By George E. Kontis PE
The Model 1896 Broomhandle Mauser pistol saw extensive use in World War I. It was reliable, accurate, and very popular because it was easy to maintain, requiring no tools for assembly or disassembly. Much of the design success was due to the fact that there were few parts, and only one of them was a threaded fastener. A single screw, used to secure the pistol grips to the weapon frame, has today become the source of an urban legend. The story has it that Paul Mauser reluctantly used this screw because he could not find any other way to fasten the wooden grips to the pistolโs frame. Reportedly, this so frustrated Mauser, at design completion he sat down and cried.
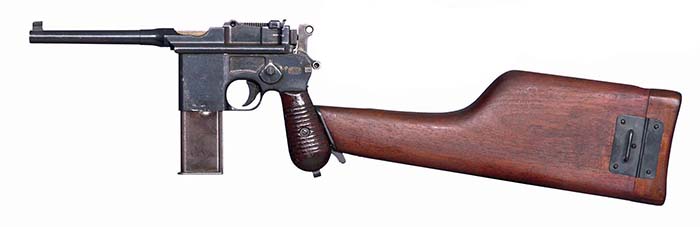
Closer to the truth is that it was not Paul Mauser, but three brothers working in his Oberndorf factory who designed the Broomhandle Mauser and it is not likely there were any tears shed over this hot selling product. In any event, it makes for a good story and emphasizes some important points. The first being that over one hundred years ago, some clever gun designers led the way by demonstrating they could design a gun that requires no tools, no threaded joints, and no fasteners. Whatโs more, these designers had already learned there were very valid reasons to avoid threads of any kind when designing a gun. More than a hundred years later, it seems weโve learned very little from the Mauser example.
Threaded fasteners are a handy way to connect parts and threaded joints make it easy to connect parts together โ so what is the big objection to their use? Threaded fasteners are unreliable. Vibration from firing shakes them to the point where they loosen and sometimes fall completely out. Threaded joints are problematic because of the motion between the male and female threads during firing. They look and feel tight under static conditions, but during firing, high shock loads cause movement in the joint. Sometimes you hear it described as โrocking on the threads.โ Care must be taken in the design of the threaded interface so this doesnโt happen. The tight fit between threads in gun systems is much less rigid than you might think, and can and does cause problems.
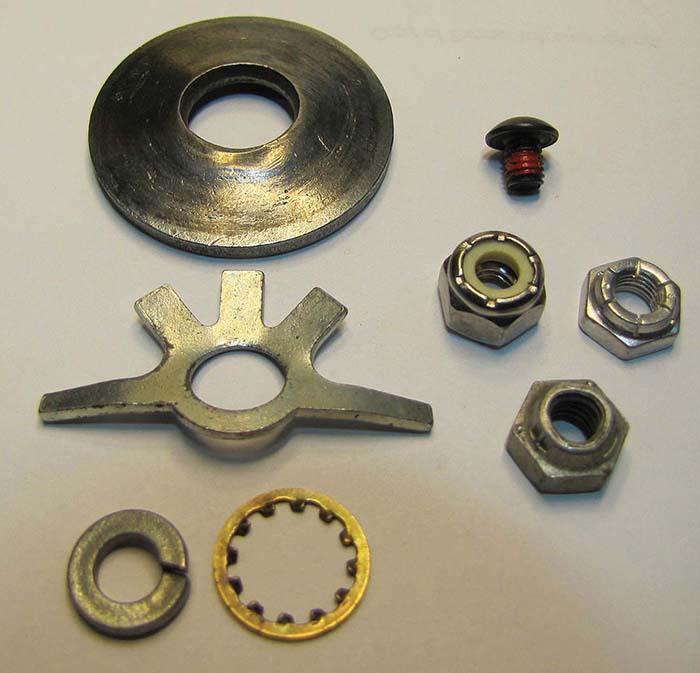
Since the late 1800s when the Broomhandle Mauser was designed, extensive studies have been conducted to understand why threads loosen. Engineers studied their use, focusing first on what happens during the tightening process. They determined that a threaded fastener is nothing more than a very stiff spring, which becomes stretched, twisted and bent during tightening. After being torqued into place, the only forces that hold it in place are friction forces that occur at contact points. If they are subjected to high vibrational loads the threads will eventually loosen. They further determined that joints loaded in shear (perpendicular to the threads) vibrate loose more often than joints loaded in tension.
In the late 1960s an American engineer, Gerhard Junker, conducted mathematical studies on bolt torque equations and presented what is known today as โJunkerโs Theories.โ Junker determined that when the bolt is stretched during tightening, there is enough torque created to cause the bolt to loosen. When subjected to high vibrational loads the male and female threads slip. Simultaneously, the area where the bolt touches the joint surface loses contact with the component being held so that the frictional holding force in this area is also lost. With the holding friction gone, both ends of the bolt are freed and the energy stored in the bolt from tightening cause the bolt โ not the nut โ to rotate loose.
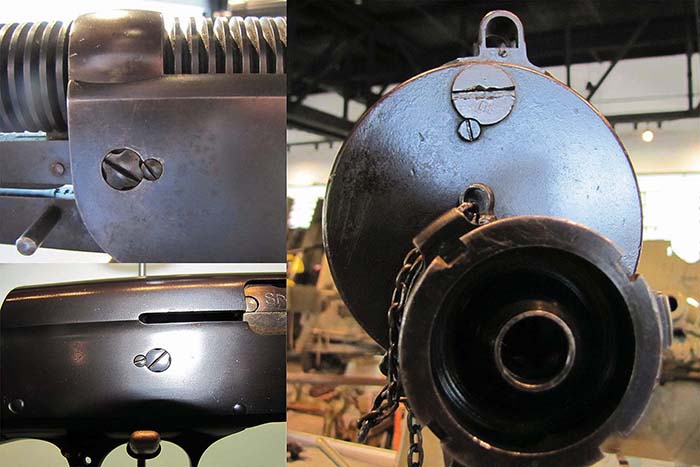
The use of any threaded fastener or joint on a firearm gives the assembler, soldier or maintainer the responsibility of applying the correct amount of torque to each fastener or joint. Depending on their particular body strength and the tool used, too little or too much torque can be applied. This is a disadvantage since over tightening and under tightening are both problems. This is sometimes โcorrectedโ by specifying the amount of torque that should be applied. A host of new problems accompany this. Specifying a torque load is fine for the gun assembly department, but in the field it requires a torque wrench and either a technical manual or a good memory to recall the torque requirements. We Americans make it even harder for the rest of the world by failing to give the metric torque equivalents. Torque wrenches everywhere else in the world read in newton-meters rather than our inch-pounds. Returning to Junkerโs theories and the discoveries by other engineers, unless some serious provision is made for maintaining preload under the shock loads of firing, why would you bother to specify torque in the first place?
In the past 100+ years, few gun designs are up to par with what we might now call the โMauser Challenge.โ Instead, designers have attempted to rely on โself lockingโ fasteners and other means that have been developed since the days of the Broomhandle Mauser. These can be classified in three categories: 1. Devices added to mechanically retain the fastener such as lock washers or retaining wire. 2. Nuts or bolts with deformed threads or ones that come with patches of anti-loosening materials formed on the threads. 3. Liquid solutions called thread locking compounds that are applied directly to the threads during installation.

Mechanical devices that include lock washers, toothed lock washers, Belleville washers, wave washers, and jam nuts are all better than nothing but none work very well. Some that do better are castellated nuts (also called crown nuts) and lock wire, which is sometimes called safety wire. After the castellated nut is torqued on, the assembler passes a cotter pin through a hole in the bolt, assuring retention. Properly installed lock wire assures that the nuts or bolts canโt loosen and fall out. Unhappily, neither the pinned castellated nut nor the lock wire is it very effective in preventing loss of preload. Just a tiny bit of rotation from vibration causes the fastener to tighten against what retains it while the preload is lost or reduced. Lock wire requires special pliers and reasonable skill to install. Both are a hazard once itโs in place because lock wire and cotter pins have sharp edges that can injure the end-user or maintainer.
There have been successful methods of simultaneously maintaining preload and retaining fasteners. On one of their aircraft cannons, the Russians ran bolts through the outside of the receiver to hold cams and guides on the inside. After installation and torqueing, each of the bolt heads was welded to the receiver body. It wasnโt pretty or elegant, but the bolts held their torque and didnโt vibrate out. The U.S. Marines discovered a similar solution for the bolts that kept loosening and falling out of their tank treads. When treads were new, they made a quick run through the surf and the bolt heads rusted tight to the treads.
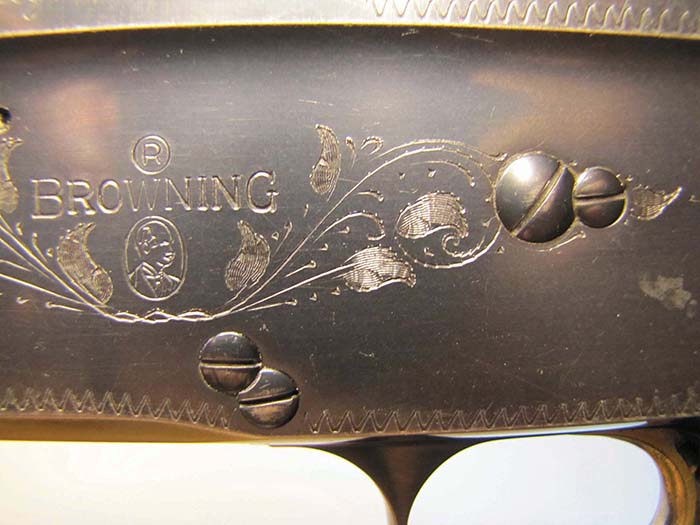
Sometimes the threads of nuts or bolts are modified to create an interference fit with the mating thread. These have limited success on firearms because any time the nut or bolt is removed, the deformed thread becomes โundeformedโ and looks like a normal thread. Other types have a patch of nylon added to the threads to prevent loosening, but after removal very little of the nylon patch remains. Once removed, these fasteners should be replaced with new ones and the maintainer must be trained in the importance of discarding used hardware. Unfortunately replacement hardware availability and adequate training are not always up to par in combat conditions so reliability is compromised.
Last but not least are thread locking compounds. These are liquids that come in a color coded bottle to aid the designer or user in determining just how serious he or she is in maintaining the joint preload and the securing of nuts or bolts. Depending on which color is selected, retention ranges from locking the threads just enough for easy removal by mechanical tools to compounds that require the joint to be heated with a special heat gun before loosening can occur.
Loktite is the thread locking brand most commonly used on gun systems, and I can assure you, their factory representatives hate to visit when Iโm around. Itโs not that their product doesnโt work. It does, but there is a high price to pay for using it. In order for it to work correctly, the threads must be totally free of lubricant or protective oils, so they must be degreased before application. Keep in mind that almost all threaded fasteners have been coated with protective oil just after manufacture to prevent corrosion. You can be relatively sure that threads right out of the box are greasy. If the degreasing operation is missed, Loktite doesnโt work.
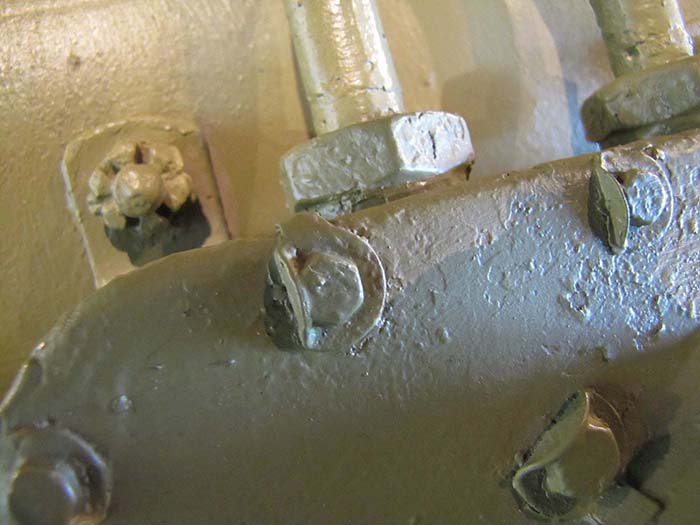
Thread locking compounds have a finite shelf life and every bottle has an expiration date. The next time you see a bottle in an arms room or in an armorerโs tool box, check the date. Donโt be surprised to see ancient bottles lying around because it seems nobody ever likes to throw them away. There is more. Since itโs a liquid itโs easy to apply where you want it and even easier for it to go in places where it doesnโt belong. Iโve seen more than my share of field problems caused by a sloppy application.
Once Loktite is applied and the joint is torqued to the correct value, there is no way to tell that Loktite is present or that a sufficient amount was applied. This presents a challenge to the Quality Control Inspector. Correctly applied from a fresh bottle on a properly prepared surface โ it works. Add the human element, and all bets are off. Itโs easy to make mistakes in application and even easier to miss the application altogether should the assembler lose focus โ particularly when multiple threads are involved.
I suggest you buy or borrow a Broomhandle Mauser. Take it apart, and observe the ease of assembly and disassembly. Fire a few aimed shots and note the high level of accuracy achieved from the fixed barrel. Next, attach the wooden holster to the backstrap and fire it from the shoulder to see how the accuracy further improves. Remove the screw from the grips and ponder ways of replacing it with something that doesnโt have threads. Let your mind wander to high mountain tops in Afghanistan, where soldiers are challenged with torque wrenches, lock wire, and special tools. Think about civilizationโs last 100 years of progress in engineering. Remember the 1896 Broomhandle Mauser, and then have a good cry.
(The opinions expressed are solely those of the author.)
This article first appeared in Small Arms Review V17N1 (March 2013) |