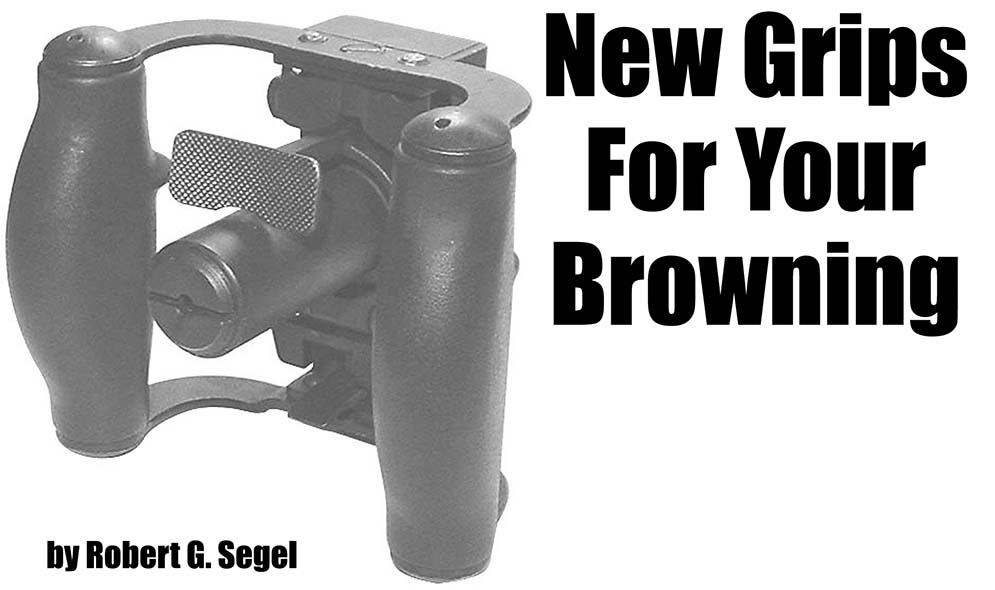
By Robert G. Segel
Jon Moranโs father, Thomas Moran, Jr., was an aerial gunner on a Ford built B-24L in the 15th AAF during World War II with the 49th Wing, 461st Bomb Group, 765th Bomb Squadron at Toretta Field near Cerignola, Italy. His office was an Emerson Electric A-15 nose turret where he spent hours in absolute boredom and moments of sheer terror. Jon grew up hearing many stories of his fatherโs adventures. When his father passed away in December, 1998, Jon came across his scrapbook and it rekindled his childhood interest in his fatherโs experiences. It ultimately led to his building a website devoted to his dadโs crew and their experiences in Italy during the war. (www.liberatorcrew.com)
Jon enjoys going to air shows to hear the sweet sound of the old piston driven warbirds and tour static aircraft to view the armament up close. During one of these outings, at the Oceana Naval Air Station in Virginia Beach, he was doing a walk-around of a fine old B-25 Mitchell bomber. Flexible aircraft guns typically have the Bakelite ergonomic finger rest type of spade grip handles. The nose position of the .50 caliber Browning machine gun on this aircraft had what appeared to be dowel rods in place of the original handles. Upon returning home, Jon scoured the Internet looking for a source for the original handles โ and found nothing.
As it happened, he was also working on building a set of spade grips for a semi 1919A4 that he had recently assembled. The 1919A4 was never issued with spade grips, but the .50 cal. was too big for the space he had in his study, and the cost of a full-auto in any caliber far exceeded his means. Nevertheless, he wanted something that might give him the โfeelโ of the air gunnerโs tools, and the 1919 seemed a reasonable compromise. However, once again, he was faced with the lack of availability of finger rest spade grip handles. Making his own seemed the only solution, so once again he went to the Net. He researched modern resins and then set out to find someone with some casting experience. He found a very nice gentleman who maintained a site devoted to casting GI Joe heads out of modern polyurethane resin who was kind enough to teach him the basics of the process. Now all he needed were two things โ vintage spade grip handles to use as patterns, and someone willing to send them, on loan, to a perfect stranger.
Jon had become a member of the 1919A4.com board during his semi build project and put out feelers to the group to see if there might be someone who could help him. Almost immediately he got a response from John DePasquale, who owned a Bell Aircraft gun adapter of the type used at the waist positions of the B-17 and B-24. He was kind enough to remove the rear section of the adapter and send it to Jon.
At this point, Jon was following conventional wisdom and making separate mold halves, using aluminum plate to build the boxes and putting in pins to index the two halves. It was very time consuming, and it presented an obvious problem: the original castings have mold lines and his mold was recreating a second line. Any attempt to remove the lines through sanding and polishing opened tiny bubbles which had formed during the casting process.
Jon actually had two problems: the seams, and a lack of continuity in the set resin. To remove the bubbles he was going to have to degas the resin in a vacuum before pouring it into the molds. A good vacuum chamber was in the neighborhood of $1,000, which was out of the question. He looked for an alternative, and remembering the bell jar vacuum chambers in his university biology lab, he set out to make his own. He bought a $13 Venturi vacuum pump from Harbor Freight, a compressor to drive it, and made a chamber by inverting a tongue depressor jar on a stainless steel plate using a sink basin gasket for a seal. That left the problem of the seams. He had to be able to produce a casting that was finished when it came out of the mold. If it required any improvements to the surface at all it was going to be far too labor intensive to produce for sale and keep the price down. While he had not planned to market these, he was already $2,000 in the red from the expensive mold making rubber, casting resins and compressor, not to mention hundreds of hours of R&D to develop a feasible casting system. What started out as a simple effort to produce a few handles had snowballed into a project he now felt obliged to carry to its conclusion. He now wanted to be able to provide handles for aircraft and weapons restorations and was his chance to contribute something to the effort.
As many talented people tend to do, instead of counting sheep at night, they usually fall asleep working on some engineering problem related to whatever project is at hand. This is invariably where their best thinking is done. He needed a finished casting with no seams, which meant a seamless mold. But he could not see how he would get a casting out of a solid mold, even a rubber one. Nonetheless, he decided to make a one-piece mold anyway and see where it led. He set the pattern on an aluminum plate. The pattern had an extension at the top to create a reservoir for resin over-pour. He then placed a length of aluminum pipe around the pattern to create a containment, and filled the assembly with degassed mold rubber. Once set, the bottom plate and containment were removed to reveal a cylindrical mold, open at both ends, containing the pattern. Now he had to figure out how to get the casting out of the rubber mold. His first attempt produced a perfect casting but a damaged mold. No matter how hard he tried, he couldnโt seem to massage the casting out of the flexible mold without tearing the mold. On a hunch, he attached a 2-inch PVC cap to an air nozzle, placed the open end of the end cap over one end of the tubular mold, and aimed the other open end of the mold into a pile of rags. Giving it full air, out popped a perfect casting into the rag pile. The air inflated the rubber, which released the casting and allowed it to pass out the now expanded end of the mold. He had a system!
During this phase, Kris Hartwig of Hedgehog Mfg. contacted Jon. He knew Jon was working on this project and he had just purchased an NOS (New Old Stock) spade grip for a Browning ANM2. He sent Jon the spades and he was able to get good molds of the handles as well as an up close look at the standard GI mounting system, a 5/8 inch splined tube. Because he had been unable to find any information on the ANM2 spade grip, he took the opportunity to reverse engineer the spades and created a Website with images and drawings of the entire spade grip assembly. Jon sent the original spade grips back to Kris with a set of the handles he made to use as range grips, or whatever.
During the next phase of development everything was refined. When he poured the resin around a 5/8-inch splined brass tube, he got a finished handle that was a direct replacement for the ANM2 original. He worked with the color to match the original brown, made a press to remove the tube from the casting, and came up with a clean way to part the resin over-pour from the handle ends. He found that he could use almost any center rod in the mold, so he could make handles for custom spade grips adapting to whatever mounting hardware was being used. The molds had a limited life, as the repeated inflating eventually caused them to weaken and blow apart. But they were much easier to make than the tiresome two-part molds and the perfect seamless castings could be made no other way.
The basic GI spade grip handle is mounted using either a plain or splined tube. The round handles employ smooth tubes, but because the finger rest handles must be kept facing forward with a 15 degree toe-in, splines are added to the tubes. These splines run the length of the tube and fit into notches in the brackets. Drilled or slotted truss head spanner screws complete the installation. As a rule, the handles are 4-1/8 inches in length, whether on a .50 caliber Ma Deuce, or a .30 caliber ANM2, and are made of banded wood (early) or Bakelite. The Bakelite handles are usually brown and have a slight texture to the surface.
The K12 adapter, however, is an exception to the rule. The K12 handles are 4 inches in length, and unlike the earlier aircraft handles, the finger rest does not project out the sides, but only forwards. The seams are front and back instead of on the sides as with the ANM2, and the surface is smooth and shiny. The handles are integral with the tubes, which project out the bottom so they can be pressed into the rear adapter casting and then secured with a single cross pin.
The Browning FN30 uses the American ANM2 system, except that the spline is short and only at the top. Additionally, the handle is 1/8 inch longer than the USGI, or 4-3/16 inches. A new pattern had to be made to add the additional length to the center.
No one could have guessed that taking note of a dowel rod at an air show would lead Jon to bring an obsolete handle back into production while developing a seamless mold system. Anyone who has spent any time with these vintage old war-horses knows that reviving them and learning their history often leads us on a wonderful journey. Such is the case that, thanks to Jon, we all benefit.
This article first appeared in Small Arms Review V10N6 (March 2007) |