By Louis T. Carabillo, Jr.
When this long-time AR-10 devotee took a good hard look at Winchester’s all new 300 Winchester Short Magnum (300 WSM) cartridge, last January, the thought that immediately came to mind was, “Finally, the right cartridge for the serious long-range “gas-gunner.” Indeed, from an AR-10er’s perspective, if a team of engineers had been commissioned to design a cartridge specifically for a proposed “Maximum Output AR-10”, and came up with the 300 WSM, all requirements would be met. It’s that good. To say that my interest was piqued would be a gross understatement.
You’re probably one of the many thousands of shooters who now own one of the variations on an original theme by one of America’s foremost firearms designers, the late Eugene Morrison Stoner, and available today under a variety of nomenclatures: SR-25, AR-10, ASA .308, HAR25, etc. Any of these quite robust hybrids (a cross between the original .308 AR-10 and later .223 AR-15 designs) offers today’s big-bore shooter a good value. Your question, “Why would you want to change a perfectly good-shooting AR-10”? My answer, “Maximum Output”, of course. You can take a look at the old .308 Winchester and the new 300 WSM Cartridges, along with their respective interior and exterior ballistics in the charts on page 41.
OK, so the new 300 WSM looks good on paper, but does it deliver? In this author’s opinion, most magnums don’t. In the average production hunting rifle, even with the longer 26” barrel, the 300 Weatherby Magnum actually delivers about 3100 fps MV with a 180-grain bullet; the 300 Remington Ultra Mag, about 3150 fps, and due to their 100-plus grain case capacity, both recoil and muzzle blast are excessive.
Therefore, I was pleasantly surprised to note that the two 300 WSM factory loadings tested during the course of developing the conversion actually delivered, as advertised (using the ASA 24” match barrel): the 150-grain “Ballistic Silvertip” averaged 3,300 fps; the 180-grain “Power Point” averaged 3,075 fps, exceeding the advertised figure for that loading by more than 100 fps, and from a gas-ported barrel. I was impressed.
It’s clear that this short, fat design has great potential. Accuracy seems to be enhanced as well (something the benchrest crowd discovered years ago). Both factory loadings averaged about 3/4” groups, at 100 yards, using the Harris bipod. With a case capacity of about 80 grains (water), neither recoil nor muzzle blast were the least bit objectionable. The superb 190-grain Sierra HPBT MatchKing bullet with a Ballistic Coefficient of .533 would be an excellent choice for 600-plus yards shooting. Extrapolating from the above-delivered velocities, I would expect that a muzzle velocity of 2,975 – 2,985 fps should be easily obtained with the 24” 300 WSM-chambered barrel.
In view of the 300 WSM’s impressive performance and the popularity of today’s “AR-10’s”, I wouldn’t be surprised if one or more companies offered this exciting combo in the near future. It must be said at this time that patience has never been one of the author’s attributes. Therefore, waiting for something which promised this much excitement to “happen” just wasn’t an option; converting an American Spirit Arms Corp ASA .308 Match Rifle to work properly (autoload) with the new 300 WSM cartridge, right now, clearly was.
Prime candidates for this conversion are any of today’s “AR-10’s” with their robust flat-top upper receivers, and stiff 24” barrels. Though each offers their own individual character and strengths, many of the components are quite similar, if not identical. In short: much of the proven formula for the ASA .308 – 300 WSM successful conversion will work for the others.
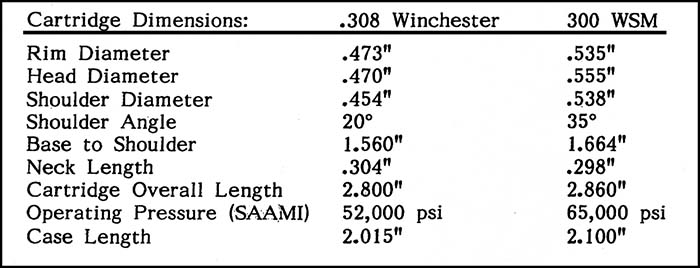
Upon close examination of the comparative dimensional and operational figures of these cartridges, it becomes clear that enlisting the services of a competent gunsmith would be a prudent measure. First, his expertise is invaluable in determining whether or not the design of any particular rifle has the necessary margin of safety built in. Second, he can offer the high degree of precision work required on this conversion: rechambering; opening up the bolt face; reworking the extractor; other machining, as may be necessary.
When one checks the interior length of an “AR-10” magazine (modified M14-type, as equipped, used in this conversion), we discover that there’s barely .005” left when using the maximum Cartridge Overall Length established for the new cartridge. Indeed, the 300 WSM is the practical limit for this design. As would be expected, the short, fat case limits magazine capacity: the typical 20-round (.308) mag will accept about 12 300 WSM “Maximum Output” rounds.
Less obvious is the new demand placed on the extractor and spring-loaded ejector. The new 300 WSM fired case is more than 4% longer, 18% wider and 33% heavier (239 grains v. 179 grains) than that of the .308 Winchester. Due to the much wider rim diameter, the ejector face is .031” farther from the edge of the 300 WSM rim than the .308 Win. resulting in less mechanical advantage. Mechanical advantage is reduced further due to the fact that the 300 WSM fired case has used up .0425” of its arc swing from centerline, prior to exiting the much fatter chamber.
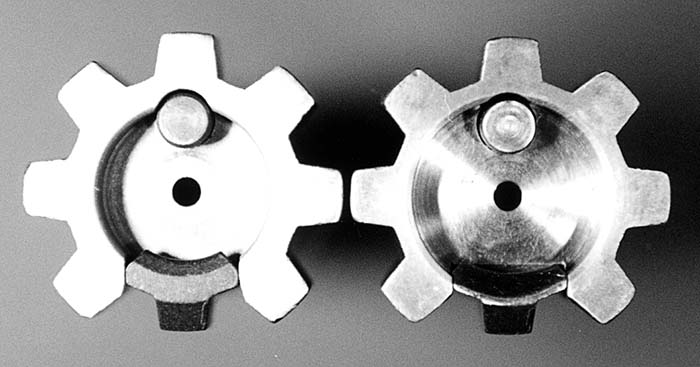
Finally, the significant increase in operating pressure of the new cartridge must be addressed. Delay its delivery; reduce its volume: the options. I prefer the former, and as no device to accomplish this was available for this specific application, elected to fabricate one — which worked well. For comparison purposes, I also experimented with adjusting the volume of high-pressure gas directed to the action.
I got the project rolling by contracting Accuracy Systems, Inc., a local gunsmithing shop. Gunsmith, Carl Emmite, executed the necessary rechambering (standard SAAMI 300 WSM chamber) and bolt face reworking (opened up to .535”). The cost of this service was $100.
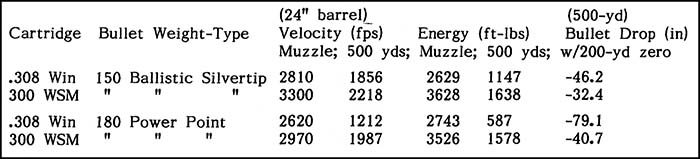
In the meantime, I fabricated a coiled gas tube (which my wife, Pam, calls “The Sidewinder”) using a 30”-long piece of 3/16” (actual diameter: .185”) hydraulic tubing (purchased as a straight piece at a local automotive parts store, $2.29). The standard ASA .308 Match Rifle tube (actual diameter: .180”) is about 15” long. I took note that the inside diameter of the standard tube is approx. .125”; that of the hydraulic tubing approx .135”. The challenge: maintain the 30” length of the hydraulic tubing, which allowing it to be used in the same overall length occupied by the much shorter standard-length tube. I accomplished this by using a 15”-long section if 1” ID PVC plastic tubing (purchased at a local home improvement store, 49 cents), which has an outside diameter of approx. 1.300”, as the mandrel, along with a 12” length of tightly coiled (ID: approx. .200”) chrome-plated spring (purchased at a local hardware store, $5.49). With the hydraulic tubing inserted in the chrome-plated spring (to prevent kinking of the hydraulic tubing), I then coiled the two around the mandrel (slipping the spring forward, as the work progressed), leaving short straight sections on both ends of the tube. I then dressed both ends to the .180” outside diameter required to fit the gas block and the gas tube coupler on the carrier. This procedure resulted in a free-floating spiral gas tube which effectively delayed delivery of high-pressure gas, until the fired case had relaxed, allowing case rim-friendly extraction. The difference was profound: the standard 15” gas tube produced fired cases with rims that were severely deformed by the extractor; the 30” “Sidewinder” produced fired cases with rims showing no deformity.
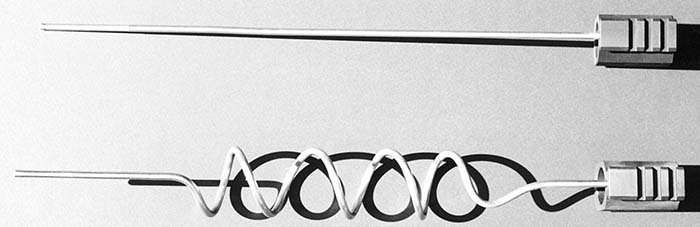
During the course of developing a working formula for a successful conversion, Pam, armed with the family camcorder, often accompanied me to my test facility out on the high Colorado prairie (formerly an Air Force bombing range). She set up the equipment to closely monitor the ASA .308 action cycling during my initial test firing of 300 WSM cartridges. Upon our return home, we played the tape on a JVC HR-S9800U VCR, with “Time Scan”. In this way, we were able to study the action, frame by frame, 33 frames per second. We found that when using the standard 15” (unregulated) gas tube, the complete cycling of the action averaged just two frames duration. When replaced with the 30” “Sidewinder”, complete cycling of the action averaged four frames duration. In the interests of maintaining reasonable reliability of reciprocating parts, as well as reasonable case life, the use of the standard 25” gas tube in this application, unregulated, was discontinued (the option of using a regulated 25” gas delivery system is discussed later on in the report).
The AR-10 extractor is well-designed to do its important job, under highly-stressful conditions. Three separate surfaces must be precision machined in order for this conversion to be successful. It should be noted that the spring-loaded extractor accomplishes its function within the tight confines of the barrel extension. Sufficient metal must be removed from its “three faces” in order for the action to even close. Remove the extractor from your “AR-10” bolt-carrier assembly, and let’s take a close look at it.
The “lug” on the back side of the extractor is, in fact, a strengthening rib, and is so shaped to fit between two locking buttresses in the barrel extension. It’s important not to remove any metal from the back side of the extractor. Now, let’s examine the “three faces” of the extractor. We’ll refer to the beveled tip as “A”: it’s the point at which the case rim first makes contact “B” is the extractor claw tip, the face of which fits the radius of the extractor cut on the .308 Winchester case. “C” is the square-edged cut which accepts the rim of the .308 case.
Following some trial and error with Dremel-type tools to first determine the precise amount of metal to be removed, I contracted Gunworks of Colorado, Inc. for this phase of work, as they were set up to do the precision machining required on the extractor. Gunsmith, Bart Miller, performed the task per my specifications:
•1- Remove approx. .030” from the beveled tip, “A”, slightly more at the top, to allow the much wider 300 WSM rim base to contact this sloping leading edge;
•2- Remove .030” from the extractor claw face, “B,” leaving a proper radius for the wider .480” diameter 300 WSM extractor cut, while maintaining a claw face of approx. .020” high;
•3- Deepen cut “C” .025” without removing any metal from its roof, maintaining the sharp-edged corners at the rear, and leaving a proper radius for the wider .535” diameter 300 WSM case rim. NOTE: .025” and .030” are from the centerline of the extractor face. The cost of this service was $35.
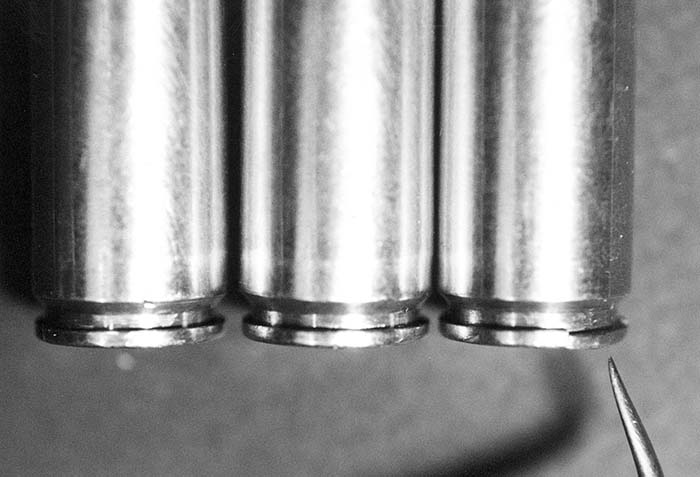
Mr. Miller executed the work exactly as requested. As a result, the extractor performed its task, consistently, and without interference by the barrel extension buttresses. With a secure grip on the case rim, and working in concert with the ejector, it now insisted on ejecting fired cases in a direct line opposite the ejector, and with no deviation from that line. That was OK with the much narrower .308 Winchester case, but, more often than not, resulted in a less than graceful exit for “the fat lady.” The problem was corrected by removing .040” from the upper lip of the ejection port. I contracted Accuracy Systems, Inc. for the precise execution of this procedure. The end mill must be introduced at an angle of 90 degrees from the top face of the lip to prevent cutting into the carrier raceway on the interior of the upper receiver. The cost of this service was $20. If I later choose to use the ejection port cover, I’ll rework the spring-loaded plunger to extend further, and cut a detent slot for it in the top of the ejection port opening.
In order to give back a bit of mechanical advantage to the ejector, I added just enough spacer in the ejector-ejector spring bore to allow the combination to be flush with the bolt face when compressed. In addition, I stoned the sharp corners of the two guiding barrel extension buttresses to prevent any degree of deceleration upon exit. This attention to detail, combined with the other modifications outlined above, results in the reliable ejection of fired 300 WSM cases, if not to the great distance experienced with the original .308 Winchester chambering.
Having discontinued the use of the standard 15” gas tube due to the resultant violent cycling of the action, and extreme deformation of the fired-case rim by the extractor, it was rewarding to discover that substituting with my 30” long “Sidewinder” gas tube corrected both problems, while maintaining reliable autoloading. It occurred to me that by restricting the volume of high-pressure gas directed to the standard 15” gas tube, a proper balance might be reached that could parallel the good results obtained with the “Sidewinder”. This prompted some experimenting eventually leading to more revelations and new rewards.
Keeping in mind that the diameter of the gas port in the ASA .308 Match Rifle barrel is .0935”, and that the connecting hole in the gas block (to the gas tube) is .135”, by relocating the gas block (held in place by three set screws), forward, from the point of the barrel stop (causing misalignment of the holes), one effectively restricts the volume of gas to the gas tube. I discovered that locating the gas block forward approximately .045” resulted in reliable functioning, but with only slightly less deformation of the fired-case rim that the extreme degree observed when the gas block butted against the barrel stop; approximately .065” resulted in reliable functioning, and with no apparent deformation of the fired-case rim; approximately .075” resulted in reliable ejection, but failed to autoload (no apparent deformation of the fired-case rim); approximately .090” resulted in sporadic ejection, and failed to autoload (no apparent deformation of the fire-case rim).
If the concept of a “Maximum Output AR-10” piques your interest, contact he manufacturer of your favorite twenty-first century “AR-10”. They’ll thank you for your call/letter. Be sure to mention that you read all about it in the Small Arms Review.
WARNING: This report is but a brief summary of the authors conversion to a chambering not yet authorized by the manufacturer of the firearm used. It is not intended to be a do-it-yourself guide, but a less than definitive informational source on such a conversion, making no representation re its safety. The author and publisher disclaim all liability for any damages or injuries occurring as the result of persons using this information.
Sources:
American Spirit Arms, Corp.
15001 North Hayden Road, Suite 112
Scottsdale, AZ 85260
(888) 486-5487
Accuracy Systems, Inc.
1653 South Laredo Street
Aurora, CO 80017
(303) 755-3530
Gunworks of Colorado, Inc.
3355 South Yarrow
Lakewood, CO 80227
(303) 986-9412
This article first appeared in Small Arms Review V5N5 (February 2002) |