By Matt Smith
SAR has a policy of trying to bring new Class 2 manufacturers to the attention of the readers, as well as our interviews with long time industry people. We recently had the opportunity to sit down with Ty Meligan of TL Guns and ask him a series of questions about his background and history as a Class Two Manufacturer. Ty is located in Oregon, a state that has a very high machinegun rating per capita including many other dealers and manufacturers. He has been getting a lot of attention on the Internet among the Class 3 community there, and we thought we should bring him to the attention of the SAR community.
SAR: Ty, how did you get into the firearms business?
Ty: It started about six years ago with a gentleman named Dan Tanner. I went by his gun shop one day, where he had machineguns and suppressors all over his walls. I started asking questions and discussing what I knew about them from the military. I had no idea that you could legally own this stuff, but there it was in front of me. I got to know Dan as a friend, and he eventually asked me to help run his equipment to manufacture suppressors. I told him it had been a while since I had done that, but I quickly came back up to speed on the equipment, and started manufacturing suppressors for Dan.
SAR: What kind of technology were you using for the suppressors?
Ty: I wouldn’t really call it “Technology”. It was basically just flat baffles. I was working as a machinist manufacturing what Dan wanted. I was making .223 cans, 9mm MAC cans, integral Mark 2 cans, and screw on .22 cans. Sales were mostly to local residents, but we did have some Internet sales, as well.
SAR: When did you become involved in the designing of suppressors?
Ty: After I had been working for Dan a while, I approached him and asked him if I could try some of my own ideas. Dan gave me the go ahead to make the improvements that I felt were necessary to improve performance on the cans. I started by trying ideas from suppressors I had used in the military, but I knew I could improve on these designs as well.
SAR: Ty, what was your military background that exposed you to suppressors?
Ty: I was in the Army Special Forces as an 18 Bravo Weapons Sergeant. We were attached to an infantry unit at Fort Sherman in Panama. My main function was as an armorer. We captured weapons, and did documentation on what we found. Often, we found weapons with modifications to them, held together with rubber bands and paper clips. One of the most interesting weapons ever confiscated was an old M16 that was so worn it had a hole in the magazine well where you place your thumb to drop the magazine. All of the plastic had been removed and replaced with wood. Who knows how it had made its way from Viet Nam to South America. We did a lot of work with the HK MP5 SD and HK muzzle cans. This is where I was first exposed to the K baffle, and I wanted to improve upon this design. I started doing my own version of a baffle with different types of cuts, different angles, and different ways of manipulating the gas. I’ve also attacked other aspects of suppression such as how to reduce ejection port noise and reduce the overall sound signature.
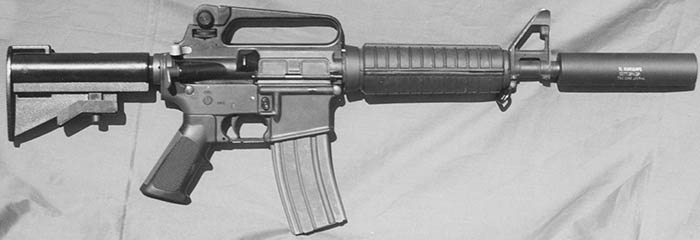
SAR: How long did you work with Dan Tanner before going out on your own?
Ty: I worked with him off and on for two years, until one day when Dan told me that I was really good at this and should be doing this on my own. He complimented me on my workmanship, quality, and new designs, and encouraged me to get my own manufacturing license, which I did. I started out part time, since I had a full time job as an electrician. There was a student that was going to a local Christian college studying advertising and marketing. He asked if he could do his final report on my business, from where I started to where I am now. This included manufacturing from the raw materials to the finished cans. The first year in business, I made about 20 suppressors, which was mostly for fun. I was making good money as an electrician at the time. The second year, I made about 60 suppressors. I was out in the shop more working at night. The third year, I made nearly 100 suppressors. This was the point where I started asking myself what I really wanted to do. At about the same time, the company I was working for went out of business, which more or less made up my mind to start manufacturing full time. I did some advertising, got my web site built, and my business just took off. I think the main thing that kept my business going was that customers liked the quality, the looks, and the price.
SAR: Tell us about your shop and the equipment you’re using.
Ty: My shop was originally in my garage, where I had kept my two race cars. One by one, the cars were removed as I started getting equipment. I’ve got a nice lathe, a couple of milling machines, a drill press, a grinder, a solvent tank, a bead blast cabinet, a band saw, and an Iron Worker punch. I just picked up a nice Okuma CNC lathe. It has eight tool heads and a seventeen-inch swing. A new industrial park has gone in nearby, and I have moved my shop there. I have gone from a 24 X 30 shop to a 2000 square foot shop. I will also open up as a general machine shop, in addition to the firearms business. It is only about 2 miles away from my former location.
SAR: What were the first suppressors you started manufacturing once you were out on your own?
Ty: Integral Mark 2 pistols. At the time, many of the other suppressed Mark 2’s were full of packing material and miscellaneous parts and pieces. They were a pain to get back together. I wanted to simplify the design, and reduce the number of items in the assembly. I started by combining the baffles and spacers into one piece. My design includes an aluminum inner tube over the barrel with an end cap, the spacer and baffle assembly, the outer tube, and an end cap. I started with a setscrew to hold it all together, but found that after a couple years of use, a gap developed between the receiver and the tube. I don’t like to copy other people’s stuff, because not only is that not righteous, I like to come up with my own ideas. I decided to drill a hole in the bottom of the end cap, where you could stick the end of an Allen wrench to tighten or loosen the threaded end cap. I now thread my outer tube onto the receiver, mill a slot for the sights, which are welded from the underside of the tube, and it all makes a nice package. Some of the other guns that we suppress are the Ruger 10/22, 77/22, Buckmark .22 rifle, Marlin Papoose .22 rifle, various sub-machineguns and high power rifles. I also make a screw on .22 suppressor.
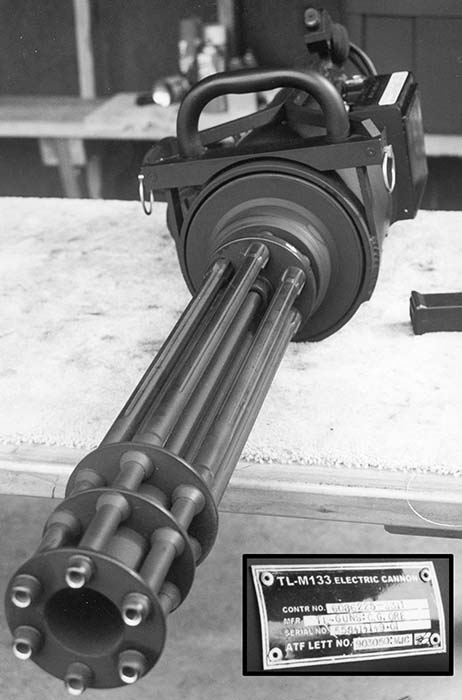
SAR: What type of materials do you use in your suppressors?
Ty: On the stainless guns, everything is stainless. On the parkerized guns, the only thing that’s steel is the barrel, the outside tube, and the end cap. All the internal parts, including the baffles, are stainless. The outer tube is 4130 chrome moly, and the end cap is tool steel.
SAR: How does the 77/22 suppressor differ from the 10/22 suppressor?
Ty: The internal barrel for the 77/22 is 15 inches long, verses 13 inches for the 10/22. The outside tube is therefore longer by 2 inches on the 77/22. Both guns use the same baffle stack, but the 10/22 has a 16 inch tube and the 77/22 has an 18 inch tube.
SAR: Can you describe your .22 screw on suppressor?
Ty: This can measures 1 inch by 6 inches long, and is made totally of 304 stainless. Two mounts are available for this can. The first type is a 1/2 by 28 internal thread for an external threaded barrel. The second type has a 1/2 by 28 internal thread and an 11/16 by 24 external thread to fit inside an internally threaded bull barrel. This eliminates the need for a thread protector on the bull barrel. This suppressor is designed for both rifle and pistol use.
SAR: What other pistol suppressors do you offer?
Ty: I have a 9mm pistol suppressor that measures one inch by seven inches long, and weighs 4 and 1/2 ounces. Most of these are threaded 1/2 by 28, but I can also do a 1/2 by 32 if necessary. These suppressors are made of 7075 T8 aluminum, and will cycle on a Glock 17, some Glock 19’s, Sig P226, and all Beretta 92’s without a recoil regulator. I also have a .40 caliber pistol can, that includes a recoil regulator to insure cycling in all pistols, including Glock’s.
SAR: Have you had any problems with your cans?
Ty: I’ve only had a few cans to come back for repair. One was from a dealer in Alaska who had worn out the spring in the recoil regulator of his .40 cal pistol suppressor after firing thousands of rounds through it. Another instance was when I received back the second 10/22 rifle I had ever suppressed, from George Denkins. Back in those days, I wasn’t Parkerizing, I was moly coating. George wanted the suppressor rebuilt and parkerized. He had had his suppressor on a full auto 10/22 and shot the heck out of it. When I opened up the tube to rebuild it, I was pleased to find out that there was only a small amount of carbon, and no lead build up. I also had to recall some .223 cans that I sold. I had an idea for lightweight .223 cans using a thinner tube material than usual. I made ten of these and ended up recalling them all because with excessive firing they would heat up and bulge. Seven of the ones I received back had only been fired in semi auto and were fine. Two of them came back blown up, and one has never been sent back. I replaced all of these for free with cans made of my regular materials.
SAR: What suppressors do you make for submachine guns?
Ty: I make an MP-5 can, using Gemtech’s three lug quick disconnect, as well as suppressors for the UMP-40 and UMP-45 with a quick disconnect that I designed. I make a combination can that can be used on both a 9mm or .30 caliber weapon. I can supply adaptors including three lug mounts, threaded adaptors for M11/9, MAC 10, Uzi, KG-9, or any other thread pattern required on the host weapon. I also make Uzi cans, as well as Smith & Wesson 76 cans. One of the most interesting cans I’ve built was an integral suppressor on a Yugo 49, which is the only one that I know of in the world and is it awesome! This gun was originally 7.62 X 25mm and was never designed to be suppressed. John Nichols is the lucky owner of this weapon, which is now a 9mm. I made an adaptor so that Sten magazines can be used with this firearm. This adaptor will also allow you to use Sten magazines in a PPSH-41. I just made a new suppressor for a 5.45 X 39mm for the AK-74 Krinkov or full size rifle. It is an exact exterior copy of the Russian suppressors, which are not available in the United States. This is a complex suppressor which utilizes four different external pieces, and has a tang on the front that can be rotated to different positions for more accurate firing. I manufactured this suppressor based on a picture out of a Russian book that was scaled by Steve Hill of Spotted Dog Firearms of Arizona. The idea came from a friend of Steve’s who works for the SAS, where they have a real suppressor in their vault. I designed the internals, since there were no specifics available on the baffle stack. Another big seller is the Greasegun suppressor that I manufacture. I’ve produced over thirty of these in the last several months, as no other manufacturers seem to be making these actively right now. This can looks similar to my MAC suppressors which have the two stage look. I use an inch and 3/4 tube for one stage and then press four inches of two inch tube over the main tube to give it the two stage look. The can is ten inches by an inch and 3/4, with the two inch back piece. Anyone who wants one of these should send me a barrel and $400, and I will send you back the suppressed barrel assembly. These are extremely efficient suppressors! One of my personal achievements is an integrally suppressed 30.06 Ruger M77. It sounds like a pellet gun when you fire it. I’ve also built these in .308 on a Remington 700 rifle. I port the barrel so that the velocity of military ball ammo is reduced to 960 feet per second. These are basically one hundred yard guns, but are extremely quiet, and you don’t have to use expensive subsonic ammunition.
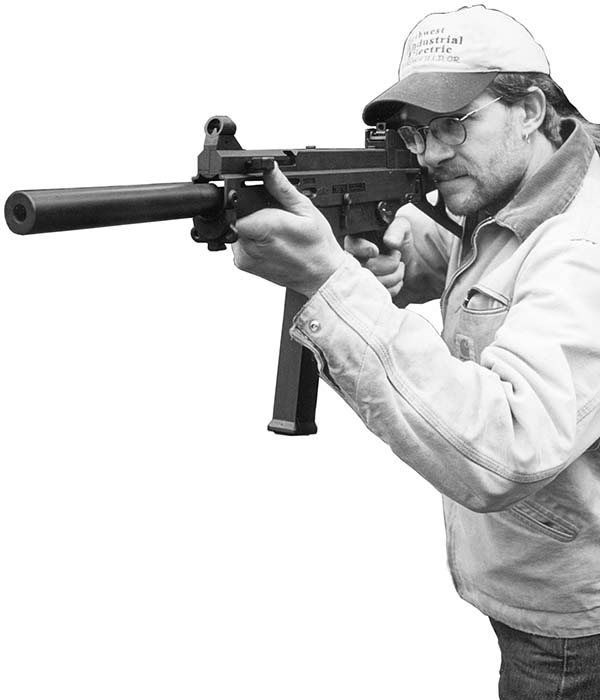
SAR: What other products do you offer, other than suppressors?
Ty: I can repair just about any machinegun. Krinkov’s and M16’s are my favorites to work on. My favorite Krinkov has a six inch barrel with a K grip and my favorite M16’s have seven and 1/2 inch barrels, which all cycle like a champ. Occasionally, I have to retard the timing, and I do this by adding material to the hammer to eliminate the light strikes. Another specialty is to modify weapons into short-barreled rifles. My M96 Robinson rifle has been shortened and now has a ten-inch barrel. I’ve also started to build a semiautomatic MG-42, and I’m having to figure that one out as I go along.
SAR: Ty, I think the most impressive firearm you’ve shown me is actually your minigun. Can you tell us how this firearm came to be?
Ty: Yes, one of my most unique projects has been manufacturing the six barreled .22 LR “Minigun”. I call it the TL-M133 Electric cannon. This was a collaboration between myself and Brian Abbot. His idea was to have a collar in the front for holding the barrels symmetrically in the front, and a collar in the back to keep everything straight. The collar in the back included skateboard bearings around this round tube to allow the barrels to rotate. I liked the concept but not the execution. I told him to let me design and build my own version of this gun. He was mainly after a certain look, while I wanted it to function properly. We bought six Butler Creek bull barrels, threading each of the barrels 1/2 by 28 on the ends with a collar going over the threads, and barrel extensions that thread over the barrels to hold the collar on. There are two more collars that go over the barrel extensions and a soup can that goes in the middle to give it the Minigun look. After the first prototype was put together, we found it to be very heavy, and weighing about fifty-six pounds. We milled down the barrels and shaved eight pounds off the original weight. We used a stainless steel shaft and some eight inch diameter aluminum tubing for the outer housing, with a flat plate of aluminum inside, and two other pieces, one coming up in the front with a high speed bearing pressed into it, and the other piece with a smaller high speed bearing pressed into that in the rear. The shaft goes through the bearings, with the front bearing holding the shaft and the rear bearing keeps it from tipping up and down. There is also a collar on the shaft to keep it from sliding out. When it was first put together, there was too much weight on the end, which made the assembly sag and bounce. To eliminate this problem, I put a bolt on the end of the shaft and a bolt on the inside. These bolts were pulling in opposite directions stretching it out, keeping the shaft straight with no wobbling in any direction. Then we took the round housing and mounted a base plate inside, which was bolted down to form the receiver with a spinning action. A cosmetic plate with holes in it is slid over the barrels to plug up the end. You turn the gun over to insert loaded Ruger 10/22 ten round magazines. There’s a pistol grip that goes on the top with a button to spin the action. It’s actually a Ford Fiesta starter motor to spin the barrels, but this does not fire them. When you pull the trigger, there is a cable that runs up to the front and pulls a firing tang back and forth. So as you pull the trigger, the tang contacts the triggers as the action spins. The BATF has classified this as a Title 1 long gun because there are six individual receivers that are still all semi auto, and are still being fired by one pull of the trigger. This is the same concept as the trigger cranks that are available to rapidly fire other semiautomatic rifles. The electric motor does not fire the gun, but rather the tang trips the trigger to fire it. You can spin it by hand, and still fire the gun or you can spin the motors and not fire it at all. A real Minigun fires because of the motor spinning the barrels, while mine does not. We currently have a provisionary approval from the BATF, but still have to take the gun to the Tech Branch in D.C. for a final classification. They wanted me to register it as a machinegun and send it to them, but I want to be standing right there in person when they evaluate the gun. I now need to find two weeks time to take the gun in person and finalize their evaluation. If anyone is interested in one, they may be purchased for $7000, and I will make the time to visit the Tech Branch.
SAR: Is it true you are involved in the binary exploding target business?
Ty: Yes, I am helping my friend Scott Hall market binary explosives that he has developed. These are produced by SDH Manufacturing and I sell them through TL Guns. These are of extremely high quality when compared to others on the market. A starter kit is available which is comprised of two eight ounce and five two ounce targets, a funnel, mixing bowl, measuring spoon and a stir stick for mixing the two products together. SDH Manufacturing has included pre-measured activator packets for a precise mixture. Targets can also be purchased individually or by the case. We are currently looking for dealers and distributors across the country. The targets must be engaged by a .223 or larger caliber weapon to function. Individuals should check out their local laws and regulations prior to purchase.
SAR: What’s in the future or on the drawing board for TL guns?
Ty: I have a dual Browning 1919 mount that I’ve recently brought out. These cost $1000. There is a base mount with an upper portion where the two guns mount, as well as two ammunition can mounts built into the assembly. My design utilizes a single trigger to fire two automatic weapons or there is a different bar that you can put a crank on for semiautomatic Brownings. I also have a quad 1919 mount in the works that is similar to the quad fifty where you sit behind the four guns to fire them simultaneously. It’s all pneumatic, the whole thing rotates 360 degrees, and the guns move up and down. I have the base plate done and I’m currently working on the mount. I will use solenoids to fire the guns while the pneumatic piston moves the gun up and down. There is a hydraulic motor with a rubber tire on it that runs on the shield to impart motion. I am also working on two shot burst cams for the M16 to retrofit three shot cams. These run $50. Another new item is an integrally suppressed upper for M11/9’s or MAC 10’s. I also offer an adapter to allow the use of an MP5 stock on the MAC’s. A Weaver rail will also be a part of the suppressed MAC uppers. Another option will be a pop up peep rear sight similar to those available for AR-15’s. Something I really would like to perfect is an American 180 upper for M11/9’s or MAC 10’s. This would allow you to fire the large .22 LR drums on your registered MAC or even a semiautomatic MAC. I have had some discussions with Val Cooper at E&L Manufacturing about this project. I am working on a new .50 caliber suppressor for Jason Hinkle’s Alaskan .50 rifle. I couldn’t believe it, he sent the rifle to me wrapped in used boxer shorts. I used pliers to remove them just in case (laughs). I welcome a challenge in this business and will take on just about any project.
SAR: Ty, it has been a pleasure talking with you. Thanks for sharing your thoughts with our readers.
Ty: You’re welcome Matt.
TL Guns & Manufacturing
SDH Technologies & MFG
1298 N. Douglas Avenue
Cottage Grove, OR 97424
Phone (541) 942-8703
Fax (541) 942-6137
Website: http://www.tlguns.com
E-mail: tlguns@tlguns.com
This article first appeared in Small Arms Review V5N5 (February 2002) |