield the correct overall calculated receiver length. The jacket is fitted over the mandrel and precisely indexed to the front of the receiver tube. It is then very carefully MIG welded to the tube while the mandrel draws off excess heat. This procedure is absolutely critical as barrel/sight alignment and faultless functioning are fully dependent on receiver straightness. Once this is done, the weld bead is ground down to precisely blend in with the receiver. Also, the rear cooling holes in the barrel jacket may need to be redrilled to their standard 9/16” diameter.
Next, the buttcap locking ring is removed from the rear of the severed Sterling tube. This is done by drifting out the index pin and carefully milling away the remaining tube so only the ring remains. Once removed, it is pinned/indexed onto the Sten tube and silver soldered on. This, too, requires precise fitting as the buttcap locks into this ring and supports the folding buttstock. Fractions of a millimeter are critical.
Other components such as the handgrip, mag well housing, rear sight, rear finger guard, buttcap locking lever, etc. are all removed from the Sterling receiver and silver soldered onto their respective new locations. Close attention must be paid to the pistolgrip and mag well housing as they determine ammo feeding and sear/bolt control.
The first step before attaching the handgrip is determining the exact location of the new sear slot. Typically, the Sten slot must be opened up towards the rear about 1/4” to permit correct functioning. If necessary, a steel blanking piece is welded into the old slot and a new slot is recut. The external bead is ground flush with the receiver while a boring bar is run down the interior to mill flush the internal bead and also clean up any excess barrel jacket weld. The handgrip is then carefully MIG welded in four spots to the receiver, ensuring it lines up with the new sear slot and the grip is parallel to the bore axis. Remaining mag well seams are filled with silver solder.
Installing the mag well housing follows the same painstaking process as even a degree off specification will cause the rounds to be improperly stripped by the bolt and jam during chamber entry. Further, the ejector is contained in the mag well housing and also functions as the bolt guide. If this is out of tolerance the bolt will not cleanly release from the sear and its ejector slot will drag. To complete the work in this area the mag well and ejection port are slightly milled out to match original Sterling specs.
Both Stan and Don are very careful throughout this entire process of removing parts from the Sten tube and installing them to the new tube. While damage to the parts is possible, it is not likely due to their robust construction. What is possible, however, is the same flaw which bedeviled ROF Fazakerley: warping of the receiver tube. Fazakerley ruined over 7,000 tubes throughout 1956-59 due to heat buildup causing receiver warpage. The C2 gets one chance on your expensive registered receiver. Therefore, they go to great lengths to protect it by using the lowest amount of heat to permanently install the parts and special fixtures to draw off excess heat.
The single item which causes the biggest conversion hurdle – yet keeps the tube within BATF guidance – is how to integrate the Sten tube’s 50 degree cocking slot with the 60 degree slot of the original Sterling. This is done by modifying the cocking handle so the interior portion engages the bolt while the exterior handle travels in the 10-degree offset slot. This is achieved by cutting off the handle section itself and then MIG welding it back at a slightly lower position. The end result is beautiful, quite effective, and looks right out of Dagenham.
The folding stock presents its own problems. Each Sten tube is fairly unique as they were made by so many different C2’s before the 1986 ban and tolerances range from tight to terrible. This means the butt trunnion which holds the stock must be iterated back and forth a fraction of an inch at a time until the precise fit occurs between the stock locking lugs, the buttcap and the lug cutout in the barrel jacket.
The assembly of the other parts is straightforward yet time consuming. Metal dings are smoothed out to “as new” condition and the spot welds are made flush by a Swiss file. Also, the headspace is checked for one last time for safety purposes. One bit of trivia is most NATO/military L2A3’s had a chamber .012” longer than commercial models. This allows all types of “ammunition of dubious origin” to be used. Chambers so cut have a “L” (Long) stamped above the extractor slot.
Once the entire Sterling is assembled and test fired, it is then disassembled for final finishing. All steel parts (except the springs and a few other items) are #7 glass beaded and black phosphated per the original Sterling SMG specifications. Then, it is time for the final step: the famous black “crackle” finish.
Military L2A3’s had Sunkorite #259 satin black baked enamel applied over phosphated steel. The exact match for this is John Norrell’s HK-color molycoat. However, during a phone conversation with author Peter Laidler, I learned most commercial Mk4’s were finished in “Trimite Crackle Finish (UK, MoD, Trimite 303, Plain Black, Heat Resisting)” paint as manufactured by Croda Paints Inc. Today, this is duplicated by using Harley-Davidson engine case paint. As most parts kits came from commercial guns the crackle finish is what most customers consider to be “true” Sterling and therefore highly desired.
The Sterling is first masked off and sprayed with crackle paint. It is then placed into an oven and cooked for 15-20 seconds at 170 degrees. This causes the moisture in the paint’s suspended wood resin to slightly swell and create the famous “crackle”. This is repeated a second time to give the almost-correct density/depth of crackle. The masking is removed and a third spraying is performed. This is then selectively cured by using a heat gun to raise the crackle to its final state. Baking in the oven thermally cures the finish into an epoxy-like hardness which is a work of art.
Sterling Characteristics
Specifications
The Mk4/L2A3 is 18.9” with the stock folded, 28.0” with it locked into the open position and carries an unloaded weight of 5.9 lbs. Sight radius is 16.25” and when new had to place the MPI of five rounds into a 2×3” square at 25 yards in order to pass accuracy standards. Since the 7.9” barrel almost never wore out you can rest assured this “new” Sterling will be quite as accurate. One Sterling in the UK MoD Pattern Room has fired over 250,000 rounds through the same barrel and remains in serviceable condition! The front sight is adjustable for both elevation and windage with one revolution of the sight blade moving the point of impact 5.5” vertically at 100 yards. Windage is achieved by drifting the front sight base. The rear sight is a “L” shaped dual blade affair which has graduated apertures for 100 and 200 yard ranges. Simply flip it to the range needed.
Rate of fire is an optimum 550 rpm, at 1280fps, with Commonwealth military MkIIZ ball, 115gr, 9mm ammo. This can be sustained for a long period of time since the muzzle blast draws cooling air through the perforated jacket and over the barrel. As it fires from the open bolt there is no danger of cookoffs or out-of-battery firing. It will fire so long as the 34-round magazine has rounds and the finger does not get tired on the trigger.
Loading/Firing
Like all open bolt guns simply cock the bolt, insert the magazine, move the selector to semi or fullauto, aim at your target and pull the trigger. Due to its open bolt nature it is best to prevent unwanted sear wear by ensuring full depression of the trigger rather than “feathering” it with only minimal sear disengagement. When firing this arm, the rate of fire feels exactly matched to proper target acquisition and engagement. Unlike the MP5K which “hoses” rounds, the Sterling places them precisely where you want – and under total control at all times.
Takedown/Cleaning
Ensure the folding stock is locked forward, take out the magazine and cock the bolt. Visually inspect the chamber to ensure no rounds have crept in by accident. Release the bolt and “walk” it home upon the empty chamber. Then, depress the buttcap locking lever and rotate the buttcap counterclockwise to unlock/remove it from the receiver tube. Do this carefully as the recoil springs generate significant pressure! Pull the bolt back until the cocking handle is beneath its cutout hole; lift out the cocking handle and then remove the springs/bolt assembly. Further disassembly is not necessary.
Every few cleanings you can remove the trigger assembly locking pin and extract/clean the trigger assembly. This area normally stays fairly sanitary as very little debris finds its way past the sear slot into the trigger mechanism. After completing the cleaning and oiling, reassemble the Sterling and carefully store it away. One note: due to the automotive nature of the crackle finish you should avoid ammoniated cleaners. BreakFree and similar products work fine.
Spare Parts
As of this writing, there are two sources of Sterling spare parts: IMA or PS Arms. By getting another IMA kit you obtain a whole new set of relatively inexpensive parts. With PS Arms you get brand spanking new parts as these were taken from demilled new SMG’s of 1984-87 manufacture. The difference is component wear and price. Spare 34-round magazines are available from PS Arms or Ohio Ordnance – get them now before any Executive Order kills their import.
Conclusion
The Sterling SMG is recognized throughout the world as extremely well built and utterly reliable. With few fully transferable examples available they are almost impossible to own. That has now changed. By integrating a Sterling parts kit with a registered Sten tube one can now own a true piece of martial arms history.
This integration is a joy to behold as the metalworking skills demonstrated by Stan and Don immensely add to a relatively unique SMG. With the cocking slot being the only discernable difference, this fully transferable version retains absolute fidelity to the original Mk4/L2A3 design. Heck, other than the Sten tube, all the parts are Mk4/L2A3. Should you wish to discuss this further or need current conversion pricing please call Stan or Don at their numbers below. They will be glad to discuss your particular project and delivery schedule. Rumor has it the rare Mk7 parapistol and the extremely desirable suppressed Mk5 are now available – any truth to this Don?
The Sterling Mk4/L2A3 is truly a classic SMG which has earned a worldwide reputation over the past 40 years for quality and utter reliability. Finally, fully transferable versions are now becoming available in America…and yielding their lucky owners quite “Sterling” service!
Stan’s Gunsmithing Services
Attn: Stan Andrewski
719 Battle Street
Webster, NH 03303
(603) 746-4387
Don’s Gunshop
Attn: Don Quinnell
3112 S. Palm Avenue
Ft. Myers, FL 33901
(941) 334-6779
PS Arms
Attn: Paul Sadowski
PO Box 798
Easton, PA 18044-0798
Roaming phone (500) 445-1432
Voicemail/fax (877) 286-2253
IMA
Attn: Mark
PO Box 256
Millington, NJ 07946
(908) 903-1200
Ohio Ordnance
PO Box 687
Chardon, OH 44024
(440) 285-3481
C&S Metall-Werkes Ltd
4025 Old Highway 94S
Suite O
St. Charles, MO 63304
(314) 928-1511
Long Mountain Outfitters
223 Sugar Hill Rd
Harmony, ME 04942
(207)-683-2169
This article first appeared in Small Arms Review V2N12 (September 1999) |