By Thomas Hoel
Few firearms in the civilian NFA world have garnered such wide ranging attraction, and criticism as the short barreled version of the ubiquitous Stoner/Colt military standard- the “Shorty M16”. This “Shorty” label can variously be applied, and be construed to describe, virtually ANY version of the standard M16 rifle with a barrel length LESS than that originally intended by Eugene Stoner in his benchmark design. Despite real-world reasons to the contrary, NFA gun owners have had a virtual love affair with the shorter barreled versions of the design. While trying incessantly to chop the barrel on this weapon down to ridiculous proportions, they still expect the original design, forgiving as it may seem, to perform and function as well and reliably as the standard 20” barreled rifle. The firestorm of reliability complaints can usually be traced to a practical misunderstanding, or unfamiliarity, with the design concepts of the base design as envisioned by Mr. Stoner. As such, this article will attempt to bring to the forefront the practical and mechanical aspects of the synergistic effects of altering the barrel length on the overall reliability and functionality of the design.
In the world-wide catalog of short-barreled designs employing small caliber, small case cartridges, such as NATO 5.56mm M855/M193, there is basically a three way division of mechanical operating systems employed by the various firearm designs: the first and most basic mechanically, is some form of blowback direct acting type action as typified by such guns as the FAMAS, CETME Modello LC, or the numerous H&K incarnations. These rely upon the direct backward force generated against the bolt face in propelling the projectile down the barrel to function the self-loading mechanism of the specific design. Due to this direct action energy transfer, it readily becomes apparent that barrel length, per se, has no relevance upon functional reliability, as the backward impulse imparted to the bolt face by the forward projectile movement remains, in practical applications, nearly constant down to all realistically employable barrel lengths. An HK53K is a good example of this in action; with a barrel length little more than 4”, it functions reliably in the full-automatic mode.
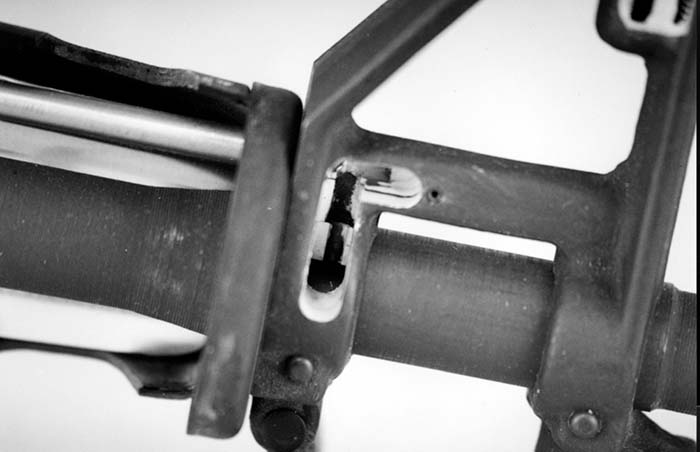
The next type of basic design, and the most commonly encountered, is a gas operated mechanism operating through some form of piston/action rod movement acting upon a bolt carrier to transfer the energy of the expanding propellant gases to work the self-loading action. Guns in this type group include such designs as the Galil SAR/Glilon, Beretta SCS70/90, SIG 551, or Zastava M85. Though they may seem similar in design concept to the M16s’ direct gas system they are fundamentally different for one very basic reason; all gas operated, moving piston type designs allow the face of the gas piston to rest in close physical proximity to the actual gas port on the barrel from which the high energy operating gas stream is tapped. This close proximate relation allows the high energy gas stream to almost immediately, in time relation, begin transferring its energy into mechanical movement of the operating mechanism by impinging upon the face of the gas piston and start it moving the operating parts rearward. The short distance between the gas port orifice and the face of the gas piston, as a function of time, is the critical relation which allows reliable functioning.
The distance between the gas port on the barrel, and the muzzle, is the critical factor on ANY gas operated design because the duration of TIME between projectile passage of the gas port (when high energy gas can begin to act upon the operating mechanism), and projectile exit at the muzzle (when gas pressure instantly drops to ambient atmospheric levels), is the only point in the action cycle that operating energy is available to function the mechanism. Thus, it becomes clear that the most important of design criteria is to allow for a sufficient exposure to the high energy gas stream, in terms of TIME, to consistently transfer energy from the propellant gases to the operating mechanism through the gas system. In almost all piston actuated gas operated designs the size of the gas port hole is determined by the MINIMUM amount of gas (energy) needed to start the piston backward and instill sufficient residual momentum to overcome the mass of the operating parts, plus the recoil spring energy, there-by allowing for the self loading cycle to repeat itself. The port size is then optimized for this minimum level, plus a sufficient reserve to compensate for adverse conditions, or variations in ammunition. The significant design advantage of this type system is that once the piston/bolt carrier is started moving backward at the required velocity, any excess gas can be bled off through a venting system, so it is self compensating for differing ammunition or environmental conditions. By sizing the gas port hole larger than absolutely necessary for normal operation, an operating reserve is built in, yet because of the venting or gas bleed off, there is no worry of excess energy not being able to be dissipated. It becomes apparent then that there are two separate factors, in terms of energy, to be considered. First, it is necessary to allow for the gas stream to instill SUFFICIENT energy to cycle the action through the recoil phase, and secondly, it is necessary to prevent EXCESS energy over and above that required for reliable extraction/recoil spring compression from being instilled as residual momentum into the operating parts. Thus it is that RELIABLE ultra-short barreled, gas-operated designs, like the AKSU-74 or Micro-Galil, invariably utilize a gas piston type action, with a self compensating cylinder provided with overboard bleed vents. Such designs may also typically utilize a muzzle mounted expansion chamber type device to provide for more reliable functioning by providing a fractional time delay in the absolute pressure decay of the high energy gas stream prior to the instantaneous drop to ambient pressure after muzzle exit. These devices, in effect, lengthen the effective distance, and thus add time, between the gas port and the muzzle. It is an absolute misnomer to call these devices “sound moderators”, or believe they exist for any reason other than to improve functional reliability. (Use of these devices may significantly increase the velocity of the bolt carrier, and it would be prudent to adjust gas port size accordingly).
The third type of operating system is, in reality, a simplification of the piston actuated, gas operated system. This is commonly known as a ‘direct gas’ type of operating system because the energy of the expanding propellant gases is transferred directly to the bolt/bolt carrier without the intervening action of a piston or action rod. This is the heart of the M16 design. By simplifying the mechanical end of the design by eliminating a need to employ a separate gas piston or action rod, a significant amount of weight and complexity was eliminated, unfortunately though, so was a significant amount of forgiveness in terms of operational reliability when deviating from the original rifle specifications. The only current production, short barrel, designs to employ this type of operating system are the numerous “M16” variants, and the Daewoo K1. So now with a bit of the mechanical differences explained between various short barreled automatic weapons, some with a reputation for reliable function, some with a not so good reputation, we are ready to delve into the specific functional problems encountered when trying to extract reliability from the M16 design when utilizing other than the original barrel length of 20” (and the usage of the original fixed stock).
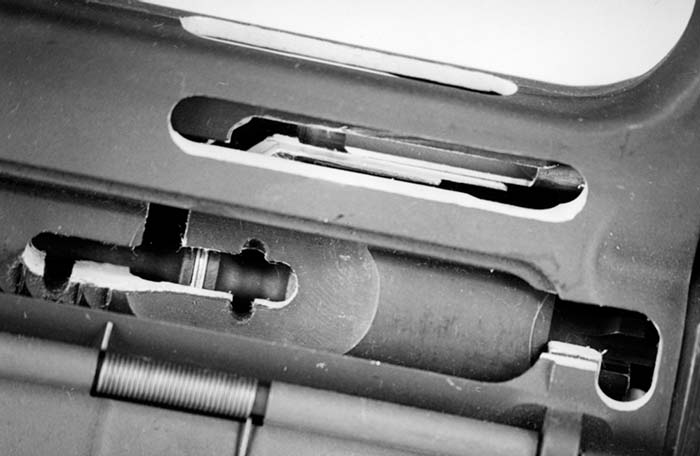
The M16 ‘Shorty’ problem is no mystery to solve. Many people have erroneously attempted to correct mis-behaving guns by altering what they perceive is a “timing” issue related to barrel length. That is to say, they believe that a gun with a short barrel should employ an altered point of release of the hammer by the automatic sear during the final dwell movement of the bolt carrier during the counter recoil stroke to compensate for problems encountered when utilizing a shorter barrel. Timing IS NOT the problem. If a certain receiver will work with a 20” Barrel, it will work just fine with ANY barrel length, theoretically (there may be other inherent problems with a particular receiver, but that is beyond the scope of this discussion). The problem with Mr. Stoner’s gun, when altering barrel lengths, is that the gun and ammo were designed as a SYSTEM, with everything balanced in harmony: gas generation pressures and volume from the cartridge, gas port size, gas tube length, cylinder and piston displacement (bolt carrier and bolt), recoil counter balance energies, etc. Stoner designed his cartridge and gun as a paired system to function in harmony with a 20” barrel, period. The problems arise when solutions are attempted that do not take into account the synergistic effects on the entire operating system when altering a single component or variable in the entire equation. The direct gas type operating system needs to be understood completely before an effective solution can be achieved. While the below discussion is also relevant to the semi-automatic mode of fire too, it will be seen that functional reliability problems often encountered with short barrel M16’s are mostly peculiar to the cyclic mode of fire due to the high speed of the operating components when operating automatically resulting in, most commonly, “light primer strikes” though “short recoil” may evidence itself in the semi-auto mode too.
The M16 operating system (Gas system), to function reliably in the recoil portion of the cyclic operating mode, needs two things from the energy contained in the burning powder charge: 1. Sufficient energy to begin functioning the reciprocating parts and overcome the counter recoil energies contained in case extraction and the recoil spring/buffer mass and, 2. Sufficient exposure to those minimum energies in the time spectrum to overcome these counter recoil forces, complete the extraction cycle, and instill sufficient residual energy in the operating system, as retained potential energy, to fully compress the recoil spring/buffer throughout its’ travel limits. This covers the first ‘half’ of the operating cycle, up to the point of counter recoil. The other potential area for problems is in the portion of the operating cycle that encompasses the counter recoil travel of the operating components during re-chambering and final bolt carrier dwell movement following bolt lock-up.
The two most common problems with these “shorter” barrels ( i.e., barrels with LESS distance forward of the gas port than the standard 20” barrel), are “short recoil” (failure to extract fully and/or re-chamber a fresh round), & “light primer strikes” (bolt CARRIER rebound during counter recoil). These are really very simple to understand in the context of time exposure. The problem with these “Shorties” is NOT, I repeat NOT ‘timing’, it is TIME. There is a direct correlation between the location of the gas port and the remaining length of barrel before the muzzle exit point. THIS IS ALL THAT MATTERS, the length of barrel FORWARD of the gas port. This is TIME. The design substitution of a long gas tube to pipe gas stream energies directly back into the bolt carrier “cylinder”, instead of using a gas piston located in close proximity to the gas port, has the practical mechanical effect of inducing a time delay into the operating system between when the high energy gas stream exits the barrel at the gas port, and when it can actually start to force the moving components rearward. This design “feature”, combined with the extremely short distance from the gas port to the muzzle combines to produce the majority of the functional reliability issues experienced with this particular short barrel weapons system.
Assuming you have not altered the diameter of the gas port hole, if you swap an 11.5” barrel, on an otherwise properly functioning receiver, you may FIRST experience short recoil; this is clearly indicated by the fact the high energy gas stream delivered to the operating system sufficient energy to BEGIN the extraction/recoil cycle but then stopped; it did not instill enough residual energy to overcome the counter recoil forces and movement stopped when the pressure it was exposed to instantly dropped to zero as the bullet exited the muzzle. Had it continued to be exposed to this high energy stream for just a little more TIME, you would have no “short recoil” type functioning problems at all. TIME is the key to building up in the operating system that residual energy, over and above that required to begin extraction, to complete the recoil cycle. Three barrels that ALL work reliably are the 20”, the 16”, and the 14.5” M4; notice anything between them? They ALL have the same or greater (in the case of the 16”) amount of tube BEYOND the gas port to the muzzle. Ever wonder why Colt came up with the 14.5” barrel anyway (from the Colt Model 653)???? It is the least barrel length, while utilizing the other standard carbine components, that held the minimum distance from the gas port to muzzle exit point the same as the standard rifle barrel. Colts’ never did achieve TOTALLY RELIABLE operation of a “Shorty” gun until they went to the 14.5” barrel. Do not believe what you may have heard about the late 1960’s XM177/E1/E2 muzzle device being used as a “sound moderator”; that device was, pure and simple, a pressure accumulator designed to delay the high pressure decay in the operating system for a fraction of a second longer than a plain 11.5” barrel, enough to get “reliable” operation, by instilling just a bit more residual energy to the operating system before the pressure dropped instantaneously at the muzzle exit point.
Mr. Stoners’ genius was evident in his design of the direct gas system using the bolt and carrier as the gas cylinder and piston, instead of using a large separate piston and rod set-up like other designs; this works great AS LONG AS THE OPERATING SYSTEM IS EXPOSED TO THE REQUIRED MINIMUM ENERGY LEVELS FOR ENOUGH TIME. The long gas tube used eats up time; look again at other gas operated “Shorty” designs, they all have a piston which is physically located very close to the gas port; gas stream energy can immediately begin to transfer energy to the piston as soon as it leaves the barrel, for all intents and purposes. Shorty Galils work fine, shorty M16s’ have trouble. Colts’ attempted to solve the problem with the redesign of the operating system to include a gas piston arrangement in their experimental Model 703, work which later showed up in the Taiwanese version of the M16A1, their Type 65 rifle. The civilian ‘Rhino Conversion’ for the M16 also capitalized on that work when that company added, in reverse engineering to Mr. Stoner, a gas piston operating system to improve operating reliability, the same as the new ZM-Weapons Co. is doing today.
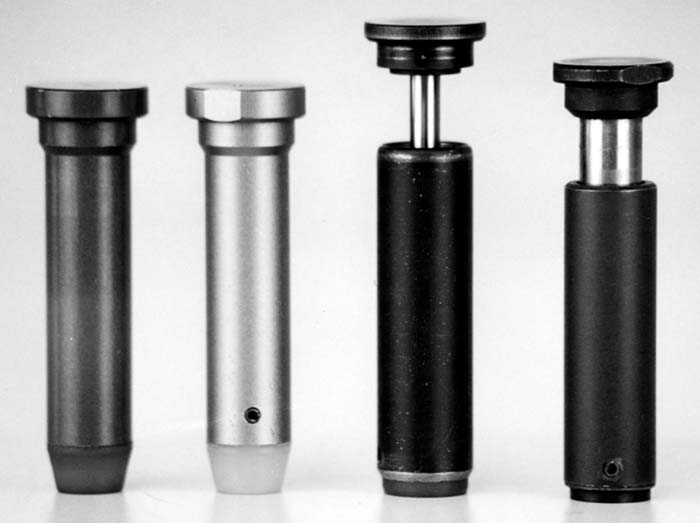
For most people struggling with the problem of short recoil, there seems to be almost a universal belief that the answer lies in increasing the size of the gas port hole in the barrel. Opening up the gas port hole will only add more VOLUME of gas to the system; since, in the practical application, pressure remains nearly the same you will in all likelihood achieve the next problem commonly encountered, i.e., “light primer strikes” causing failure to fire and stoppages after two or three shots. Light primer hits are caused by ONE thing (assuming your gun is mechanically OK to start with); excess counter recoil energy is not being dissipated upon completion of chambering and the bolt CARRIER rebounds off the rear of the barrel extension and the bolt itself literally starts to unlock again, at which point the hammer, traveling only under the spring energy imparted to it from the comparatively weak hammer spring, hits the backward traveling bolt carrier with insufficient energy to send it forward again, relock the bolt head, AND strike the primer anvil with enough energy to cause ignition of the cartridge. Under these circumstances, the hammer has acted basically as an anti-bounce deadener. The reason the gun will fire correctly for MORE than one round, but will usually stop after two or three, is that the face of the bolt carrier and the rear of the barrel extension experience a cyclic increase in what is known as the “coefficient of restitution”. This physical phenomenon is best described as a decrease in the ability of the impacting metal surfaces to return to their original “shape” or “height” following repeated impacts, thereby robbing them of their ability to absorb, or “deaden”, the forces of impact in the exact same capacity following the initial impact. In practical terms, after the first shot the impacting surfaces are unable to provide a sufficient cushion to prevent excessive rearward movement of the bolt carrier until a point is reached to where the energy of the hammer spring is overcome and firing ceases.
If the gas port hole diameter has been increased in an attempt to cure short recoil, you have now most likely ADDED to your list of problems. By observation of your gun following such a ‘fix’, the operating system obviously is imparted with enough energy to go through the extraction and recoil phase but it now cannot dissipate the EXCESS residual energy that the additional gas volume has now imparted to it by drilling out the gas port hole (giving an effective increase in gas flow per unit time). Remember, Stoner designed every element of the rifle system to work in harmony; any excess gas volume, above what he balanced the gas cylinder (bolt carrier) for by specifying the standard diameter of the gas overboard vent holes in the side of the bolt carrier to a specific size, will impact the system’s performance.
The time and distance the cylinder (Bolt carrier) travels while moving to the rear and unlocking the bolt, relates to the point where the remaining gas charge is dumped through the ports. The retained gas in the system continues to ADD energy during recoil, energy which cannot be dissipated by the spring energy of the recoil spring and buffer mass. This increased energy, having been transferred to the recoil spring/buffer assembly, will manifest itself as INCREASED driving force during the counter recoil cycle (read ‘cyclic rate’). This is more energy than the carrier/bolt/barrel extension were designed to absorb during re-chambering and so the carrier ‘bounces back’ after chambering and bolt lock up.
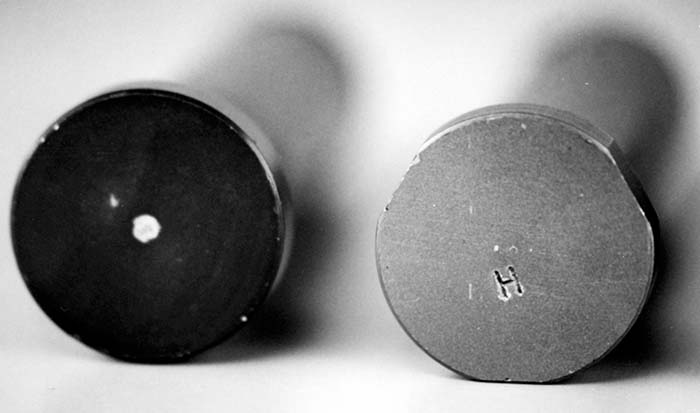
The solution to fixing “shorty” problems then is simple, but most people don’t want to believe it. You must return the TIME element in the operating system (Gas system) to the designed level of the 20” barrel standard, while maintaining the original energy levels designed for in the recoil system. The primary reason that excess counter recoil energy is induced into the operating parts is that the gas port hole has been over ported in an attempt to cure short-recoil, but what causes the gun to display a tendency to seemingly NEED that extra ‘power’ in the first place? This is the real START of the problem(s)! The base cause for this then can almost always be traced to ONE element in the system, the barrel, or more correctly the chamber of the barrel. With rare exception, the barrels available from commercial sources are produced with chamber dimensions of SAAMI specification to the .223 Remington caliber, with differing minimum and maximum tolerances around that general specification. Commercial .223 Remington IS different from 5.56mm NATO chamber dimensions, and Colts’ proprietary chamber dimensions are different still. More importantly to our case at hand, if there exists a variance in tolerance in these commercial barrels it usually goes toward the “tight” side in a vain attempt to advertise the barrel in question as being more “accurate”. The problem is that in a MACHINE GUN you DO NOT desire absolute accuracy as a first criterion in designing barrels; it is more important to design in any attributes that would lead toward a higher degree of functional reliability. It should thus be obvious now that what we seek in a chamber of a MACHINE GUN barrel is a dimensioning that allows RELIABLE chambering and extraction, using the LEAST system energy possible. This is the heart of many “troublesome” short barrels installed on civilian M16’s, and why they won’t function reliably.
Almost without exception, the commercial producers of “M16” barrels are selling the exact same barrel, with the exact same chamber dimensions, as those they sell for use in semi-auto AR15’s and clones. Because SOME individual barrels MAY have a chamber dimension that is closer to NATO spec, they may run fine, but most will not. And to compound the problem, most commercial barrels are now sold as being Chromium plated in the chamber area which renders them impossible to alter the chamber dimensioning (be VERY careful about so called “polishing out” a chrome chamber; it generally CAN NOT be done in a uniform manner!). And so, because the chamber dimension is not optimized for high speed full automatic cyclic function, we immediately introduce into the equation a factor of high required extraction energy levels; this is the reason most people want to open up the gas port diameter. It should be noted now that the standard size of .063” for a gas port in a 20” barrel is a dimension optimized for all the preceding reasons, and that because of the reduced TIME element of the short barrels’ gas port-to-muzzle distance, this size is often increased as a compromise to the time factor by adding additional gas volume-per-unit-time, as described above. Since the chamber dimensions of commercial barrels are known to vary widely, it is generally impossible to state with certainty an optimized gas port hole diameter for a specific barrel length such as 10” or 11.5”. The next compounding problem is that a gas port hole selected to give reliable function without exhibiting ‘short recoil’ tendencies may already have reached an energy level in the operating system that will induce ‘light primer strikes’ from excess energy levels in the counter recoil stroke. There is a very fine line between curing ‘short recoil’ and inducing ‘light primer strike’. The best guarantee that a short barrel will function reliably in the cyclic mode is to start with a barrel that was INTENDED from the point of manufacture to be used in a machine gun, as the chambering dimensions will already have been optimized for this intended usage. It is far better to obtain a barrel of ANY length that is a MIL-SPEC M16/A1/A2 new/replacement/surplus part, and then alter the length to suit and re-mount the front sight/gas block assembly in the proper position, than it is to gamble on a ready made “shorty” barrel of unknown pedigree. This DOES NOT have to be a “Colt” barrel; any barrel that can be positively identified as being MIL-SPEC manufactured as an original part or a replacement or spare will do, such as those made past and present, by H & R, GM-Hydramatic, FNMI, ‘Bushmaster-Quality Parts’ (M4 type), or DIEMACO. The trick is to get a “machine gun” barrel from the outset, as then your chance of developing a cascading series of problems while trying to “fix” a problematic gun will greatly diminish.
Since most people use a “CAR”, or telescoping, stock with the short barrels our problems are compounded again. To begin with, the telescoping “CAR” stock assembly, by its’ physical dimensions, has a reduced capacity to absorb recoil energies compared to the original full size fixed stock/recoil spring/buffer assembly. This already puts us at a disadvantage! Remember, any increase in recoil spring RATE, in an attempt to absorb excess recoil energy, will cause an increase in counter recoil velocity leading to light primer hits. (Conversely, there is an incorrect belief that cutting or shortening the CAR recoil spring is the correct answer; while it MAY work for a PARTICULAR combination of barrel/receiver, you are seriously compromising the longevity of your expensive weapon by tremendously increasing operating stresses!! Do NOT cut springs, unless you don’t care for your weapon!!). The most logical place to cure the problem(s) is in the recoil assembly, but that requires some expanded understanding of its’ capacities and inherent weaknesses. Adding mass to the recoil assembly in the form of a different buffer is not a good solution as this only causes an increase in the striking energy of the bolt carrier on the barrel extension, and the added mass may not be sufficient to discourage rebounding. What IS desired is some form of energy ABSORBING function contained within the recoil assembly, or barring that, some form of anti-bounce device to deaden the eventual bolt carrier rebound energy before hammer release. Testing by trial and error for a PARTICULAR barrel/stock assembly may result in satisfactory performance, but do not be tempted to alter the recoil absorbing abilities of the normal recoil spring/buffer assembly, and it is also unwise to significantly increase the mass of the buffer due to increased stresses developed. If you must have a short barrel and can’t make a CAR stock assembly function reliably with your particular barrel used, simply switch to a standard fixed, full length stock/recoil assembly. The increased length of recoil travel and buffer mass increase will almost always give reliable function with a short barrel, without undue stress and strain being imposed on the gun. For those that must use a CAR stock assembly, the most practical thing to do is to obtain, as an “off the shelf” component, one of the “Hydraulic” buffer units currently available. These are a mechanical adaptation of a simple hydraulic cylinder in which the front end of the buffer acts as the piston, acting against a fluid medium, to compress an internal spring, thereby absorbing a great deal of recoil energy without transferring it to the recoil spring. This simple action does much to prevent excess counter recoil energy and its’ attendant problems. By installing this singular component, it will allow the gas port hole to be opened up for reliable function without any further ‘short recoil’ tendencies, while eliminating any problems with ‘light primer strike’. There are other possibilities to solving this delicate balancing act between curing ‘short recoil’ and inducing ‘light primer strike’, but they all require a LOT of advanced weapon modification. Such things to try would be re-balancing the gas venting equilibrium by resizing the vent holes in the bolt carrier side; adapting an expansion chamber type device into the gas tube itself or the front sight/gas block; incorporating on the rear section of the bolt carrier a sliding mass anti-bounce weight device; incorporating on the relieved front face of the bolt carrier a section containing an impact deadening material, such as phenolic composition plastic; or using a set of variable increasing rate telescoping recoil springs.
With the advent of the M16A2-M4 Carbine, Colts’ has for the first time acknowledged that the gun comprises a DEDICATED operating system, utilizing components designed to operate in harmony as a short barreled weapon. The basic system comprises the barrel with Colts’ proprietary chamber dimensions, a modified angle on the cartridge feed ramps, and a modified recoil spring operating in unison with the so called “Hydraulic” buffer unit, or more currently, a one ounce heavier non-hydraulic buffer called the “Heavy buffer”. This Heavy Buffer is marked on the face with an “H”. What is significant is that ALL these features are designed to help alleviate the above mentioned problems, while retaining the ability to posses a usable reserve of available operating energy for adverse conditions, without sacrificing functional reliability in the cyclic operating mode. By employing the hydraulic or heavy buffer unit they can “over port” the barrel gas port to give a valuable reserve of energy for reliable extraction and then dampen it out on the recoil stroke to prevent excess energy build up in the counter recoil stroke. The hydraulic buffer unit is no more than a mechanical means of returning the time element, and thus reliability, of the standard rifle barrel gas port-to-muzzle relationship by inducing a mechanical increase in the amount of recoil energy absorption prior to the end of the recoil stroke. And as the operating parts reach their final dwell movement of the counter recoil stroke, the hydraulic buffer can act as an anti-bounce deadener by allowing any rebound energy to be absorbed in the movement of the hydraulic piston.
For most civilian shooters, it would be most practical to follow Colts’ lead and simply substitute the hydraulic or heavy buffer, after determining the correct gas port hole size for their particular barrel being used. With a better understanding now of the synergistic effects of the change to a short barrel, the civilian M16 owner should be able to assemble a reliable version of the “Shorty M16”, or cure his particular guns’ ill manners!!
This article first appeared in Small Arms Review V1N4 (January 1998) |