Text and Photos by Jean-François Legendre
This study, divided into two parts, is intended to describe the feed systems for U.S. .50 cal. Browning machine guns. The present Part 1 is devoted to metallic links and fabric belts. Part 2 will be devoted to the belt boxes and belt assembling machines.
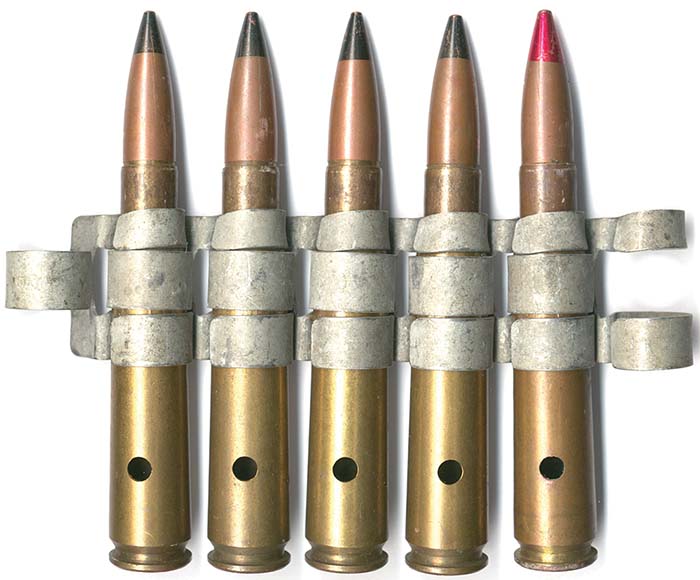
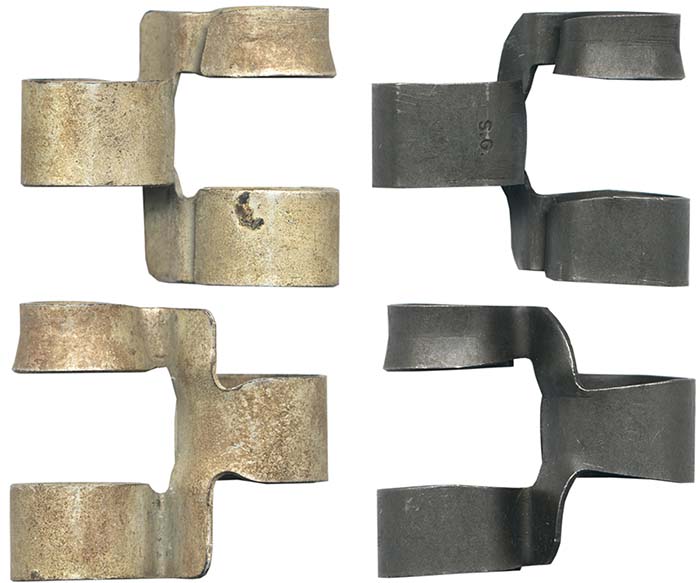
The Disintegrating Metallic Belt Links
During the Second World War, more than 9 billion metallic links were produced by U.S. companies to feed the various .50 cal. Browning machine guns used by U.S. Armed Forces on ground, on sea and in the air.
Two official U.S. documents represent the major sources of information for this study, namely the report published in 1945 by the Chief of Ordnance, Machine Guns – Development and production of metallic belt link and fabric ammunition belt and the minutes of the Metallic Belt Link Industry Integration Committee compiled up to September 1944.
In 1940, the different models of .50 cal. Browning machine guns used on ground, air and sea are fed with the disintegrating metallic link M1. It is a direct scaled up version of the .30 cal. disintegrating link that was designed at the end of the First World War to feed the Marlin aircraft machine guns.
These .50 cal. Links, M1, of standard issue in the U.S. Army were manufactured by Rock Island Arsenal and are protected against corrosion by an electro-plated zinc coating exhibiting a typical light grey appearance. These links produced before 1940 for the U.S. Army are devoid of markings. Specimens bearing the Colt logo are commercial export production; it remains unknown to the author whether these links were produced “in house” by Colt or were subcontracted.
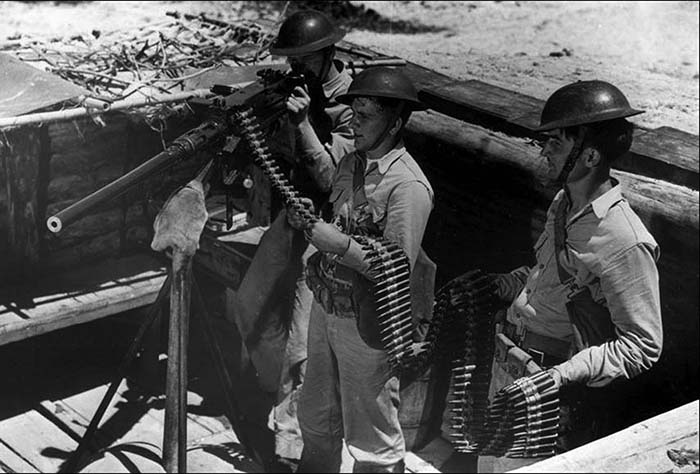
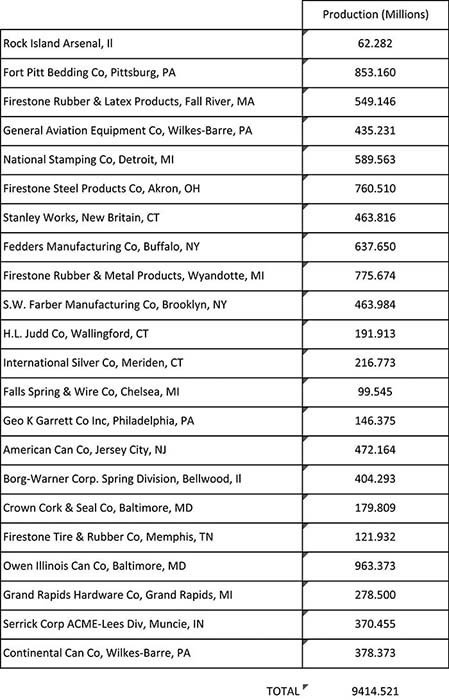
The development of a new link to replace the M1 finds its origin by a requirement of the Chief of Air Corps hereafter excerpted from his memorandum addressed to the Chief of Ordnance on April 24 1940. “In recent developments on remote control mounts and power-driven mounts for aircraft machine guns, it has been found necessary to place the entire ammunition load for a given gun mission in one belt and in one ammunition container. In order to do this in the restricted space involved with some mounts, such as tail guns and engine nacelles, considerable flexibility in the metallic link belt is necessary. The present standard link belt does not give sufficient flexibility to afford utilizing space in the most efficient manner. It is therefore requested that immediate steps be taken to materially increase flexibility in both torsional direction and in the plane of the belt. This matter should be expedited as much as practicable as it vitally affects the machine gun mounts now being given a high priority of development in the Air Corps.”
As a result of the above memorandum, a new metallic link was adopted as standard in February 1941, which almost doubled the flexibility compared to that of the previous type M1. This was accomplished by the redesign of the sides of the center loop, which are tapered; the center loop is also slightly larger in diameter than standard and the connecting ears are more rounded.
A new rust-proofing coating made of iron phosphate saturated with oil was adopted as standard for all M2 links. As the minutes of the Belt Links Committee indicate, this change in rust-proofing coating was made to eliminate the difficulties arising from the electrolytic corrosion resulting from the contact of the zinc plating with the brass cartridge case.
During peacetime in the interwar period, Rock Island Arsenal (RIA) had the exclusive responsibility of the design and production of the metallic links for U.S. Ordnance. During the sole 1940 year, Rock Island Arsenal produced 14.876 million .50 cal. M1 links, most of which was delivered to the Air Force. During 1940, several U.S. companies were asked by the British Government for the production of metallic links and therefore began building new production capabilities.
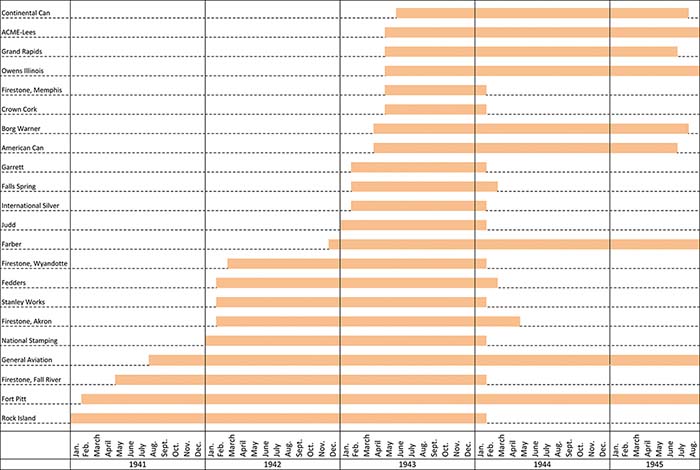
As soon as mid-1940, bearing in mind the possibility that the United States could enter the war, U.S. Ordnance anticipated a considerable increase of requirements for metallic links, essentially for Air Force use, and therefore prepared for procurements from private companies. In June 1940, the Fort Pitt Bedding Co. of Pittsburg is the first private company to be notified of a contract by U.S. Ordnance for production of .50 metallic links. During 1941, another three private companies began delivery of .50 metallic links to U.S. Ordnance namely: the Barnard Aviation Co. (which later became the General Aviation Co.) in Wilkes-Barre, Pennsylvania, the Firestone Steel Products Co. in Fall River, Massachusetts and the National Stamping Co. in Detroit, Michigan.
In December 1941, following the entry of the United States in the War, the mobilization program scheduled a need for 3 billion .50 cal. links for 1942 and 5 billion for 1943. In order to fulfill those considerable requirements, six new private companies began production in 1942 followed by 12 others in 1943.
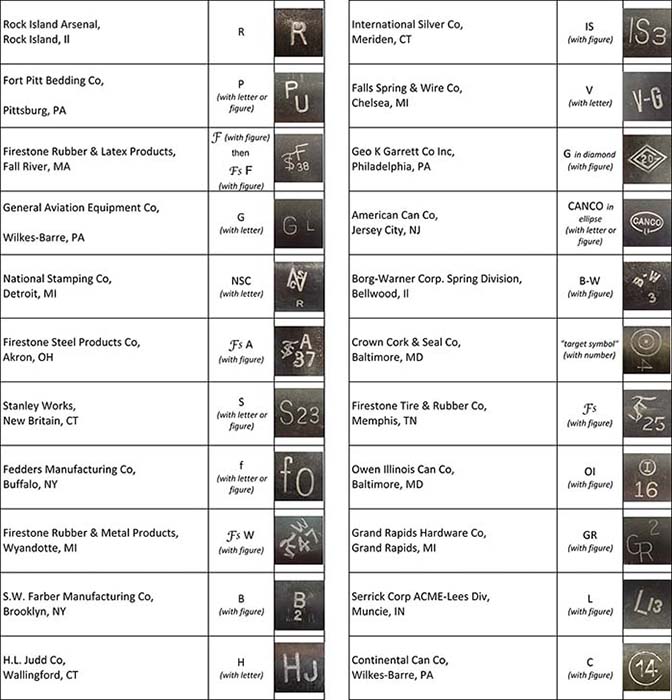
The salvaging of .50 M2 links was proposed and tried in early 1943 when the supply of links was acute, but because of the unknown factors in the previous history of the links necessitating a 100% inspection, and the cost involved in refinishing and packing, the project was abandoned. At that time, the suggestion for making Grade A and Grade B was also offered, but was not given serious consideration because of the number of complications it would have introduced in the supply program.
It was in September and October 1943 that the maximal full production output of all 22 factories involved in the production of .50 metallic links was reached. At that period, the cumulative monthly rate of all 22 factories reached 522 million links.
The coordinated production of the 22 factories, the organization of raw material deliveries, the development and procurement of machine tools, the harmonization of standards and quality control, all these key requirements have been possible through the Metallic Belt Link Industry Integration Committee. This committee, composed of representatives of U.S. Ordnance and the various manufacturers and sub-contractors, was created in July 1941.
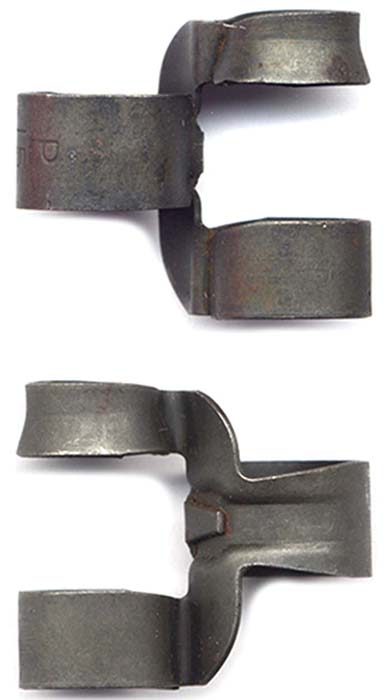
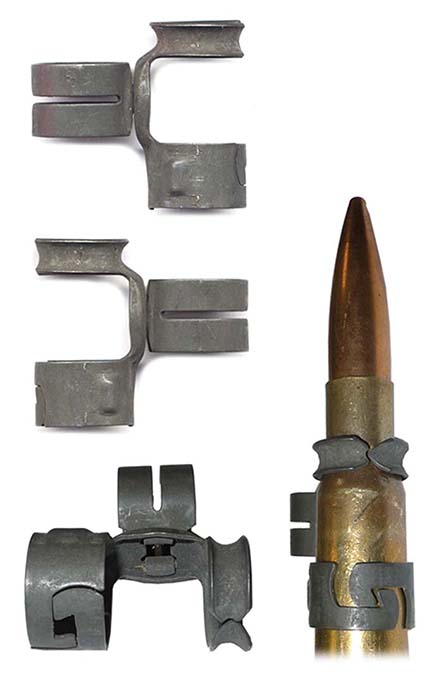
In October 1943, according to the amount of links already in stocks and the actual consumption rate by combat units, the expected production requirement for 1944 was reduced down to a total yearly production of 2 billion only. This reduction in the production requirements drove early 1944 to the complete termination of production for 13 out of the 22 factories and a large reduction of monthly production rate for the remaining 9 factories. Mid-1945, after the close of the hostilities in Europe, 4 more factories stopped production. In August 1945 with the Victory over Japan, only 5 factories were still in activity. From January 1941 to August 1945, a total of more than 9.4 billion .50 cal. Browning links had been produced.
M2 links bear the manufacturer marking associated with a number or a letter, which indicates the machine tool used in order to precisely locate the faulty machine in case of non-standard production.
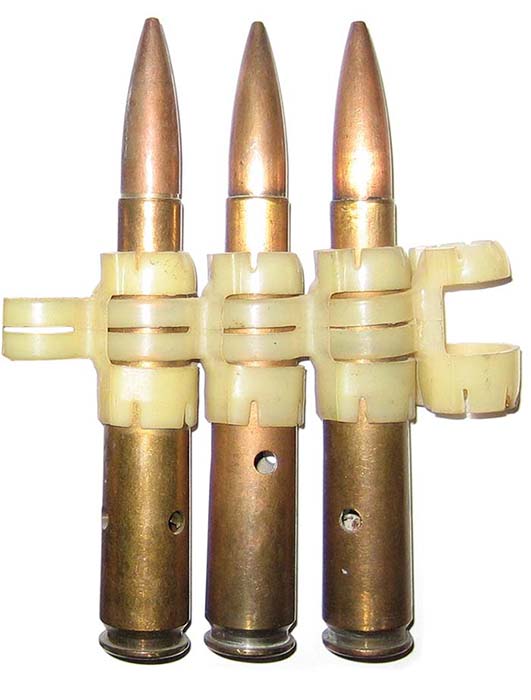
Experimental Links
The further development of experimental links is described in much detail in the Record of Army Ordnance Research and Development published in 1946 from which the following information is excerpted from.
Although the M2 link was officially adopted as standard on 20 February 1941, and was considered acceptable by the Army Air Force, the link development program was continued in order to keep abreast of the rapid development of combat planes by producing a still stronger and more flexible link.
The development was conducted along three general lines. The first deals with the modification of the M2 link and development of other one-piece designs in an attempt to minimize the modifications in existing manufacturing processes. The second approach deals with the development of a two-piece link in which the connecting loop was joined to the bridge of the body loop by a swivel joint, which accomplished greater strain flexibility than is practicable with a one-piece design without sacrifice of the required strength. Finally the third approach was the investigation of the feasibility of employing materials other than steel to determine whether the advantage of reduced weight and increased resistance to corrosion could be obtained whiteout sacrifice of strength and other characteristics of the steel links.
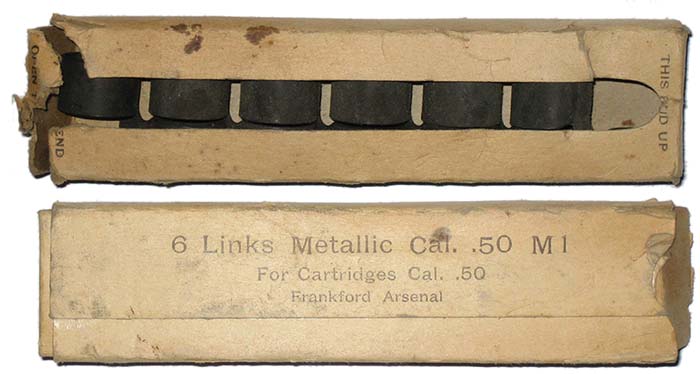
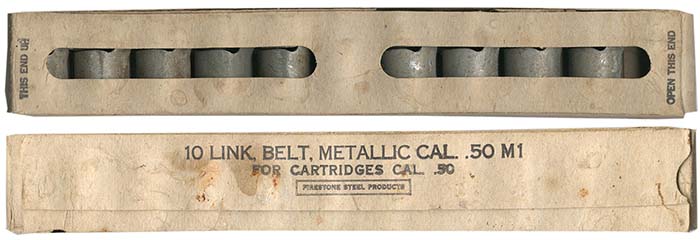
A considerable amount of study was given to the improvement of the M2 link that resulted in at least 28 experimental models that retained the essential characteristics of the standard link with simple modifications. The final result of the study on one-piece links was the development of the T43 design with increased resistance of the center loop obtained both with the addition of a tab at the end of the center loop to prevent it from opening up under load and also with the addition of stiffening ribs. This test model was the precursor of the model later adopted as M9, which is still nowadays the standard link for modern Browning weapons.
The third approach based on the use of non-steel materials involved both plastic and aluminum links. Experiments with plastic links that might generate a saving in weight of 60% or more and an entire freedom from corrosion had been conducted over a period of more than 4 years and were still in progress after the close of the Second World War. Several different companies dealing with plastic materials patented various plastic links designs. Among the plastic materials investigated, the most promising was determined to be DuPont FM-1 Nylon as used for the T37 series of links. The major drawback of plastic links at the time was the impossibility to find plastic materials that would stand the extreme climatic conditions specified (both low and high temperatures).
Aluminum was also considered in an attempt to reduce weight and improve resistance to corrosion. However, the lower mechanical properties compared to steel would require an increase in thickness of stock that would nullify any saving in weight. No surviving specimen of WW2 aluminum links has been observed so far by the author.
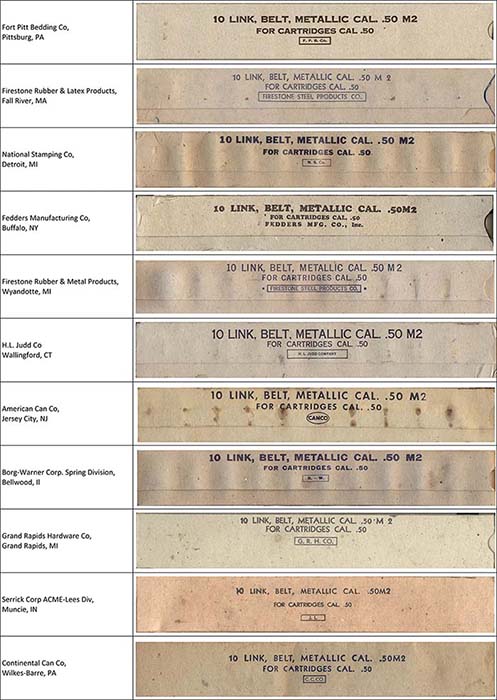
Packing of Links
During the early 1930s, the first M1 links were packed by 6 pieces in a chipboard carton according to the design of the manual linker type L-56 for which six cartridges are simultaneously inserted into links.
In 1935, the Link Loading Machine Cal. .50 M2 was adopted as standard. This linker enabled the simultaneous introduction of 10 cartridges into links. Therefore, a new 10-link chipboard carton was adopted also. These 10-link cartons bear printed on the chipboard the designation of the content as well the manufacturer (either in abridged or in full text); the cartons are undated.
As of 1942, the approved packing for .50 M2 links was 1,000 pieces in 10-link chipboard cartons. The 100 individual cartons are wrapped in two sheets of waterproof paper, and then packed in an exterior container made of either a fiberboard box or a wirebound wood box. An exterior container made of a nailed wood box was also approved at that time but not used by link manufacturers.
By end of 1942, the use of the two waterproof sheets was abandoned in favor of a unit waterproof envelope. The packing used at this time was not an overseas pack because 90% of the links were being used in this country to make up ammunition belts. In May 1943, after some experience in the handling, storing and reshipping of the links packed in fiberboard boxes, the use of this box was discontinued because of its poor stacking properties and low wet handling strength. Therefore for the last half of 1943 and first half of 1944, all the facilities were using wirebound boxes.
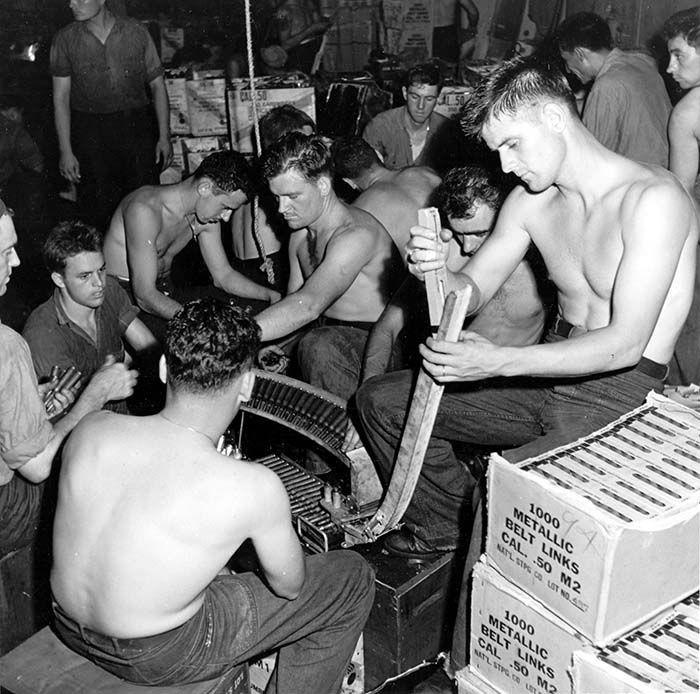
At a production rate approaching one half billion links per month during the last quarter of 1943, this meant that approximately one half-million wirebound boxes were needed monthly. Because of the critical supply of veneer and lumber at this time, and in view of the many other demands for the wirebound box industry, the shortage of wirebound boxes loomed large. A reuse program was set up whereby wirebound boxes were returned from the ammunition belt assembly plants to the link manufacturers.
In March 1944, the Navy Bureau of Ordnance requested that all links to be consigned to the Navy be packed in an approved overseas interior pack and a nailed wood exterior box. At this same time, the method of packing links for domestic shipping was also improved in anticipation of long term storage. A higher quality waterproof envelope was used and openings were properly sealed with waterproof adhesive.
The packing for the Navy consisted of 10 links per chipboard carton, 50 cartons per intermediate fiberboard carton that was then wrapped in a greaseproof paper and dipped in wax; then two of these intermediate packages were packed in an exterior nailed wooden box. This form of packing was both moisture and vapor proof and was designed to withstand the extreme conditions encountered in amphibious landings. From the middle of 1944 on, the total production of three facilities (Fort Pitt Bedding Co., Acme-Lees Division and Grand Rapids Hardware Co.) was packed this way for the Navy.
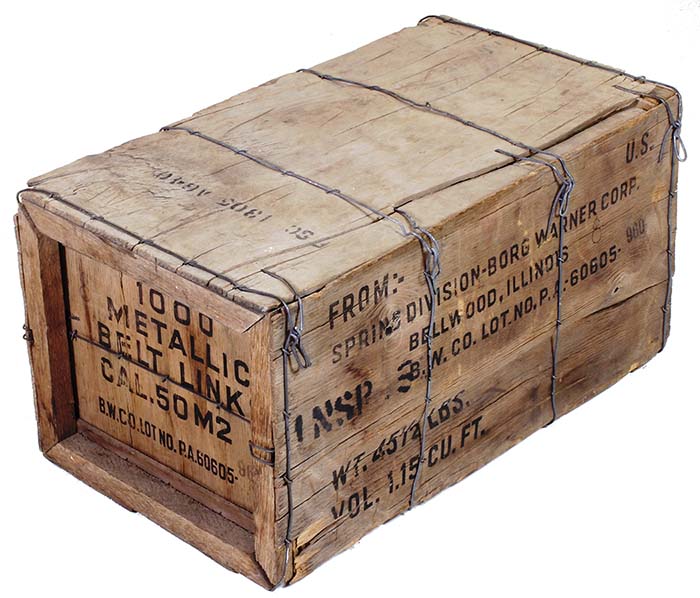
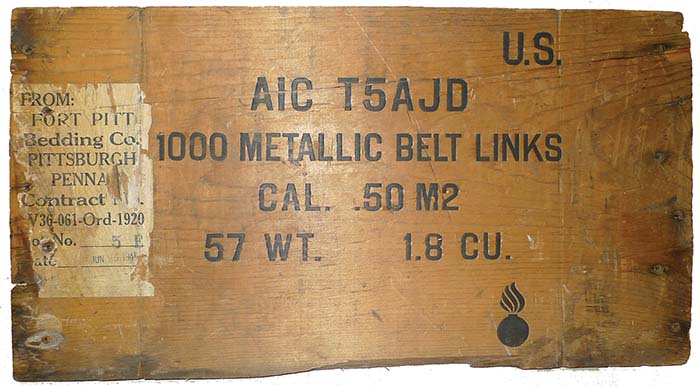
Fabric Belts
The earliest water-cooled M1921 Browning machine guns for ground use were fed with 100-round fabric belts. The belts are devoid of starter tang and are accommodated in a wood chest that can be fastened to the weapon mount. The design of the fabric is based on the contemporary .30 Browning fabric belts. With the adoption of the M2 Browning machine guns by U.S. Forces in the 1930s, metallic links became standard and fabric belts remained only offered for export.
At the end 1942, while several private contractors were tooling up for the mass production of M2 metallic links, the Metallic Belt Link Industry Integration Committee anticipated that the production objectives of metallic links M2 for 1943 could probably not be met according to delays in the procurement of certain machine tools and shortage of steel sheets. The Bureau of U.S. Ordnance then initiated a study in order to replace metallic links by fabric belts for all uses other than for the Air Force, which required exclusively metallic links. Experiments were very quickly conducted on the basis of a 100-round fabric belt manufactured by Russell Manufacturing Co. and already exported to Great Britain. This export 100-round fabric belt bears at both ends six fabric pockets stitched closed in order to play the role of starter tangs.
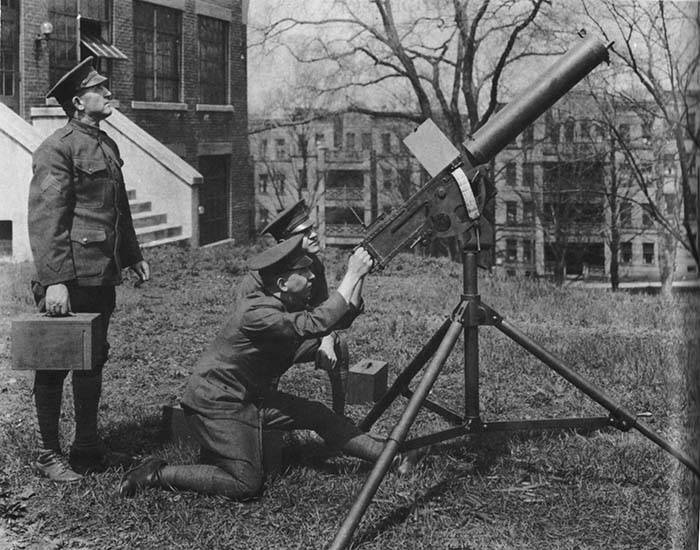
On 8 January 1943, a 100-round fabric belt was adopted as standard under the designation M7. This belt is completely made of fabric and is fitted at both ends with fabric connecting loops. These connecting loops, patented by The Russell Manufacturing Co. with U.S. Patent number 2,422,898, enable to assemble two fabric belts together. This feature fulfilled the specific requirement of the Anti-Aircraft Artillery Board that needed a 200-round belt assembly to be fitted into the large Chest, Ammunition, Caliber .50, M2.
The disposable box M2 with a nominal capacity of 105 rounds mounted on metallic links proved capable of accommodating without difficulty a fabric belt with up to 110 rounds. Accordingly, during the first months of 1943, the capacity of the M7 belt was increased from 100 to 110 rounds, while keeping the M7 designation unchanged. In September 1943, all metallic link factories reached nominal production rate therefore enabling to fulfill all requirements for air, ground and maritime uses. The M7 fabric belt was then reclassified as “Limited Standard” and the metallic links M2 became of standard issue for all U.S. .50 Browning weapons.
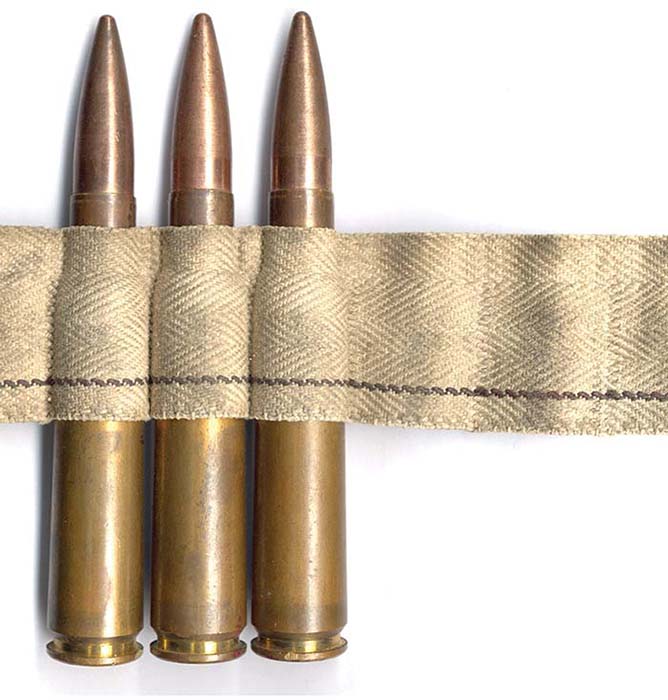
Unlike what is sometimes written, fabric belts were not reserved for training purposes only in the continental United States. Ammunition belted on M7 fabric belts were definitively used during combat in Europe. These fabric ammunition belts are sometimes seen in period photographs and are sometimes recovered still nowadays in combat areas of North-East of France on the border with Belgium (Battle of the Bulge) and with Germany (Battle of Alsace). No surviving specimen of the early 1943 M7 belt with the original capacity of 100 rounds has been observed so far by the author.
Most M7 belts were made out of green fabric and only a small quantity were manufactured out of white fabric. The belt pockets are numbered in black ink every 25 rounds with numbers ranging from 25 to 100, while the first pocket is numbered “1” and the last “110.” The belts also bear in black ink the designation of the manufacturer, the month and year of production and the reference to the U.S. patent No. 2,061,072 granted to The Russell Manufacturing Co. in 1936 corresponding to the fabric weave.
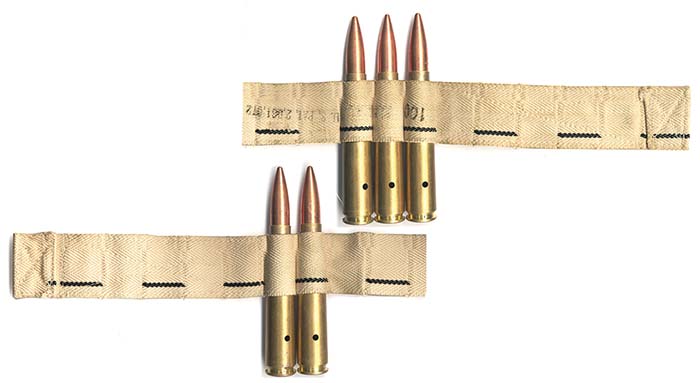
Production of 110-round M7 fabric belts was shared among 7 factories, which on the other hand were also involved in the production of .30 Browning fabric belts. From April to September 1943, a total of more than 8.6 million M7 belts were produced, which means that these fabric belts are by any means not scarce. It seems that only a small proportion of these millions belts was actually loaded with ammunition and nowadays the vast majority of the M7 found are still in new unissued condition, sometimes still rolled and fastened with a small piece of string, as out of the belt weaving factories. Sometimes the M7 fabric belts were recycled as trousers’ belt or sewn as reinforcement ribbons in sleeping bags.
(Look for Part 2 in the next issue of Small Arms Review that will be devoted to the .50 cal. belt boxes and belt assembling machines.)
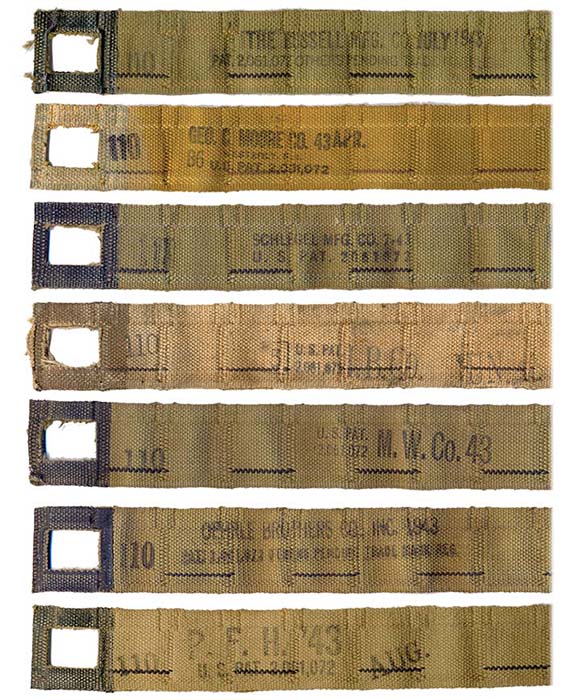
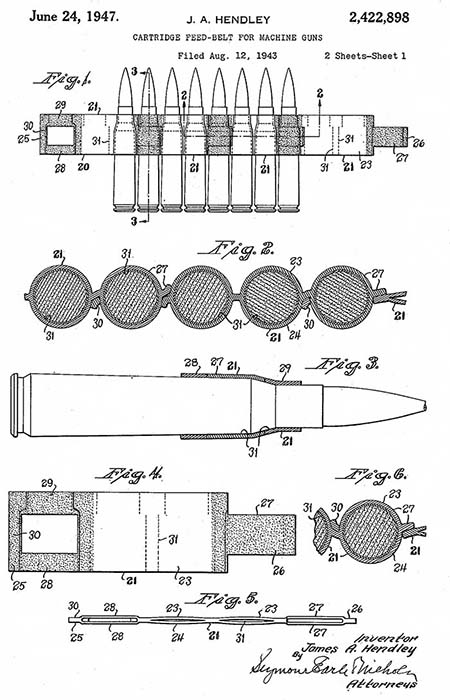
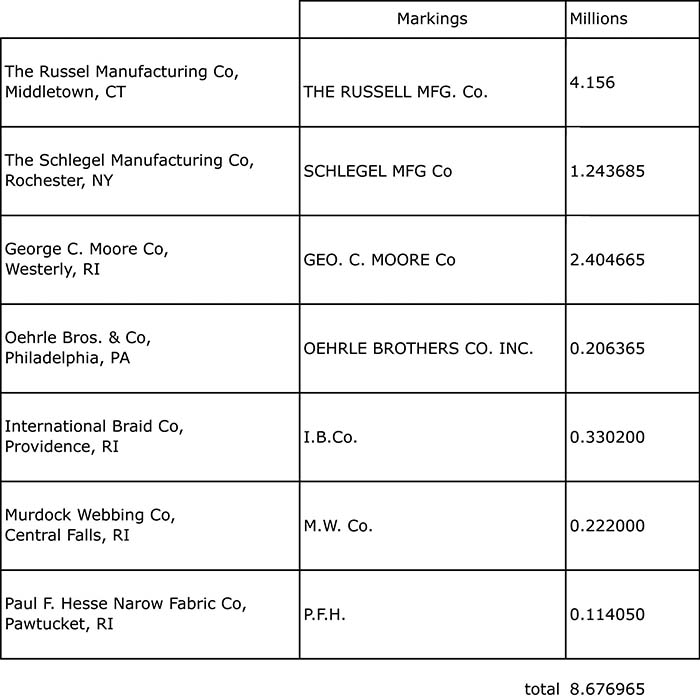

This article first appeared in Small Arms Review V17N4 (December 2013) |