By Miles Vining
Since the companyโs inception in the 1980s, Barrett Firearms has made leaps and bounds from the former garage that Ronnie Barrett used to make the first M82 anti material rifles. Today the company is expanding into the AR market, machine guns, and precision rifles with their MRAD design. Taking that momentum into the 21st Century is Christopher Barrett, the current president of the company. Chris was kind enough to sit down with SAR as we interviewed him about his history with the company, and where he wants the company to go in the near future.
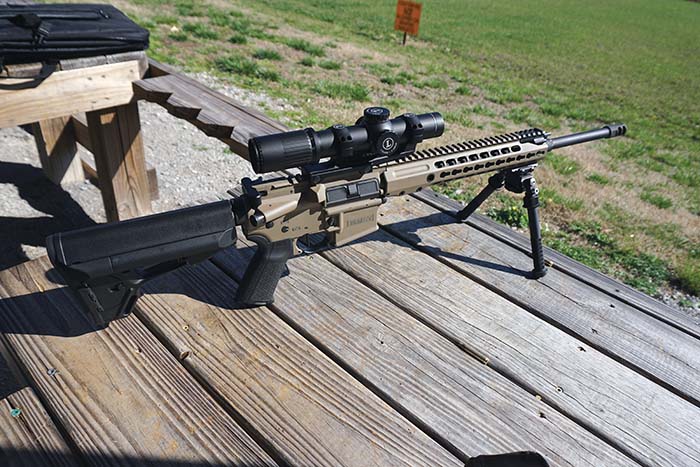
SAR: Were you involved with Barrett Firearms from the beginning?
Chris: My earliest memories were of my dad shooting, and his firearms interests. He had machine guns in the 1980s, was a big time hobbyist, always shooting in sub-gun matches. He just had the coolest things in the world to a little boy. Iโve always been a part of the culture of this industry. I was around four years old when dad really came out with the company in 1982. I was shooting at a very young age, which a lot of people might not agree with these days, but it came naturally to our family. It helped make me the shooter I am today, and also helps with the designing aspect. I mean, people who actually shoot a lot, can identify what works and what doesnโt, and we put that into our designs. You could call it the Barrett โDNAโ of the company, a lot of us are shooters, and we use the products we make. As an example, we donโt make submachine guns, but we still learn things from them that we can put into our other designs. If you are always in tune with that sort of thing, it makes you a good designer.
SAR: How did the company develop, throughout its history?
CHRIS: Well we started with the garage years, we lived in two different houses, with two different garages that dad was putting the rifles together in. The first house was in downtown Murfreesboro, and it was literally a wood walled garage, with gravel on the floor. They rolled out carpet over the gravel, and they realized that if they dropped a pin or other small part, they couldnโt find it. So they took the carpet and turned it over, and you were walking on the back portion of a carpet. But dad made a lot of guns out of there. Then from the garage, we actually leased a building because we outgrew it, out on Manchester highway. It was a former bus repair building where they fixed Bluebird school buses. It was owned by a man in Murfreesboro who invested in the company early on. We had that building for several years, during the 1990s. Then in the early 2000s, we moved over to this building. We built every M107 of the initial contract in that old building. We quickly outgrew that new building, and then built an extension to it, which is where we are today, connected by a ramp and it was a much higher ceiling for the running of CNC machines. Very thick concrete floors because these machines have to be on a very stable base, because of the vibration and harmonics.
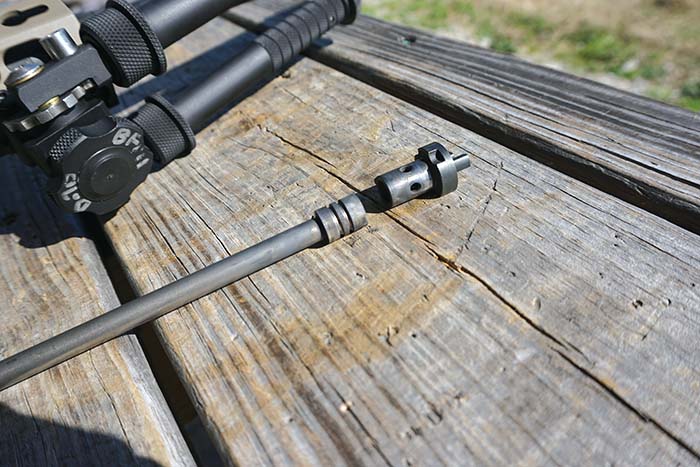
SAR: When did you really start getting involved with the company?
CHRIS: Even as a young teenager and a child, I was tinkering at the plant. I remember being a kid, around 10-12 years old and I was operating acetylene torches, and doing stress relieves on welds. When you see your dad doing stuff like that, you always want to be a part of it. Another thing that helped was that we worked on cars together, we restored cars together. When I was 14, he bought a 1964 Corvette and we restored it together. I did the small jobs while he did the big stuff, but what you learn about metal working, fiberglass working, engine building, playing with gears in a transmission, you really take with you for the rest of your life. Most people just donโt have that opportunity anymore. We were doing that as the company was growing from the very early times. I went to High School, took computer aided drafting as a class, specializing in AutoCAD, working with two dimensional drafting. We donโt really even do that anymore, we do all our work in three dimensions now. When I graduated High School, I had no aspirations to attend university or go to college whatsoever, didnโt even occur to me. I wasnโt a good student, so I came right out of high school and that summer I came to officially work for the company full time. I got to work in the back, doing some of the jobs that I was already doing as a teenager, sand blasting, operating a band saw, sawing up raw stock. Every job I did, I wanted to improve immediately. For example I said, โHey, letโs get a new sandblasting cabinet, letโs automate this sawing processโ. So I got to move around the company and do a number of these jobs. This was around 1997 or so. After having this spot for a while I started realizing that this was all still on paper, there was no automation to it. We needed to make a revision to this. Chris Vaser, one of our oldest employees, was still drafting designs on paper for the company. Absolutely phenomenal draftsman, old world type with the lead pencils and putting things on paper. But this was what our technical data package was at the time, and this in the 1990s! It was on pencil and paper. It is beautiful and romantic when you think of it, but the technology of the industry at the time had far surpassed this. I mean, as a high schooler in 1995, I was working with AutoCAD programs. As an example, it automatically verifies geometry, with a pencil and paper, you could โcheatโ and could get away with making mistakes. Computer aided drafting has really changed this industry in ways that we canโt imagine. I mean, we are in the golden age of firearms design. There is nothing like a brand new off the shelf rifle, a $400 hunting rifle that can outshoot the sniping rifles from the Vietnam War. A lot of this is because of computer aided modeling.
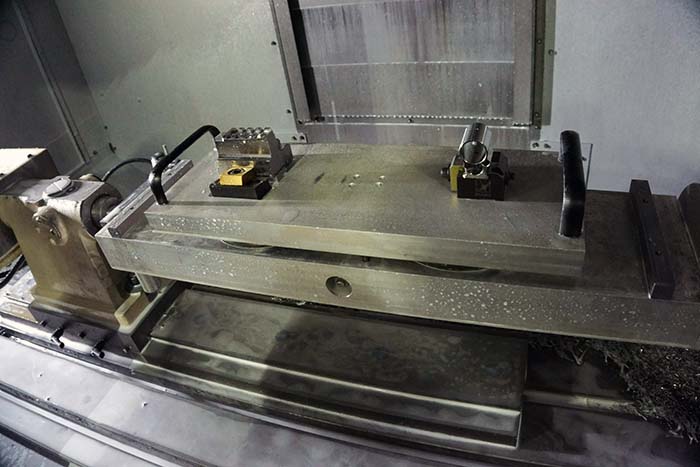
SAR: What role did you play in this computer revolution?
CHRIS: I bought the first engineering computer for the company, I remember it was a monstrosity of a tower and a monitor which was probably only 18 inches at the time, and we thought it was huge. We spent almost five grand on it, and in that day it was considered a major investment, along with the Pro Engineer software package. At the time it was the leading computer modeling software, so I sat there and learned how to use it. Not the most intuitive thing in the world, but after about a year or so, I designed the very first Model 98 on that. The prototype was actually a semi automatic .338 Lapua. Up to that point, it was the most radical departure we had made from our .50 caliber designs. The .338 Lapua Magnum was just starting to really gain some traction in the U.S. in 1997/98.
SAR: Accuracy International was becoming successful with their .338 Lapua and the Swedish contract in the early 1990s.
CHRIS: I hate to throw a bone to a competitor, but that rifle, at the time was recognized for there being nothing like it outside of AI. We heard the buzz about .338, and through that we kept plugged into our community of military and police buyers, so we knew there was beginning to be a need for the cartridge in a sniper rifle. It was sort of the thing in 98, but then it went dormant. We then heard of military solicitations for a .338 rifle in 2008, about 10 years later. At the time, we only had the Model 82A1 series, and the Model 95 and that was it. We only had two products back then, and they came in one color, and in one caliber. We essentially had two fixed products, like Henry Ford with the Model T, just coming in black. They were of a certain architecture at that time, and stamped sheet metal. They were .50 caliber, and were actually precision limited, in some part due to the ammunition. The .50 BMG round is not developed like a .338, a .308, or even a .223 is. Itโs a machine gun round. Getting into the world of precision shooting was tough because we really didnโt build things like that.
SAR: Essentially they were 3 MOA anti material rifles.
CHRIS: Exactly, I mean even the Model 95, you probably could get an inch, inch and a half group out of it, depending on handloading. At the time we knew we needed a precision rifle. We did like semi autos, but we looked at what was the most accepted, most accurate, and precise rifle at the time. And it was the Accuracy International line. So dad bought one of their AWs for testing and evaluation. And we were looking at certain things, about what made it shoot so well and we found out it had some principles that we liked. But we wanted a semi-automatic, and were thinking along the lines of what would a semi auto version of the AW look like. So in the Model 98, you can see some of that inspiration with a strong rigid, bedded chassis, a flat bottomed receiver that looks a lot like a bolt action. A free floated barrel with a handguard beneath it. There was some influence there, but on the inside it was one of the most novel things ever. Although we never put that design into production at the time, we were able to take certain design elements from it and use it in our current rifles. Aside from that, when it comes to firearms design in general, you have to learn to only take the good elements from other designs, and make sure to reject the bad. However, I hate novelty for noveltyโs sake; I want to design things for a practical purpose. But moving on, we werenโt and arenโt financially managed. We donโt have a list of share holders to report back to, we essentially do what we think is best for the company. Thus, the Model 98 project was sort of shelved until 2008. We noticed other companies were starting to produce their own single shot .50 caliber rifles, but no one was really getting into the .338 production. So that is where we focused our efforts on production and design. Looking back on it now, the original design we had for the Model 98, was interesting and forward thinking, but it wasnโt designed for production. And that goes back to our Advanced Research Group, a term that I prefer to R&D. Ideally those designers back there should be dreaming, not developing. They should be building up a design library, coming up with concepts such as the Model 98, that although might not be feasible to produce, will all us to come back to them in the future when we might actually see the potential for such products. Separate from this we have a product development team, that does that product development, because that has to happen, in order to keep the company on track.
SAR: So what kicked off development of the single shot Barrett?
CHRIS: We saw all these cheap single shot fifties springing up all over the market, and it really hit us because we established that lead with semi-automatic .50 caliber rifles. We didnโt want to lose that edge we had in the .50 caliber rifle market. We developed the Model 99 immediately. That was entirely new architecture as well. It looks much like a Model 95 on the outside, but it is entirely different. The Model 95 and Model 82 series are all sheet metal, fabricated, and welded. The Model 99 was really the first use of the architecture that became everything that we build now, in the Model 98B and MRAD series. It is made from a single piece of aluminum extrusion that forms the foundation of the receiver, with the barrel rigidly affixed to that. The Model 99 is really the genesis of what I believe has become the new defining architecture for precision rifles. The 98B and the MRAD basically are really different. When they came out, people were still just taking sporting rifle actions and solidly bedding them into fiberglass stocks that mimic wood stocks. We called it โBโ because it was a revival of the 98 program, B for bolt action. But it was a head scratcher to people when they first saw it because they would look at it and say, โWhereโs the action? Where is the stock?โ. Well, there isnโt an action or stock in the way that you know it, like a Winchester Model 70, or a Remington Model 700. That doesnโt exist in the Model 98. It is a barrel rigidly affixed into an aluminum chassis that surrounds the barrel, and puts the bore axis really low, and gets the scope up higher. Then a lower receiver that separates from the upper like an AR does. So I think it really set a new course in the industry because after that I started seeing a lot of chassis going around. Another thing that is significant about the Model 99 is the breech mechanism, it has that interrupted thread that has been a significant design feature of the 98B and MRAD series.
SAR: What motivated Barrettโs movement towards the AR15 platform?
CHRIS: It started with the Barrett M468 in around 2003, and prototype production in 2004. What got us into the 6.8 SPC experiment was that the Army Marksmanship Unit, and some other entities at 5th Special Forces Group, specifically Master Sergeant Steve Holland, came to us back then and were showing us all this 6.8 stuff. It wasnโt even SAAMI standardized yet, AMU was hand loading these cartridges out of .30 Remington cases. They also had a .22 SPC, a 6mm SPC, a 6.5mm SPC, and a 7.62mm SPC. People donโt realize just how extensive this testing was. They were shooting all these odd cartridges, and they finally settled on 6.8mm. They came to us with a Mark 12 Designated Marksmanโs Rifle, and said, โWe need this, in 6.8, or a Recce sort of rifle, also in 6.8mm. We had no interest in getting into the AR game at the time, it wasnโt even a blip on our radar. But this whole 6.8 thing piqued my interest, the fact that it goes on a standard 5.56 lower receiver. We shot some of it and realized it was significantly more powerful, and it wasnโt some sort of niche that fills a gap between two cartridges that you canโt tell the difference between. So we started looking at it and that is how the M468 came along. I made some enhancements to it, such as the larger gas block because of the increased bore size. But we made a novel front gas block that had a flip up front sight and a suppressor interface for a suppressor design that would surround the barrel and actually attach to the gas block. If you look at an M468, you will see a ratchet on the gas block that attaches to a suppressor. The idea doesnโt really work nowadays because people are wanting suppressors to be modular and have the ability to be put on different rifles, but it was just something we were experimenting with. We built a good amount of M468s, probably put more into civilian circulation in the U.S. than any other company.
SAR: Development of the M468 then led to the REC7?
CHRIS: We started looking at the viability of a piston operated AR because of that, although the M468 itself was a mid-length direct gas impingement rifle. At the time there wasnโt much of a choice when it came to piston operated ARs. 2007 was the official release date, and we came up with REC through Reliability Enhanced Carbine, and 7 for the year 2007. The piston system on it, in my opinion, is the finest piston operated system on an AR out there today. It is one piece, it comes out the front of the rifle with one other part that holds it in. A lot like an FAL really, but the handguard doesnโt have to come off, and it doesnโt separate into seven different pieces. It is indicative of what we strive for at Barrett, making it well, but not overly complicated in a smart design. Anyone can make something complicated, but a good designer will strive to make something simple.
SAR: What sort of inspiration did that piston design take from?
CHRIS: I would say it is a hybrid of the FAL and the AK. The gas plug is a little like the FAL but doesnโt have this spring loaded mechanism like the FAL does, to retain it or switch it to a grenade position. The piston design takes a little from the AK, but we patented the fluted cylinder that is in there. This is important because a lot of other piston operated AR designs try to trap the gas in there, using gas rings, etcโฆ We wanted the REC 7 to be simple, and hard to break. Ours runs without gas rings, like an AK. We found out a way to let the gas out of the gas block by incorporating a fluted cylinder. Early prototypes werenโt allowing enough of the gas out of the system and the piston was actually getting stuck in there from the carbon build up. We then put four flutes in the back of the gas block cylinder, cut with an end-mill that took away surface area at the rear, but we left it sealed at the front, where it needed the power stroke, then when the piston gets to the rear, it enters an open area, similar to an AK. These flutes allow that gas to blow around the piston and not allow it to clog up. The gas will then flow into the handguard, and this is why on REC7s with thousands of rounds, youโll see some soot underneath the handguard. One of our earlier prototypes went 22,000 rounds without any sort of cleaning. From there we advanced the design to a Gen 2, with a better handguard system, and built-in steel QD mounts.
This article first appeared in Small Arms Review V20N9 (November 2016) |