By John Bibby
The premise for this article is that a Dillon 650 XL reloading press can be used to create precision rifle ammunition. A slightly different methodology will need to be employed, and the production numbers will fall based on the precision bias, but it can be done and done much more quickly than using a single-stage press. The methodology for this article was NOT to provide maximum precision; but rather to compare precision while eliminating as many variables as possible. Due to starting with a caliber this author does not normally load for and using a loaner Precision Rifle in that caliber, I did not have a dialed-in load. With this in mind, I did not adjust the seating depth to chase the best possible group size. By eliminating this process, I saved five (or more) ladder tests and a ton of time and range trips. I will only be using one COAL at 2.800 inches. (Determining COAL, or cartridge overall length, is about finding the optimum length for hand loads, for your rifle.) This will limit my ability to get the perfect load, but it will give an equal basis for both single-stage loading versus using the Dillon 650 XL. It is also the most common COAL for factory ammo. Again, the goal of this test is not to define absolute precision, but to determine the difference in precision between single-stage versus progressive loading on a Dillon 650 XL.
The initial modifications to the Dillon 650 XL loading technique are to completely remove the powder measure and substitute hand weighing of the powder. The automated powder measure system integral to the Dillon 650 is a good system; but precision reloading requires much more consistency than just โgood.โ
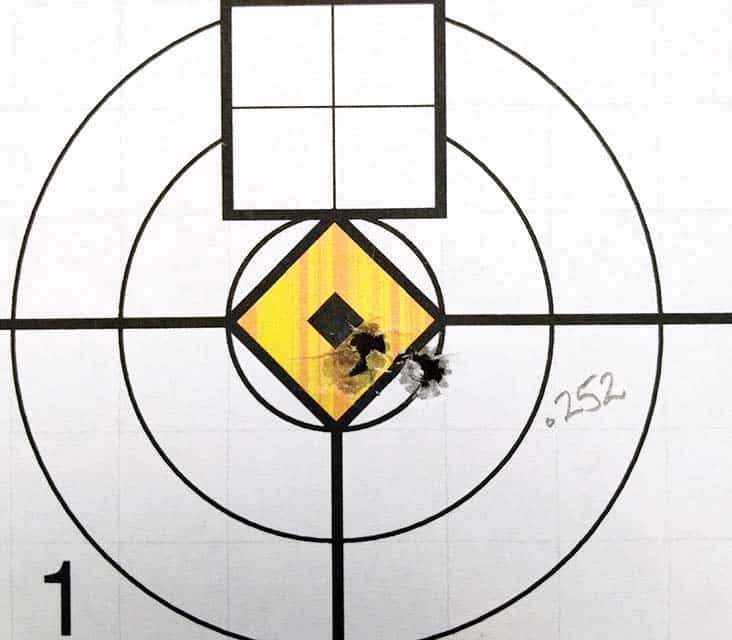
Case Prep
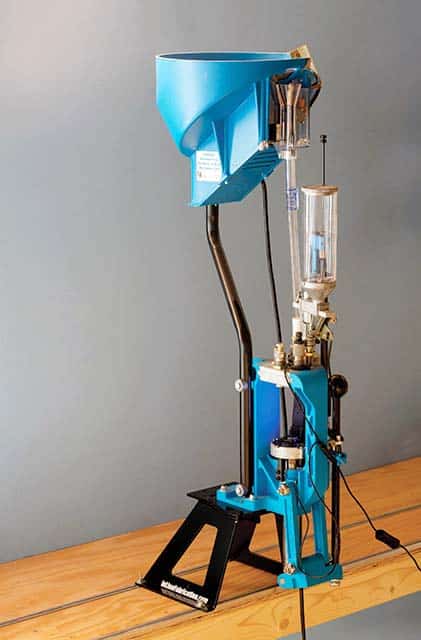
Case prep is done the same regardless of loading method. Starting with brass from the same lot is always best. All my case prep is done manually. The first step is to tumble the brass with walnut shells mixed with Lemi Shine to remove contaminants. I do this even with virgin brass. It helps to insure all brass is similarly lacking in production gunk and oils. Next, is to lubricate and full-length resize to insure a consistent neck diameter. Then all brass is measured and trimmed to a standard length. The primer pockets are uniformed, and the primer flash holes are deburred. The last step is to chamfer the trimmed necks and deburr them. After all this is done, I sort cases for weight uniformity. This gives a very uniform starting position for all brass.
I also sort the bullets by โlength,โ prior to loading any projectiles. This is actually done using a comparator which checks a set spot on the ogive, as that is where the bullet engages the rifling. The comparator method is much more precise than measuring overall length. A second measurement needs to be done if you are using magazines to insure the ammunition will still be below maximum magazine length. The bullets are grouped in +/- .001-inch groups. Any oddballs are reserved for the practice round or barrel heating loading only.
For rounds used in competition, I never use virgin brass. It is best to use brass that has been fire-formed in the competition rifleโs chamber. The once-fired brass is then run through the above process, except only the neck is resized. With this said, the issue with virgin brass, is a higher tendency towards flyers, which I do not see as an impediment during practice.
For my single-stage precision reloading, I prime manually with a Sinclair hand primer. This provides very consistent primer seating depth but is extremely slow. By automating this portion of the process, it recovers some of the time lost with manual powder weighing.
The removal of the powder measure allows for precise manual powder weighing. It also removes the need for a powder check station as each charge is individually measured and added. I kept the check station as a safety and because I have one more station than is required. I do not crimp precision ammo. Crimping tends to have a detrimental effect on run out as well as provides variation in grip to the projectile. With this in mind, the final COAL die is put in place of the crimp die.
For my experiment, I used a Gem loading scale that measures to (theoretically) 0.02 grains of powder. In practice, it is more like 0.04 grains. This is still magnitudes more precise than most powder measures at +/- 0.1 grains. The scale is affected by fluorescent lights, so be aware of that concern. The ballasts in fluorescent lights create electromagnetic interference. This tends to increase with the lampโs age and creates instability in the reading of the charge for the Gem scale. My fix to this issue was to change the lighting in my reloading area to LEDs. This powder set-up requires manual trickle charging and manually pouring powder into each case. This dramatically slows down production compared to using a powder measurer. However, precision is the end goal, and this allows for very consistent powder weights. My goal was less than 10 fps variance for extreme spread. With the sin gle-stage press, the ES averaged 9 fps. The modified Dillon generated an average of 13 fps.
The first seating die is set to 0.003 long. The second seating die is set to the exact COAL desired. This is the same method I use in single-stage loading, and I am usually able to stay within +/- .001 using this method. This compares to roughly 0.003 to 0.005 when I do a seating as a single step. In my experience, the fat part of the curve (70%) stays at the +/- 0.003 range with the single seating method. This is all I ever do for non-precision ammo, as it is perfectly fine for that use. But for precision shooting, it is unacceptably sloppy. It is still a 0.006 variance from shortest to longest length; this will greatly increase the variance in velocity from round to round.
Even then, 30% of the ammo falls outside that range. By going with a rough first seating and a final second seating, the fat part of the curve jumps up to +85%, and in that part of the curve, the variance is reduced to +/- 0.001. Automating the tighter tolerance helps to recoup time spent reseating. As you can see, it also reduces the variance greatly both in COAL and in percentage that fall outside the desired parameter. Any of the loaded cases that are still too long could be pressed again on a single-stage press to bring them into compliance. Any cases seated too short are sorted for length. Cases that do not exceed 0.002 short are used as fouling or barrel warming rounds. Any that exceed 0.002 are disassembled. The brass on disassembled rounds is checked for proper case prep / neck tension, and the bullets are rechecked for proper sizing as well.
The above process produces +95% usable ammo. Most of the remaining โfaultyโ ammo is usually traced back to poor case prep or an over- or undersized bullet.
I should note that some people sort for weight uniformity before starting the case prep process. I find this to be wasted time if one is starting with a known high-consistency brass. The lack of uniformity in this type of brass is usually fixed in the resizing/trimming stage as the discrepancy is usually a function of slightly longer brass or extra material in the primer pocket or flash hole. When fully prepped, this tends to disappear. In brass that is not known to be superbly consistent, sorting before and after case prep may be warranted.
Results
In single-stage loading, I was able to produce 30 complete rounds in 80 minutes starting with fully prepped brass. Remember, no attempt was made to determine if this rifle โlikedโ bullet jump or jam. Proper determination of this preference can easily remove 0.100 inch or more from group sizes. A better shooter than me may well be able to tease out another 0.100 inch from the groups. As an indication, Don Fraley routinely achieves groups in the high โ1sโ to low โ2sโ with this rifle. Considering I ran magazine-length loads, I was quite happy with the group sizes.
- The best group was 0.252 inch;
- The worst group was 0.683 inch and most likely involved user bobble;
- Five groups were clustered between 0.360 inch and 0.395 inch with an average of 0.380 inch.
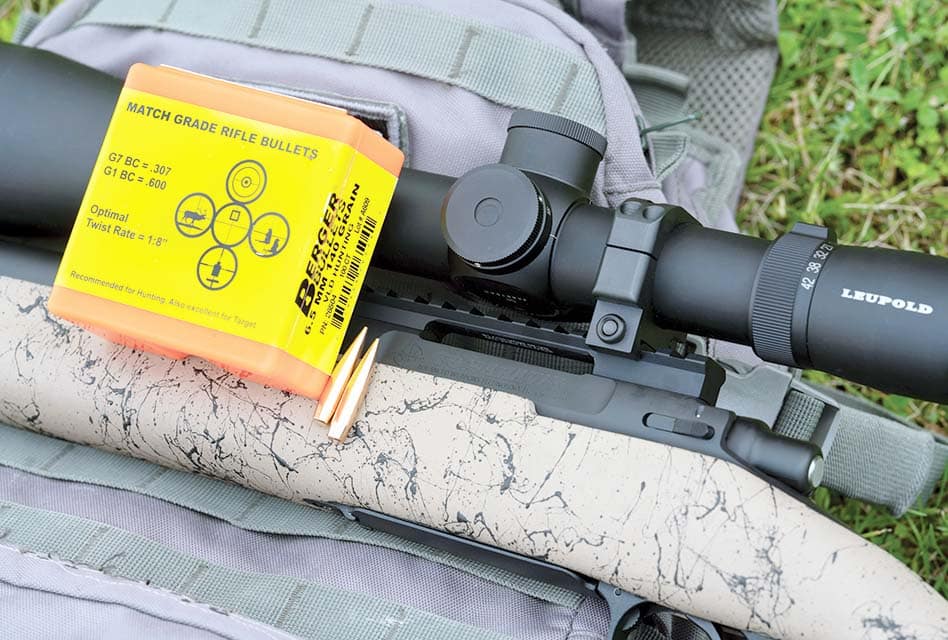
Including the probable flyer group, this gave an average group of 0.395 inch. Minus that group, the average was 0.362 inch. In this series, there were three groups tighter than the five-group bunch and two larger.
Using the Dillon 650 XL, the group sized opened up, but not nearly as much one might expect. Considering I was able to make 30 rounds in 30 minutes, I am quite happy with the trade-off. Also, with more practice, my efficiency should increase a bit for more rounds produced in that same time period.
- The best group was 0.303 inch.
- A cluster of five groups went from 0.412 inch to .0475 inch, with an average of 0.443 inch.
- The worst group was 0.869 inch and almost certainly contained a user induced flyer.
Including the possible flyer group, this gave an average group of 0.492 inch. Minus that group, the average was 0.451 inch. In this series, there were two groups tighter than the five-group bunch and three larger.
I pulled out the clustered five-shot groups and averaged them as a means of at least partially editing out shooter error/lucky groups. The clusters in both strings of shooting show an average difference of 0.063 inch. At least for this shooter, that is a worthwhile compromise for nearly triple production numbers. I would not use rounds made on the progressive for competition, but I would gladly welcome less time reloading and more time spent behind the trigger, for practice.
I would be remiss if I didnโt discuss the rifle that made all this testing possible. When another manufacturer backed out, Don Fraley of Advanced Weapons Technologies (AWT) stepped up and loaned me one of his precision rifles. Notice folks, this is NOT a benchrest rifle. It is from his precision/tactical/varmint line. Having said that, at a local or regional competition, this rifle would not be the reason you werenโt competitive. My best group with this rifle was notably worse than what Don gets using his handloads, built with H-1000 and 140-grain projectiles. His load is fine-tuned for what the rifle likes in regard to jump versus jam and provides him groups in the 0.170- to .210-inch range. He is also a better trained shooter and gets in a lot more practice time. This leads me to believe, with proper adjustment/testing for jump preference, my group sizes would decrease by roughly 0.075 inch. This would provide average groups from the single-stage in the high โ2sโ and from the Dillon in the mid โ3s.โ That is with my shooting skills, which are far from poor, but also far from world class. The rifle shoots better than I do or at least better than my abbreviated precision reloading process allowed me to show.
To Summarize
Average cluster group with single-stage loading | 0.38 in |
Less 0.075 for seating depth preference | -0.075in |
Less 0.075 for a better trigger puller | -0.075in |
0.230 in |
These are group sizes that are slightly larger but that are in line with what the gun builder and his shooting classes have obtained with this rifle.
Remove the same handicaps from the Dillon 650 XL reloader, and the average group size is 0.293 inch. There are many in the elite benchrest world who would be horrified by groups that large. For the rest of us, those are impressive (theoretical) groups. I would suggest that even the actual groups are pretty damn good.
The Details
- Primer โ Standard CCI small rifle primers
- Brass โ Lapua, small
- Primer โ 6.5 Creedmoor
- Powder โ Hodgdon 4831SC
- Bullet โ Hornady 147gr ELD Match
- Scope โ Leupold VX-6 7-42ร56
- Rings โ Ken Farrel 34mm rings
- COAL โ Author only tested at 2.800 inch; no jump or jam preference determined
- Rifle โ 6.5 Creedmoor custom-built precision rifle by Don Fraley of Advanced Weapons Technology; 26-inch Wilson Select Match barrel with a Precision/Target contour and an 11ยฐ target crown; custom AWT short action chambered in 6.5 Creedmoor; M16-style extractor; HS Precision tactical stock; Timney 510 B Elite trigger; and an AWT custom bolt knob.
Normal Dillon Steps | Precision Steps |
---|---|
Resize โ decap | Neck size โ decap |
Prime-automated powder drop | Prime-manual powder weigh |
Powder check | Powder check |
Bullet seat | Long bullet seat |
Crimp | Final COAL bullet seat |
was noticeable.
This article first appeared in Small Arms Review V24N4 (April 2020) |