By George E. Kontis, PE
The visit by Springfield Arsenal representatives to the General Electric firing range was official business. Their purpose was to monitor the progress the engineers were making on a development the Army had funded. Leading the visitors was Otto Von Lossnitzer, the former head of Mauser in Nazi Germany who had been courted at the end of the war to work for the U.S. Government. Otto had been a party to many gun developments including a 20mm revolver cannon he designed for use on the F5 Aircraft. The gun GE was developing was a 7.62mm Gatling gun, called the Minigun. At this stage of the development, it was having its share of problems. As the customers watched, the gun experienced one stoppage after another. Otto and his team were forced to wait while each jam was cleared, damage assessed, and cause determined.
At the other end of the building a range technician sounded a countdown: “Ready to fire, One- Two- Three:” Wonnnnnnnnnk. There was a short pause. “Ready to fire, One- Two- Three” came again, followed by Wonnnnnnnnnk. The unmistakable sounds of bursts coming from a small caliber Gatling gun reverberated through the range building. “What was that?” asked Otto. “Oh, just some R&D project,” came the reply. “Can we see it?” he asked. “No, sorry, it’s a Company proprietary project,” was the answer. What the Springfield team had heard was the sound of Minigun B.
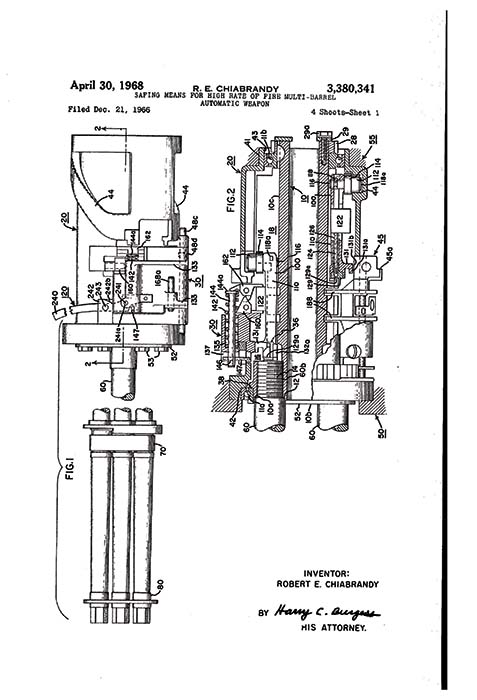
GE upper management was well aware of the development problems with the gun and between them were now calling the Army-funded gun “Minigun A.” The development of Minigun A was not going well and management recognized the importance of this Army contract. The decision was made to spend Company money on a back-up plan. They selected one of the company’s most talented engineers, Robert (Bob) Chiabrandy (pronounced Sha-Brandy) to complete an alternate 7.62 Gatling that would come to be known as, Minigun B. This would mark the second time Bob was asked to design this gun.
In the early 1960s, the General Electric Armament Systems Department in Burlington, Vermont was actively engaged in the production of 20mm cannons for gun pods and internal applications for fighter jets like the F104 and F105. Insurgency actions in Vietnam, including the movement of weapons by personnel along the Ho Chi Minh trail, suggested a fast-firing small caliber Gatling might be an effective anti-personnel weapon when fired from fixed wing aircraft or helicopter. Glimmers of interest from both the Air Force and the Army got GE’s marketing department excited about the prospects of such a gun. When Advance Design Engineer, Bob Chiabrandy went to his boss with the idea to design one, there was plenty of companywide support. Chiabrandy offered them a deal that was hard to pass up. Give him a designer to help him work out his concepts on a drafting board and he would perform the engineering analysis. In three months he promised a complete design.
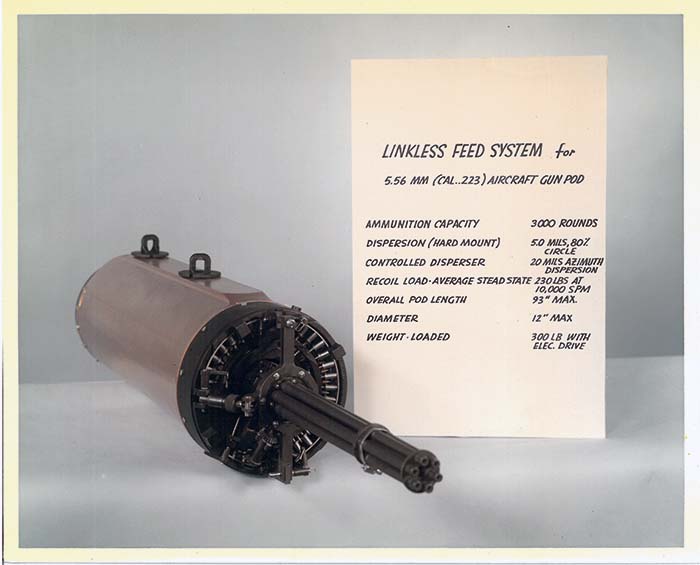
Before the design began, Chiabrandy set the design goals. The most important one was that all barrels would be clear of live rounds at the end of every burst. Safety was key. There would be a safe way to arm the gun and a safe way to disarm it as well. There would be as few moving parts as possible, particularly in the gun bolt. Springs were allowed, but only when there were no other reasonable options available. When used, pins and other fasteners were trapped or otherwise secured so there was no chance they would loosen during the tremendous vibration expected during firing. All load-bearing components would receive a thorough stress analysis to assure long life and all rounds and cases would be under complete control throughout the cycle.
Talented designer, Dick Eaker, was assigned to work under Chiabrandy’s direction on the program. While Dick began laying out the design on the drawing board, Chiabrandy conducted complex dynamic and stress analyses using a slide rule and design charts. Stresses in the gun bolts were analyzed to assure a sufficient margin of safety. Other hardworking components were analyzed for strength, fatigue, and wear. There was no guesswork and no cut and try. If there wasn’t a way to find the forces and other data needed to conduct a proper analysis, Bob would base his calculations on sound predictions or tests he designed and conducted. Nothing was left to chance because that was the way Chiabrandy worked. He was highly regarded in the company, particularly by his colleagues in the Advance Engineering Department.
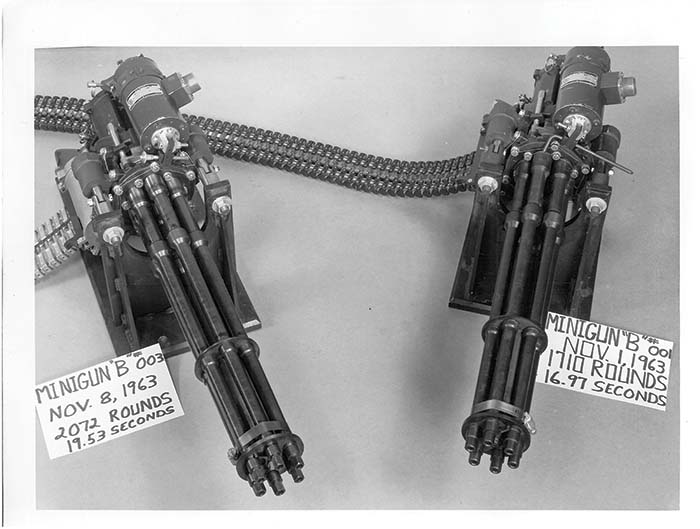
The starting point in the design of any Gatling is the elliptical cam in the main housing. Depending on the length of the round, the number of barrels, and the desired firing rate, this cam determines the diameter of the gun. The elliptical cam Chiabrandy developed was no ordinary textbook design. He custom tailored the cam corners to give smooth acceleration and deceleration of the bolts to assure smooth operation and long life. The stroke of the cam was ideal for the 7.62mm round.
A six-barreled Gatling gun is made up of six individual gun mechanisms secured to a common rotor. A bolt for each gun completes a stroke feeding rounds in and fired cases out while pausing at the front and rear only long enough to fire at the front and extract at the rear. Since the rotor is rotating at all times, the length of the forward dwell is of utmost importance. It must be long enough to allow for complete chambering and locking and of sufficient length to allow the firing pin time to fall. After primer ignition, even more dwell time is needed for pressure in the chamber to rise and then fall to a level that is low enough for extraction. After that, even more time is needed to unlock the bolt before the elliptical cam engages the bolt roller to bring it to the rear. If the forward dwell is made too short, the gun unlocks under pressure from the round, working the extractor hard and possibly even creating a case separation or other unsafe condition. If the dwell is too long, the diameter of the cam is unnecessarily increased and the all-important gun weight increases rapidly. For a six-barrel Gatling, the forward dwell was sized to reach 6,400 shots per minute (spm) at start up in order to average 6,000 spm at steady state.
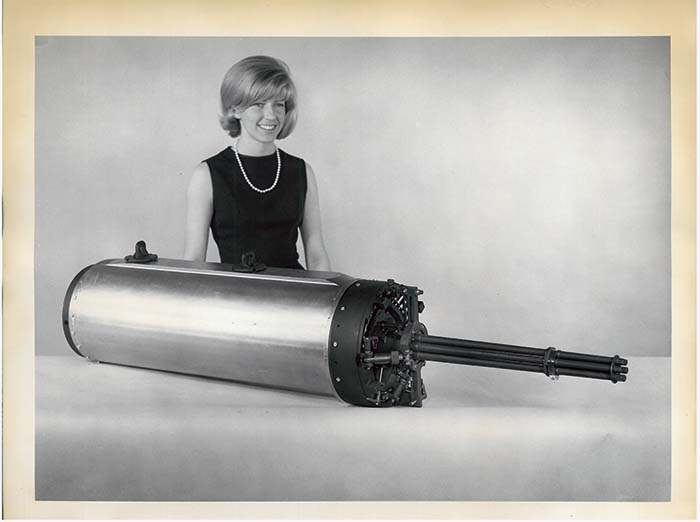
After three months the design was complete. Unlike the multi-piece bolt of the 20mm M61 cannon with its tilting lock block, Bob’s bolt was easily machined from a single block of steel. From the top it looked like an arrowhead with a fixed extractor at the point. After chambering a live round, a fixed cam on the gun housing forced the front of the bolt down into a pocket in the rotor where it remained locked as the round fired. When the chamber pressure was low enough, another cam on the housing engaged a hook on the front of the bolt and lifted it out of the locked position. There were no moving parts, no wing locks or bolt rotation. The bolt body was a single block of hardened steel. The bolt design included a unique safety feature that had never been tried on Gatling guns and might have even been unique to firearm design. The firing pin and the primer were not in line with each other at any point in the cycle except for that one time when the bolt was fully locked. There was no chance that a round might fire inadvertently from a broken firing pin or a sudden stop in the gun rotation. It was genius.
During the design review mandated by GE company policy, the manufacturing team reviewed the design package and pronounced this gun would be inexpensive to machine and easy to produce. The Manufacturing department had often struggled with building complex design shapes, being limited to some extent by their conventional lathes and mills. They welcomed this new design because every one of Bob’s parts was easy to produce. What many of them didn’t know about Bob was that he was also a talented machinist. Before he would affix his signature to the drawing title block, he would review the placement and tolerance of every dimension. He imagined how he would set it up to machine it and had his draftsmen dimension the part accordingly.
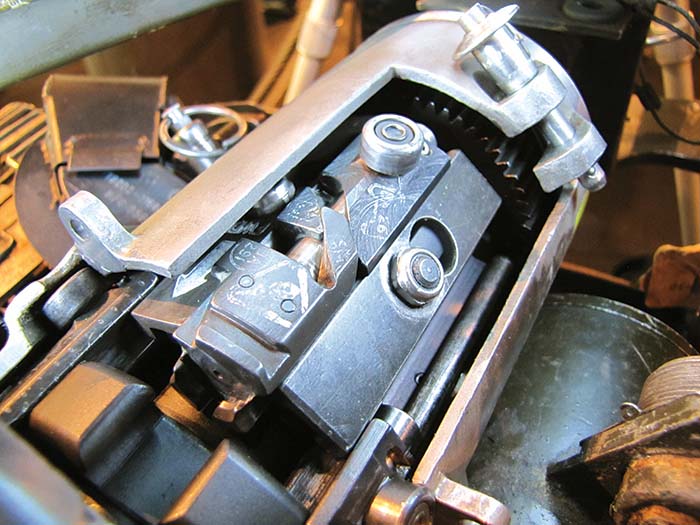
As Chiabrandy took the gun through the early development stages he was fully on board with its eventual transfer to Product Engineering. GE split its developmental engineering into two parts. The Advance Engineering Department dedicated most of their time to Research and Development projects, while the rival Product Engineering Department followed production and developed new systems primarily by modifying or scaling existing designs. There was plenty of bickering between departments, and not all of it good natured. Advance Engineering was viewed as a bunch of overpaid eggheads who rarely came up with a saleable idea. Product Engineers were accused of performing little to no technical analysis, designing “by eye,” or “trial and mistake” as they jokingly called it. In truth, there were huge talents in both departments and a lion’s share of the world’s most innovative and reliable gun and ammunition handling systems developed in the last century came from one or another of these two departments.
Soon after the design was complete, Bob’s big opportunity came when he was invited to present his design to the engineers at Springfield Arsenal. Traveling with Bob were the marketing representative, Dick Burke and Ray Patenaude, a hard-charging engineer from the Production Engineering Department who was poised to take over after the gun was released for production. When it came to engineering, Bob and Ray were complete opposites, and as far as company politics went, the mild-mannered Bob, was no match for the intimidating Ray. Their briefing would be to none other than Otto Von Lossnitzer who headed R&D at Springfield.
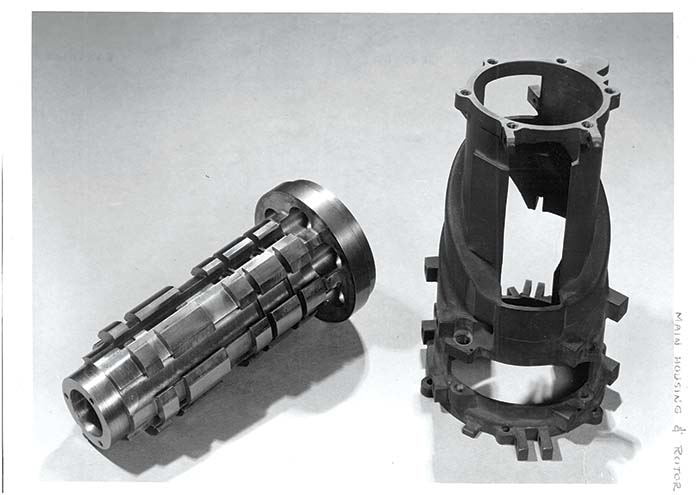
Bob explained all of the proposed weapon functions that included a de-linking feeder, safing and arming means, and a method of clearing to assure there was no round left in the chamber lest it would cook-off at the end of a burst. Von Lossnitzer and his team listened attentively as Bob did most of the talking. Suddenly Otto blurted out: “Now I understand,” he said, looking directly at Bob. “You represent the technical approach.” Glancing at Ray he said “…and you are a politician.” Then turning to the salesman who had contributed little to the discussion he said: “What is it that you do?”
After the paper design was complete, GE sent the final report to Springfield who responded three months later. It seems Otto was not too complimentary on the design. He felt there were unnecessarily complicated functions, like the end stripping feeder, and the clearing action that diverted 6 to 8 live rounds out of the gun after each burst. Bringing live ammunition into the battlefield and dumping some of it overboard after every burst? This had to have affected his German sensibility. Considering his former experience with revolver cannons, Otto was not a big fan of the Gatling. Bob was devastated by the negative report. Jack Harding, manager of the Product Engineering Department wrote a strong rebuttal. As politely as he could, Jack pointed out to Otto that all the design features he was shown had been thoroughly worked out and were essential to the design. In spite of that, Springfield’s interest waned. At that point in time, nobody in the Army wanted to fund a 7.62 Gatling gun development.
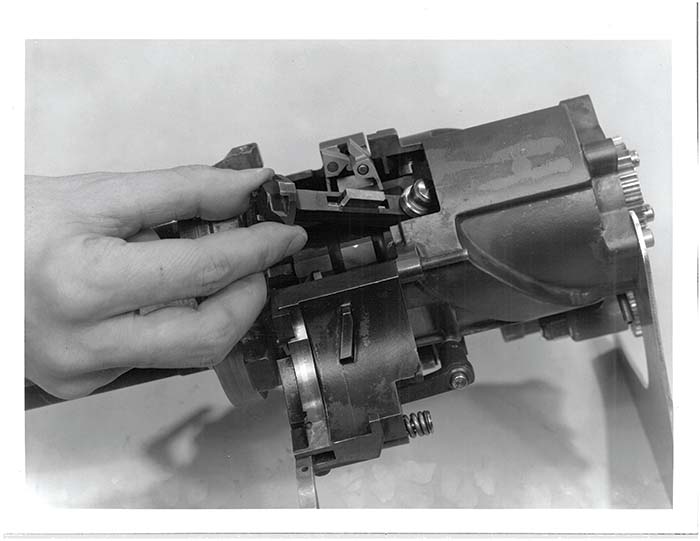
It must be noted that in those years, all of the services, were supporting the development of various gun designs that included caseless ammunition, case telescoped ammunition, and liquid propellant guns. Each service wanted industry to investigate new gun and ammunition concepts and often provided funding, but their interests were never in sync. To a developer and producer like GE, it meant that if they had a design that one service no longer wanted, interest from another would not involve a long wait. True to form, it wasn’t long before Eglin Air Force Base, led by Dale Davis, said they wanted a 5.56 Gatling gun pod. Since Bob Chiabrandy was working on an important project at the time, and because so much development work had already been done, a scale down to the 5.56 Gatling design was given over directly to Ray Patenaude. To assure continuity in Bob’s absence, the hapless Dick Eaker was made part of their team. While the design was in process, Eglin’s interest faded and suddenly Springfield responded with renewed interest, reiterating their requirement for a 7.62mm gun, not the 5.56mm. Due to an embarrassing, but what now may be recognized as a fortuitous engineering error, Product Engineering had made the length of the elliptical cam on the 5.56mm Gatling far too long. It was so long that it could accommodate the larger 7.62mm round. Patenaude, his engineers, designers and draftsmen were able to make adjustments for the larger cartridge.
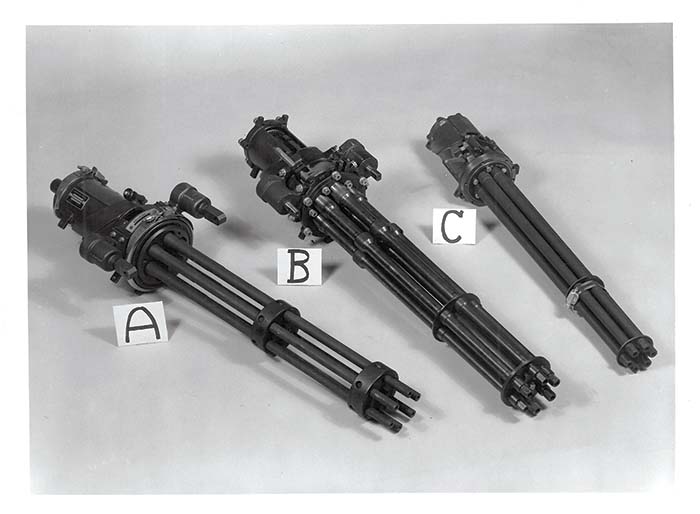
Chiabrandy quietly monitored the progress of Patenaude’s design. Chiabrandy, who would drop by Dick Eaker’s drafting board from time to time, was surprised to see a huge departure from their original concept. “That doesn’t’ look anything like our design.” Sizing up the design features, Chiabrandy could tell these new innovations were not going to work. Dick responded that he was only doing what he was told by the guy in charge of the project. Chiabrandy was worried, not only for the Company, but for his reputation as well. He knew it wasn’t his business to interfere, but he was the one who pitched the initial design to Springfield and he was concerned that the Army would associate his name with the final result.
Sure enough, as soon as the new gun was put into test there were major problems. Chiabrandy had predicted that the breech would fail and it did. It required a major redesign. There were no provisions for safing the gun, none for clearing the chambers at the end of a burst and there were other essential features missing as well. Problems with the new design reverberated through the company. The heads of Product and Advanced Engineering met with their boss and the decision was made that this project was too important to fail. GE’s upper management decided to let Chiabrandy build Minigun B as a back-up to Patenaude’s Minigun A.
Chiabrandy’s gun required certain long-lead items, so he went ahead and ordered them. Castings for the feeder and the main gun housing were ordered, as were the drive motors. He had been allocated a budget with sufficient funding to build three sets of everything. Oddly, no barrels were ordered, ostensibly because he could use the ones from Minigun A – if Patenaude would allow it. He did not. That didn’t bother Bob in the least. Even without barrels he could prove out a lot of the design by cycling dummy rounds through the system. He would check for round control and any signs of excessive wear while putting the gun through all of the design cycles and carefully working up to full cyclic rate.
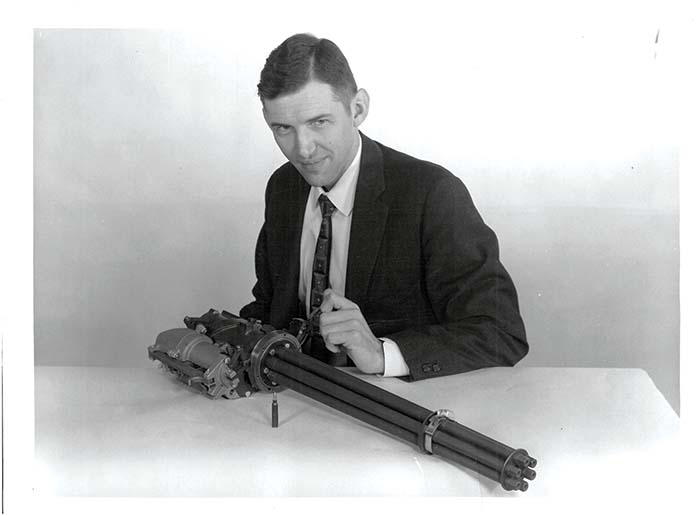
In early March, Minigun A gun was experiencing problems. Top management decided to give Bob money for barrels in order to get his design turned back on. However, they decided to keep the existence of Minigun B from the customer. By the summer of 1961 Minigun B, had fired 20,000 rounds. Weekly meetings were held between the heads of Advance and Product Engineering along with Chiabrandy and Patenaude.
Much of the source of the problem with Minigun A was its complex two-piece bolt. The back half of the bolt was a casting where the main roller was mounted. A cam slot in the aft bolt portion accepted a finger from the front bolt portion. After a round was chambered, the front part of the bolt would stop forward motion while the aft portion continued to be driven forward by the roller engaging the elliptical cam. Forward motion of the aft bolt caused a rotation of the front part in order for its locking lugs to be rotated to an engagement point for locking into the rotor. In order to accommodate the extra forward motion required for locking, the elliptical drive cam in Minigun A had to be made extra-long. Many questioned the wisdom in selecting this bolt design. Not only was it complex, it was extremely difficult to machine. The finger extending from the front bolt was long and flexible – difficult to hold steady to allow proper machining. The Production Department was quick to dub it “the fickle finger.” Many in the Company asked why he’d made it so complicated. Patenaude would explain that it needed to be difficult to manufacture, otherwise even the most unsophisticated of our enemies would be stealing the design and shooting guns like these back at us. Surprisingly, some management warmed to this idea.
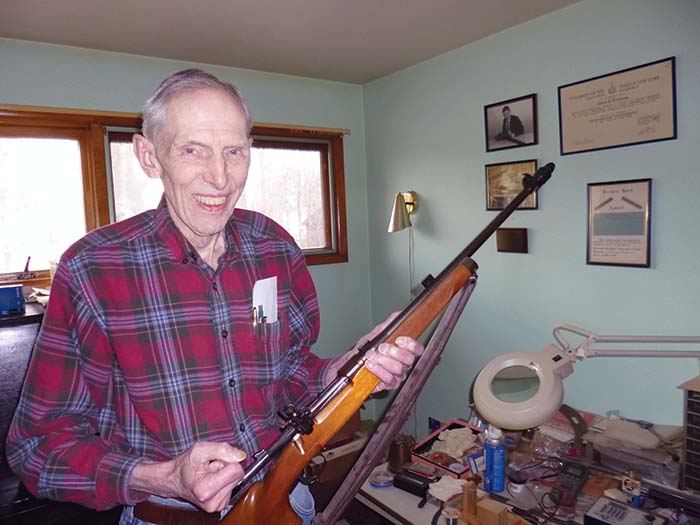
In time, Patenaude and his engineers fixed their problems and Minigun A was running well. The decision of which gun to continue with was left up to Patenaude’s boss, Jack Harding. Jack announced that he’d decided to go into production with Minigun A. Patenaude had won. Chiabrandy made it known how displeased he was with the decision. It was more than just sour grapes. Chiabrandy had started the project and interfaced with the customer. Now he no longer wanted to be associated in any way with Patenaude’s Minigun A.
Jack Harding’s decision was not well received by the Manufacturing Department. They had already expressed displeasure when charged with building the Minigun A prototype parts. Many of its complex parts were seen as a production nightmare. When production did start, Manufacturing found that the dimensions on the drawings did not necessarily make acceptable parts. They were forced to set up dedicated machines that would make bolt parts to a point where they could be tested. If they passed, the manufacturing would continue. It wasn’t just the bolt that was complex. One of the secrets in getting the main gun housing through production was the deburring operation on the elliptical main cam. Deburring is normally a point in the production cycle to remove sharp edges and eliminate cut hazards. The elliptical cam of Minigun A was “deburred” until a bolt could be smoothly cycled through, otherwise it wouldn’t work.
In spite of the difficulties experienced in building the components of Minigun A, when the gun was sent to the field, it worked great. Minigun A was an enormous success on the battlefields of Vietnam, making the ever increasing heap of scrap bolts and other parts worth the effort. Years later, when Production Engineering head, Jack Harding, left GE for another company, he confided to upper management that if he’d had it to do over again, he would have selected Minigun B.
Bob was very concerned about the morale of the dedicated Minigun B team. He consoled them by reminding them that at the end of the day they could at least say they’d had a lot of fun. Probably unbeknownst to Bob, the team had few regrets. They had gotten to work with one of the best mentors in the business, Bob Chiabrandy. Everyone who ever worked with him recognized how much better they were at their job afterwards. Each member of his team had acquired a new appreciation for the importance of dynamic and stress analysis, the need to think about how a part will be made before describing it on a drawing, and best engineering practice. Not long after the Minigun A and B saga ended, I joined GE and had the opportunity to work under Bob’s direction.
As one might have predicted, the Air Force revisited their interest in a small caliber Gatling. It was a pintle version of the 5.56mm Minigun they sought. This time there was no question in the minds of top management that design responsibility would remain in the hands of Bob Chiabrandy as long as possible. Only after the design review and successful testing would the newly designated “Minigun C” be turned over to Production Engineering.
Minigun C did look slightly different than big brother B, but the bolt design remained the same. Considering a potential aircraft application where short time on target necessitated a high firing rate, Bob designed the forward dwell to reach 11,400 spm for a steady state firing rate of 11,000 spm. When the gun worked flawlessly, it was passed over to Product Engineering, again under the direction of Ray Patenaude. One of Patenaude’s technicians, Dave Hathaway, was a huge fan of the design, believing that Minigun C gun could exceed its design rate, possibly even reaching 12,000 spm. One day during development testing, under no authority but his own, Hathaway charged up the 24 volt batteries to their peak and added an extra one for good measure. Minigun C fired several bursts at 12,000 spm. Bob Chiabrandy had designed the fastest firing gun in the world.
The Air Force ordered a small quantity of these that were delivered and deployed in an undisclosed application. The Company named the 6,000 spm pintle system the “Six-Pack.” No one can be found that knows exactly where they went and what they were used for, only that they were deployed somewhere on a classified project.
This article first appeared in Small Arms Review V19N1 (January 2015) |