By Michael Heidler
The successful use of the silenced Sten Mk II S for the British Special Operations Executive (SOE) also aroused the U.S. Ordnance Department‘s interest in a suppressor for SMGs. Founded in June 1942, the Office of Strategic Services (OSS) could use such a weapon for it’s own special operations and to support resistance groups in Europe and the Pacific Theatre. The M3 seemed to be well suited for that purpose.
Standard.45 ACP rounds fired from short barreled submachine guns are inherently subsonic, it is one of the most powerful pistol calibers available for use in suppressed weapons. Suppressors reduce the audible report by slowing down and channelling the high speed gas generated by the burning and expanding gunpowder before it exits the muzzle. Suppressors cannot act on the supersonic shock wave continuously generated by a bullet exceeding the 1,084 ft/s (332 m/s) speed of sound at 32 °F (0 °C) ambient temperatures. This shock wave is continuously produced throughout the entire flight path over which the bullet is supersonic, which extends long after it exits the barrel. One major disadvantage of automatic and weapons, however, remains: the unavoidable noise of the moving internal parts when the spent case gets extracted and the next round gets automatically loaded. So a weapon with suppressor is not completely silent, but it lacks the typical hard “bang“ and for the enemy it is more difficult to locate the direction of the sound’s source.
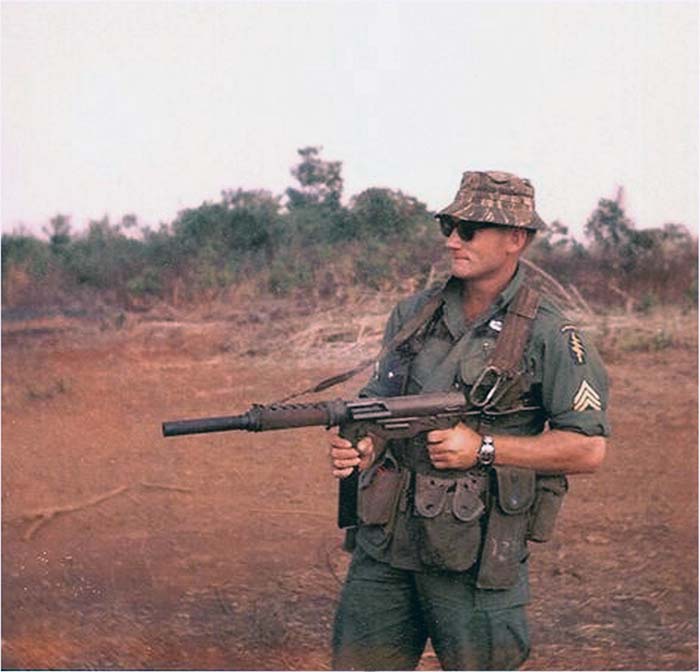
The first trials with suppressed M3 submachine guns were already being held in 1942 at Fort Benning (Georgia). These devices were based on the designs of Hiram Percy Maxim, with curved vanes of thin sheet metal, but were not convincing. The design was heavy, the gun became extremely top-heavy and the suppressor heated up quickly during continuous fire. Two different models were tested, a long one with 20 inch barrel and a shorter one with 12 inch barrel. Because of the unsatisfactory results, the tests were discontinued.
In 1943, the Ordnance Department contacted the company Bell Laboratories on behalf of the OSS concerning the development of a suppressor for the M3. The production of the suppressor parts and the assembly should take place at the High Standard Manufacturing Company in Hamden (Connecticut). The production of special barrels and modified barrel nuts (collars) was assigned to Guide Lamp. The first order was for 1,000 devices. Whether and in what quantity follow-up orders have been placed is not known. One of the big advantages of this suppressor design was that the standard M3 barrel could be removed and the suppressed barrel could be quickly screwed on in its place.
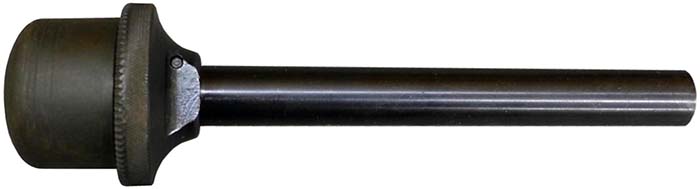
The outer form of the special barrels of Guide Lamp did not differ from the standard serial barrels. However, a total of 48 holes were drilled into the barrel (in four rows of 12 holes) to allow gases to escape as the bullet was fired. Each hole had a diameter of .25 inches. The muzzle was threaded at a length of about .5 inches. The barrel nuts were taken from the serial production and have been modified at the front to serve as a support for the rear end of the suppressor.
The suppressor itself is comprised of two sleeves. The rear sleeve (barrel covering) of 7.5 inches length and 1.5 inches in diameter forms the expansion chamber and is filled with a stainless steel wire mesh cylinder, which is fitted over the barrel.
The threaded muzzle part of the barrel protrudes from the expansion chamber. The actual suppressor housing (barrel extension) is attached to the barrel covering by a connecting piece (barrel extension retainer) that is screwed onto the muzzle thread of the barrel, thus locking the covering in place against the modified barrel nut. The extension of 7 inches length and 1.13 inches in diameter contains 230 perforated discs of stainless steel wire mesh. The front end of the extension is closed by a screwed-in end plate.
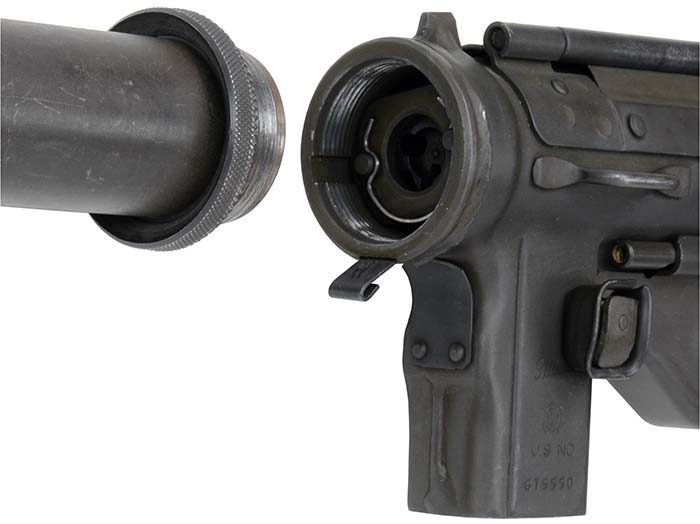
When the projectile travels down the bore some of the propellant gases escape through the 48 holes in the barrel into the expansion chamber, where they are slowed down and cooled by the steel wire mesh. When passing through the connecting piece, the projectile leaves the barrel and moves through the perforated steel wire mesh discs in the barrel extension. Here the remaining gases are trapped for a short time and cooled down and then escape into the surrounding air.
The influence of the suppressor on the noise is described in a test report from Aberdeen Proving Ground as follows: “While the silenced barrel does not completely eliminate the sound, the reduction of the report makes it difficult to determine the exact location of the weapon when being fired at a distance of 50 yards or greater. The sound heard by the individual varied with his position with respect to the weapon. When the individual was in the line of fire or forward of the gun muzzle a louder sound was heard than when positioned at the rear of the gun. When positioned at the side or at the rear of the gun the noise caused by the operation of the mechanism was most noticeable.”
The use of the suppressor, however, deteriorated the impact of the projectile on the target. Tests showed that an M1 steel helmet will not be penetrated at a distance of 75 feet. Using a standard barrel without the device, it was no problem to perforate the helmet even at greater distances. Also it was found out that the projectiles sometimes strike the edge of the central opening in the front end plate of the barrel extension, thus damaging it. Pieces of the bullet jacket were lodging in the sleeve behind the plate. In some cases the end plate was shot out of the sleeve and the installed wire discs fell out. This problem was caused by the not absolutely rigid connection of the two sleeves. The connecting piece is screwed only onto the muzzle thread and so the alignment of the barrel extension with the bore of the barrel is difficult because the suppressor is too flexible. The connection does not withstand the leverage effect of the long protruding extension. A slight enlargement of the opening in the plate to a 0.550 inches diameter solved the problem.
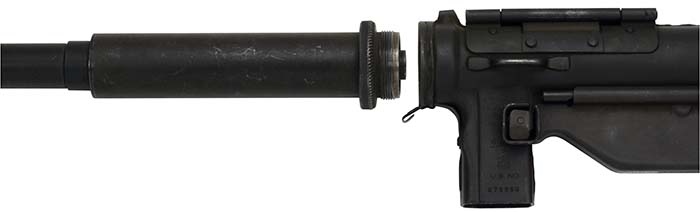
The care and maintenance of the suppressor proves somewhat complicated. In particular, the perforated steel wire mesh discs are difficult to accommodate in the barrel extension. If they slip in the housing or get deformed, the way of the projectile is not free and it can hit and damage the discs (thus reducing the suppressing effect). As already mentioned, the barrel extension could easily deviate from the exact alignment with the barrel – especially during transport. For this reason, a special tool has been issued with each suppressor: An “aligning rod” should be installed inside the suppressor during transport or shipment as a stabilizer. It reaches from the cartridge chamber of the barrel to the front end plate of the barrel extension and should prevent bending of the two sleeves. By means of a detachable handle, this stabilizer could also be used as a cleaning rod. Every suppressor was also issued with a special “barrel cross-hole brush” for cleaning the 48 small laterally holes and a sheet metal “barrel thread protector” to be screwed on the thread of either the suppressor or barrel nut (depending on which part was in use). Two versions of the protector cap were made. The early one with a smooth back was often hard to remove, so the design was changed and the later ones got a square pressed-in recess for applying a tool.
According to the reports, the use of the suppressor improved the accuracy when firing automatically. This fact is probably due to the increase in barrel weight and dimensions and to the lower velocity, causing lower recoil energy. Another positive effect is the elimination of the muzzle flash. No flash was observed when firing the suppressed weapon at night.
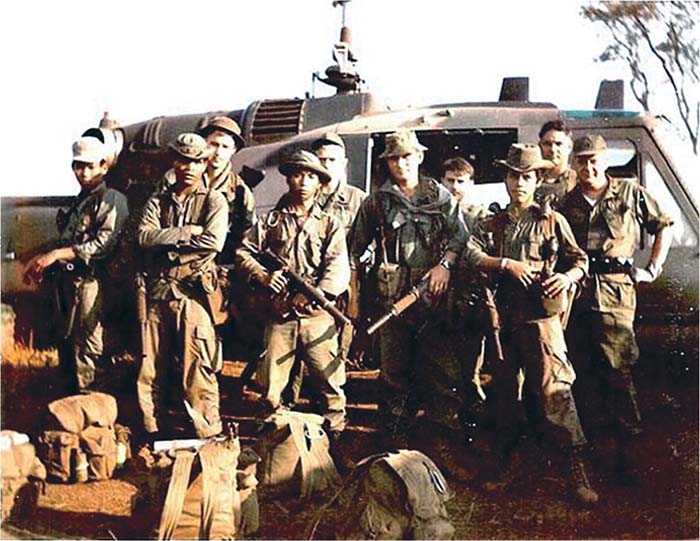
The M3 and M3A1 without suppressor are indeed relatively accurate submachine guns. But they are no sniper weapons. Although the suppressor improved the accuracy it was almost impossible to get a precise, targeted hit with a single shot – which of course would have been optimal for a silenced weapon. The demand for development of a special suppressed submachine gun with high accuracy was often mentioned in the test reports but went unheard. Despite all efforts, the Bell suppressor was only about 80% as effective as the British counterpart of the Sten Mk II S. This fact has been determined in a shooting competition in Aberdeen. Nevertheless, the suppressor remained unchanged and was successfully used in Korea, Vietnam and other conflicts.
The highly decorated Vietnam veteran Jim Bolen for example used a suppressed M3 in his time with the Special Forces. He later wrote down his experiences in his recommendable book “No Guts, No Glory”. As a leader of a reconnaissance unit he survived more than 40 top-secret MACV-SOG missions (Military Assistance Command Vietnam – Studies & Observation Group), which among others took him to Laos and Cambodia. He remembers the suppressed M3 very well:
“Normally one member of the recon team carried the M3 with an integral silencer. It was a 45 caliber and was used as a RON (remain over night) gun in case at night an enemy, civilian or even animal would accidentally happen on us we could kill same without giving away our position or even the fact we were in the area and also for prisoner snatches to get in and out without being compromised. The weapon was reliable but with the amount of ammo needed for a mission it was very heavy. My gear weighed between 95 and 110 pounds depending on the mission. Weight was always a big problem on our missions, which was the reason we generally didn’t carry large weapons such as the M-60, large amounts of claymores or hand grenades, on standard missions. When using the M3 on a prisoner snatch mission the weapon is usually broken down and divided between all team members to distribute the weight then assembled when needed.
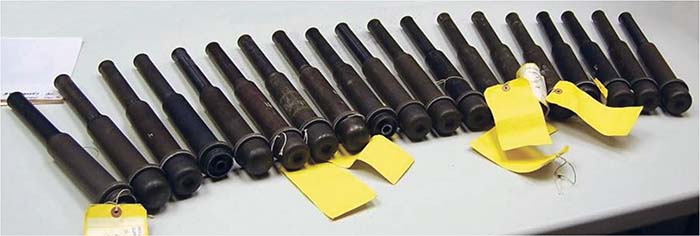
The M3 had one disadvantage in combat, yes. More than one occasion when carrying the silenced M3 I would be confronted by NVA. Normally I would have the advantage by opening up first on full auto using my CAR-15 with every round being a tracer. This would scare the hell out of the enemy. But when I am carrying a silenced weapon and I open up on them they don’t realize I am shooting at them and start returning fire ASAP. This is the truth and I will testify to it.
Incidentally the High Standard Manufacturing Company also made a suppressed version of its small-caliber pistol “H-D” (.22) for the OSS at the same time. The design of the suppressor came from Bell Laboratories and was very similar to that of the M3 with its two chambers and the stainless steel wire mesh parts. The gun was based on the suggestion of Deputy Directors for Research and Development Stanley P. Lovell. From October 1943 until March 1944 2,600 pieces with the designation “MS” (Military Silent) have been delivered.
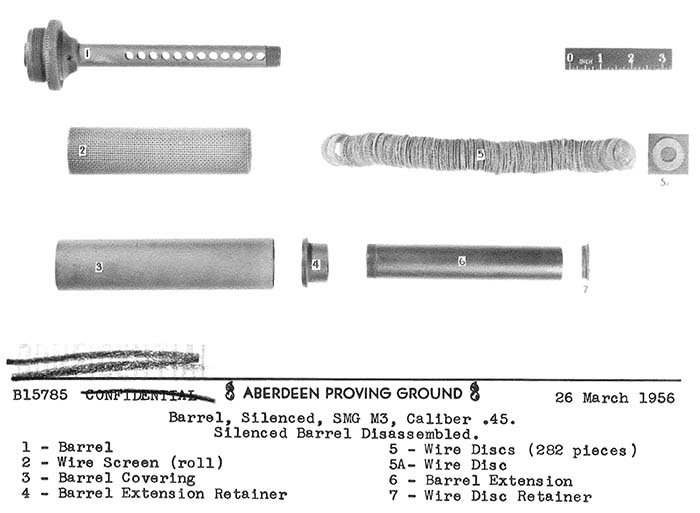
While fighting in Vietnam a lot of foreign weapons fell in the hands of the Americans – including numerous Grease Guns that were made in China. Some of them were equipped with suppressors. However, since the OSS suppressors were not marked, it remains unclear whether these suppressor were originally made in the U.S. or in Chinese workshops. An interesting finding is that the wire mash cylinder in the expansion chamber was often replaced by an oil-soaked felt in many of these suppressors.
Me and my team practiced a lot on the firing range with what ever weapon we were required to carry on a specific mission. Do this we would take the silencer apart and clean the original screens with a wire brush and cleaning compound, once they become clogged it reduces the silencing capability. Never noticed any round being quieter than another. I know when we use the .223 round with a silencer we have to use the first 3 rounds sub-sonic because of the crack sound of the high velocity .223 round.”
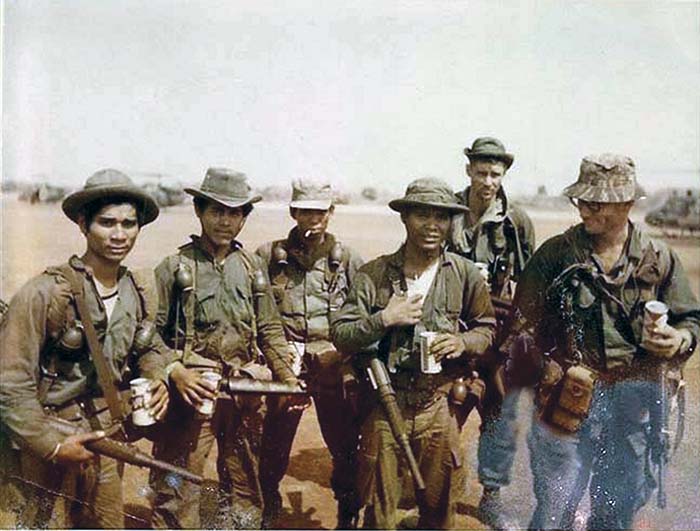
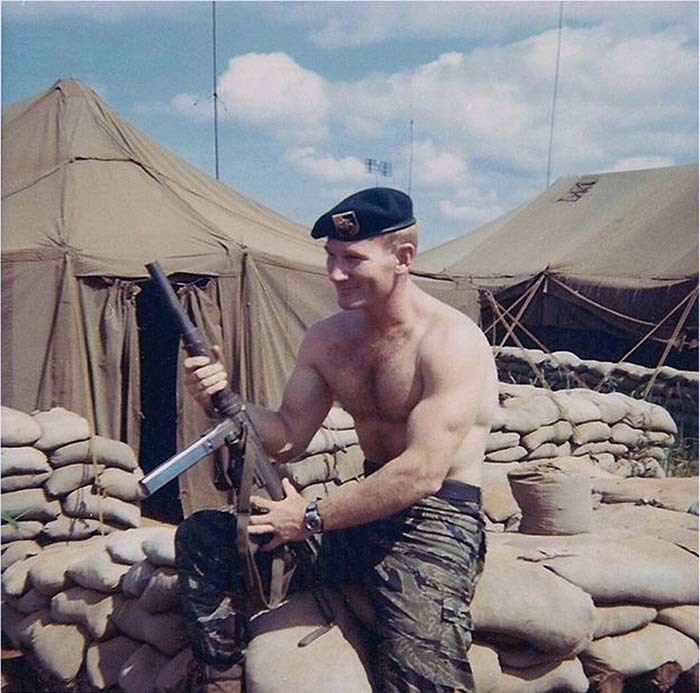
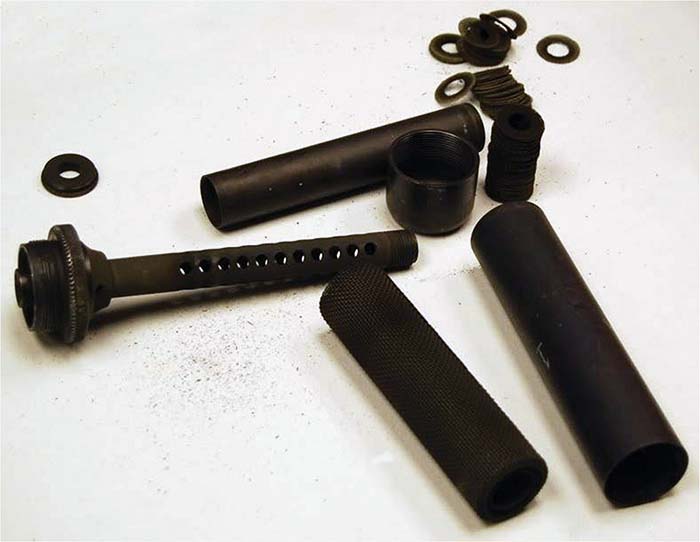
This article first appeared in Small Arms Review V20N10 (December 2016) |