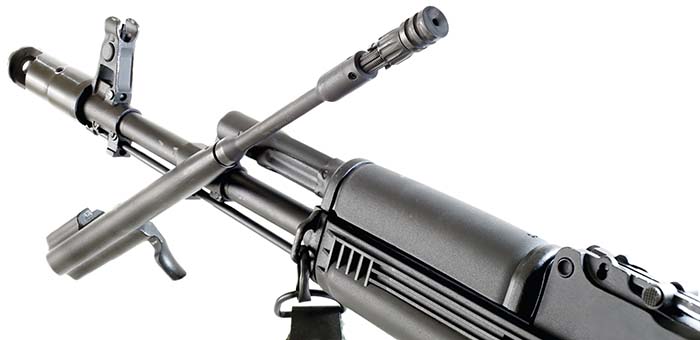
By Alton P. Chiu
Avtomat Kalashnikov, a storied and proven rifle, is adored by both militaries and citizens alike. However, its propensity for vigorous cycling and ejection can cause complications with sound suppressors as well as induce premature wear and tear even when unsuppressed. The KNS adjustable gas piston mitigates this overgassed condition that factory rifles commonly arrive with.
Principle of Operation
Unlike an AR-15 gas block, the AKโs is interference-fitted to the barrel and requires a shop press to remove. Although aftermarket adjustable gas blocks exist, they cannot be easily installed at home. The KNS adjustable gas piston changed that as it only requires one to field-strip the rifle; installation can be accomplished by hand tools. No permanent modification is necessary, so there are no qualms partnering it with a collectable parts kit.
A hole at the tip of the KNS piston channels excess gas to a vent further back on the piston, whereby it makes its way out of the gas tube. The size of the piston vent hole is regulated by a collar in order to soften the recoil impulse and facilitate controllable rapid fire. The collar moves axially along the piston by threading around it like a nut.
KNS produces variants with different thread pitches, hole distances and working lengths to fit the AK family (including but not limited to AKM, Arsenal, Yugo, Krinkov) and even its extended cousins (e.g., Valmet, Galil). For this article, the AGP-A-20S model was evaluated on an Arsenal SLR106F chambered in 5.56x45mm which sported a 16-inch barrel.
Installation
The rifle was field stripped and the bolt carrier, sans bolt, was removed to a vise. Note that the bolt carrier is hollow, and the vise jaws should be applied to the piston to avoid damage. The author then searched for the rivet securing piston to carrier with a good light source in order to remove the OEM piston. During installation at the factory, a rivet was bucked on both sides into the countersunk holes on the carrier. The excess material was then ground down and finish applied over. The one on the Arsenal ran side-to-side and was fairly well hidden. The author prepared the rivet for drilling by first creating a divot with a center-punch. A 5/64-inch drill bit was applied about 2mm deep before the punch and hammer were used in earnest to drive out the factory rivet. The OEM piston could then be unthreaded from the carrier.
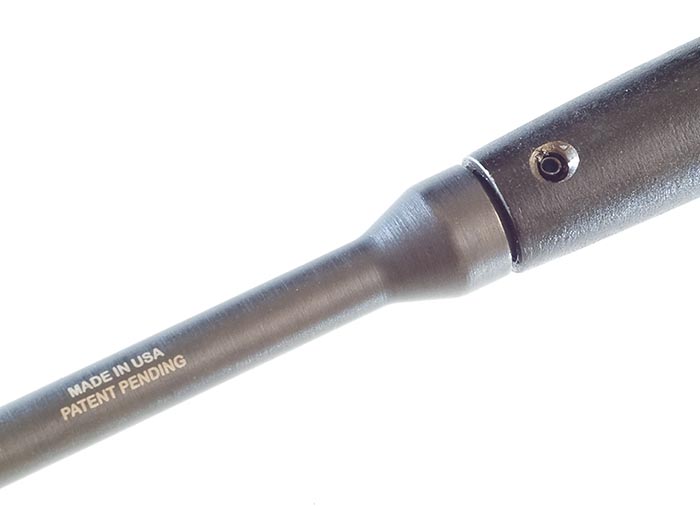
The KNS piston came pre-drilled in two axis so that a hole is visible with every quarter turn. The piston was then threaded into the carrier until the holes were aligned and the roll pin inserted. This pre-drilling saves the end user from needing a drill press as in the traditional assembly process. As with the factory counterpart, there was some wiggle in the KNS piston to carrier fit which did not impede function.
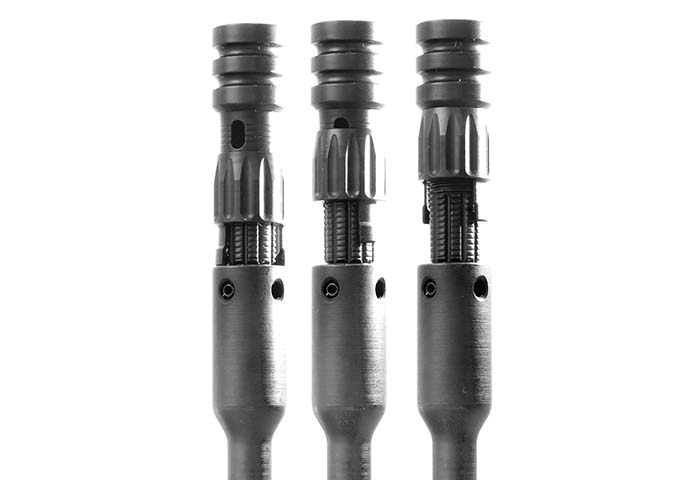
The author found the installation procedure quick and easy, requiring only a standard hand tool he already owned. However, KNS also offers an installation service with same-day turnaround for a small fee.
Shooting Test: Methodology
Since the test rifle is chambered in 5.56x45mm with a 1:7 twist barrel, the author used five different ammunition loads (in both 5.56 and .223 pressures) as the treatments. Changes in group size, point-of-impact and felt recoil (measured qualitatively) form the response variables.
Federal XM193 55gr and XM855 62gr represented the 5.56 pressured ammunition. Wolf Polyformance 62gr HP and 55gr FMJ provided data for .223 pressured ammunition. Lastly, the authorโs handload for across-the-course high power matches (75gr Hornady HPBT, 24gr Ramshot TAC, CCI #41, LC case) provided a data point in between the two pressures.
To reduce the atmospheric effects, targets were placed 25m distant. To reduce the effects of a heated chamber, five shot strings followed by a 3-minute cool down period were observed. To reduce bias from factors such as shooter fatigue and lighting variations throughout the test session, a random treatment (i.e., ammunition) was drawn for each five shot string with no repeats allowed. The strings were repeated until 10 shots were fired for each treatment. To avoid swapping pistons repeatedly, the author first collected factory piston data in one session with KNS piston data collected later. The sights were not adjusted during testing, and a 6 oโclock hold was used on a 4cmx4cm square.
Shooting Test: Data and Discussion
Following KNS instructions, the author started with the collar fully closed and then opened five clicks at a time until short-stroking occurred. The collar was then closed two clicks at a time until reliable cycling was achieved. Wolf Polyformance 55gr FMJ had one out of 10 failure-to-cycle with the OEM piston, but it adamantly refused to cycle even with the KNS piston collar fully closed. Wolf Polyformance 62gr HP had four out of 10 failures-to-cycle with the OEM piston and also wholeheartedly declined to cycle a fully closed KNS piston. While their muzzle velocity data are included in this article for completeness, they are considered โno-testsโ and not further analysed. Note that this is not an indictment on the ammunition, rifle, or piston; it merely illustrates the challenge in achieving reliability across numerous variables.
Using the OEM piston, the empty brass of XM193, XM855 and 75gr handload all exhibited dents from impacting the dust cover and were flung to a 2 oโclock position 15 feet away. The excess gas also drove the rifle off-target with every shot. Using the KNS piston, XM193 cycled reliably with the collar 13 clicks open, XM855 11 clicks open and 75gr handload five clicks open. As adjusted, none of the brass exhibited dents. XM193 and 75gr handload deposited brass at 3 oโclock four feet away while XM855 ejected brass at 4 oโclock 10 feet distant. All three ammunition types cycled notably softer with the rifle staying on target. As the tabulated data shows, there was no discernible difference in muzzle velocity between the OEM and KNS pistons.
On the other hand, plots of the shot groups show a shift in point-of-impact but not in group size. While not statistically significant, the shift does illustrate an interesting trend. 75gr handload shows a marginally decreased group size (0.2 MRAD) with the KNS piston as well as a sizeable lateral shift of the group center (0.9 MRAD). XM855 exhibited a nearly identical group size and marginal lateral shift of the group center. XM193 displayed no change in group size and a diagonal up-and-right shift in group center. While providing a reason would be pure conjecture, it is reasonable to expect needing a re-zero after installing the KNS piston.
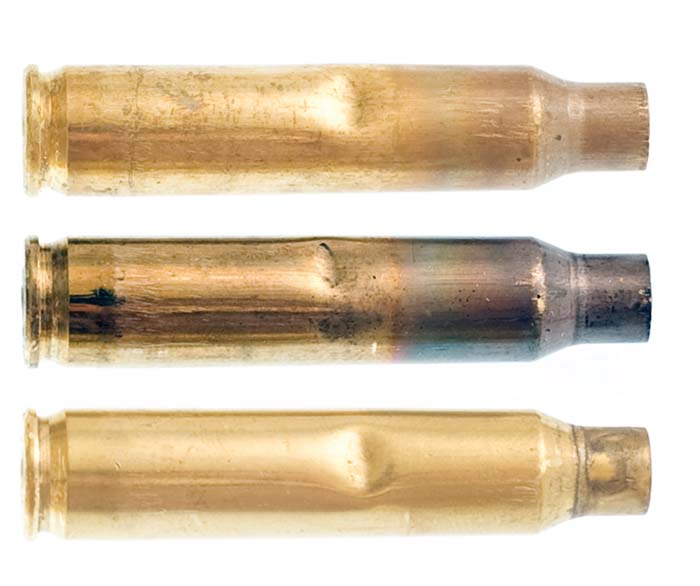
Also, note the horizontal pattern of the 75gr handload compared to the predominantly vertical pattern of the XM855 and the circular pattern of the XM193. It is reassuring that changing the piston did not visibly affect the way the rifle patterns.
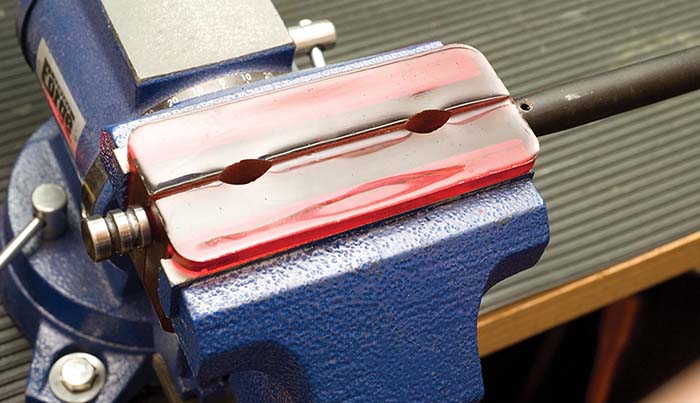
Conclusion
The KNS adjustable AK gas piston is a worthwhile addition for mitigating the overgassed condition that factory rifles commonly suffer from. It notably reduced recoil and muzzle jump while the resulting slower bolt speed should increase parts life. Indeed, this piston may help a shooter win so much that one gets tired of winning.
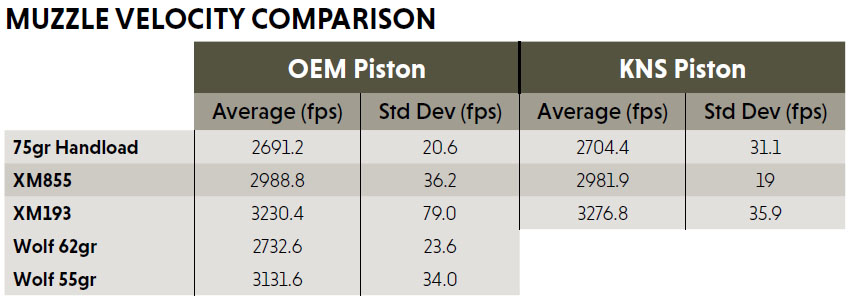
This article first appeared in Small Arms Review V23N1 (January 2019) |