By Tracie L. Hill
For years Thompson collectors have debated the history of when and who manufactured the various drum magazines. However, never before now has definitive information been available for historical review. This article, in part, is based on letters and correspondence between Auto-Ordnance personnel and the various concerns manufacturing the drums. The later discussion on production during World War II is based on information from the National Archives.
At this point it is important to explain a few definitions of terms used in this article. First, the word “mismatched.” This term refers to drum magazines with covers and bodies that are either not matching in serial number or have different manufacturers’ parts. As an example, a United Specialties cover with a Crosby body assembly would be considered a mismatched drum. Second, a “transitional drum” is a drum which has a body and cover assembled by the same manufacturer that is using the remaining parts of one production in the beginning of another. As anyone who has ever worked in a production facility knows, you try to use up the remaining inventory from a prior production run prior to using new production; this is the most economical use of leftover stock. For the collector, these are very important drums as they can tell the historical order of various production runs.

(West Point Military Museum)
Originally, the first ammunition feed device to be tried was a cloth belt. However, after several trial mechanisms failed to prove reliable, the Colt Model of 1911 box magazine was pressed into service. Both General Thompson and Theodore Eickhoff were very familiar with these magazines from when they worked together in the US Army Small Division. General Thompson was in charge of the development of not only the .45 caliber cartridge, but also the trials for the new Model of 1911 Colt service pistol.
The first Annihilator I, serial number one, was designed to have “wings” on the receiver to handle several Colt magazines in a line. Later, the engineers designed the twenty round box magazine for serial number one. The first design required the use of an adaptor to hold the box magazine in position.
Oscar Payne was assigned the task of designing a larger capacity magazine. After several initial designs that were unsuccessful, he created the “Spiral Drum Magazine.” The first of these Spiral Drums used a removable crank handle to wind the drum spring. This design was quickly abandoned in favor of the now familiar winding key. These very early designs, both failures and successful, were in all likelihood made in the Auto-Ordnance Engineering Department’s own machine shop at 6536 Carnegie Ave., Cleveland, Ohio.
However, once a successful design was finalized, they turned to a local company to help with the manufacturing of production quantities. The company was John’s Machine and Stamp Works Company in Cleveland, Ohio. With John’s Co., Auto-Ordnance’s Engineering Department went about the tedious and time consuming job of producing drawings for each part of the C and L drums. From these documents were created the tooling to manufacture the XX box, C and L drum magazines.

All of the formed metal parts were made by John’s Co. The rotor springs were ordered from Wallace Barnes Co., Bristol, Conn. Wallace Barnes supplied the springs to Auto-Ordnance clear through to United Specialties production in 1939.


By the end of November 1920, the partnership with John’s had produced 205 sample C drums at a cost of $871.17, 200 sample L drums at a cost of $180.69 and 506 sample XX box magazines at a cost of $327.70. The cost of the tooling for these samples totaled $48,994.28. This included 14 sets of dies to produce the XX box magazine, 40 sets for the C drum and 36 sets for the L drum. Some of the sets of dies were used to produce common parts for both the C and L drum. For example, the winding keys, rotor retaining clip, body and face plates, etc, are common to both drums. Later, John’s Co. would also be tooled to produce the felt pad oiler system for the TSMG.
It appears that John’s Co. was also assembling the drums after forming of all the individual pieces. This assembly was being closely overseen by the Auto-Ordnance personnel to assure quality. The first drums produced by John’s were of the type found in the accessories that accompanied Model of 1919, serial number 17. These drums are a bright blued finish with the serial numbers stamped into the face plates and the rotor. Markings for instructions are vibra etched into the face plates.
The second version is the first drums to have stamped information on the face plates. The rear face plate contains the winding information and has a stamped “No.” location for the etched serial number. These were the drums available when Colt’s began production of the Model of 1921. According to a report by Theodore Eickhoff, dated January 4, 1921, 4,000 of each drum (C and L) have been produced to date.
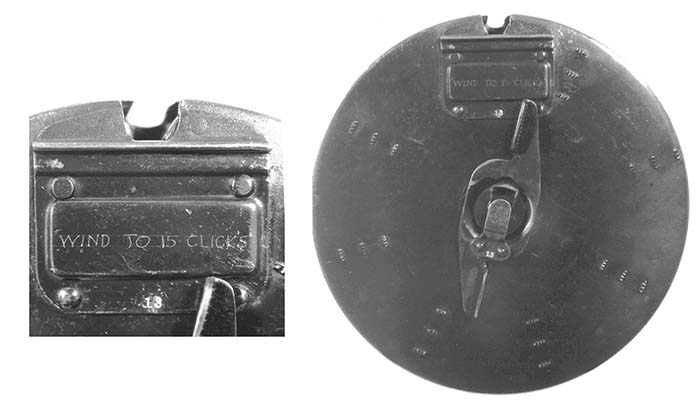
It is at this point that the John’s Co. drums start to have the dull blued finish applied to them. This is a second generation John’s C drum, but with the grit blast finish applied by Colt’s prior to blueing. With this grit blasting, any information of the face plates that was not deeply stamped would not be visible. Therefore, the etched information was not used and the winding information was still stamped into the back face plates.

As production of the guns began, the winding information is still on the back side and the serial numbers are now restarted and stamped, such as serial number one. As production continued, some time within the first hundred drums, the winding information on the back face is moved to the front face and patent and address information for Auto-Ordnance is stamped into the rear. The surface of the drum is still grit blasted and blued. The serial number (which is actually an assembly number only) is stamped into the front and rear face plates.

It was costing Auto-Ordnance approximately $5.54 each to make a C drum plus an additional .85 cents for Colt’s to grit blast and blue. The L drums were costing $3.54 each plus the additional cost of .65 cents for Colt’s work. So from these new records it seems that all variations of the C drum were produced by John’s Machine and Tool Co.

There is still the question, “How many were made?” The highest number seen on a C drum to date is about serial number 5,000. But, this does not mean that only 5,000 were made. In a letter from Oscar Payne to Auto-Ordnance he states that, “…if a drum failed to pass final inspection we did not produce a new C drum with the same number as the drum that was rejected. We simply threw it away and made another.”



The real question should be how many still exist? It is not known for sure but keep in mind that 535 C drums were shipped in the first ten weeks of production shipments (ending 6/11/21). Most of these went to the IRA. Thus, assuming 5,000 were made, this means that 11 percent are already outside the US.

This article first appeared in Small Arms Review V9N2 (November 2005) |