By Matt Smith
This interview was conducted at the NDIA Small Arms Symposium at Ft. Benning, Georgia, with a follow-up in Vero Beach, Florida.
SAR: Reed, give me a background on yourself and tell me how you got into the business.
Reed: In the mid 70’s, I was competitively pistol shooting and had spent quite a bit of time with the Secret Service pistol camp. They’ve done a lot of training in Florida. I was shooting the revolver for police combat. I had spent a lot of time at Beltsville, and they spent a lot of time in Florida. I had met one of the Secret Service agents that had gone down to Little Creek, Virginia. While he was down there, he had found that they had some Stoner 63’s that were inoperable. He told the armorer there that he knew a guy that had parts for Stoners and that he could call me, and I could probably get his guns working. I went up to Little Creek somewhere in the mid 70’s and repaired a bunch of Stoner machine guns there on site. I had the parts and the knowledge. They had crossed some of the 63’s with the 63 A’s, but I got the guns up and running.
SAR: How did you become interested in Stoners, and find all the parts and weapons you have?
Reed: In the mid ‘70’s, I was at a gun show and a friend of mine gave me a barrel for what appeared to be some type of a machine gun with a carrying handle on it. It was in a canvas, asbestos-lined bag, and I had no idea what that barrel fit, or what it was. I started asking everybody I knew what it was to, and it was like a giant Easter egg hunt trying to figure out what the barrel went to. Finally, I found out the barrel was for a Stoner 63 automatic rifle, which was the one with the offset front sight. From there, I questioned what a Stoner was, and began researching everything I could find on the Stoner and the Stoner system. I became more and more involved in it and I bought a couple guns form different people. Roger Cox, of Law Enforcement Equipment Company, was pretty heavy into them. He had a Stoner 63, that I bought from him. I started chasing more leads down, finding a couple more Stoners, and some parts here and there. Then one day, I called Mr. Stoner down at his house and introduced myself. He had a business up at Fort Pierce, which was about 5 miles away from my shop. One day, he stopped by for lunch. We talked, and our friendship grew from then on.
SAR: What about items from Cadillac Gage?
Reed: In about 1981, Stoner had a warehouse up in his factory in Port Clinton, Ohio, which he wanted to clean out. I went up to look at it all, and we loaded up 3 semi-truck loads of stuff. It was 13 tons of Stoners, Stoner parts and tooling.
SAR: How did Mr. Stoner collect so much ?
Reed: All this stuff had been given or sold to him at the end of the project. They had spent so much money for so many things, chasing so many things, that they just gave it to him for his efforts.
SAR: When did you establish a working relationship with Mr. Stoner?
Reed: It was shortly thereafter. We did a lot of projects together. I did some consulting work for him on the 5mm Advanced Combat Rifle Project. We would go to shows together because of our close proximity. We would travel together, have lunches together, and discuss different projects together. We built a pistol together, the SR 25 we did one summer, and we had a lot of other projects as well.
Trey: He was very open with his information as a mentor. He appreciated the fact that someone was interested in his work. He was happy to share his knowledge.
Reed: Every day, when I would go home from work, I would get books out, and research the older guns. You amass a knowledge that helps you to find the rare guns that are out there. When the book The Black Rifle came out, there were pages and pages of guns in there that I didn’t know existed. Today, I own many of those same guns-not one like it, but that exact, same gun. I consider myself very lucky that I was able to be at the right place at the right time. I got all of Stoner’s personal guns, which were not a lot, but were very significant and meaningful due to the fact that he bothered to keep them. He had an H&K that was a very early ‘60’s .308. I have a picture of him shooting that same gun. From there, he introduced me to the Fairchild Corporation, and I was able to buy all of their guns which were the early protoypes of the ones that he did not own, or have in his name. I was able to accquire Stoner’s guns, Fairchild’s guns, Chuck Dorchester’s guns, the president of Armalite, the Armalite guns from Burt Jenks, as well as Sam Cumming’s guns and the Colt collection. The chance of one person being able to put all these collections together is phenomenal! It has taken me over 20 years to do this.
SAR: Did one thing lead to another?
Reed: On some things, one thing did lead to another, but on others, it was just pure luck! Absolutely being in the right place at the right time, and the right person, and dealing the right cards. I cannot imagine the luck of some of these occurrences, and the odds of finding them. I can show you some parts and pieces where I found half of the gun in California, and the other half in the Colt factory.
Trey: Mr. Stoner, himself, when he would walk in and see the collection, couldn’t believe it! He would see different stages of his life, from when he was in totally different sides of the ocean, all in one place. All of the evolutions, and all brought back together in one spot, has been quite a feat. A lot of people really don’t understand the magnitude of the project with the detail and energy that went in to it.
Reed: Let me give you another example. I found a belt-fed AR-10 at the Colt factory. Five years later, I found the bolt and carrier in a private collection in California. The owner knew it was an AR-10, but he didn’t know it was of a one of a kind prototype part. Five years before I got the gun out of Colt, I had gotten the charging handle and the bipod from a lady who’s husband had died, but who had bought it from Armalite. So five years before I got the gun, I got some parts for it, and five years after I bought the gun, I got the rest of the parts for it. It is finally all put back together. What is so phenomenal about all this, is acquiring parts that are one of a kind, and with only one gun built. I found a box of parts in 1974 that I bought. In 1986, Mr. Stoner transferred Stoner 63, serial number one to me. The lower trigger group was missing off the gun, it was just the receiver. I looked in the box of parts I had bought in 1974, and found the lower trigger group that matched up to gun number one. I determined this by examining photographs of serial number one, which had the same scratch as one of the lowers in my box of 200 to 300 parts. The chance of seeing that scratch and putting that back together, knowing that it fit that gun was one in a million.
SAR: How did you get started with the Military and silencers?
Reed: A month or two after I fixed the Stoners at Little Creek, the SEALs had a problem with what they called ‘vapor lock’. Basically, they were shooting the green tip Supervel subsonic ammo in the Smith and Wesson 39’s with a screw on Hushpuppy. This system had a slidelock and the high pressure cases would stick in the chamber. When they went to eject the cartridge case, the extractor would climb out over the cartridge case. The gun would have a malfunction because it couldn’t clear that cartridge case once the extractor ripped off the side of the rim. I did a lot of work with that and found it mostly to be an ammo issue. I built them a better system using the old 92 Beretta. It was not a military gun back in the late 70’s. I spent time doing that and improving the old Hushpuppy design, which was a Smith and Wesson product on the old 39’s and later the 59’s. The Beretta had a stronger, wider extractor which grabbed the cartridge case, even with that high pressure ammo, the Beretta would actually work better. So we built slide locks on the Berettas, and built thread-on suppressors.
In the late 70’s, a requirement came out of JSSAP for suppressors for the Air Force. We built a product and submitted a proposal and lost. Two companies got an award-one of them was Smith and Wesson, and the other one was Beretta. I didn’t get an award, so I funded the project with my own money. I called the project Snap On. It was an aluminum suppressor with wipes, and simplified the system. In the early 80’s, they were ready to test this program. The Air Force went out to buy parts for the Hushpuppy as the baseline. I just happened to be the only manufacturer for the Navy at that time making parts for the Hushpuppy. When I found that they were going to be doing these tests, I asked the testing committee if they would throw my gun and product into the test. I explained to them I had proposed my system earlier, but didn’t win the contract. The government had spent a quarter of a million dollars with each company to develop this product.
SAR: Had you been supplying the wipes?
Reed: I had been supplying the wipes to the Navy all during that time. The wipes were in a little can, prestacked in a little aluminum sleeve, with the sleeve rolled up. It looked like a roll of quarters, with 8 wipes in it, pre-X’ed. This assembly was put in the front of the original Hushpuppy, with a spring, “O” rings, and a little mechanism inside there. That was the original Smith and Wesson design that they copied from Walther, in Germany. My system used threads, it didn’t use springs, and was a much simpler system. When they got through with the tests and the trials from the Air Force at Eglin, my suppressors won out over the Smith and Wesson and the Beretta. In the mid’80’s, they bought 3800 of these systems from us. They sent us the barrels, and we put the barrel extensions on, and gave them back a barrel and a suppressor in a little plastic box. That was one of the first major contracts that we had on suppressors.
In 1982, which was prior to that, the Navy had gone out on the street, and Mickey Finn, Don Walsh, and myself had proposed silencers for the M16-A1, that the Navy had. It had a very strong endurance test. It had to fire 200 rounds in a very short period of time, and the suppressor had to live through that. Our suppressor was very large, very robust, and used double wall tubing. Our suppressor was the only one that lived through the endurance test. The others would melt down. Don Walsh’s suppressors made out of aluminum would only go about 110 to 115 rounds. It actually burst on the very first trial, so we won it by endurance. It was a fairly large contract in ’82 for us. It was about 1400-1500 Navy suppressors made out of stainless steel. These had a barrel collet on the back of it. You took the flash hider off the gun and threaded the silencer on the end of the barrel. You tightened this collet and it squeezed down on the barrel to make it sturdy. This also kept it in alignment and kept it from vibrating off. It was heavy, and big, but it was effective. It was about 30 – 32 DB’s, which is pretty good. It was an inch and 3/4 in diameter, and it was about 12 inches long. Part of it telescoped over the end of the barrel.
Trey: I think a side note to that is that at the time, he was involved in (orange) grove care. We had a small machine shop set up. I can remember that summer working on those Navy cans, with one other person and myself in this little shop.
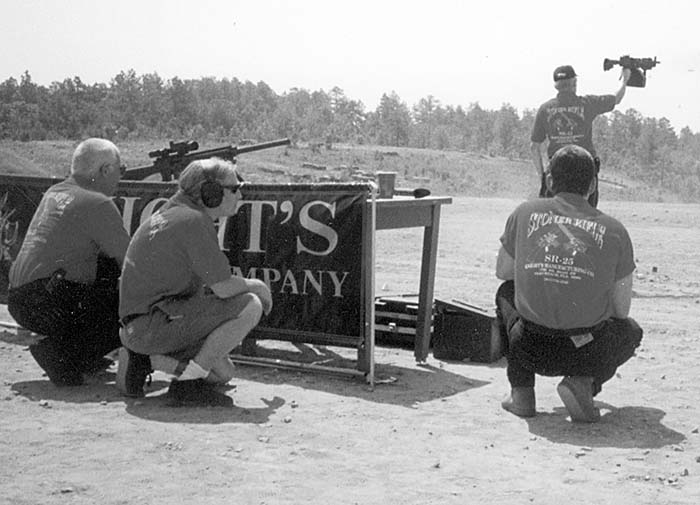
SAR: Which is much different from your facility today, which is pretty large?
Reed: Exactly. We didn’t realize that once you won the contract, then you had to figure out how to get it built. All we were looking to do was win the test. We didn’t have enough sense to know that once you got it, and it was a tar baby thing, that you had to figure out how to build it. We subcontracted some of it out, and did the rest in the shop. A local guy did the blackening of the stainless steel, and we did the engraving. Everything was done in a little Mom and Pop shop. At the time, it was the largest silencer contract that the Navy had ever bought. When the Air Force bought the 3800 Snap On’s, it was closer to the largest silencer contract the entire government had ever bought. We had won the two big, major silencer contracts in the ‘80’s that came out, even though the premier silencer technology house was Mickey Finn, where Doug Olson had been working. They had the leading technology at the time. We won not by default, but being in the right place at the right time, and paying attention to the requirements. I think their product was better than ours, but I don’t think their product totally met the requirements. It’s like wanting a fast car or a station wagon-it depends on whether you’re going to haul something to the dump or whether you’re going to go do a race. That was the early years with suppressors, up to the mid ‘80’s.
SAR: What was the next suppressor that you worked on?
Reed: It was a suppressor for Colt, who did it for DEA. It was an integral 9mm in the late ‘80’s. In ’86 or ’87, we did a suppressor for Colt, like an MP5-SD, only it was Colt 9mm. We vented the barrel, and built an intricate suppressor under the hand guard of the 9mm Colt submachine gun. At that time, I was quite cozy with Colt. I had been doing some work, being a subcontractor for the ACR program, the Advanced Combat Rifle. I did the muzzle break for it. I had gotten in with all their engineers, which helped us when we built the suppressor for their 9mm for DEA. In the late ‘80’s, we developed a suppressor for revolvers, using telescoped ammunition. It was called the Revolver Rifle and was based on the Ruger Blackhawk .44 magnum handgun frame. This was novel, because it was a short gun, light weight, and could come apart to go into a small briefcase. The ammunition used an o-ring gas seal and forcing cone to obtain maximum suppression. We built some very effective suppressors with this system. That was the first time we could get 30 caliber suppressors to go down to 116 DB. It was large, light weight, and a very effective suppressor.
SAR: By that time, would you say you had full machine shop capabilities?
Reed: Yes, we moved into our new building in 1990 and installed our four CNC machines, which were originally purchased in 1986. Today we have about 15 CNC machines. We have grown to about 92 employees, and we do a lot of other things now.
(Author’s note: Reed left at this point in the interview to attend another meeting and Trey Knight and Doug Olson continued the interview.)
SAR: The building you’re in now, you have about 2 other businesses. Can you tell me about them?
Trey: Lawmen’s and Shooters Supplies, is a law enforcement distributor company, selling other peoples products in the state of Florida and the Southeastern United States. Knights Armament Company, is the military side of the house. Knight’s Manufacturing is a company that we set up more for commercial business when the SR-25 was introduced. That was our first time out of the closet, so to speak, with a product we could take to shows and talk about. Mr. Stoner was on board with us fully at that time, allowing us to do things that we would have never been able to do before then.
SAR: Doug, when did you come on board?
Doug: I started to work at Knight’s in January of ’92. I was hired specifically as program manager on the Offensive Handgun suppressor. And at that time, they had the subcontract to Colt on the Offensive Handgun, which was in competition with H&K.
SAR: So you began working with Colt on the suppressor, and this transitioned to H&K?
Doug: That’s correct. At the end of that contract, both the Colt and H&K guns went to the Navy for trials. The H&K gun was the clear winner. The Knight suppressor was the clear winner. The follow-on contract was marrying the two together.
SAR: What were the challenges with this suppressor?
Doug: There were a lot of challenges, and this was a major project! Up to 1992, the state of the art was about 19DB reduction with a plain, dry, suppressor. Not very much. The problem was with the straight-through baffles, which have a large hole and a small outside diameter. It was a major step forward to try and meet the Navy’s requirement of 30 DB reduction. That seemed an incredible task at the time. Everybody knew that this was going to be a very severe challenge
SAR: Did you have a lot of trial and error, then?
Doug: (Laughing) Much! I spent almost two years working full time on this, trying to solve all the problems. We went through a lot of optimization on the baffle. We had a can that we could put the parts in and out of, and we went through a lot of different baffle configurations. We made a matrix of all the possible combinations of components, built them up, and tested them trying to figure out what to do. Some of the things we came up with weren’t obvious. We built them in both directions from where we were, and we were very lucky and very successful.
SAR: Did the manufacturing present many problems?
Doug: We were set up primarily as a machine shop. It turned out that this baffle and the entire can involved an awful lot of fabrication, tooling, and tig welding. That’s how we were able to keep the weight down, and get the suppressor to function so well. The baffle actually turned out to be a follow on from work that I had done with Qual-A-Tec and AWC. We actually dropped that baffle in and we changed how many we used in the can. We changed the shape, but that was what got us to the final solution.
Trey: I don’t think anyone else could have produced that suppressor, even once they had the technology. The manufacturing was almost as much of a challenge as the design was.
SAR: Did you exceed the requirements in the end?
Doug: In the end, we were never able to get to 30 DB dry, but we ended up with 27 DB dry. If you add a little water, we were getting 39 DB, which was unheard of prior to that. On the manufacturing side, once we won the contract, then it was how were we going to produce these things. We bought a welding robot, and a wire EDM. This gave us the capability of getting the bore through the center of the suppressor uniformly, and in line with all the parts.
SAR: Does the EDM burn a hole through the suppressor?
Doug: Yes, you start with an undersized hole, and then the wire puts a bore through the center hole that’s in absolute alignment. That has turned out to be one of the keys to making this a successful suppressor. That’s where H&K was having all their problems building the Mickey Finn suppressor. By the time you weld all these baffles together, and weld them in the tube, how do you machine a hole through the center of it and keep it straight? We found out we had to completely weld the suppressor together to get it to line. A good suppressor gets hot very fast, and so the challenge is how to handle the heat. How do you keep the baffles from melting down? You have to get the heat to the outside of the suppressor, and radiate it out, while keeping the inside from collapsing when it’s red hot.
SAR: Did you have to use any special materials?
Doug: Not on the handgun. We went to a 321 stainless, which is one of the better high temperature stainless steels. This material was enough to handle the volume of fire anticipated.
SAR: Tell me about the H&K SD suppressor.
Doug: What we did with all the H&K suppressors was to take the baffle stack we developed for the .45 Colt, and scale it down to 9mm. We made an all welded can, trying to use as much of that technology on the H&K suppressors. We did both the screw on short cans as well as the SD cans, which utilized the same baffle stack as the .45, and that worked very well. We were able to keep the size down to a 1 and 3/8th inch tubing. What we did was take the Colt Offensive Handgun suppressor and adapt it to become the H&K SD suppressor.
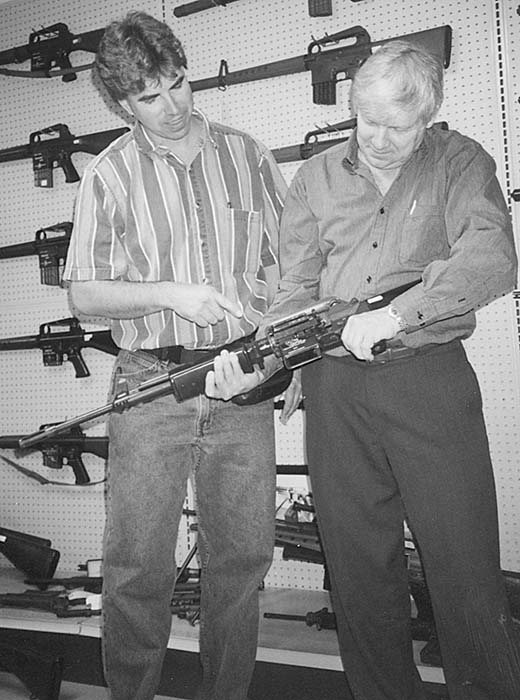
SAR: Did you achieve some dramatic reductions in DB’S with these cans, as well?
Doug: They’re very quiet, but I wouldn’t say it’s as dramatic as the .45, because it’s always easier to make the 9mm quiet. It’s certainly very quiet, very rugged, and more durable. To me, there’s a lot more important things to suppressors than how quiet they are. Everybody dwells on how quiet they are, but to me, it’s how long do they last. Most rounds in the military are used up in training. They’ll go out, take two or three guns with them, and run ten people through the shooting houses, putting several thousand rounds through a suppressor in a day. It’s the durability and no maintenance issues that count in the military. You can’t be changing out wipes thirty-seven times during the course of a day. What Knight’s has done is bring suppressors into the ‘90’s, so that they’re really user friendly.
SAR: Tell me about your current M16 suppressors.
Doug: The M4-QD is what we call it. When I came to Knight’s, they were working on a suppressor for the M16 carbine. They were looking at shortening the barrel, machining baffles on the lathe, milling parts, and putting it all together. There was always a durability problem. We tried putting tungsten carbide inserts in there to take the initial blast, which worked well, until it got so hot that the tungsten carbide cracked. Once that cracked, the whole suppressor was useless. We ended up going to real high temperature alloys, and welded a tube within a tube, which was the key to being structurally sound, and getting through all the tests. It would take 210 rounds within three minutes, and be able to go back into the field with a full compliment of ammo.
SAR: What’s the most number of rounds that you’ve heard have been through one of these M16 suppressors?
Doug: I don’t know, but I have heard they are using it on the M249 Minimi quite successfully. The SOCOM is issuing the M4 in large, unprecedented numbers. They are planning on buying 8000 of these. They are getting to be used more and more. Part of this is that if you are planning to “own the night”, you don’t want to give your position away with flash. That’s why you need a suppressor like ours for the M16. I know that Crane has put over 5000 rounds through our suppressors in testing, and there’s almost no loss of DB reduction.
Trey: We have suppressors in house that have over 10,000 rounds through them, and we haven’t had a failure yet.
SAR: Are these being issued to all the Services?
Doug: I’m not sure exactly who’s getting them. They’re being issued throughout SOCOM units.
Trey: That brings up an interesting point. We’re up against the ideology that a suppressor is only a sniper’s tool, or an assassin’s tool. There are so many other benefits that a suppressor gives you—properly done, there’s an increase in accuracy, the shot time is decreased due to reduced recoil, as well as other benefits. When you have a supersonic round, you’re going to have a ballistic crack. It’s going to be known that someone’s firing, anyway.
Doug: I think one of the big keys of the supersonic is that if you’re down range, and I shoot past you with supersonic, my position is much more masked than if I shoot past you with subsonic. Subsonic rounds are very directional. If your object is to come back from a mission alive, I would rather shoot supersonic. If the object is that you have to get in and out undetected, then, of course, you have to shoot subsonic. You’re at more risk using subsonic, because if there’s somebody out there when you shoot, your location is more compromised. I think the users are getting more training in the use of suppressors and ammunition. The future will see more and more suppressors used, including in regular army units. They will be a part of “owning the night”.
SAR: Tell me about the SOPMOD system.
Doug: Really, this has been a number of contracts. Reed started with the idea of coming up with ways to mount things to the M16 rifle. When I went to work for Reed, one of the things that they were doing was building some test guns for the Marine Corps. I became involved with that and helped come with the first prototype that mounted in place of the handguard. The more we worked with it, the more of a systems approach we’d take.
Trey: The SOPMOD kit is adding performance to a known weapon.
Doug: It’s going to keep moving forward. The kit is going to change over time. That’s the whole idea. As new pieces appear, they’ll be added, and as pieces become obsolete, they’ll be taken out. The suppressor became part of that kit really because it could be abused and used through all the training, and still survive. It is becoming more of a standard issue piece of equipment.
SAR: Are there any other products which you see yourself working on in the future?
Doug: Yes, as we go into the future, I see more and more suppressors for big guns. We’re expecting a contract from Holland for a 25mm gun, which is a discarding sabot gun.
SAR: How do you deal with the sabots?
Doug: It’s going to be interesting. What’s driving this is that their test range is beside an environmentally sensitive area, with nesting birds. We hope to build a suppressor that will at least take the muzzle blast out of that. They look at DB, not just as a peak, but based on an average. It’s going to be a challenge because the sabot starts to open up immediately upon exiting the muzzle. The suppressor has to accommodate this, and we’ll take our best shot at it. I’d like to do work on the 155mm, as I think there is a need there. How many cannon cockers do you know that have all their hearing? People need to look at the environmental side of suppressors. In Europe, they are accepted because if you go hunting, you don’t want to disturb anyone, or hurt your own hearing. This feeling that suppressors are only assassin’s devices is going to change slowly.
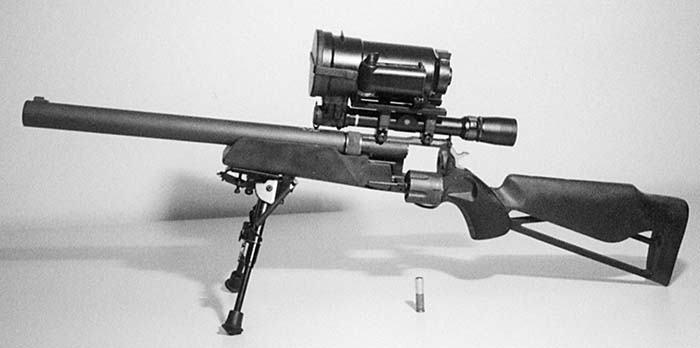
SAR: Tell me about your work with the .50 caliber.
Doug: One of my first projects at Crane was the .50 caliber sniper rifle. Back then, Qual-A-Tec was one of our contractors. We built an aluminum tube .50 cal suppressor with all titanium baffles. We were able to do some real good work with that. We were able to shoot 16 inch groups at 1500 meters, with the suppressor. I see a potential need there, but so far there hasn’t been a large contract for these.
Trey: We are finally getting our .50 caliber rifles into production and start working on the suppressor in the near future.
(Author’s note, Reed rejoins the group at this time).
SAR: Tell me about the Military Armament Corporation auction.
Reed: There were about 15 people there. It was a bankruptcy auction for the entire factory and inventory. It was cash and carry or certified check only. One guy, Fred Rexler, who was a large Class 3 dealer at the time, put in a bid for everything to be sold for $250,000. The auctioneer rejected it, and the auction lasted for 3 days. The most significant thing I remember was them trying to sell guns, but there were no buyers. They had pallets of Mac 10 .45’s, with 100 guns on a pallet. There were 3000 to 4000 guns all together. The auctioneer asked how many people wanted to buy a pallet at a minimum bid of $650. I raised my hand and bought a pallet of 100 guns for $650. The guy next to me told me I was crazy because they wouldn’t be good for anything other than bookends, and I was just wasting my money. I thought to myself that I had just thrown away $650. I raised my hand again when another pallet came up, and bought it. After a while, with no one else buying them, I questioned myself, and what I was doing. I owned two machine guns the day I walked into the auction-an MG 42 and a Mac 10. I walked out of that auction owning 750 NFA weapons. I bought all I wanted, and there were plenty left. Everyone was telling me I would never get them transferred to me, and I would never get my money back. We didn’t know if the government was going to destroy the guns, or if they would transfer them to us. The ATF was struggling with a federal judge and a bankruptcy auction, and since these were assets, the judge wanted them sold. The ATF said maybe they’ll transfer, and maybe they won’t.
SAR: Were these completed guns?
Reed: Most of them were completed guns. All were in boxes and packaged for sale, with matching suppressors in other boxes and lots for sale. I bought some of everything. I had $50,000 in cashiers checks that I took to the auction, and I only spent $11,000. I could have spent a lot more money, but I looked at it, and I was very conservative. If I had been more knowledgeable, I would have done better. At that time, I didn’t know what to get and what not to get.
SAR: What does a Mac 10 sell for today?
Reed: Somewhere between $850 and $1000. I still have 200 to 300 of them left.
SAR: Were you a Class 3 dealer at that time?
Reed: Yes, with my 2 machine guns. I was just setting myself up. I had no real knowledge of what to get or what not to get. I went by myself to the auction, but met Pedro Bello who sat next to me. He cost me a million dollars, and I remind him of that every time I talk to him. He scared me off from making money.
SAR: Who else was at the auction?
Reed: Romalee Skinner was there, the people from Interarms, Ron Martin, and others whose names escape me at this time.
SAR: How did you hear about the auction?
Reed: It was in Shotgun News, and it was just a blitz to state there would be a bankruptcy auction. Nobody really went, though. It was just a fluke that I went. After that, every time someone had an auction, there were a million people there, because they thought it would be like the Military Armament auction.
SAR: I want to thank all three of you for sharing your thoughts and experiences with me and the readers of the Small Arms Review.
This article first appeared in Small Arms Review V3N5 (February 2000) |