By J.R. Moody
The Madsen Saetter was designed as a General Purpose Machine Gun (GPMG) during the 1950’s. Armies throughout the world were rearming geared towards the new concept of the GPMG. These machine guns allowed advancing troops to meet out a high rate of accurate fire, and it also served a dual role as a heavy machine gun, tripod mounted, for perimeter defense and in tank and troop carrier use. The high rate of fire was possible because the quick-change barrel enabling the operator to change barrels before over heating took place. This allowed one barrel to cool while firing another. The German army of WWII had pioneered this concept.
The Madsen Company was no stranger to the firearms field. Based in Denmark, they manufactured one of the most prolific machine guns of the first half of the 20th century. The Madsen magazine fed light machine gun. Later, the company moved on to design the Madsen Saetter (GPMG) which was a much newer innovative design. This system incorporated many facets of other successful guns manufactured previously. The Madsen Company saw no real reason to reinvent the wheel. The Madsen Saetter (GPMG) employed the locking system of the Russian RPD, which consisted of levers being forced out into the recesses of the receiver to lock the bolt. The gun also utilized the extremely reliable belt feed mechanism of the German MG42 system.
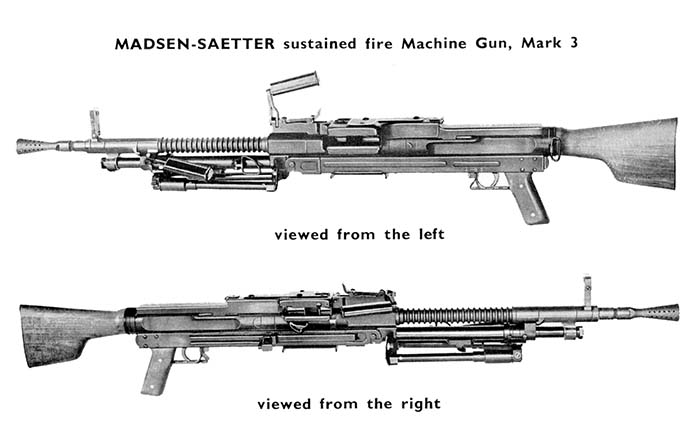
This well made system, typical of Madsen, was designed with a capability to be manufactured in many less developed countries. Being gas operated with a piston op-rod system, the gun had a 3 position gas regulator which would enable it to fire in adverse conditions. It also enabled it to change the rate of fire as needed.
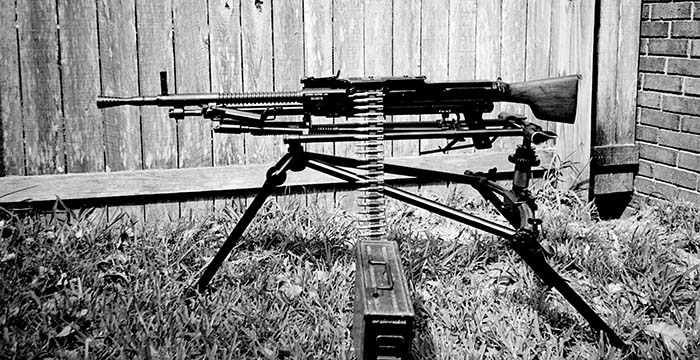
In the 1950’s an early version of this gun, the Mark I, was tested in England by the British army for possible adoption. The more expensive but very reliable FN MAG succeeded in beating out all other competitors, including the Madsen. All this came a little too late because the lion’s share of international sales had now gone to the FN MAG or the West German 42-59. Madsen had to be contented to sell to a few small South American countries. It was only adopted and manufactured under license in Indonesia.
In researching the Madsen Saetter system, it is quite evident that the main reason that the system didn’t compete in the world market more favorably was the fact that the gun wasn’t fully developed for trails until the third model or the Mark III. Unfortunately when the British rested the Mark I at their trails, they found it unreliable. This hurt the marketability throughout the world.
Thus the Madsen Company had to make this system more reliable. Madsen initiated the following changes from the Mark I to the Mark III, (the Mark II was virtually the same as the Mark I). The barrel was shortened by four inches but made much heavier to dissipate heat more efficiently. The barrel locking mechanism was strengthened. The front sight was strengthened and made to fold out of the way when not in use. This decreased the likelihood of damage. The bipod was strengthened and lightened by changing its manufacture from steel to aluminum. Sling swivels were added, the Mark I and II had none. The top cover was reengineered to allow closure whether the bolt was forward or in the rear cocked position. The Mark I and II only allowed the top cover to be closed if the bolt was in the cocked position. The Mark III incorporated a belt box holder under the center of the weapon which enabled the soldier to utilize a neat and well designed 50 round box. This allowed troops to move without the problem of getting belts caught on bushes, trees, or flopping about in the sand. The trigger guard was substantially beefed up on the Mark III. This may seem unimportant, but all the Madsen Saetter machine guns utilized the trigger guard as the rear lockup mating it to the traverse and elevating mechanism on the tripod. This strengthening of the trigger guard was crucial since a machine gun not tightly locked to the tripod would not be accurate or reliable. One of the most important aspects of improving the reliability of the Mark II I over the Mark I or II, was the enhancement of the charging handle lock which prevented the non-reciprocating charging handle from moving about and jamming the gun. After the weapon was changed, the new lock kept the handle in the forward position more securely. All the above enhancements to reliability of the Madsen Saetter system would have greatly helped. Unfortunately, it all came too late.
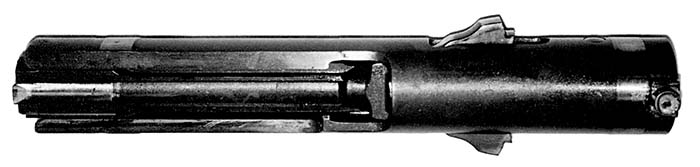
The Madsen Saetter machine gun was manufactured typically in 8mm. 30.06 and 762x51mm. But it appeared that if desired, one could change caliber by changing the barrel, feed tray, and in some cases, the ejector. This would enhance logistics considerably. Also, the gun utilized the German pattern non-disintegrating link belt, but Madsen made their own which differed slightly. Both worked just fine in the Madsen Saetter Mark III.
The Madsen Saetter tripod was an engineering marvel; light weight, easy to fold. It provided a very secure firing platform, furthermore accuracy was enhanced because the mount was buffered. This meant that the machine gun while firing recoiled very gently in a state of equilibrium due to the buffered system. Madsen did well with their gun mounts, so well that they stopped manufacturing weapons altogether and concentrated their efforts on making gun mounts for all the world’s weapons including their old competitors, the Belgium FN MAG and the West German 42-59. With their new focus on machine gun mounts the Madsen Company changed their name to Disa System Group of Denmark.
Madsen-Saetter Field Stripping
1) Perform a cocking motion by pulling the cocking handle fully back so that the action-head of the Bolt Assembly engages the sear; press the safety catch back as far as it will go )to position “Safe”)
2) Open the feed cover by pressing the feed cover latch and turn the feed cover and the feedway platform to a vertical position; ensure that the chamber is empty and let the feedway platform come down to its horizontal position.
3) Remove the barrel by swinging the barrel handle forward and turning it to the right vertically and, after pushing it forward, remove from the receiver.
4) Push forward the safety catch to “Fire” and let the moving parts go forward by pulling the trigger. At the same time control the forward movement by holding the right hand on the cocking handle.
5) Remove the Butt Assembly by pressing the trigger housing latch with the left thumb and with the right hand turning the butt stock 90 degrees clockwise, or counter-clockwise, and pulling it straight to the rear out of the receiver. (If the gun is not resting on a table or similar support, the left hand should be held under the trigger housing or the pistol grip to prevent the Trigger Assembly from swinging downwards).
6) Remove the feed lever cover by pulling it straight backwards as far as it will go and lifting the rear end upwards; the feed lever is now uncovered and should be removed by lifting it upwards out of the receiver.
7) Place the gun with its right side upwards, and remove the trigger housing by swinging its rear end with the pistol grip to the right and then disengaging the hooks at its forward end from the two trunnions on the receiver’s barrel support block.
8) Remove the Gas Piston by pulling it backwards until its head is just outside the clearance in the bottom of the receiver. Free it from the coupling-groove of the bolt carrier and, after turning it slightly clockwise, the Gas Piston can be pulled completely to the rear out of the barrel support tube.
9) Remove the Bolt Assembly by letting it slide rearwards out of the receiver.
10) Strip the Bolt Assembly – with the nose of a cartridge press the bolt carrier pin as far out as possible to the side so that it can be removed by the fingers. Pull back the action-head and remove the bolt by sliding it straight backwards out of the bolt carrier, the firing pin, with its spring, will then slide backwards out of the bolt. The bolt-locking-pawls should not be removed from the bolt during field stripping.
11) Assemble in reverse order.
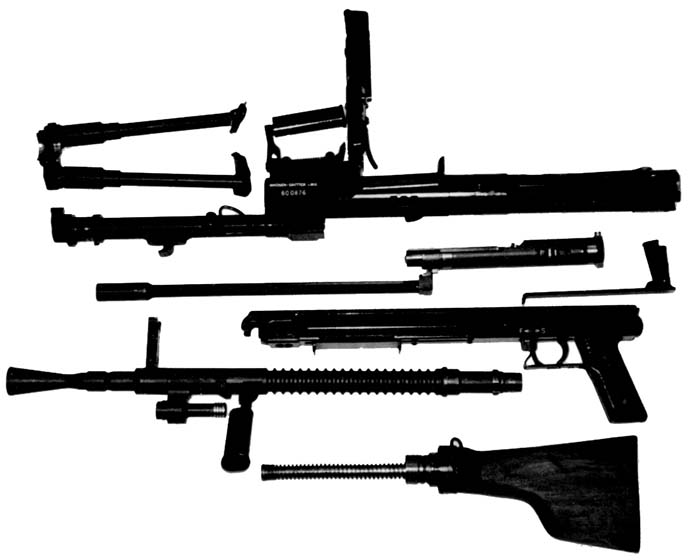
This article first appeared in Small Arms Review V1N11 (August 1998) |