By Doug Olson
MK 23 SUPPRESSOR DEVELOPMENT: THE TRANSITION FROM THE COLT TO THE H&K PISTOL
Your faithful correspondent recently had the opportunity to view the genesis of the Offensive Handgun Suppressor by Knight’s Armament Company (KAC). While there is much talk about the newly adopted suppressor and its amazing performance, little is ever shown of exactly “What” makes it function so well. The new system adopted by USSOCOM was an engineering challenge of the first order, and KAC spent over $250,000 and 18 months in the development process. SAR contributor Doug Olson was Chief Engineer on the project, and I managed to talk him into telling the story himself. We hope you enjoy this SAR exclusive look not only into this amazing suppressor, but the intense process that goes into filling a U.S. government firearm procurement.
The development of the Suppressor for the Mk 23 USSOCOM Pistol was a huge challenge. The U.S. Government’s desires for the Suppressor’s performance far exceeded anything that had ever been accomplished commercially. The initial development contracts were released in 1991: one to Colt’s Firearms with Knight’s Armament developing the suppressor and one to H&K with their own suppressor design. The state of the art at that time was the Qual-A-Tec/AWC Technology produced Nexus 45 for the M1911 Colt. That 1991 suppressor only delivered approximately 18db reduction, wet. That was a long way from the 30db dry that the Government was seeking. KAC went through a 12-month development process that resulted in delivery of suppressors for the Colt OHG that in Government tests averaged 28.8db reduction with M1911 ball and 26.6db reduction with +P. The H&K suppressor averaged 22.2db reduction with M1911 ball and 15.2db with +P. That was only part of the story because the KAC suppressor yielded an incredible 36db reduction when water was added to the suppressor. It was obvious why the Government wanted to have the KAC suppressor attached to the superior H&K weapon. That was a very impressive advance in the state-of-the-art in a relatively short time frame.
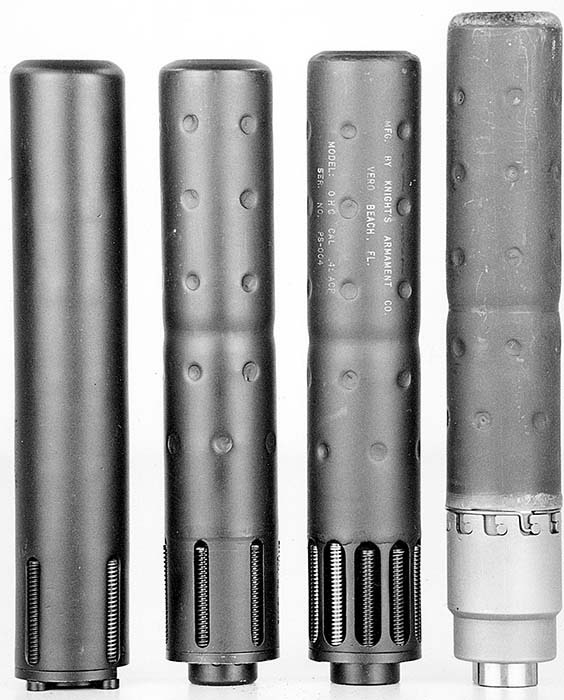
The Government initially decided that surely KAC could easily convert the design from the Colt’s Pistol to the H&K Pistol with no additional development expenditure and thus decided it would not fund any additional development effort. That erroneous situation was finally corrected and late in 1994 KAC was issued a contract to change its suppressor design to fit the H&K weapon.
The task proved to be a more formidable challenge then even KAC had anticipated. The suppressor for the Colt pistol was attached directly to the frame of the weapon. That meant that the Suppressor for the Colt pistol did not need a booster to force the weapon to function with the additional weight of the suppressor. The job was now to adapt the suppressor to a gun that required a booster, while keeping the performance of the original suppressor.
One area of the suppressor that many still do not understand is how the recoil regulator (booster) works. This is sometimes referred to as a “Nielsen device”. Based on many years of experience with the system, the following will try to explain its function. If one were to mount a conventional suppressor to the barrel of a pistol that uses a short recoil mechanism (like the M1911 or H&K OHG) one would immediately find that the weapon would not cycle semi-automatically. That is because the suppressor mass was added to that of the barrel and slide putting the total mass beyond the design limits of the gun. One could of course reduce the mass of the barrel and slide and change the recoil spring to achieve proper functioning with the suppressed pistol. The problem would be shifted to cycling of the converted pistol without the suppressor. The low slide and barrel mass would result in increased velocities of the parts and the gun would have a greatly reduced service life and increase the risk to the shooter of the slide coming off the back of the gun after firing. Neither of these situations is acceptable.

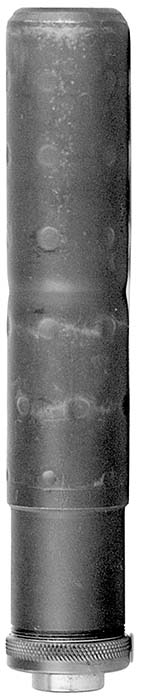
What then is the solution? It is to allow the mass of the suppressor to move independently of the barrel and slide until after the slide is unlocked from the barrel. A piston is added to the back of the suppressor that attaches to the barrel. The suppressor is thus allowed to move forward along the axis of the piston against a spring load. The propellant gasses that enter the suppressor work to apply a force to the piston head tending to drive it along with the barrel and slide to the rear while driving the rest of the suppressor forward. This “equal and opposite reaction” against the barrel makes the weapon function more or less normally.
What must happen is that the suppressor must reach the end of its stroke AFTER the barrel becomes unlocked from the slide. It is easy to imagine the shock that the barrel sees when the suppressor reaches the end of its stroke. As they say “timing is everything”. Much work was done to make sure the suppressor matches the weapon to provide for equal weapon life with and without the suppressor. Hundreds of thousands of rounds were fired throughout the development and test cycles of the weapon and suppressor.
That also means that a recoil regulator for one type of weapon may not work on another type. That was exactly the situation KAC ran into with trying to adapt the OHG Suppressor onto the smaller H&K USP and Glock pistols. The relative slide and barrel mass of these weapons was, from a dynamics standpoint, very different from that of the OHG. The Tactical pistol’s slide only lived 300 rounds when the OHG suppressor was first tested on the gun. To prevent that from happening, H&K changed the barrel threads from right hand to left hand to prevent the OHG suppressor from inadvertently being fired on the Tactical gun. H&K ran an exhaustive test and developed a special modification to the piston, regulator spring and buffer that provided proper functioning with the Tactical. KAC has built its commercial Tactical suppressors with those modifications and even with springs provided by H&K. It is of note that very few rounds fired from the wrong regulator setup can ruin a gun. It is also interesting to note that the lighter slide and barrels reduces the efficiency of the suppressor and results in a sound pressure level reduction of 3db less.
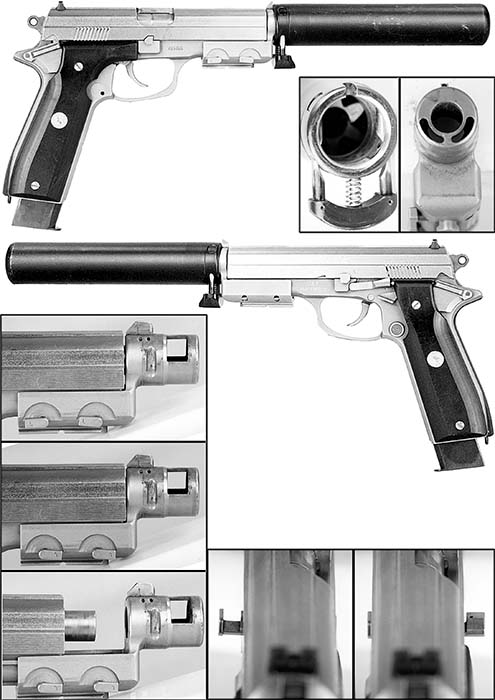
One of the problems the first generation H&K suppressor displayed was that it loosened from the barrel. When this happened bullet strikes were noted inside of the suppressor and accuracy was lost. The culprit was traced to the barrel to suppressor interface. The interface for the suppressor onto the barrel had to be changed to provide for additional stability. The first generation H&K OHG had threads at the end of the barrel with a single diameter behind the threads to support and align the suppressor. KAC had the interface changed to have two bearing surfaces, one behind the threads and one in front of the threads that provided support at both ends of the interface. Because the pistol itself was so long, H&K could not allow any more length of engagement between the suppressor and the barrel. That meant that the allowable tolerance with which the two diameters on the barrel and the two bores within the piston had to be reduced to keep the allowable misalignment at the end of the suppressor to acceptable limits. Both bores within the piston ended up with +/- .0005 tolerances. It also means that the threads no longer provided any alignment, they simply held the two parts together. An “O” ring was added within the piston that engages the front diameter on the barrel. It acts as a friction device to help keep the suppressor tight onto the barrel. The dual diameter support helps keep the alignment of the suppressor to the barrel even when the suppressor is not tight on the barrel.
When KAC first started to adapt its Suppressor for the Colt OHG to the H&K gun, one of the challenges was to make a piston for the recoil regulator to have geometry similar to the muzzle support for the Colt gun. Contrary to the initial looks, the muzzle device for the Colt gun was designed to be an effective component of the suppressor and not to be any thing special from a muzzle brake design. That muzzle device was responsible for bringing down the sound pressure level of the suppressor by a full 3 db over a straight interface.
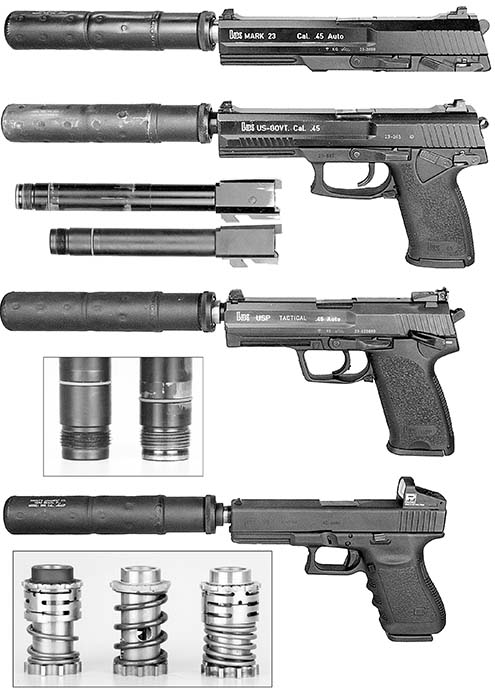
The initial suppressor prototypes were fitted to first generation H&K guns and in order to keep the muzzle brake interface as close as possible KAC tried to move the recoil regulator springs to the outside of the can. At first it was thought that four small springs would work, then six, then ten. The small diameter and short springs just too severely limited the stroke of the piston and were finally abandoned. Moving the spring to the inside of the can exposed it to all of the contamination and heat from the propellant gas but there was no option since KAC had to keep within the size limits imposed. The piston, spring and buffer designs all went through a number of iterations before a final design was found that provided acceptable sound pressure level reduction and had proper service life.
Small changes such as increasing the length of the piston where it engages the bore of the suppressor were found to be necessary to allow easy removal and reinstallation of the piston. Since the overall length of the suppressor could not increase and the stroke of the piston could not decrease, the longer piston bearing resulted in a reduction in the total length of the baffle stack. The shorter baffle stack of course reduced the net efficiency of the can. In all the baffle stack had to be shortened by approximately 1/2 inch from that of the Colt pistol to keep the system overall length within the specification. Certainly a quieter suppressor could have been delivered if the length of the can could have been increased. On the commercial side of the suppressor business limits like this are seldom imposed. Designing a suppressor to meet a Government Specification can present a great challenge.
Another problem that KAC accidentally found was that the H&K Pistol would not tolerate any interference between the suppressor and the recoil spring guide rod. The problem is that static measurements do not show the true situation because the recoil spring assembly has a secondary buffer spring. Under dynamic loading, the guide rod can protrude further from the weapon in full recoil than was obvious when taking static measurements. What happened was the suppressor on its return to battery would just tap the end of the guide rod. That tap resulted in a broken slide. Hard to believe? We thought so too, but it happened. The dynamics of this system must be understood to achieve long weapon life.
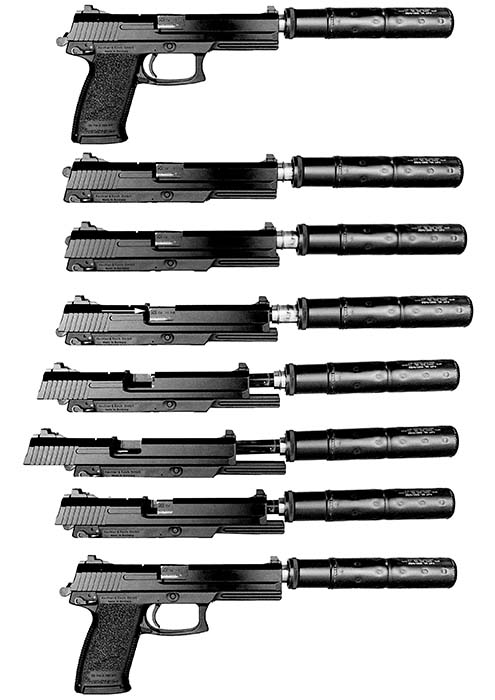
The end result, the MK23 Suppressor, has set a new standard in suppressor technology. It has been tested with more rounds than probably any other suppressor ever built. At the 1997 Suppressor trials at Knob Creek it produced an unheard of 42db reduction with a little water in the tube (wet). That is quieter than many of the 22 caliber suppressors that were tested. The problem is we know it could have been even quieter had KAC been allowed a little more volume. But the user (USSOCOM) has an excellent piece of hardware that will see service for many years to come.
Knights Manufacturing Company
Dept. SAR
7750, 9th Street S.W.
Vero Beach, FL 32968
(561)778-3700 – Phone
(561)569-2955 – Fax
This article first appeared in Small Arms Review V2N2 (November 1998) |