By George E. Kontis, PE
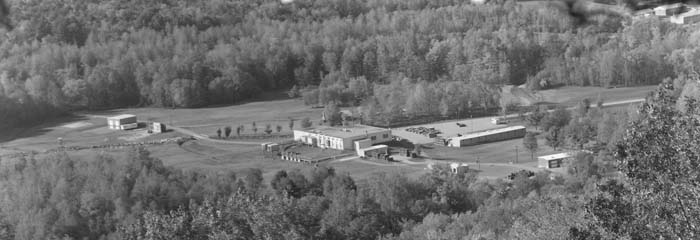
At the beginning of 1967, the Vietnam War was escalating and defense industries were responding to the military’s need to counter an increased enemy threat. Numbered among the most effective and reliable systems were the various Gatling guns produced by the General Electric Armament Systems Division in Burlington, Vermont. The war brought on an ever increasing demand.
GE weapon systems at that time were designed around two Gatling guns: the 20mm M61 and the 7.62mm Army M134 also designated by the Air Force as GAU 2B/A Minigun. Both guns and ammunition handling systems were being produced in record numbers. Internal installations of the M61 were found on most fighter and attack aircraft and a few bombers. The F4 Phantom aircraft had no internal gun systems and relied on the SUU-16 and newer SUU-23 gun pods for strafing and close combat encounters with enemy MIGs. Miniguns were finding application everywhere. Pods, helicopter pintles and internal aircraft applications were all being manufactured along with a module system used for side firing these guns from AC-47 cargo planes – a deadly system nicknamed “Puff the Magic Dragon.”
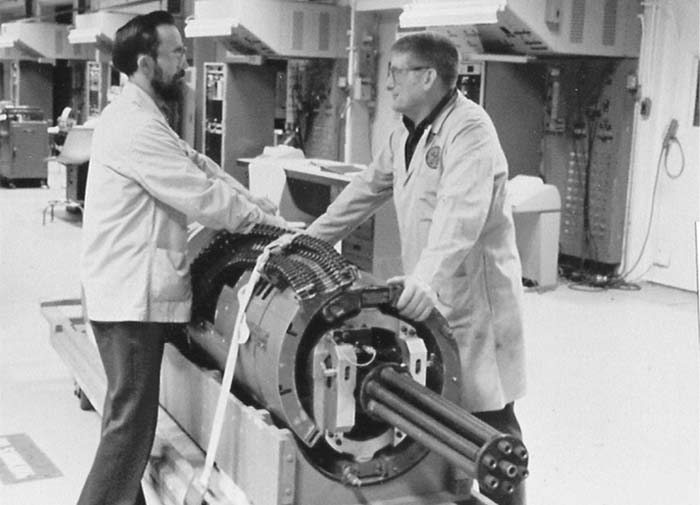
On January 3, 1967, the Monday following a huge weekend snowstorm, more than 100 new employees waited patiently outside the GE plant while the guards arranged for them to be escorted to security processing and orientation. GE desperately needed inspectors, machinists, secretaries, engineers, and other workers to support new production. Fresh out of engineering school, I waited with them, anxious to get started on my first real job.
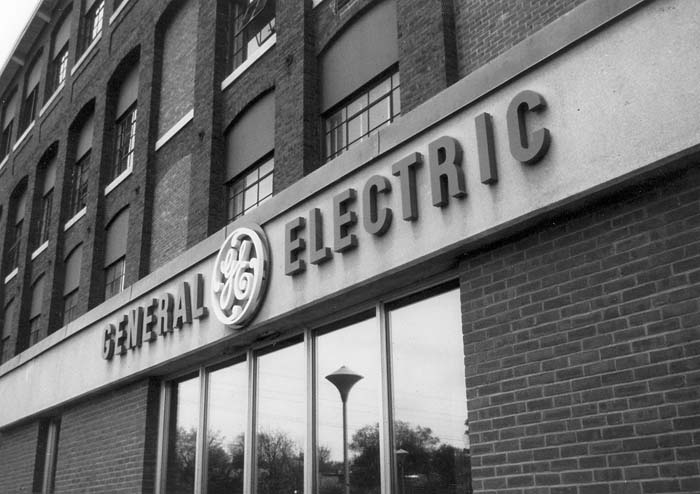
Soon after their employment, every employee in any way involved in design or testing was made aware of the most important design secret responsible for the success of these weapon systems. That secret was Round Control. GE guns were like no others. Rounds were not fed by being launched into free flight with hopes they would find their way into the chamber. There were no fired cases or links propelled by springs or ejected out of gun receivers by impact. GE guns and ammunition handling systems always had 100% complete control of the round, the fired case, and if there was one, the link. Every round transfer, every link movement, every round transport had to be under complete control at every position in the weapon cycle. Springs were permitted in these systems but were never used for positioning of rounds, cases or links.
Achieving round control in these designs was a costly and labor intensive process. In the earliest stages of design, a layout was prepared by highly skilled draftsmen, called “designers.” On their layouts, silhouettes of rounds, links, or fired cases, (appropriately called “paper dolls”) were moved to every position through the system to determine if control was maintained throughout the cycle. After the first prototype was built, technicians and engineers went through a similar ritual by moving dummy rounds through the system. Dummy rounds were rotated through the sprockets and passed by round guides to see if one could be forced out of control, or moved into a lock-up position. They tested for any condition that could potentially jam the system. Evidence that control could be lost was cause for a redesign and retrial. No live firing was permitted until these design flaws were corrected.
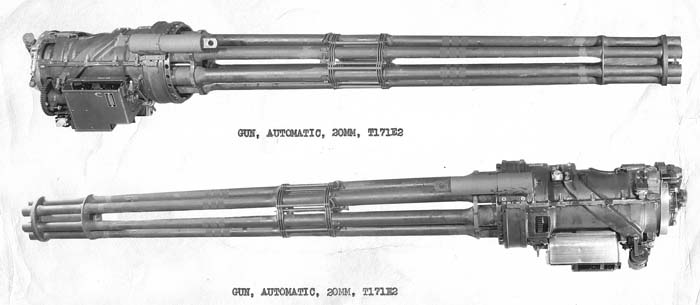
During these trials, it was inevitable to find some obscure sequence of events that might cause a round or case or link to be coaxed into a position where a jam or loss of control was possible. A debate would ensue. Could this bizarre sequence ever really happen? Was it worth the risk or would it be wise to modify to the design? In the end, the older, experienced heads would prevail. Appropriate changes were made and retested. Inspired by Murphy, GE had a corollary to the Round Control rule: In a gun system, if it can happen, it will. After the hand cycling system testing was demonstrated to keep good control of the ammunition, it was time to move out to the firing range.
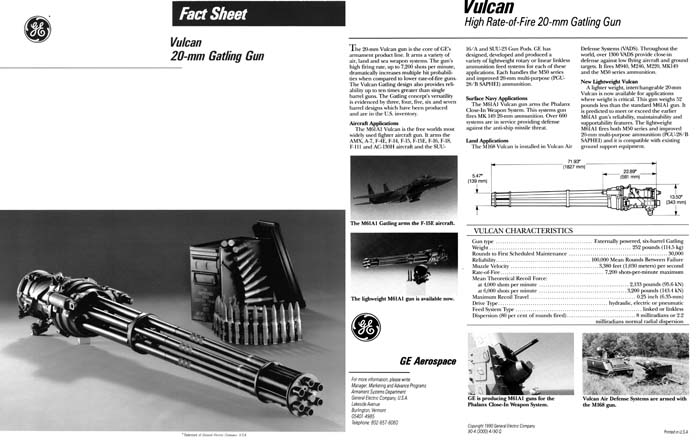
At the range, company photographers trained 16mm Fastax cameras on various parts of the system to see in slow motion, what happened when the gun was fired. Depending on the camera model, the rotating mirrors in these Fastax cameras captured motion at a rate of 5,000 to 16,000 frames per second. After a lengthy development process, the films were reviewed on special motion analysis projectors that permitted frame counting – a feature that enabled engineers to estimate the speed of the moving parts they were observing. It was always amazing to study these films. Steel parts and tightly bolted joints seemed to move as if they were made of rubber while traveling waves ran back and forth in the springs making some parts of it extend while elsewhere adjacent coils crashed into each other. Camera set-up and filming of weapon systems was time consuming and costly but was one of the only ways to indicate problems that would have gone unnoticed until a part failure or jam occurred. High speed photography was another one of the GE secrets used in the development of reliable weapon systems and was an invaluable tool in figuring out the cause and corrective action of feed jams – appropriately called “wrecks.”
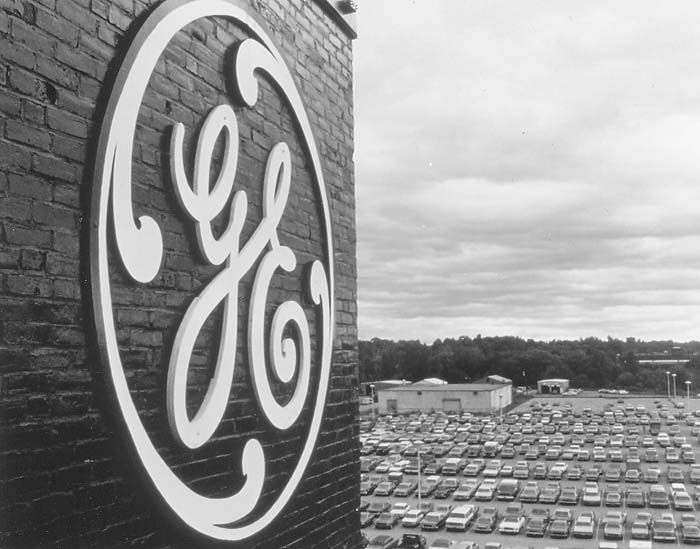
Before the development of a new Gatling gun could begin, some important design parameters had to first be decided. The maximum rate of fire achievable was fixed by the length of the round, the pressure characteristics of the ammunition, and the number of barrels. One important design parameter resulted from a decision on how the weapon would be cleared at the end of a burst. The intensive heat developed in the barrels during firing would quickly rise to a level that would cause a live round to detonate shortly after it entered the chamber. Gun powder only has to reach around 330° F before cookoff becomes a problem. Cookoff is a safety issue that cannot be tolerated and it was up to the design engineers to figure out how avoid it. GE had a simple rule: no matter how it was accomplished, at the end of each burst, all barrel chambers had to remain free of live rounds.
There were various ways to clear a Gatling gun and each one had advantages and drawbacks. Designers of the first modern Gatling gun, the 20 mm M61, solved the problem by allowing the gun bolts to cycle through a second, alternate cam within the main housing. The primary cam moved the gun bolts fore and aft so the weapon would fire as the barrels rotated. A second cam held all the bolts to the rear, in clearing mode, so rounds being fed simply went into the gun and came out without ever being fired. A solenoid actuated switching cam determined in which cam the bolts would travel. This hold-back clearing method was simple and effective but was not popular on the battlefield. In the 20mm gun pods, SUU23 and older SUU16, hold-back clearing dumped 6 to 8 live rounds overboard each time the pilot released the fire button. When dropped over Vietnam, they could be picked up by NVA or Viet Cong who used them as a principle ingredient for booby traps. Their electric primers were easily detonated with a common battery.
The 7.62mm Minigun used diversion clearing that was almost the same as hold-back clearing; only it happened a little earlier in the feed cycle. As soon as the gunner let off the trigger, the gun feeder would divert live rounds overboard so they would not be fed to the gun bolts. This system had the advantage that it didn’t require an expensive, separate cam path in the main gun housing like the M61 to keep the bolts to the rear at the end of the burst. Like holdback clearing, the rotating barrels and rotor could coast to a stop without stressing the system. The disadvantage was the same – more rounds carried out to the battlefield that never got fired.
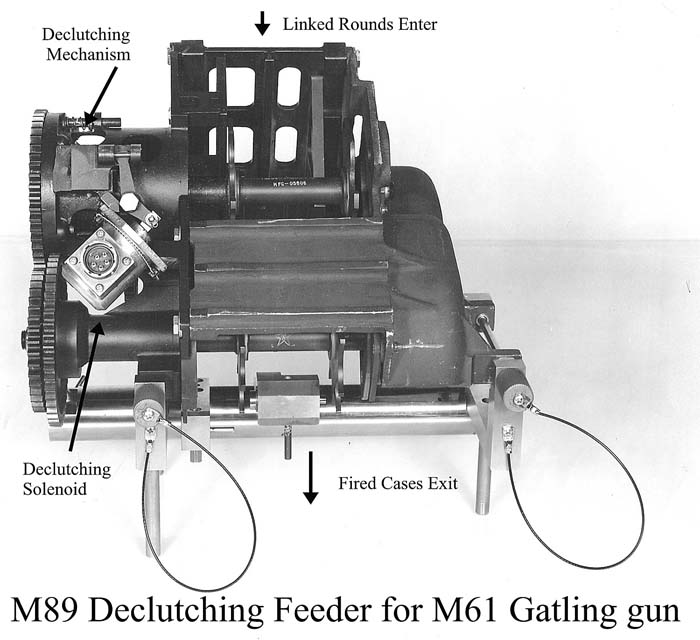
Some of the helicopter gun systems and eventually the Minigun system used a declutching feeder for clearing. The declutching mechanism was located on one of the sprockets feeding the weapon. The principal of operation was simple: when the sprocket turned it fed rounds when it stopped turning it didn’t. The sprocket was connected to a series of rotating knife blades and a solenoid activated clutch that caused the feed sprocket to stop and start.
The advantage of the declutching feeder was that it didn’t dump any live rounds overboard and left the chambers clear of live rounds after each burst. The disadvantage was that when the feed was declutched, the gun system spun free to wind down, but the entire feed system including links and ammunition was forced to come to a sudden halt. Consequently, this method could only be used on lower rates of fire since at full rate, 6,000 shots per minute, the knife blades and other parts would eventually self destruct.
The achievement of 100% round control would not have been possible without another GE secret, the linkless feed drum ammunition handling system. Here was a system that allowed for the efficient storage of ammunition in the airframe capable of reliably feeding ammunition at 6,000 shots per minute. To the relief of ground troops, the “double ended” linkless feed system retained all fired cases and unfired rounds within the system rather than releasing them overboard.
The linkless feed system may someday be remembered as one of the most ingenious article storage and delivery systems ever designed. The workings were simple, but the design and execution was complex. The basis for the system is a drum with longitudinal retaining tracks that engage the rim of the round for control and allows the rounds to travel along the rails.
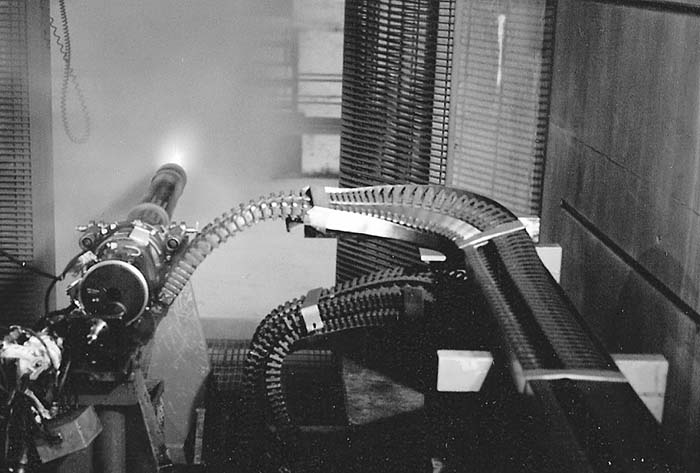
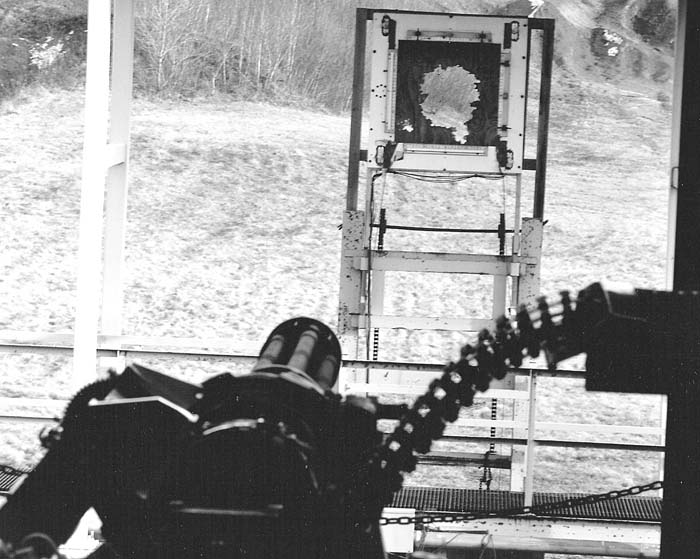
A sheet metal auger, called the helix, works as a screw conveyor to push the rounds along the tracks as it turns. Follow the path of a round in the figure as it makes a complete cycle through the system. Beginning with the round labeled “Round A”, as the drum helix turns it augers all the rounds in the drum toward the exit. When “Round A” reaches the end of the feed drum it is plucked out of the retaining tracks and moved by the scoop disc sprocket. It is then placed into a rotating ring that has retaining tracks that constrain the round longitudinally by holding it at the case rim. At this point, it’s important to note that the drum helix is really a double lead helix; meaning that at the same time “Round A” reached the scoop disc sprocket, another round reaches a second scoop disc sprocket located 180 degrees away. Both rounds enter the retaining ring at the same time, and rotate around with the retaining ring until they are picked out by a sprocket in the drum exit unit. The drum exit unit places each round into a conveyor bucket called a “conveyor element.” The conveyor elements are linked together and constrained to work in flexible chuting – a semi-flexible channel that keeps rounds or fired cases under control as they are transported.
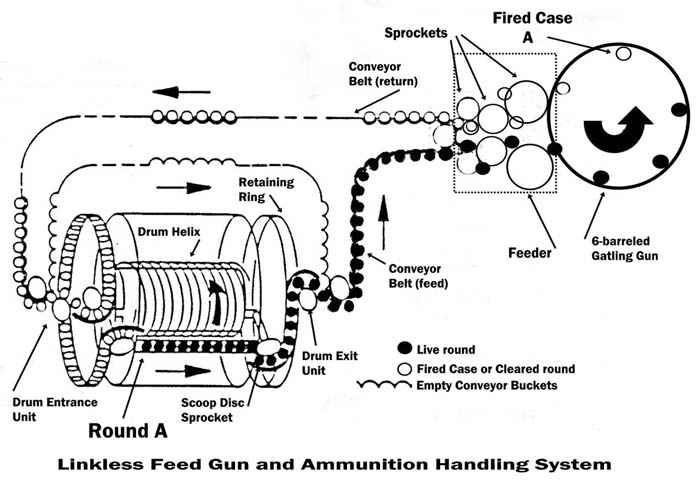
After “Round A” reaches the gun feeder it is picked out of the conveyor element and fed into a gun bolt through a series of feeder sprockets. Another secret of the GE designs is that when rounds are transferred from the control of one sliding or rotating member to another, the transfer must take place with both devices moving at the same speed. For example, feed sprockets must accelerate rounds to match the speed of the faster-moving gun bolts. Conversely, fast moving fired cases are slowed down after they leave the gun bolts to match the velocity of slower-moving conveyor elements.
At the gun/feeder interface each round is precisely fed into in the fixed extractor of a gun bolt so the bolt can chamber and fire the round. After being fired, “Round A” is now depicted as “Fired Case A” in the figure and is extracted by the rearward-moving gun bolt. “Fired Case A” passes through the unload sprockets on the opposite side of the feeder and is decelerated to match the speed and spacing of the conveyor element. The moving conveyor transports “Fired Case A” to the back side of the ammunition drum where it is picked out by the Drum Entrance Unit. Hereafter it is transported by components identical to the exit side of the drum, “Fired Case A” is returned to control of the drum helix and finally reaches the point where it started through the system as “Round A”. The linkless feed system goes from completely loaded to completely empty as rounds are fired by the gun system. Round control reigns as king in every transition and along every inch of conveyer, through the gun and back into the feed drum as cleared rounds are placed back in the drum.
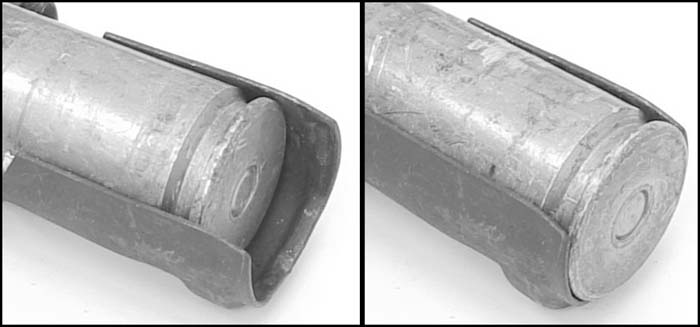
Through much of the 1960s, helicopter and fixed wing systems were armed with the 20mm M61 Gatling gun that still used linked ammunition handling systems. Linked belts of ammunition were simply pulled from a box and into a feeder where the link was stripped and the round fed, as always, under rigid control. As long as every round was properly linked with every cartridge rim properly seated in the link detent provided for that purpose, life in the gun system was good and reliability could be maintained at a high level. But every now and then, somehow back at the ammunition factory where the belts were initially linked, a round could be linked “long”. The case rim was forward of where it should have normally been causing the projectile of the long round to stick out from the belt about 1/4 inch higher than the rest.
Unfortunately, accommodation of this condition was overlooked in the original design of the feeder. When the long round entered the feed sprocket the case rim went over the top of the rim guide instead of being properly engaged by it. The round would pass through the feed sprockets long and instead of this feeding round being engaged in the fixed extractor groove in the gun bolt, it was fed out ahead of it. The round was pushed forward by the bolt, chambered, crushed a bit by the extractor, then was left in the chamber as the bolt drew back. Since the bolt extractor was not engaged with the case rim the round could not be extracted. The fun really started when the next round was fed into this bolt. The incoming round came forward and found the long round already chambered. The hydraulic motor powering the system didn’t know or care that two objects were now trying to occupy the same space and the bolt came grinding forward to create a surreal union of these two rounds. Detonation was possible and wreck of huge proportions was assured. In the aftermath the remains of the two rounds, properly de-activated, made an interesting artifact for an engineer’s desktop as an inspiration to develop a means to prevent this occurrence.
Eventually a clever engineer figured out the cure for the long round malady. It was out of the box thinking that made GE world famous in gun design business. What did he do? It was surprisingly simple. He merely redesigned the feeder so that every normally linked round was pushed forward to become a long round and then he positioned the rim guide and all of the other components for proper feeding and engagement of what were then all long rounds. Should an improperly linked long round ever come along it simply didn’t get pushed forward since it was already in position to feed normally: and it did.
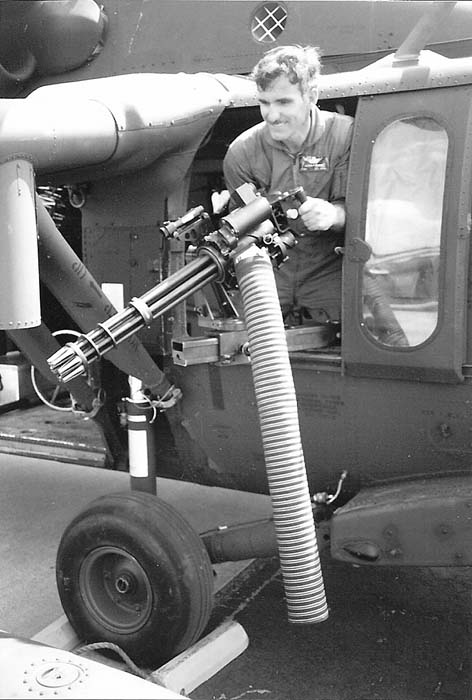
The engineering time required to lay out a complete gun and ammunition handling system was very long and laborious, but GE did it right. Engineering designers working on drafting boards made layouts showing different views of all connecting and related parts. Engineers worked with the designers making tedious slide-rule calculations and laboratory tests with bread board and brass board models to verify the integrity of the design. When the design team was happy with the job they held their first design review, passing out copies of the design layouts to a review team of engineers not associated with the program. There were several design reviews held throughout the development phase of the system with a formal design review required before full scale production could begin. Their purpose was to root out any obvious or not so obvious errors to be corrected before proceeding to the next stage in the development. With so much brain power in these meetings, it was not uncommon that major design improvements were often suggested, resulting in an even better system.
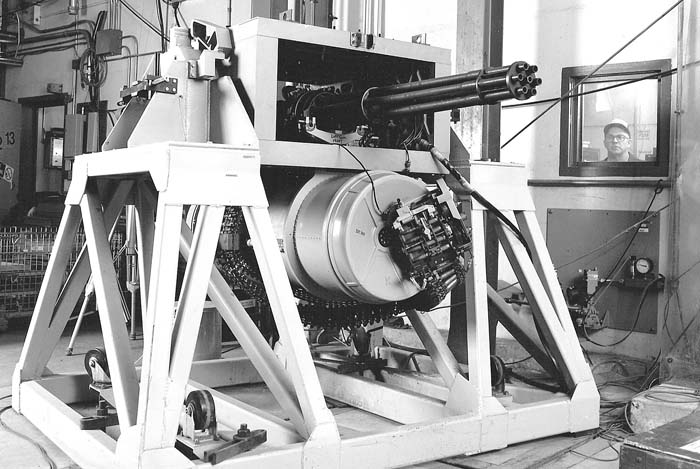
The design review team was relentless. After determining the design met the basic design criteria, they dug deeper: Could any parts be assembled backwards? Could disassembly assembly be done safely and with common tools? Were chamfers put on parts to aid in assembly? How were threaded fasteners kept from loosening? Were the hardness levels appropriate and did the design team make sure that parts of the same hardness did not slide against each other – a design subtlety found in the best mechanical designs? The design team was given a list of action items for design remediation and a redesign effort took place followed by the final design review. Only after proper corrections, testing and reviews were completed would there be approval to commit the design to production.
When a design was finally approved for production, a team of draftsmen and drawing checkers would be assigned to make the final drawings and parts lists. It was these individual part drawings making up the Technical Data Package (TDP) that played a major role in the success or failure of any design. TDP drawings were used by the Production Department for the manufacture of parts, and were the documents to be sent out to vendors of springs, castings, forgings, and other procured items. Intensive studies were undertaken to make sure that the tolerances – maximum and minimum dimensional extremes of every feature of every part would always produce components that worked together without interference at one extreme or excessive play at the other. Tolerance studies were expensive and time consuming but uncovered potential problems that, if overlooked, could turn a great design into an awful one.
Before any drawing would be released for production, the responsible draftsman sat with an experienced manufacturing engineer to review the manufacturability of the part and to establish what are known as datum planes. Datum planes are used in manufacturing to orient the part in the x-y-z planes. In general, three datum points or “targets” on the part specify the principal plane, restraining the part in the X direction, two datum targets specify how the part is held in the Y direction, and a single target is all that is needed to restrain the part in the Z direction. When the part is positioned for manufacture it is held in a fixture that touches on the datum targets. The Quality Control department uses these datum targets too, positioning the component by these targets in order to inspect the part the same way it was manufactured. It may appear odd to applaud something as obvious as this, but surprisingly few manufacturers do this and worse yet, they’re surprised when their parts don’t measure up. But GE knew how to do it right and it was another secret to their successful designs.
When the draftsmen met with the manufacturing engineer to establish the datum planes and targets, it was not uncommon for them to be in conflict. After all, the designers knew which dimensions were important to the design and had their own ideas on how the parts should be held. The manufacturing engineer, on the other hand, had the last word on how the parts would be manufactured and established the datums based on ease of manufacture. Their conflicts were known to GE management and purposely overlooked. In today’s advanced managerial courses, managers are taught that not all conflict is bad and properly handled can be a driving force for improved performance. Accepting that the manufacturing engineer had the final say, the draftsmen would think through the manufacturing of the part and establish datums and datum targets at points that made good manufacturing sense to them. In time, most of the draftsmen got so adept at this that the manufacturing engineer would only make few, if any, changes to the first draft, saving everyone time and GE money.
After guns systems were built they were trucked out to the Underhill Range, a government facility that was managed by GE. Here the systems would be bolted to the floor of a three sided weapons bay so the guns could be fired and measurements taken of accuracy, power consumption, and rate of fire. All firing was done from behind a reinforced door since wrecks and cookoffs were extremely dangerous. It should be noted that even though the gun was designed to be empty at the end of a burst, an unplanned stop in the cycle caused by a wreck can leave a live round in the chamber.
Today, companies tout their certification with the International Standards Organization (ISO-9000 or ISO-9001) to assure their customers that they are following strict quality control standards. Predating ISO was the U.S. Government quality standard Mil-Q-9858 that was enforced along with a host of other guiding military specifications. Adherence to specifications under the watchful eye of an in-house U.S. government inspector became yet another reason for the success of these systems.
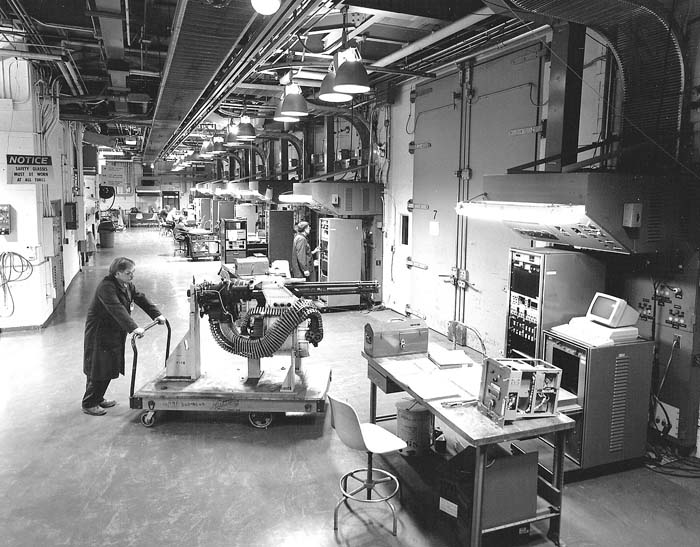
In the peak and latter years of the Vietnam War, the dedicated men and women of the General Electric Company Armament Systems Department worked tirelessly to consistently produce the finest, most reliable gun systems in the world. These were built to support American and allied fighting forces, yet almost daily these employees would be subjected to insults, heckling, and even threats from war protesters who paraded back and forth in front of the factory in organized demonstrations.
The GE Armament Systems Department was eventually sold to Martin Marietta and later to General Dynamics (GD). Today GD finds that they can do the same work with fewer employees due to the major strides made in computer aided engineering, computer aided manufacturing, high speed videos, and advances in computer numerical controlled manufacturing and inspection. With more modern equipment, GD still designs and produces advanced weapons and ammunition handling systems. Most of the Vietnam era employees retired long ago, but not before the design secrets had been passed along. GD continues to produce weapons with enviable reliability records and is well known for their expertise in the field of weapon system development.
This article first appeared in Small Arms Review V12N1 (October 2008) |