By David Lake
When you pick up one of your firearms, or peer at a new one though a glass pane… likely that all you’ll ever feel and see is the outer surface. This outermost finish must be visually pleasing to the eye and supremely protective to wear, age and abuse. The science and engineering of the materials and internal mechanisms of a firearm could be considered remedial when compared to the high science behind surface coatings and treatments.
To simplify, one could divide this discussion into three classes. Coating will embody any layer or film that may be directly applied–like paint. Plating will encompass the deposition of material by electrical, chemical, or other passive means. And conversion–where the substrate material is altered or manipulated on a molecular level to produce desired properties. All of these treatments and finishes serve the same purpose; to protect and enhance a firearm’s performance and appeal. But there is no clear winner among these categories as to durability, economy, or performance.
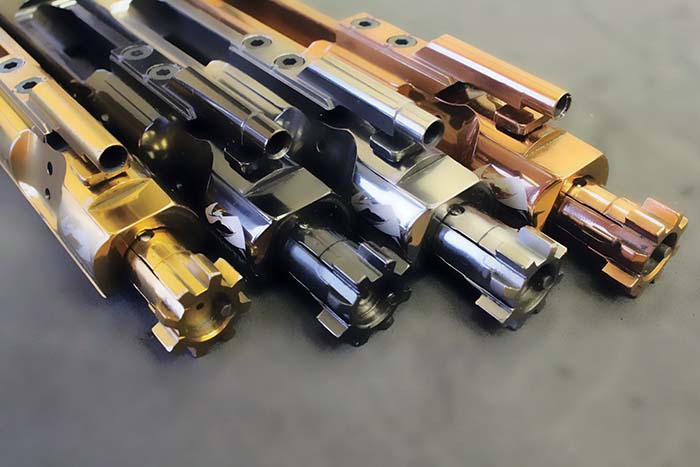
Coatings
The current crop of high-performance paint (essentially, that’s indeed what they are) comes by many names, though not all created equal. This class of paint includes the likes of CeraKote, DuraCoat and Gun-Kote (to name a few). These are usually 2-part epoxies that must be baked on. There are “air-cure” options available as well, although these are demonstrably less durable. These coatings may be applied to steel, aluminum, plastic, and wood. They require no more special equipment than a paint gun and an oven for baking if that is required. They do however ask for fastidious and nuanced preparation and execution. Should the finish fail or become unsatisfactory due to use, abuse, or wear, these coatings are quite easy to repair– just prep and re-apply. One distinct negative side-effect of all coatings of this type– they are quite thick– that is, they “build” the surface considerably when compared to metal plating and surface conversion. This can be good– take for instance, a poor-fitting war-era 1911 pistol. It may rattle and present with disappointing accuracy. CeraKote can be counted on to fill in some lost tolerance between working components. Use of these products, for this purpose is becoming common practice. When using a high-build coating prior to application, it is imperative that tight-fitting “working” surfaces are masked and protected from the impending encounters with a sand blaster and paint spray-gun. Best case fix after poor preparation, excess paint or overspray may need to be scraped off to allow reassembly. A worst case possibility– from gross negligence–if left in the corners and crevices, residual blasting media can become permanently cemented to the gun by the paint film. This condition has been observed to be the cause for undue wear and possible failure of a firearm. The lesson to be learned here and now is that CeraKote, DuraCoat and Gun-Kote should always and only be applied by an educated, certified and authorized purveyor of that service. Beware the new local startup advertising gun refinishing service.
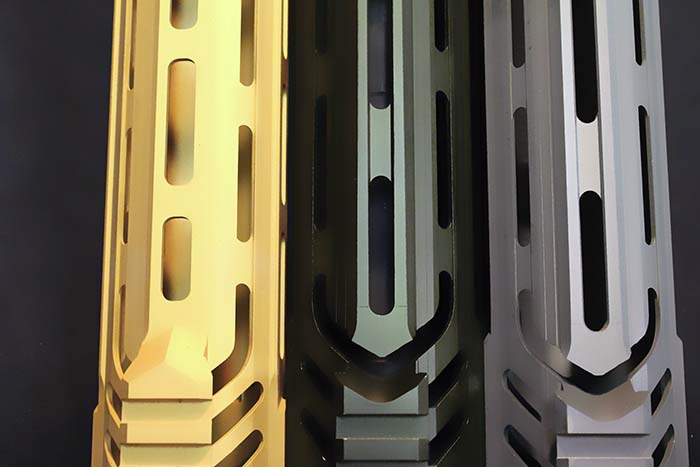
These spray-on coatings are becoming more than just a color option– some make sound, practical argument to their own favor. Among the three brands listed here, there is one that makes a coating that claims to subdue infra-red signature. Others boast operability in extreme environments– attributed to some genius stroke of science on the microscopic scale– by including Teflon, graphite, and similar polymeric compounds suspended in the paint film to reduce friction and thus may require no liquid or other chemical lubrication. All said, and aside from any practical purposes, these coatings have brought about the age of tactical fashion–an arms “image” race. There is no color combination or derivative thematic appeal that cannot be captured by the artistic application of the aforementioned high-performance paint.
There is a long-standing presence of more specialized “in-house” coatings. These were around long before the “take and bake” bottles of gun paint ever hit the market. They bear industry labels like Ro-Guard, Black Ice, and Black T (to name a few). These represent a less pedestrian class of “paint.” They are applied in very controlled conditions and with very special equipment. Some are described as a “matrix” of metal, polymer, or other solid lubricant. This type of coating is not available in a bottle to the end-user; even one with the most distinguished DIY credentials. No–these are proprietary and protected processes. One must ship a firearm to these companies to receive the special treatment. These types of coatings are typically well proven and have been tested and vetted by industry experts and armed professionals. These treatments come with certifications and guarantees and documented performance records. They promise perfect consistency and ultimate protection and performance. These are to be regarded as a step above– not mere paint. Some of the heavy-hitters in the gun business reserve some “secret-sauce” high-performance coatings for their own use only. For example, Beretta faithfully employs their home-grown “Bruniton” finish. And Heckler and Koch is extremely proud of their miracle “Maritime Coating.” These are typically black– no color options–all business.
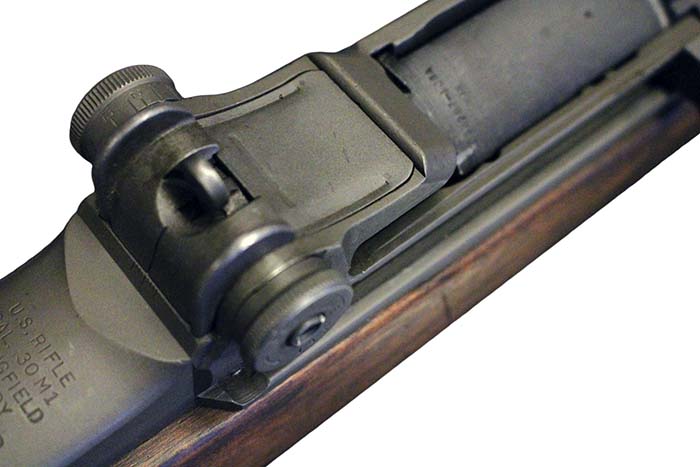
Plating
Plating is basically just a very thin layer of metal– less than a thousandth of an inch– bonded to a metal surface sub-structure. The two types of plating most abundant in the gun market and worth a mention are Nickel and Chrome. These metals are applied either by electroplating or acid deposition. In years past, Electroplate was the most common, as it was cheap and easy to execute en masse. However, electroplating is prone to some inherent problems. The uniformity of the plate can be difficult to maintain. So much variation can occur that at one extreme, a gun cannot be reassembled– on the other extreme whole areas of metal may be missed by the plating process. Also, any deformity or pitting in the substrate metal can turn into voids or pinholes in the plating. These micro imperfections leave the plated object unprotected– and susceptible to oxidation and ultimate failure of the finish. Also, electroplate finishes can be less elastic than the substrate material. So as dents and scratches occur, the plating can detach from the surface and the failed bond can propagate across the entire surface. This type of failure is evident on many older nickel plated handguns. Very few of those pistols and revolvers have kept their original nickel finishes over the last century. Electroless deposition has been found to be superior for all applications. Film thickness can be precisely controlled. Electroless plating ensures a smoother finish on the micro-scale– thus a more lubricious surface. It provides a harder finish as well. This process can be used to apply nickel or chrome directly to steel and aluminum, where electro-plating may require various layers of more compatible metals before receiving the final finish. Electroless nickel has become a standard option among Europe’s big brands for a non-black gun. Nickel presents with a subtle rose or bronze tint, while hard chrome always exhibits a pure silver color.
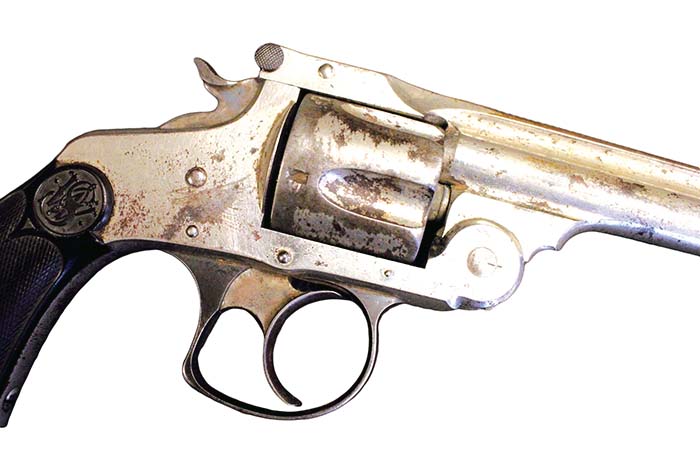
Electroless nickel and chrome have been tested to be more corrosion resistant than stainless steel– and they won’t wear or gall like stainless can. Due to the ultra-smooth micro finish high-wear or high-temp parts protected by electroless plating are far less dependent on chemical lubrication to maintain smooth operation. The acid deposition process is also compatible with low-friction polymers. Nickel and Teflon have been brought together in a composite matrix to create a very formidable surface treatment. The coating is called NP3 and the company offering it is called Robar. NP3 boasts all the advantages of the individual components– high resistance to wear, chemical attack, zero friction; and a diminished need for lubrication, etc… without any of the inherent weaknesses of those constituent components.
As good as it is, even Nickel-Teflon can be one-upped– by Nickel-Boron. It is applied in an alkaline solution instead of an acid. However it’s created, it is incredible stuff. It’s been tortured and proven in all manner of testing. Many manufacturers now offer Nickel-Boron as standard kit on their gun parts. It is becoming the standard go-to metal treatment where high load, high heat and regular abuse must be endured. It can be applied to any metal from aluminum to the hardest of tool steels. The most common use is on AR-15 bolt carrier groups. Increasingly, small parts– triggers and such are being plated in Nickel-boron. One company, Patriot Ordnance Factory, is plating their entire upper and lower receivers in this nickel-boron matrix.
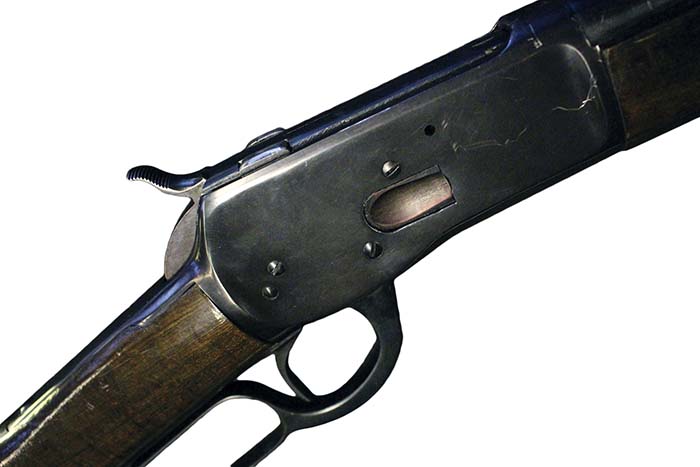
The most exotic, supreme metal-plating technologies are known as PVD– physical vapor deposition, CVD– chemical vapor deposition, and TRD- thermo-reactive diffusion. These processes can impart super abilities and attributes to a metal object. The “vapor deposition” process requires that the object to be plated be positioned in a special vacuum chamber – often referred to as reactor. You read that right- a reactor. The object to be plated is heated by induction, radiation, or direct electrical current. The material to be used as plating is introduced into this chamber as a metal vapor or gas- achieved either by chemical dissolution or laser vaporization. To clarify, an ingot of sacrificial material is either dissolved in acid or it is “blasted” from a stable solid state by a laser to create a cloud of free reactive molecules- which will find their way to, and bond with the target parts in the reactor. To be general, the compounds in PVD, CVD and TRD finishes form oxides, nitrides or carbides of metals like titanium, aluminum, zirconium, iron, and vanadium. PVD, CVD and the like can be applied without any measurable change in dimension to the original part. The micro-structure of these finishes is perfectly smooth. The breadth of features and attributes and superiority of these sorts of plating are beyond contention. These coatings make possible the modern age of manufacture- in fact the machine tools used to make guns today are treated with these coatings. Wear, abrasion, friction, and the resultant failure they cause are non-existent. Many companies offering these surface platings insist that parts never require lubrication. This is true-the substrate metal will tend to fail from fatigue or fracture before CVD or PVD plating gives up (but you should still lubricate your firearms). Many small gun parts- triggers, bolts, muzzle devices and the like are now offered with these supreme finishes. One company in particular has capitalized on new plating technology- Cryptic Coatings. They make the smoothest, longest wearing (and prettiest) AR-15 bolt groups available.
There is an extension of the technology derived from PVD and CVD processes- which deposits an atom-thick layer of carbon- that approaches the structure, and thus, the properties of Diamond. This is called DLC, or “Diamond-like Carbon.” Such a hard finish with such a micro-smooth surface is beyond good stuff- perhaps too good for most gun manufacturers. The price and prevalence of the technology would suggest this. Though still very uncommon, DLC is slowly finding its way to into our favorite guns.
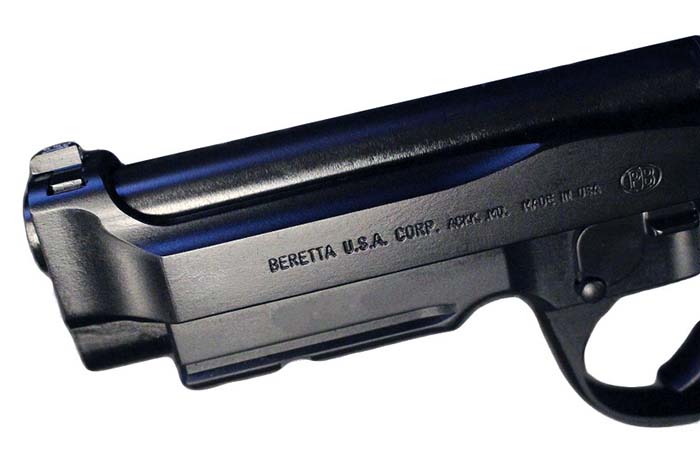
Surface Conversion
The last type of treatment to discuss can safely be called surface conversion. These types of treatments differ from coating and plating in that the substrate metal is directly involved in the formation of the protective film. Substrate metal is neither removed nor covered up. New material may be introduced and bonded with the surface of the metal substrate, but the substrate material lends itself to the final result. It becomes part of the “converted” finish. These surface conversions can be achieved during a heat treat or quench process, as found in the increasingly popular “nitride” or “nitro-carburized” processes. This sort of treatment finds its roots in the old fashioned color case hardening of steel. That old “casing” process produced a carburized skin on steel’s surface. Now with better controls and technologies, the process has been manipulated to provide even greater effect. Steel, aluminum and titanium become totally inert and very hard- even as hard as glass- by the introduction and diffusion of nitrogen (nitride) into the surface. Nitride and nitro-carburizing processes have come to be known by many trademarked names, but for all intents and purposes, they are similar enough to save further conjecture. They’re close enough to the same as it doesn’t matter.
Bluing and Parkerizing are the oldest standardized surface conversions intended to protect the surface of steel parts. Bluing is formed by oxidizing steel under controlled conditions to form black oxide, rather than rust, which is the result of spontaneous oxidation. Bluing is usually encountered as a smooth and shiny black or blue/black surface, but can be achieved in a matte finish by media blasting or etching the substrate steel first. Parkerizing is created when steel is exposed to phosphoric acid solute with zinc or manganese. Parkerizing can be a more durable alternative to traditional bluing; the reason Parkerizing has been the choice of our armed professionals for the past 75 years. Both processes are antique science, but still receive due attention from manufacturers. Bluing is beautiful. Parkerizing is nostalgic.
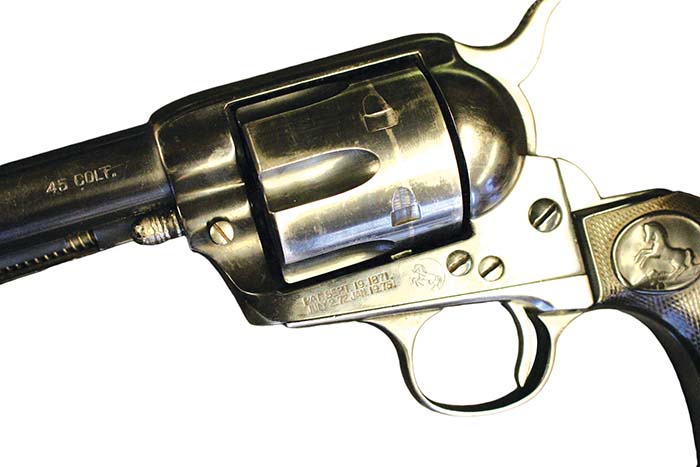
Aluminum is all too common these days, for it is the stuff that makes the AR-15. Aluminum’s surface can be painted, plated, and converted by all sorts of new methods. But the oldest way to treat aluminum may still be the best for broad application- anodizing. In its raw state, aluminum alloy will oxidize very quickly. This thin oxide layer cannot be seen, but it can be measured- it is very abrasive and exhibits high friction. So to be of any use in a mechanism, aluminum’s skin must be treated to become inert in a controlled and predictable manner. Anodizing comes in several different styles- each described by its “type” of which there are 3. Type I is regarded as a cosmetic treatment and minimally protects the surface from further oxidation and abrasion. But as of late, the chemicals used for type I have come under some scrutiny by the EPA. It is becoming more unlikely that we will encounter it on the surface of a modern gun. Type II is actually the stuff one will find in a gun shop today (contrary to what many sales pitches would insist). Type II fulfills all criteria set forth per the “mil-spec” requirements addressing anodized aluminum parts. It provides for sufficient surface hardness, reduced friction, and protects from wear and age. It is both cost effective and practical in application. Type III, or “hard-coat” anodizing penetrates deeper and builds thicker on the surface to form a thick “case” of extra hard aluminum oxide. Type III will both build on and penetrate into the surface and results in an affected case-layer up to .004” of an inch thick. Type III anodizing can actually strengthen an aluminum part and lends itself to the strongest alloys and hardest worked components made thereof. Types I and II can be expected to add less than .001” in dimension to the underlying part. Anodizing also (the most obvious reason) allows for a multitude of color to be applied to aluminum parts.
So it is with the surface of most things gun. Is surface coating the final frontier of small arms development? Hopefully not. Assuredly… no. But it’s the new colors and finishes that are easiest to spot. It’s the stuff that catches our eye and sets new kit apart from the old. Judge a gun by its cover? Absolutely.
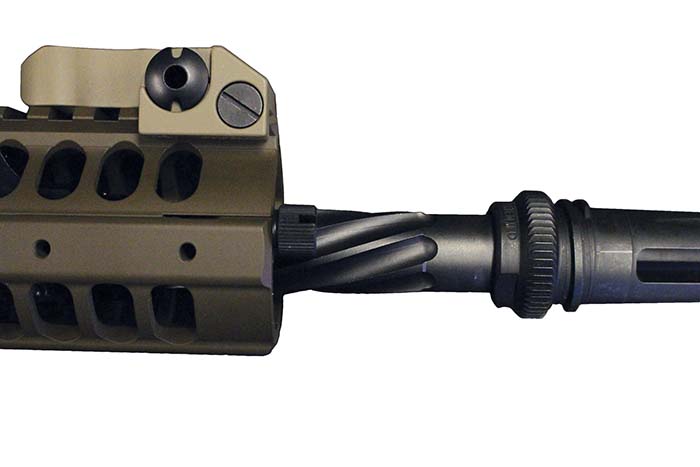
This article first appeared in Small Arms Review V20N6 (July 2016) |