M60GPMG as manufactured by J. R. Stemple.
By Thomas T. Hoel, historical and technical editing by Dan Shea, Photos by Dan Shea
There always seems to be a certain few military firearms that bear an unusual and universal interest for collectors and students of military weaponry. The US M60 General Purpose Machinegun has always occupied just such a position within the civilian NFA weapons owning population. Although there also seems to be little ability to compromise on feelings toward the design, as it is either highly praised or deeply maligned. While in the past literally volumes have been written on the military adoption and use of this interesting weapon, the scope of this discussion is strictly to aid the civilian owner-operator of the M60 GPMG as a guide in obtaining maximum enjoyment, usefulness, and longevity of his personally owned machinegun.
Additionally, specific recommendations discussed herein for operations strictly in the civilian realm will be presented as the civilian owner-operator has certain freedoms, and also certain limitations, that the original military end-users may not. The M60 has a number of well-known characteristic wear and failure profiles for certain component parts and assemblies. Anything the civilian owner-operator can do to decrease operating stresses, and attendant wear and tear on component parts or assemblies, will serve to prevent unnecessary or premature wear and failure of these parts, adding tremendously to the life expectancy, serviceability, and enjoyment of the weapon as a whole. This should be the primary concern with such the large investment these privately owned machineguns represent.
While certain distinct characteristics of the M60 design may not at all pose a serious or dangerous matter for the civilian owner in a recreational shooting environment if or when they result in a failure to function, they bear discussion to further the serviceability and enjoyment of personally owned examples. This discussion is divided into two distinct sections. The first, discusses in detail the receiver, its sub-components and construction, along with recommended practices for the care and preservation of the receiver as an assembly. The second part will discuss the various and sundry peripheral assemblies that complete the weapon, with the same emphasis in the discussion provided as appropriate.
Many of the long established military use and service protocols exist for reasons specific to the military/combat environment, or specific governmental exigencies. These include repair or service protocols where the actual military end-user is not to be concerned with the costs of repair, even if the supply of spare parts was unlimited. Since the civilian owner-operator is not bound by such exigencies, he should exploit any and all maintenance and operating schemes that benefit preserving of the serviceability of the weapon over an extended period of time and use, along with minimizing actual financial outlays for avoidable repairs parts or services. As such, certain of these recommendations are intended for use only in the civilian realm, and do not represent advice or recommendations for operational use, or maintenance functionality, of the weapon in any military or law enforcement scenarios.

The Heart of the Matter
Those M60 machineguns that are available to the civilian collector of NFA weapons can be described as being of two basic origins. The first important distinction, and the one which relates most strongly to their value as collectibles only, concerns the manufacturing origins.
The top rung on the collectability ladder is those guns that were originally manufactured by a genuine military contract producer. Although their numbers are quite small there are, remarkably, a certain number of M60’s that are of true military production-line origin and pedigree. Due to these contract producers being private companies, they were able to offer the exact same weapons they were producing under military contracts additionally to both domestic law enforcement entities, or for export to approved Friendly Nations clients. Not all guns originally destined for either of those last two markets ended up there, mainly due to some quirks in salesmanship domestically, and thus a few of those guns have been able to enter the civilian market and placed into the NFRTR. The salient feature of these specific guns is that they can all be described as being manufactured and assembled to full military specification, in both materials and workmanship, in all component parts and assemblies. While this distinction often has no bearing on serviceability for sport shooting purposes, it can have a definite in their value. The second group of guns is that in which the receiver was manufactured by any method, by anyone, other than the original military contract producers. This is the most critical distinction in the pedigree (and value) of civilian available M60 guns, and bears careful discussion.

Receiver Basics
The “receiver” of the M60 machinegun on all of its several variant models is actually an assembly of several component parts, permanently or semi-permanently joined to render the complete functional assembly. BATF Technology Branch has recently authored a reply to an inquiry letter asking for a definition of what legally constitutes an M60 machinegun “receiver.” By rendering this recent official opinion they introduced considerable confusion into what was previously the legal definition under previous Technology Branch Administrations. The “current” (as of 11/2001) BATF Technology Branch definition of a “M60 machinegun receiver” is: “…the frame or receiver of the M60 machinegun consists of a bottom plate(sic), two side plates(sic), the bridge, and a trunnion. The top cover, while attaching to the receiver, is not considered a part of the receiver.”
This definition is significant as it fails to consider two of the most structurally important receiver component pieces, namely the receiver’s sheet metal channel and the gas tube. Both parts are structural members that are permanently joined to form the receiver structure, and in the case of the sheet metal channel, to which the above mentioned five component parts must be joined together.
The “receiver” of the M60 machinegun has traditionally been defined to be made up from eight permanently assembled individual component parts, as follows:
- Barrel trunnion
- Gas tube (or Operating Rod tube)
- Stamped sheet-metal “lower receiver channel”
- Left and right side, milled, bolt bearing/guide rails
- Lower, milled, operating rod guide channel (similar to the bolt guide rails)
- Stamped rear receiver “ridge” (top cover latch)
- Mounting plate, T&E mechanism adapter.
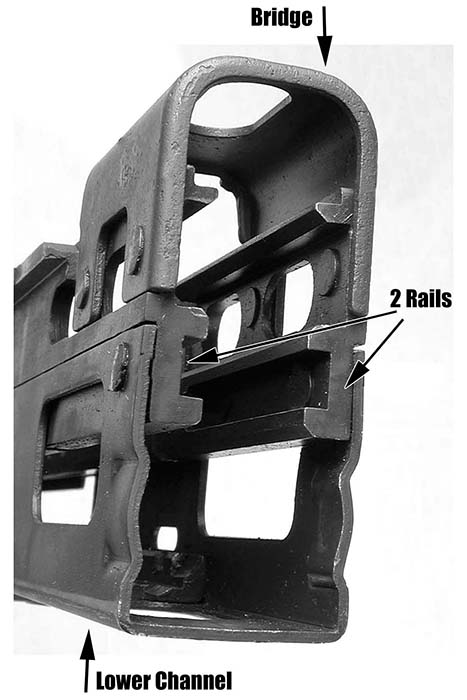
(There may be one possible additional component part not counted above. Some very early military trunnions utilized a separate, riveted-in, cartridge feed ramp. This was soon replaced in the manufacturing process by a simple machined ramp feature in the basic trunnion forging. Virtually all, new-manufacture, commercially produced trunnions have the machined in feed ramp feature.)
These above eight component parts are assembled, by either riveted and/or welded joints, into a unitized structure that cannot be disassembled to a lower individual state without destructive separation. This is a significant definition, as it relates to what BATF Technology Branch is using now to determine the legal definition of a “M60 machinegun receiver.” By electing to render this current definition, BATF Technology Branch has ostensibly recognized the true component nature of the M60 machinegun receiver, thereby presumably allowing a duly registered weapon to have any of its five legally defined component receiver parts replaced if necessary due to damage. (While it is of course prudent to get a personal reply to any proposed repair actions inquiry direct from Technology Branch, this “opinion” has been rendered verbally to others in the past) The relevant statement from the recent opinion states: “…removal of one or more of these (component) parts would not change the classification of the item as a machinegun.”
This statement, making no mention of the other two common, and structurally required, component parts, can be assumed to indicate that they do not comprise a part of a “machinegun receiver” in the current opinion of ATF and are of no consequence in its definition. However, this now introduces considerable confusion into individual guns being compliant with the markings requirements (Title 26 U.S.C., Chapter 53, section 5861(g)), as there now exists a discrepancy between their (recent) definition of the “receiver” and where certain older, Pre-5/19/1986, registered machineguns bear their legally required serial number(s), which by the recent definition, can be located on a part that is not now considered to be the “machinegun receiver, or a component part of a machinegun receiver.”
This utterly bizarre and unexplainable situation becomes highly relevant when one observes that the legally required manufacturers’ identification markings and required serial number(s) have been observed to have been applied to at least three of the major “receiver” components when examining individual commercially manufactured guns, which by the recent definition can be located on a part that is not now considered to be the “machinegun receiver, or a component part of a machinegun receiver.” The most common location to place these required markings have been the top surface of the barrel trunnion, the large flat surfaces of the sheet metal channel, or the bottom surface of the gas tube, with only the trunnion now being legally considered a component part of a machinegun receiver. (It should be noted that all of those guns that were originally manufactured by a genuine military contract producer bear their markings on the top surface of the barrel trunnion.)
In addition to these above described permanently assembled component parts, a functional M60 receiver is usually considered to also comprise the following semi-permanently installed components or assemblies, (Though these additional parts are required for a functional weapon, they do not comprise the legally defined receiver.):
- Rear sight assembly (any variant model specific assembly)
- Carrying handle assembly (M60 and M60D only)
- Tripod pintle retaining latch pin
- Cocking handle assembly (cocking handle and cover plate)
- Barrel retaining latch mechanism
It is important to understand that in the sense that though the “receiver” of the commercially produced M60 machinegun may bear markings of a Class 2 Manufacturer, only a select few parts are not original military contract origin parts. Usually in most cases, the only component part(s) known to be actually made by these civilian concerns was the barrel trunnion itself, though in some cases additionally the sheet metal channel, and/or the bolt and operating guide rail sections were of new, commercial fabrication. The remaining component parts or assemblies used to complete the weapon were simply military contract spares, commonly available on the surplus market. This was a simple necessity from practical reasons as since the barrel trunnion was the most massive and sturdiest component in the receiver design, its failure or damage in service was not seen as a common occurance, hence a supply of ex-military origin spare-part trunnions was virtually non-existent. Unlike most other common spares or replacement parts of the gun, barrel trunnions as spares simply never really reached the surplus markets, so they had to be fabricated on the civilian side. The other reason is that even in the military environment, the barrel trunnion was considered to be the (tightly) controlled part of the weapon (“the receiver”) as it bore the manufacturers markings and serial number. The remainder of the receiver components could generally be obtained, so that from that point on the “manufacture of a civilian M60 was nothing more than proper assembly of the component parts and assemblies needed to render whatever version of the gun you were trying to build. In general terms then, the civilian M60 machinegun is built up from all MIL-SPEC parts and assemblies, with the exception of certain receiver parts. How this was accomplished was not always the same, either from a mechanical standpoint, aesthetic, or “quality” perspective.
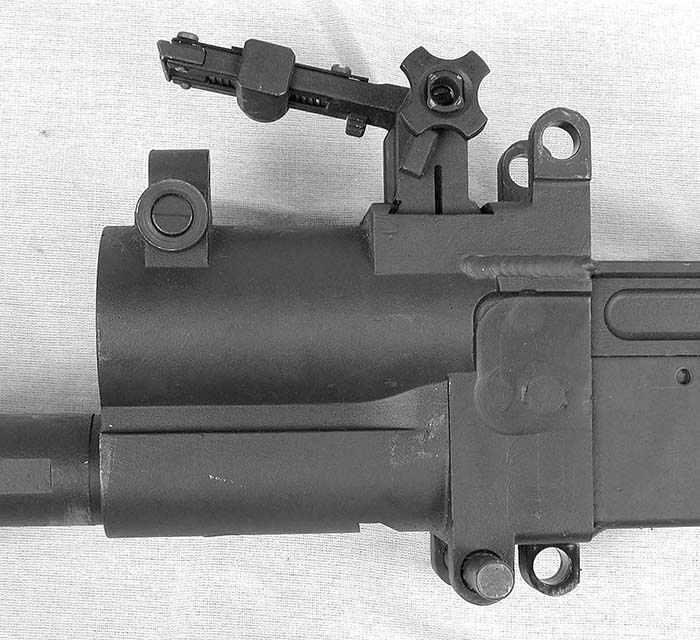
Trunnion Variations
Excluding the few guns that came from the true military contract producers, the manufacture of the barrel trunnion is where the greatest difference in civilian M60’s comes into play. The original MIL-SPEC calls for the trunnion to be manufactured from an ordnance steel hammered-pressure forging, machined to final dimensions and tolerances. This is ideal if the economics of a Governmental contract with a large manufacturing concern allow for it, but for the civilian market, such expenses for what was always a extremely limited production item, were simply impossible. Fortunately though, the design of the M60 places no direct firing stresses on the trunnion itself, as the rotating bolt locking into the barrel extension contains these; and these two component parts are MIL-SPEC items in every commercial M60 known.
Due to this fortunate circumstance alternate methods of manufacture for the trunnion were conceivable, and fully within the limits of complete safety. As the M60 barrel trunnion only receives indirect stresses of firing, and since all other highly stressed component parts are MIL-SPEC items, the civilian trunnions could be manufactured by more cost efficient methods. And no matter how the basic trunnion blank was fabricated, all M60 trunnions required machining to final dimensions and tolerances.
All forms of manufacture for the trunnion blanks, be they forgings, castings, or fully machined, require slightly differing methods of arriving at the actual blank form shape as each method must be designed to accommodate the intended metallurgical profile employed. In other words, a blank sized and shaped to be formed from a pressure forging will not be directly the same as one intended to be cast, as the different metallurgies require that different physical areas of the trunnion be formed correctly for the method used. This results in slightly differing exterior shapes and sizes of otherwise “identical” parts that have been manufactured by different methods.
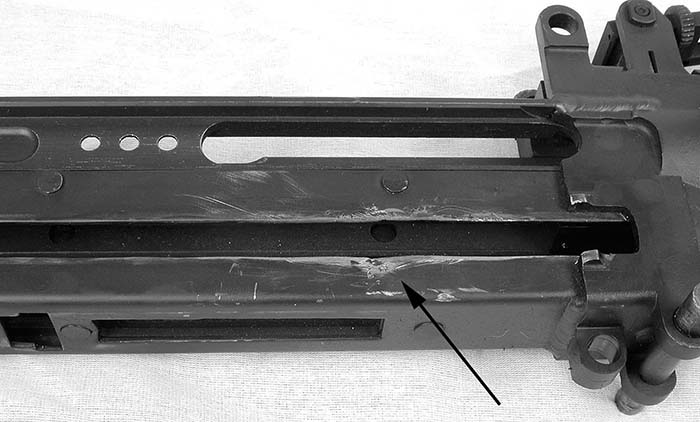
The most commonly employed method for the manufacture of civilian M60 trunnions was by investment casting the receiver blank form, though machining from full barstock or billet was also done. It may be argued that, in theoretical terms at least, a firearm receiver made from a machined billet of solid steel may offer certain theoretical advantages in the metallurgy of grain structure and orientation over a cast-steel version. However, in terms of the commercial M60 trunnions machined out of barstock or billet steel, this perceived advantage is of no consequence. The widespread application of CNC machining tools now being used even in the small-production shops today, was not the case when these receivers were machined and registered close to twenty years ago. At that time, without having access to the extremely expensive pressure forging methods employed in military production line manufacture, investment casting of the trunnion blank was the most reliable method of duplicating the compound curvatures and other hard-to-duplicate exterior forms of the originally designed MIL-SPEC forging. As a consequence, fully machined billet trunnions bear a distinctively more “heavy,” or “squared-off” appearance totally negating the size-to-weight ratio advantages of the strong, but lightweight, forging of the mil-spec original, or even the casting.
Commercial investment-cast steel trunnion guns are every bit as serviceable as their military cousins, and are equivalent in life-limit and durability if the private owner takes certain common sense precautions. Importantly, these castings also virtually duplicate the exact exterior physical contours of the forged original design, and can actually be very hard to tell apart from a MIL-SPEC forging if the telltale surface features of a casting are not known. These cast trunnions are particularly close to the forged MIL-SPEC originals as the basic casting alloy used was an excellent firearms-grade of steel, and the casting process employed produced a nearly exact unfinished blank that required nearly the same machining steps as the MIL-SPEC forging to complete. When finished, these cast trunnions displayed the greatest degree of uniformity of all commercially produced M60 trunnions. They readily accepted standard military component parts and assemblies used to complete the receiver assembly, and mil-spec parts interchangeability is virtually certain.
With those commercial M60 trunnions machined out of barstock or billet steel though, certain Class 2 manufacturers were content with only replicating the functionality of the original military spec forged trunnion. Due to the difficulties in replicating the hard-to-machine contours and compound curvatures of the original forged-blank design, exterior contours were often left in a rougher and not-exact state of duplication on these billet-steel trunnions. Fully machined trunnions are easily identifiable by their more “squared-off” contours, and while detracting from the aesthetics a bit, remain fully serviceable and inherently strong. Fully machined trunnions are readily identifiable due to their telltale machining marks along all major surfaces, and the less pronounced curvatures around the top of the barrel channel and rear sight mounting base. Interchangeability of MIL-SPEC component parts and assemblies on these trunnions can vary considerably depending upon the tolerances of the final machining; many of these fully machined billet trunnions exhibit indications of hand-fitting of individual parts during final assembly. A thorough inspection of an individual receiver for evidence of hand-fitting of parts or assemblies is highly advised, as later fitting of any replacement parts may be considerably more involved than with another type of trunnion based receiver.
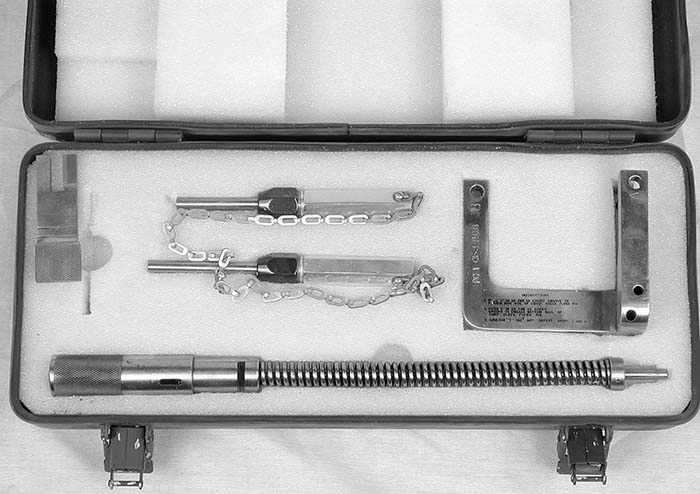
In the many decades the gun has been in military service, literally thousands have been removed from service and DEMIL-ed, and then surplused out as scrap value. It is known that over time various methods for the actual DEMIL procedure of ex-military firearms were used, generally becoming more fully destructive over the years as concerns mounted as to usability of even component parts remaining. It is further known that a few M60 ‘s were DEMIL-ed in a more “friendly fashion” leaving open the possibility of salvaging an un-cut trunnion itself, from which a new “receiver” could be fabricated quite easily. It is therefore possible to have a commercial receiver fabricated using an original, un-cut, MIL-SPEC trunnion still bearing military production markings, and while having no collector’s value, it will be desirable receiver. The major problem here is just how the trunnion was originally joined to the other component pieces of the receiver, if only rivets had to be drilled off the DEMIL-ed pieces, it may render a perfect trunnion, but if there was any welding of the other component pieces this can complicate matters. For a DEMIL-ed receiver to have escaped the mandated reinforcing weldments, it had to have been DEMIL-ed very early on, or come from an out-of-the-way locale in the inventory. (While likely exceedingly rare, there a few known to exist in civilian hands, of this exact origin.)
The last variation in available “commercial” trunnions, undeniably the least desirable, are those individual trunnions that have been re-manufactured from original military production guns that have been DEMIL-ed. Commonly known as “re-welded” trunnions or receivers. Usually these re-manufactured commercial production receivers/guns were built up with all new receiver components assembled onto an original military production forged trunnion that has been re-manufactured into a homogeneous component by welding existing-but-damaged pieces back together. Despite any cosmetic touches rendered during final finish to make it appear “new,” original forged trunnions that have undergone welding should be carefully and thoroughly examined. When originally manufactured under military contract production, these forgings were final heat treated to produce casehardened surface hardness of 57-58+ Rockwell C scale. Case hardening is not very thick as it is intended to reduce surface wear primarily, and drops off quickly to a core value in the high 20’s Rockwell C scale. When rejoining such pieces by welding, followed by seam grinding, the basic welding process along these long and deep seams will likely produce micro-granular fracturing and general stress concentrations that can possibly extend to structural cracking and failure in/near the weldments, or along lines of concentrated stress. (This is far different type of welding than the reinforcement welds described above which penetrate only to a very shallow depth, and with minimal linear progression.) To be clear then, a re-manufactured trunnion that has undergone welding is always suspect for cracking and stress failure along the re-joined seam(s). Though generally serviceable as shooters, these re-manufactured receivers warrant close inspection before purchase (a MagnaFlux®, or fluorescent dye-penetrant type, inspection is recommended), and continuously thereafter in service at regular intervals.
In Part II we will begin discussion of the various component parts and their assembly and interface to the basic receiver assembly, along with a continuing look at factors that contribute to the structural integrity of the receiver.
This article first appeared in Small Arms Review V7N2 (November 2003) |