By Matt Smith
SAR: John, how did you get interested in machine guns and silencers ?
John: I’ve always been involved in firearms since my teenage days. Someone in the ‘70’s showed me a Shotgun News. I then became aware of class III firearms. I began buying machine guns and suppressors as an individual, became a Class III dealer for a few years, and eventually a Class II manufacturer. My family had been in the wholesale/retail business for years in Jacksonville, AR near the Little Rock Air Force Base. The personnel at the military installation became my initial customer base. Since we already had machine shop capabilities at our Jacksonville Main Street location, the manufacturing of Title II weapons was a good fit with existing resources, skills, and interests.
SAR: How did you get into manufacturing?
John: When I was a class III dealer, I was buying suppressors and converted machine guns from several Class II manufacturers. The quality was just not what I wanted or expected. Many of the suppressors available at that point in time could not be readily disassembled for cleaning, internal parts were crude, others just did not reduce the sound level enough to justify a $200 federal tax (even if the suppressor was free). Many of the manufacturers producing integral suppressors available for firearms such as the Ruger 10/22 had front sights that were mounted crooked, some would not even cycle without malfunctions and others had accuracy problems. I really hated selling products that I would not want to own myself. These problems forced me into the Class II manufacturing business. I simply needed a source of products that were consistently of high quality. My concern when I first went into this business was that I would not be able to sell my products and I’d end up having to keep everything I made. Therefore, I built everything to my level of expectation to where I was pleased with it, so that even if it didn’t sell, I would be happy to keep it. I found that my standards appeared to meet or exceed most expectations of others. To this day I’m still not a high volume manufacturer, and I don’t want to be. The bottle neck in my business is that I put everything together and test fire it myself. I have two licensed shops were I manufacture parts but can unfortunately produce the parts faster than I can put them together. I have several people that work with me but I do the final assembly and fitting myself. That way I know exactly what the quality is of my products , so I very rarely have anybody call with a problem. That is really the key to customer retention and business longevity.
SAR: How much advanced notice did you have that the machine gun law in 1986 was changing?

John: I remember sitting at my kitchen table in March of 1986 reading the newspaper, and noticing there were more and more articles about the McClure-Volkmer Bill, which had just passed the House. That’s when I first started calling the NFA Branch. Gary Schaible, the acting branch director, was very helpful. During one particular call to NFA it finally hit me that the bill was absolutely going to pass both the House and Senate and be signed by the President. I had a limited window of opportunity so I started working nearly 24 hours a day. ATF was coming out every so often, and they were laughing, as they could see the stress I and others in the country were under trying to get parts registered. The local BATF inspectors were acting like the “Bill” would probably not pass the Senate or be signed by the President, so why get in a big hurry? Fortunately, anything that I did build would be something that I could still use even if it had not become Public Law 99-308. I remember driving into work in the mornings, and being in a daze due to the lack of sleep because I just couldn’t let up.
It was really frightening to see what was happening to this industry and why it’s dangerous from a financial perspective to be in the class III firearms business full time. You can pick up the newspaper some morning and read that you’re literally out of business! Laws can change that quickly. President Reagan was in Japan when the “Bill” passed the Senate, and on his return, thirteen days later, he signed the bill into law. My approach to registering firearms and parts during that time was a little different than most Class II’s. I did not want any screw-ups over what could be registered and what could not. I had the local BATF inspector come out to the shop almost every day to inspect and verify what I was sending in on Form 2’s to NFA in Washington. I obtained the local agent’s signature on each Form 2 and let the local BATF office send them in for me. This prevented me from having many of the verification problems that many class II’s had after the ban.
What is interesting, was that it was generally believed in the industry that the actual day the President signed the act into law, this would be the last day to make and register machine guns. Not many people are aware of this but the Bill was signed on May 20th at about 3:30 pm CST, but it became effective on the previous day, May 19th. The whole day of the 20th, you couldn’t count. I had sent in piles of Form 2s every day, including the 20th. The local ATF agent was coming and checking on me regularly, and my Main Street shop was like a fast food place during lunch with people sometimes lining up out onto the sidewalk wanting me to register guns and parts. I had firearms and parts all over the floors on blankets so ATF could inspect them. I remember during one inspection we were looking at M-2 trigger groups and the inspector required that I have all the parts in order to register the kits. I remember looking at one trigger group, which I had picked up to call out the serial number to the BATF inspector. The inspector said it was missing the selector spring. I told him it was still a machine gun even without the spring, but he told me it had to have all the parts or I could not count it. So I said, “Ok, let me get this straight. If I leave this part off the M-2 trigger group then it’s not a machine gun so I can sell it to any man, woman, or child that walks in my shop, right ?” The ATF agent looked at me, smiled, and said, “Ok, we’ll count it”.
ATF agents made decisions inconsistently all over the country at that time. An inspector in one state would allow a class II to register some parts and in another state the same parts would not be considered a machine gun by the inspector so they could not be registered. Example, for 10 years, I had been putting the serial number on the M-2 trigger housing when I converted an M-1 carbine, but when ATF came out to inspect me in 1986, they disallowed all of my M-2 trigger groups the first day because I had the serial numbers on the housing rather than on some other parts. They stated that I had to have the number on one of the parts that was different than the semi auto parts. Of course the full auto housing has a machine cut in it that is different than the semi-auto but that did not matter. I had to re-serial number several hundred the next day, but they came back out again and approved them.
SAR: Would you give me a break down on the number and types of machine guns that you have registered?
John: In 1986, I registered a couple thousand different types of full auto sears, UZI bolts, M-2 carbine parts, Sten receiver tubes, a few Browning side plates, etc. I also rewelded a number of military M-16 receivers that had been destroyed by the DOD. I produced these in various brands such as Colt, H&R, and General Motors Hydramatic Division, etc. We had gotten so experienced in cosmetic welding of these receivers that it eventually caused a problem during the intense ATF inspection period before the May 19th 1986 cut off. ATF kept asking me where these M-16 receivers came from since there were absolutely no cosmetic imperfections that indicated they were rewelds. Fortunately, I remembered that I had written an article that was published in the now defunct FirePower Magazine on the rewelding process with pictures. This was the only way I could convince them that these were rewelds rather than new M-16 receivers. It worked and I had no problems with them in the future.
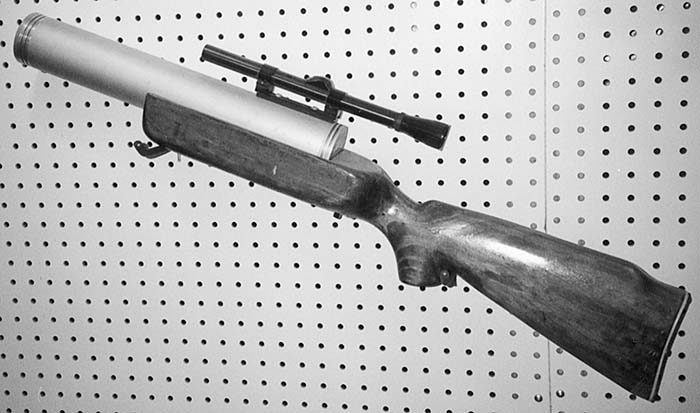
SAR: Tell me about how the select fire Ruger 10/22 came about?
John: The Atchission MKI and MKII .22 subcaliber kits for the AR-15/M-16 are responsible for propelling me into designing a full auto conversion for the Ruger 10/22. I got involved with the Atchisson .22 subcaliber units when they were owned and produced by Brocal International out of Ohio. This was quite awhile before Jonathan Ciener produced the MKIII version of the Atchission.. I started redesigning the Atchisson Mark II and eventually wrote a manual to allow shooters of the Atchisson unit to improve its reliability. I ended up producing precision match grade parts for the Atchisson MKII for few years, but I was still dissatisfied with all the work it took to make them function properly. It simple made more sense for me to focus on the conversion of a rifle that was already a .22 rimfire using what I had learned from my mechanical success with the Atchisson.
I began examining a variety of .22 cal semi-auto rifles looking for a suitable rifle to convert to full auto. I worked on a conversion for the Marlin Glenfield, the Remington Speed Master and the Ruger 10/22. The Marlin was just too delicate, the Remington had a very light bolt and was not suitable. The Ruger 10/22 by far was the obvious choice. It was not delicate, it had massive parts in its trigger group and had a heavy bolt. I spent a year and a half on designing the closed bolt conversion for it and built numerous prototypes. I shot something like 300,000 .22 cal cartridges during that year and a half for testing and eventually settled on a particular design. I started officially offering the conversion for sale in about 1985. Over the years, I’ve made numerous modifications to the conversions, and offered them with and without the suppressors. I continue to convert 10/22’s as Post-86 samples for law enforcement demonstrations and sales to dealers, and also release a few pre-’86 conversions each year. Transferable machine guns are simply investments like stocks and other commodities.
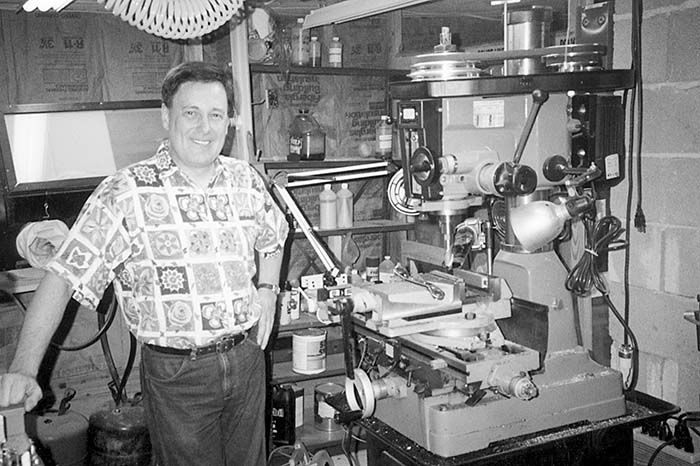
Of interest, is that a number of years ago I got a letter from the legal department at Ruger letting me know that they had been informed that I was doing a full auto conversion on the 10/22. The letter stated that the 10/22 carbine was not intended to be used as a machine gun and besides I might be doing something illegal. It was a pretty humorous letter in that Ruger’s attorney seemed to imply that Sturm, Ruger and Co. just woke up and discovered that full auto conversions on semi auto firearms were being done in this country. The letter also implied that Ruger should have control over how their 10/22 and other firearms were used by other manufacturers, dealers and individuals.
There was another company called TEK that did a few closed bolt conversions using a totally different design than mine. The TEK conversion was pretty light duty and most of them would eventually cease to function after extended use. I’ve converted most of the existing TEK conversion in the country over to my design at this point.
SAR: What are the differences on your 10/22’s?
John: These several Rugers I have displayed are my prototype shop guns. One version has a larger diameter suppressor and a match grade barrel in it. Another version is a shorter suppressor which uses the large diameter tube. One has an infrared Sure Fire light on top, and an infrared laser that I made and mounted on the bottom. I use this set up for night hunting with night vision. It is suppressed and can be fired from the waist without needing to look through sights. I recently shot a 60 pound beaver using this set-up, authorized by a state issued night hunting permit, of course. Others displayed indicate the various levels of development of the full auto conversion and suppressor design in the Ruger 10/22.
SAR: How did you register the 10/22’s?
John: I started with registered trigger groups, but I actually converted more Rugers with registered sears than any other way. I remember one man from Tennessee who was a TV repairman, who had registered a full auto 10/22, which was converted electronically. It had a little motor and a battery, and he built it all in the trigger group. When he pulled the switch, the motor would turn and shoot full auto. I converted it to a mechanical mechanism for him since his batteries would run down often.
SAR: With all the Ruger 10/22 suppressors being made by other manufactures what sets yours apart from them?
John: I think a number of manufacturing aspects may be unique to my products. First, the Ruger 10/22 suppressors I manufacture have 1’’ OD seamless stainless tubing that is the highest quality that money can buy. By that, I mean I have my shop foreman, Mike Sullivan, require that the tubing manufacturer and shipper handle the tubing in a special manner to assure straightness and roundness. Most tubing manufacturers ship tubing in 20 ft or longer sticks to their distributors. A 20 ft stick of anything is not likely to stay perfectly straight very long during shipping. Then, when the tubing distributor gets it they fork lift it around the warehouse to stack it. By the time most people buy it is not perfectly straight anymore. On a short suppressor tube of 6 to 8 inches this is not a big deal, but on an 18’ or longer suppressor tube it is extremely important that the tube is straight. Why? Because if the tube is just a few thousandth of an inch off from being straight, then the internal parts including the barrel are curved to fit the contour of the tube. This is one reason that lots of suppressed rifles on the market require you to adjust the rear sight far to the right, left, up or down to sight the rifle in. A few thousands off due to the suppressor tube may translate into inches off at 50 or 100 yards. Next, I have to make sure the bore in the barrel is straight. Bores in rifles and shotguns are usually not perfectly straight, especially in low priced firearms.
SAR: How can you tell if the bore is not straight?
John: The straightness or trueness of the outside of a barrel has absolutely nothing to do with how straight the bore may be. If you take just about any barrel and start cutting it off one inch at a time you will notice by using a micrometer on the wall thickness that the bore is not centered in the barrel through out its full length. Even Colt M-16 rifles can have the bore off center at the muzzle by .020”. This is very important if you are screwing on a suppressor with close tolerances since the bullet may hit the baffles or other structures in the suppressor. I machine every barrel based on the location of its bore not the outside of the barrel. Although I know that the bore is centered at the muzzle end of my machined barrel, I don’t know if the bore is off center in closer to the chamber end. After placing them in a perfectly straight tube, I then test fire them for center shooting accuracy. A barrel may be straight on the outside but have an arch to the bore inside. This will show up when firing because the rear sight would have to be adjusted to an extreme to correct for this. If this occurs I either don’t use the barrel or I shadow box arch or bend the barrel to straighten the bore. The end result is that the bullet will exit the suppressor straight and not at an angle. This allows me to use extremely precise baffles and other parts. Baffles are machined from solid bars of aircraft T6 aluminum on a computerized lathe for precise consistency.
SAR: Any other notable differences?
John: Possibly, the processes of drilling and deburring the gas holes in the barrels may be unique too. I use a new drill bit on every barrel I drill. I want a hole that has the least amount of metal distortion before deburring the inside of the barrel. Since holes are drilled in the barrel for some types of suppressors, the bullet will be cut and deformed as it passes by the port holes if any burrs or edges exist. I have a set of broaches in .00025” increments that I pass down the bore. These broaches have blades on them that trim the burrs off of each hole inside the barrel. Deburring the bottom of the grooves in the rifling is next. I have a specially made spring loaded tool that I insert through each port hole and it expands to let me countersink each hole from the inside. I then lightly polish the bore of each barrel to provide a glass like finish. I line my suppressor tubes with a thin wall .020” stainless tube cut into 1 1/2” lengths. This produces a suppressor cartridge that when removed from the suppressor contains all the powder residue leaving the suppressor tube clean internally. Crowning of a barrel is also a science. I have experimented with all types of crown angles and crowning tool geometry. After crowning I examine every muzzle under high magnification to assure it was cut correctly. Eventually the suppressor is assembled and test fired for accuracy and sights adjusted. It is a long process but has worked well for me. This last year I’ve added the option of a match grade target barrel installed in the suppressor for the more demanding shooter or hunter.
SAR: Have you suppressed any shotguns?
John: Yes, one prototype I designed and made back in August of ’86. I used an old Stevens Model 58 .410 bolt action and made the 12” suppressor offset so the top of the suppressor tube is flush with the receiver. I mounted the action in a Butler Creek Ruger 10/22 folding stock, installed a screw-in full choke tube, and added adjustable sights. It will shoot 3” magnum shells and sounds like a suppressed .22 rifle. (see photo page 32) I’ve hunted with it for a number of years shooting small game. It’s just kind of an all around good little game getter.
The second one is a prototype of a pump suppressed shotgun using a 20 gauge Mossberg Model 500. It has an intricate pump action that really took too much labor to ever put it into production. It looks like something you would see in one of “Arnold’s” movies. A semi-auto shotgun with a box magazine would be a good candidate for an integral suppressor but it would have to be recoil operated rather than a gas operated.
SAR: Tell me about your spear gun.
John: That’s a prototype spear gun I built from a stainless steel .410 Snake Charmer. At one point in time I did a lot of scuba diving and spear fishing, and rubber band guns were just inadequate, as well as, most pneumatic and hydro-pneumatic guns. I redesigned a stainless steel Snake Charmer .410 by placing an M-16 pistol grip on it along with a wrist support, built up the hammer weight so it would have enough momentum under water to fire the cartridge, converted the chamber from .410 gauge to .22 rimfire, and installed a large adjustable ring sight. I used a stainless spear shaft and manufactured a Teflon gas seal at the rear of the shaft.
When you’re scuba diving, you want your line to be coiled up, but when you shoot, you want it to release. This is just one of the characteristics that would define a well designed spear gun. So I made a stainless steel gas operated release mechanism for the line. I use .22 cal. Remington waterproof power cartridges to propel the spear shaft. Remington makes the power cartridges in twelve different power levels. The power produced by the cartridge propels the spear at speeds and distances unmatched by any spear gun I’ve ever seen. The spear will shoot hard and straight to 50 ft before it starts to drop. The adjustable sight is easy to use and allows you to sight-in the gun using an underwater target. The grouping is about 1” at 30 ft. I’ve shot through several fish at once on more than one occasion. You can control the power easily by using different power cartridges. After each shot, you break the action open and it ejects the .22 cartridge automatically. When you shove the shaft down the barrel, it pushes all the trash and residue out the barrel and chamber for the next shot. It makes a dull thud sound when fired and produces no noticeable gas bubble coming from the barrel. I have plans at some point in time to produce these with an adjustable power switch that will allow you to simply select the power level and penetration just a second before shooting. I’ve worked an arrangement with BATF to allow these to be produced without being considered a firearm. This would allow sales directly to dive shop and individuals without a FFL.
In keeping with the idea, I’ve also prototyped a power head for bowfishing. The light weight stainless power head allows you to shoot a .22 magnum cartridge or Remington power cartridge on the tip of your bowfishing arrow. I use the 22 cal. magnum stud driving power blank so it will not be considered a firearm. The stud driving blank will blow a 2 x 4 oak board into splinters and creates a tremendously deep and fatal wound on fish or other game.
SAR: Have you produced many AOW’s?
John: Yes, I have machined Ruger 10/22 barrels into .22 long rifle pen guns. (See photo page 32) At one time I produced a few of these and threaded some of them 1/2”-28 tpi to allow the attachment of a small suppressor made inside the shell of a Magic Marker felt pen. I made a thread protector that looked just like a marker tip and would actually write. You had a pen and a Magic Marker set which screwed together to make a firing combination. The real obstacle in producing and marketing pen guns and some other AOW firearms is the liability exposure since they don’t look like firearm. I’m also prototyping a video camcorder that is actually a very accurate .22 cal. match AOW with suppressor aimed by a laser. The cosmetics are perfect on the camera and the original operational L.E.D.s still light up and releases the safety mechanism when the camera is turned on.
SAR: How about AOW shotguns?
John: Yes, I was able to get a number of double barrel receivers when Iver Johnson went out of business, back in the 1980’s before they become AMAC. Iver Johnson had made about 30 brands of shotguns from the turn of the century. I produced these in .410 , 20 ga. and 12 ga. These were the first double AOWs made in the U.S. since 1934 when Ithaca ceased production of the “Auto Burglar” AOW.
SAR: How many did you build?
John: I only built four of the .410’s, which were more of a novelty. I built about 200 of the 20 gauge and a few 12 gauge. I still have some receivers and may go back at a later date and make some more. I also have several hundred single shot receivers too but there is simply not much of a market in single shot AOW shotguns pistols. I’m currently building AOW Mossberg pumps with 7.5” barrels and 17” overall.
SAR: Have you done any weapons with lasers?
John: Yes, I made a prototype high powered helium neon laser rifle many years ago, before lasers became common and power outputs became restricted by the Bureau of Radiation Health. (see photo on page 33) This is a very high powered laser that I’ve mounted with a scope. It will temporarily blind small game so well that you can just go pick them up. The stock has been hollowed out to hold rechargeable batteries, and it can also run off the cigarette lighter in a car. I’ve got some interesting stories I’ll tell you sometime about this rifle.
Later, I developed a laser module that fits onto the H&K Utility Light for the USP. It allows the use of the light or laser by itself or both the light and laser at the same time. I also made it with an infrared laser for use with night vision. This led to having to make an adapter to allow the mounting of the USP light onto the SOCOM MK23 pistol. None of these prototypes are yet in production.
SAR: Tell us about your mail order business.
John: My first mail order product was selling the book on how to make an Atchisson MKII function. Later, I started providing the Atchisson repair, and then slotting Uzi bolts back when you could sell them. I eventually needed a finish to put on stainless steel so I developed the finish I call Moly Resin from a molybdenum disulfide phenolic Resin. I produce the product now in ten colors and sell it to the SOCOM suppressor manufacturer, Knight Armament, the U.S. Military for refinishing their M-16’s, gun shops all over the country, as well as, in several in foreign countries. Now my business for all products lines is 90% mail order with the mix of 60% Class III and individuals, 38% law enforcement and 2% federal agencies with oddball special projects.
SAR: Tell me about the suppressed Colt 9MM.
John: The Colt Model 6450 9MM carbines was introduced by Colt in late 1985 or early 1986. So there weren’t many registered as machine guns before the May 19th cut-off. I had a large stock of AR-15 drop-in auto sears at that time and the Colt 9mm weapon converted very well. I looked at several other’s efforts in producing a suppressor under the rifle forearms. All of the ones I saw looked like the barrels were cut to 5” or so and then a suppressor tube place on the barrel with baffles. The AR-15 front sight was cut and welded to the tube or simply did not have a front sight. I felt that this design could be improved upon, so I built a two piece suppressor that couples together around the front sight, leaving the barrel the full 10 inches. I port the barrel so that high velocity bullets exit the suppressor 1050 feet per second, so it’s subsonic. It is equivalent in sound to an MP5 SD. You don’t have to worry about the front sight alignment or having some unattractive welding of the sight onto the tube. It is easy to clean, quiet, doesn’t affect accuracy, and allows the use of standard supersonic ammo,. Later on, I developed a mechanism for the AR-15 9MM magazine well blocks to prevent holes from being drilled to mount the blocks in the receiver. I designed a cam mechanism that I put into each 9MM block, which would expand and lock itself in. I also worked for several years on the four position M16 selector. Colt prototyped some of these back in the ‘60’s, but they didn’t go over then. There were several early attempts by other manufacturers to produce a four position kit for the M16, but none of these kits were of high quality or functioned well. I started building my own cams, including 2 shot, 3 shot and 6 shot cams, hammers and disconnectors. I no longer produce the burst kits but I did design and market a kit that will allow select fire with the SWD auto disconnector (lightning link).
SAR: Have you patented any of your products?
John: Yes, I patented certain features of the full auto conversion on the Ruger 10/22, and I have copyrights to some manuals that have to do with making some improvements on various guns and devices. I used to write a weekly column in the local paper, called Bullseye, for about a year. I’d write about everything from cleaning firearms to ballistics. I eventually wrote an article about Second Amendment rights and that was the end. The newspaper terminated my contract cold turkey. Apparently, the news media owners did not agree with our Bill of Rights. I’ve also written a number of articles for FirePower, Swat, Machine Gun News, etc.
SAR: Haven’t you been called to give expert testimony in firearms trials?
John: Yes, years ago I got involved in court cases for both sides. BATF has even flown me out of state to testify on their behalf, but primarily I testify for the defense. I do this not just for criminal cases, but also for liability suits and these have included everything from someone shooting themselves in the knee to the illegal manufacturing of MAC 10 submachine guns and selling them in Mexico. Of interest, is that most cases have to do with the possession of an unregistered machine gun. In almost every instance a crime of violence was not committed but rather a wife, ex-wife, girlfriend, etc. got angry and turned their husband or boyfriend in for possession. Generally speaking, BATF has not gotten very many convictions, at least in the cases I’ve been involved in. It is hard for them to convince a jury that a little bitsy piece of metal called a sear is really a machine gun. It is even hard for me to think it is too, especially considering some of the prices I see asked for them.
SAR: How did you get started in re-manufacturing M16 receivers?
John: Back in the early ‘80’s, Colt would sell a Class III dealer one “dealer’s sample” of each type of machine gun they produced. I was needing more Colt M16’s, and it was too slow getting them from Colt. You had to prove to Colt that you had sold one sample before they would send you another one. I started purchasing cut Colt M-16 receivers that the Department of Defense had destroyed. I made a special jig and fixture and welded them very carefully back together.
SAR: Tell me about the cosmetic work you do on machine guns.
John: During the learning process in rewelding M-16 receiver halves, I had to make certain cosmetic changes to the receivers as needed so they were not noticeable where they had been rewelded. I can weld over “AR-15” and re-engrave “M-16” or change the caliber from .223 to 9mm. I also weld the selector stops onto the AR-15 receiver and remark the safe, semi and auto positions. Just about any cosmetics can be accomplished except changing serial numbers or manufacturers. I don’t know anyone else in the industry that routinely is willing to weld on someone’s M-16 or AR-15 receiver. It is a very delicate process and there is absolutely no room for error. When I reconstruct other machine guns they are almost always made from steel and are much easier to weld.
SAR: Thanks for sitting down with us and sharing your experiences with our readers.
John: You are very welcome.
John Norrell Arms
2608 Grist Mill Road
Little Rock, AR 72227
E-mail: SMG1022@aol.com
This article first appeared in Small Arms Review V3N2 (November 1999) |