By Chris A. Choat
The AR-15/M16 platform is one of most prolific black rifles ever developed. In the early years there was, without doubt, a love/hate relationship by those who used it. Most of the problems were related to the powder used in the cartridges, not the rifle itself. The early powder used was not the powder the gun was designed to use and besides being extremely “dirty” causing severe internal fouling, it caused the rifle to cycle differently than it was designed for: resulting in a rifle that had different cleaning issues in the field, and was subject to extraction problems. The damage was done in the minds of many soldiers, who marked the rifle with a bad reputation. In later years, with improved powders and advanced machining techniques, it evolved into one of the most used rifles of all time, second only to the AK series. With the use of a cleaner burning “ball” type powder, chrome lined bores and chambers and a strict cleaning regimen the problems were solved and has become the highly reliable rifle that it is today. But even with the new advanced rifles and ammunition they will still get dirty and, if left long enough, will stop firing because of fouling built up in the bolt and upper receiver area. The design of the rifle is, after all, gas operated. Propellant gases are vented from the barrel, into the gas block, through the gas tube and into the bolt carrier key along with any unburnt powder and carbon deposits.
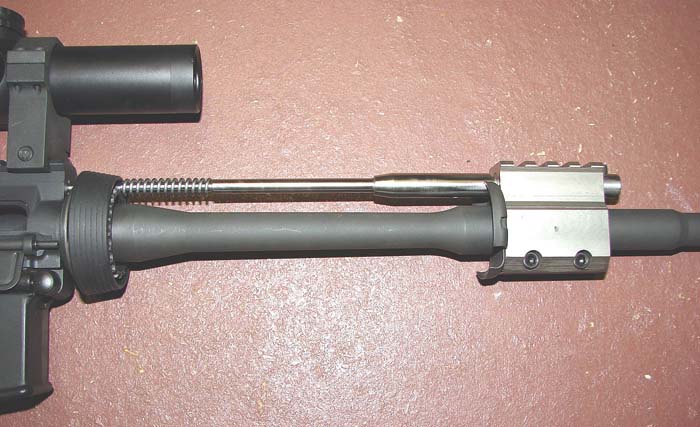
Today, the piston driven AR seems to be the way design changes are heading. Piston driven AR-15/M16s are not a new idea. In the mid 1980s, Walt Langendorfer introduced what he called the Rhino System. The system was a retro-fit kit that included a front sight unit, gas piston, spring and bolt carrier key. Although the system worked fairly well, there were issues with the spring in the unit. It just could not take the heat and would fail prematurely. Now the piston driven AR is not only accepted, it is sought after.
There are several manufacturers now making complete piston driven rifles or piston driven upper receiver units that will retrofit the existing AR-15/M16 series of rifles. These are high tech marvels and bring with them a high price tag. Not that these rifles are not worth the money, they are. A lot of R&D and expense went into developing the uppers. But what about the average guy that can’t afford to spend between $1,600 and $2,200 dollars for just a complete upper, let alone an entire rifle. Maybe the guy that has spent his entire “gun money” budget on his existing gun setting it up just the way he wants it with all of the best accessories and making it shoot perfectly.
There is now a way to have a piston driven gun at a very competitive price. Adams Arms is now producing a complete kit that will fit your existing rifle. The kit changes a standard gas operated AR-15/M16 rifle or carbine into a piston driven gun. The kit comes with everything you need and anyone can install it. You don’t have to take it to a gunsmith or do any machining. Just remove some of your existing parts and install the new ones. Installation takes only about 10 minutes from start to finish.
Installation
As is always the case when starting work on a gun, remove the magazine, check the chamber and make sure the gun is unloaded. Take the bolt carrier out of the gun and set it aside. Remove the existing flashider and lock or peel washer, remove the handguards, remove the front sight/gas block assembly with gas tube and remove the front handguard cap. If your existing gas block is the standard front sight assembly type you may have to drive out the two taper pins (look at the pins and drive from the small head side). The only other thing left to do is to remove the standard bolt carrier key. Most of these are staked in but can still be removed easily. Just be sure to have an Allen wrench that fit the screws tightly. The correct size is 9/32.
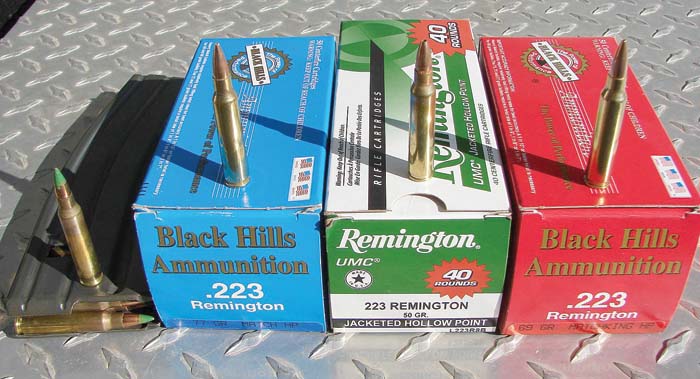
Once all the standard parts are removed it’s time to install the piston drive kit. The kit consists of a 440C stainless steel gas block, sleeve/drive rod, gas plug, sleeve/rod compression spring, bolt carrier key, a modified front handguard cap and a set of modified M-4 handguards. The upper handguard of the set has been notched slightly to accommodate the conversion’s gas plug.
Start installation of the new kit by setting the new carrier key onto the bolt carrier. The new carrier has a locating pin on the bottom that fits into the gas hole in the top of the carrier. Use red Locktite on the screws and torque them to 40 in/lbs. This is an important step. If you do not Locktite and torque them they may come loose. Next, install the bottom half of the new handguard into the delta ring then slide the handguard cap onto the barrel. Slide the new gas block onto the barrel with the gas plug groove facing toward the muzzle. As it becomes tight you may have to turn the gas block from side to side as you push it back. A rubber dead-blow hammer might be needed to nudge it into place. Be sure you line up the handguard to go into the handguard cap. This sounds like it takes three hands to do but it actually goes together very easily. Push the gas block as far as you can towards the receiver making sure that it is up against the handguard cap, straight up and down and aligned with the gas port hole in the barrel. As long as it is straight and the top of it is level, it will be aligned properly. The host rifle this kit was fitted to had an A3 flat-top upper and a level was laid across the upper and the gas block and eyeballed. You then tighten two hex bolts in the gas block to lock it on the barrel. Install the spring on the back end of the sleeve rod and thread it through the gas block, through the barrel nut, delta ring and spring and into gas tube hole in the front of the receiver. Insert the gas plug into the gas block by lining it up with the machined cuts in the front of the gas block. Push the gas plug back until the detent button on it hits the face of the gas block. Make sure it enters the sleeve on the front of the drive rod. Push the detent button in while you push the gas plug further back and rotate it 90 degrees. Install the top half of the M4 handguard and the installation is complete. The gas block on the unit tested had a Picatinny rail machined into the top. This works great if you want to install a front BUIS as it is the same height as the flat-top rail on an A3 upper. Adam Arms will also be offering a “low profile” gas block without the rail.
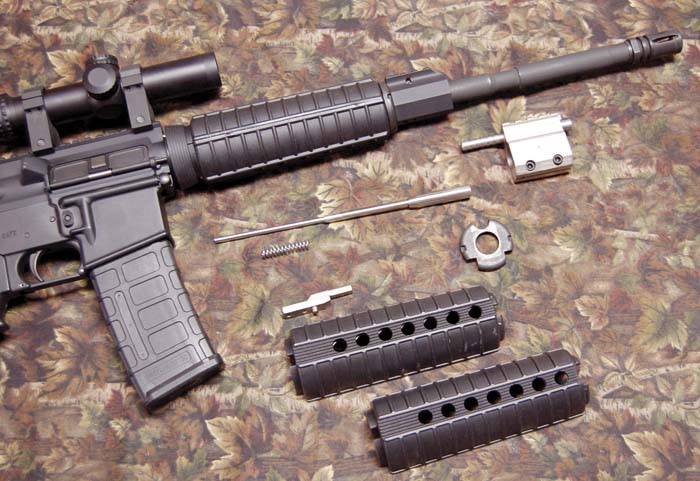
The upper that the kit was installed in was a mix of several manufacturers’ parts. It consisted of Model 1 A3 upper receiver, a Stag Arms .556, 1 in 9 twist, 16 inch M4 barrel with DPMS bolt, carrier and charging handle. Two different lowers were used, a semi-auto DPMS and a Colt full-auto lower.
Testing
The initial testing of the kit consisted of firing over 500 rounds of various types of .223 ammunition that included Black Hills 77-grain Match Hollow Point, Black Hills 69-grain MatchKing Hollow Point, Remington 50-grain Jacketed Hollow Point, XM855 green tip and some reloads with 55-grain FMJ bullets. This provided a wide variety of ammo types and bullets weights. Black Hills ammunition was mostly used as it has been found to be the most consistent and reliable thus eliminating any function problems related to ammunition. As it turned out, ammunition brand and type was not an issue. The new piston driven upper digested anything we ran through it. At the start of the test the fourth and sixth round fired and ejected but the gun failed to pick up the next round either time. It is suspected that it might have been because the drive rod spring was not seated completely against the delta ring/barrel nut. It happened while using the XM855 ammunition, which might also have been the culprit. Whatever the reason, we never had a single malfunction after that.
The testing was conducted in both semi and full auto with probably about half the testing done on full-auto. Cyclic rate was checked with a PACT timer with Rate-of-Fire option. Rate of fire was checked on the rifle before and after installation of the kit and ran right at 635 rounds per minute with a full stock on the rifle. Installing a collapsible stock on the gun raised the rate of fire to 675, which was to be expected.
Magazines used during the test included a US GI 30-round, Beta C-mag 100-round drum and the excellent new MagPul P-Mag 30-rounders. The P-Mag is a highly reliable polymer magazine that features a light weight magazine body with textured gripping surface, stainless steel corrosion resistant spring and anti-tilt follower. They are also available with a clear window in the sides to verify remaining round count.
Since this kit has no effect on accuracy it was not really a factor in the testing. Although the accuracy was normal for this type of rifle, there was no noticeable difference after the kit was installed.
During the test, one of Advanced Armament Corporation’s M4-2000 .556 suppressors was installed. It is small, light, installs fast and is capable of handling fully automatic fire. This was tried as an added test because suppressors are known for generating higher back pressures and increased cyclic rates. Over 100 rounds with the suppressor attached, in addition to the initial 500+ unsuppressed rounds, were fired. The kit ran perfectly with zero malfunctions while using the suppressor.
Conclusion
At no time during the testing was any lubricant of any kind used on the rifle. It was run completely dry. The rifle was broken open several times and parts were inspected. There was no premature wear on anything. The inside of the upper receiver around the carrier, bolt and locking lugs remained very clean with no unburnt powder or carbon present in either the upper or around the fire control parts in the lower. This is the most noticeable feature of a piston driven gun. They remain very clean and can run without lubrication. Probably the other most valuable and noticeable feature was that very little heat was transferred back into the bolt carrier and upper receiver compared to a regular gas system. During the test, 100 rounds were run through the gun with a Beta C-Mag. The gun was opened and the bolt pulled out. The bolt was cool enough to hold in your bare hand. A gun that runs cooler will have a longer service life with the advantage of fewer heat related parts failures.
The unit tested was a pre-production unit in bare stainless steel. Production units will be finished in a flat black Melonite to match the finish on most AR’s. Melonite is a thermochemical treatment for improving surface properties of metal parts. It offers improved heat and wear resistance. The drive rod return spring will have “caps” on each end to give it a more finished look and keep it from binding on the front of the delta ring. The spring will also be “detented” to the drive rod so that there is less chance to lose it when the unit is disassembled. Other improvements on the production units will be the knurling of the front of the gas plug to aid in removing it and a slot added to the front face for turning it with the rim of a shell if need be. The unit comes with M4 handguards but can also be used with several of the Picatinny rail forearms that are available. As of this writing forearm rails that will work with the system are the Predator, Midwest Industries and Daniel Defense. Others might possibly fit but have not yet been tried. Contact Adams Arms for a full list of compatible rail forearms. The kits will be available in different models for barrel lengths from 7 to 24 inches and for barrel diameters up to 1 inch. Retail price of the kit is between $550 and $600 depending on the model.
The unit is covered with lifetime money back manufacturers warranty. In other words, if it breaks they will replace it: period. Jason Adams has come up with a product that works as advertised, is well built and an economical way to have a piston driven AR-15/M16.
Adams Arms Retro-Fit Kit Update
Since this original article was written on the Adams Arms Retro-Fit kit there have been several very helpful changes that have been incorporated into the final production unit. Most noteworthy is that now the return spring is held captive on the sleeve/drive rod so that is doesn’t fall off or fail to stay in place as you’re disassembling the unit or putting it back together. This is a must, especially when using the kit on a weapon that has a rail system handguard. On the pre-production unit, the spring could easily slide off the drive rod and fall into the depths of the handguard or rail system handguard not to be seen again until you disassembled the handguard. The spring is still able to be removed from the drive rod by pulling it off forcefully but it now stays in place as it should as it is detented on to the drive rod.
There is also the addition of a stainless steel bushing on the end of the spring that rests against the Delta ring. Previously, the spring itself rested against the Delta ring and could catch on the spring when removing the unit from the gun. This resulted in the situation described above and also required removing the forearm to retrieve the spring.
Another addition is a stainless steel bushing that fits into the gas tube hole of the upper receiver. This bushing eliminates any wear that could occur to the upper receiver by the drive rod moving back and forth through the hole. Without the bushing the wear would only occur after several thousand rounds but is now prevented from happening. The bushing is easily pushed in place from the rear of the receiver with a wooden dowel or metal rod.
The last improvement involves the gas block and gas block plug. The plug itself now features knurling on the front outside edge. This allows for a much better grip on the plug making it easier to remove for cleaning or turning for adjusting as the production unit now features three adjusting positions. The first one is the standard full flow gas position. The second one cuts the gas flow down when using the unit on some short barreled guns or guns that have excessively large gas holes in the barrel. Some manufacturers seem to do this to their guns so that they can make their shorter barrels work. The third position completely shuts off the gas. This works great for that single suppressed shot. It is quite impressive by how much noise is eliminated when the bolt does not cycle.
Adams Arms has strived to make one of the best piston-driven AR kits that there is. The Adams Arms Piston Driven Retro-Fit kit has now evolved into one of the most well-made, reliable and easy to install units that is available today.
Sources
Adams Arms
Dept. SAR
32018 US Hwy 19 North
Clearwater, FL 33761
(727) 424-8240
www.adamsarms.net
Black Hills Ammunition
Dept. SAR
P.O. Box 3090
Rapid City, SD 57709
(605) 348-5150
www.black-hills.com
Advanced Armament Corporation
Dept. SAR
1434 Hillcrest Road
Norcross, GA 30093
(770) 925-9988
www.advanced-armament.com
L-3 Communications-Eotech
Dept. SAR
3600 Green Court, Suite 400
Ann Arbor, MI 48105
(734) 741-8868
www.eotechinc.com
MagPul Industries Corporation
Dept. SAR
P. O. Box 17697
Boulder, CO 80308
(303) 652-8301
www.magpul.com
The Beta Company
Dept. SAR
2137 B Flintstone Drive
Tucker, GA 30084
(770) 270-0773
www.betaco.com
This article first appeared in Small Arms Review V11N11 (August 2008) |