Thompson submachine gun enthusiasts simply use the phrase, “West Hurley’s.” By most accounts they are the scourge of the Thompson community – sometimes with good reason. They are nothing like the Colt’s in beauty or manufactured like the World War II guns to exacting government specifications. But they are a brother none the less to their earlier siblings, though some would argue a step-brother.
The first West Hurley Thompson’s rolled off the assembly line in 1975 as a product of the second Auto-Ordnance Corporation in West Hurley, New York. This was a company started by Numrich Arms Corporation (NAC) founder George Numrich and then President of NAC, Ira Trast. The new Auto-Ordnance Corporation (AOC) was formed to begin production of a new semiautomatic .45 caliber Thompson rifle, one that resembled the famous American Tommy Gun. In conjunction with the Thompson semiautomatic rifle, AOC also put back in production the full auto 1928 model with a newly manufactured receiver and frame. Full auto West Hurley (WH) Thompson’s immediately found a niche market as an inexpensive substitute for a Colt, Savage or Auto-Ordnance at Bridgeport. The initial retail price as shown in the 1975 NAC catalog was $425.
All references to the Auto-Ordnance Corporation or AOC in this story relate solely to the new Auto-Ordnance Corporation at West Hurley, New York unless followed by the words “at Bridgeport” (Connecticut).
The full auto WHs were mostly Model of 1928s, but a small quantity of M1A1 models were produced right before what has come to be called the May 1986 machine gun ban. WHs have continued to enjoy a niche market in the post 1986 period because, again, they are the cheapest Thompsons in the market place. While many purists howled and degraded the efforts of Numrich and Trast in the 1970s, everyone will agree AOC did place over 3,800 more transferable Thompson’s in the National Firearms Registration and Transfer Record (NFRTR) for all to use and enjoy. Absent a few post sample guns built from various other manufacturers from time to time, the WH full auto Thompson’s are the end of an era.
The purpose of this story is not to degrade the manufacturing process of a very small American company that produced a $425 machine gun. It is to inform owners and potential owners of full auto WH Thompsons about some of the parts used during the production – and problems associated with those parts.
AOC certainly could have used the United States Postal Service motto for flat rate shipping – “If it fits, it ships.” Standardization is not a word normally used by WH owners. Each WH Thompson is truly unique when it comes to fit, function AND parts. There is no WH specific production year or serial number range that is the best to buy – or any to be avoided. A NIB (New in the Box) WH is not a guarantee a WH Thompson will run; it only means no one has tried it out.
The majority of WH parts examined for this story are of low quality investment casting and do not conform to original ordnance specifications. Even when manufactured correctly, the resulting part is much rougher and softer than an original Colt or GI part. Many WH parts are easy to identify because of the purplish hue. Some cast parts are challenging to properly blue because of silicone that is added to the steel alloy to improve the flow when the molten steel is poured into the mold.
The saving grace is all the WH parts will interchange with GI manufactured parts. Replacement for most is always the best option.
Danger!!!
One part in particular is dangerous. The 1928 buffer pilot, commonly referred to as only the pilot or the buffer, was originally designed as a one piece machined part. Sometime during production of the WH Thompson, AOC designed and manufactured two-piece pilots. The reason the pilot was originally designed as a one piece part can be seen in the accompanying pictures; WH pilot’s can and will come apart. All owners, including dealers stocking used Model of 1928 WH Thompsons for sale, need to check the pilot (right now) to insure it is of one piece construction or a GI part. Any two-piece WH pilot should be destroyed. Why risk the potential for injury over what is now a readily available and inexpensive part.
West Hurley Parts
Most WH parts do not pose a threat of bodily injury but can and do affect the function of a Thompson. Stated below is a listing of known parts manufactured by or for AOC:
- Actuator (Model of 1928 only)
- Barrel
- Bolt (M1A1 model only)
- Breech Oiler (Model of 1928 only)
- Buffer Pilot – (Model of 1928 only)
- Butt Stock Slide Group (Model of 1928 only)
- Compensator (Model of 1928 only)
- Drum magazines (Model of 1928 only)
- Frame
- Grip Mount
- Magazine Catch
- Rear Sight, adjustable (Model of 1928 only)
- Rocker pivot (fire control lever)
- Safety
- Sear
- Sear lever
- Trip
- Vertical Fore Grip & Pistol Grip Many WH parts can be easily identified because of the lack of manufacturer markings. All U.S. government subcontractors during World War II were required to apply a marking to their production; while “S” and “AOC” (at Bridgeport) are the most common subcontractor markings, many others exist. A great reference for manufacturer markings on Thompson parts can be found in Frank Iannamico’s excellent Thompson book, American Thunder II. Careful examination and comparison of WH parts to known GI originals make distinguishing these parts an easy matter. CAVEAT: Original parts manufactured by Colt are also unmarked; Colt parts have been found on WH Thompsons.
Mr. Trast
Mr. Ira Trast, retired president of Auto-Ordnance Corporation, West Hurley, New York, graciously agreed to be interviewed. He stated at the beginning that due to the passage of time, he has probably forgotten many of the day to day production details that would be of interest to collectors nowadays. But he agreed to provide whatever information he could remember. Mr. Trast pointed out the new AOC was manufacturing both Thompson rifles and submachine guns so he was not focused solely on the production of the full auto guns during his tenure as President.
Mr. Trast stated the production of the receivers and frames were subcontracted to a local company in Saugerties, New York named Quality Manufacturing Company. AOC supplied Quality Manufacturing with the tooling for production of these parts. The tooling was quite old and had to be modified to fit Quality’s machines.
AOC had a large inventory of Thompson parts when production of the first Thompson guns began in 1975. The first full auto Thompsons were made using all GI parts but as sales increased, inventories of GI parts began to dry up. Mr. Trast spent many hours scouring the country looking for many of the Thompson parts mentioned during this interview. Mr. Trast stated it is important to point out GI parts were not only used in the beginning, but as available during the 11 years the full auto Thompson was in production. AOC only used their own subcontracted parts until new supplies of GI parts could be found. Toward the end of the production run, there was really no need to look for GI parts because none were available in any quantity.
The early Thompson guns featured original Lyman rear sights but soon supplies began to run low. Mr. Trast believes it possible AOC may have used some sight bases purchased from the Model Gun Corporation (MGC) of Japan on the full auto WH Thompson but he is not 100% sure. Sometimes parts used on the Thompson Model 1927 rifle were used on the full auto guns – and vise versa. He is certain that AOC soon subcontracted the manufacture of the sight base and these bases were fitted with an Enfield sight leaf assembly. Later, AOC had a sight leaf assembly specifically manufactured for the base. Mr. Trast remembered the cast sight bases would sometimes come loose from the receiver so AOC began using large rivets to correct this problem.
The horizontal fore-grips and sling swivels were very plentiful as were the butt stocks. Rear grips were plentiful at first, but later had to be manufactured. All the vertical fore-grips were made by a subcontractor, the identity of which now escapes Mr. Trast. As the stock slide inventory was depleted, aluminum stock slides from MGC were used. The MGC slides were not without problems so AOC began subcontracting the manufacture of the stock slide in the GI pattern but of aluminum alloy.
Many of the smaller parts like sears, trips, rocker pivots and safeties were manufactured by IONA Industries, Newburgh, New York. While AOC used other subcontractors at times, Quality Manufacturing Company and IONA Industries were the two subcontractors that manufactured the majority of parts for AOC. Both were located close to West Hurley, New York (and both are now out of business). Generally, Quality Manufacturing manufactured the bigger parts and IONA Industries manufactured the smaller parts. Mr. Trast stated there may be variations or changes of the same AOC part as production continued over the years.
Mr. Trast did not recall a problem or any issues with separation involving the two piece buffer pilot. AOC used GI buffer discs.
Compensators were another item that was soon in short supply and the manufacture of this part was subcontracted to IONA Industries. AOC roll marked the Thompson bullet logo on the top of the newly manufactured compensators in-house. Mr. Trast stated AOC had all the original Thompson roll dies starting at the Colt era. However, the older machinery necessary to use these early roll dies was not readily available and therefore many of the original dies could not be used. AOC had to remanufacture some tooling and dies when production began in 1975.
The supply of breech oilers also became a problem. Mr. Trast said AOC manufactured a few oilers, but “could not get it right.” The oilers manufactured were discarded. He does not remember purchasing any aftermarket oilers for use in the full auto guns but added this was a long time ago so anything is certainly possible. With no oilers available, a decision was made to delete this part altogether.
AOC refinished and sold GI drums at first. Supplies soon ran low and it became difficult to locate GI drums that were not too pitted and/or rusted and could be refinished into an acceptable product. AOC purchased and converted MGC drums to work in real guns. These first drums were named the XL drums, but the modifications only allowed for the loading of 39 rounds. AOC also used MGC drums for their .22 caliber Thompson by welding a .22 stick magazine inside the drum body.
A decision was made to manufacture new drums but it was almost two years before the new L (50 round) drums were on the market. This was a major effort for AOC that ran into many problems, especially with the rotor spring. AOC formed a new company for this venture, Valentine International. A decision to manufacture the C (100 round) drum came later. It was believed only 1,000 Colt era C drums were manufactured with each one being individually numbered. Mr. Trast believed AOC limited production to only 1,000 numbered C drums. As with the AOC L drum, the rotor spring became a big issue on the AOC C drum.
AOC manufactured the barrels for the Thompson guns in-house. Completed barrels were sent to a subcontractor to cut the fins and thread the ends of the barrels for the receiver and compensator. Mr. Trast remembered the early barrels with the large fins and sharp edges. AOC developed a tool to radius the sharp edges of the fins; this procedure was done in-house. As production continued, the later barrels were much nicer than AOC’s first efforts in this area. Mr. Trast does not remember if the front sight was manufactured in-house or by a subcontractor.
Mr. Trast recalled the purplish parts and how the bluing process was a problem for AOC. He believed the problem may have had something to do with impurities in the steel used to manufacture the parts. AOC always purchased high quality 4140 gun barrel steel but sometimes it came from outside the USA. He said it was a continual effort to properly color the parts.
The supply of bolts became an issue when the AOC M1 Thompson was introduced in 1985. As supplies of M1A1 GI bolts were exhausted, AOC subcontracted out the production of the M1A1 bolt.
As the interview came to an end Mr. Trast made a comment that will be of great interest to all WH owners. The “A” at the end of the serial number on the full auto Thompsons stood for “automatic.” Mr. Trast believes the ATF asked AOC to use this designation to easily differentiate the serial numbers of the full auto guns from the Thompson rifles.
Parts, Parts and More Parts
Actuator: This is a commonly found WH part with several known variations. Careful examination will reveal a casting line down the middle in many of them. Most WH actuators have what appear to be milled cavities in the side; however, later variations were machined from bar and are without these cavities. The cocking ball on the unrelieved WH actuators is actually a separate part and staked to the body of the actuator. This can be another dangerous part. One WH owner reported the cocking ball came off during firing and hit him in the head nearly requiring stitches (another excellent reason for everyone anywhere near a firing line to always wear shooting glasses). There are also differences noted in the knurling on the cocking balls; some are plain or without knurling. The WH actuator can cause functioning problems and bend or break during firing; it should be replaced with an original GI part.
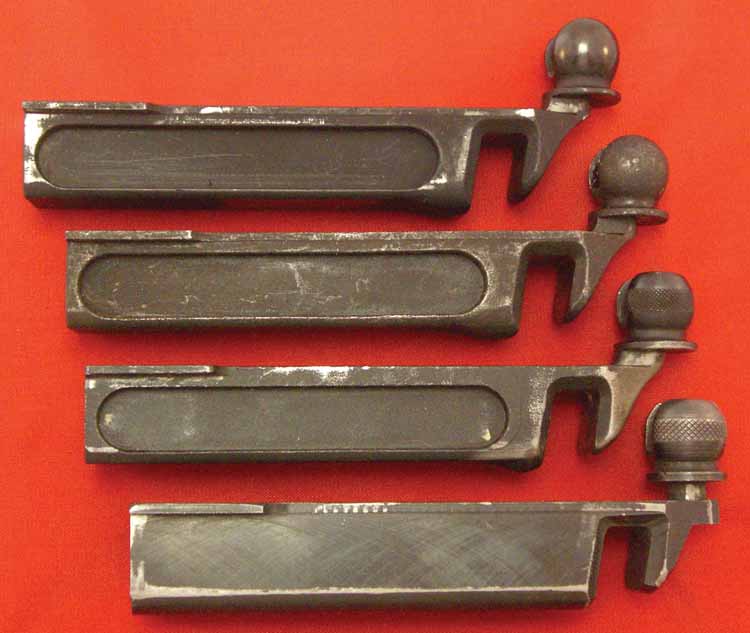
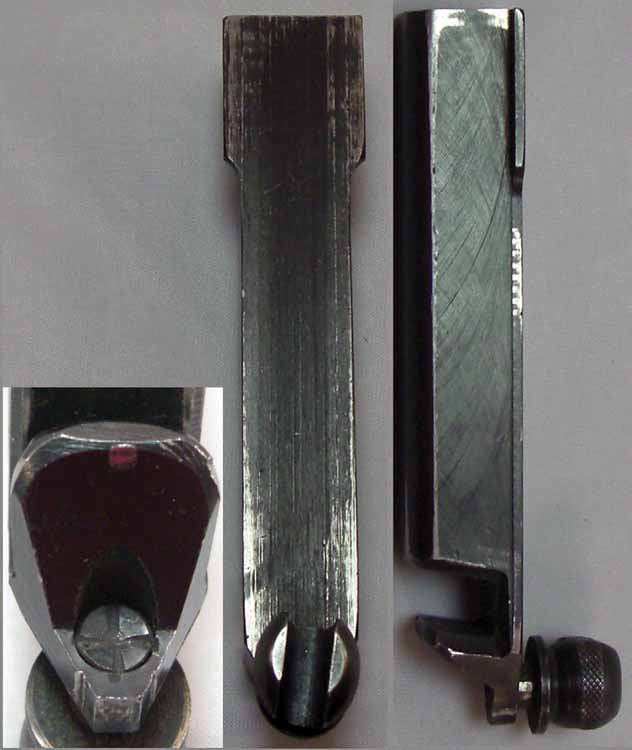
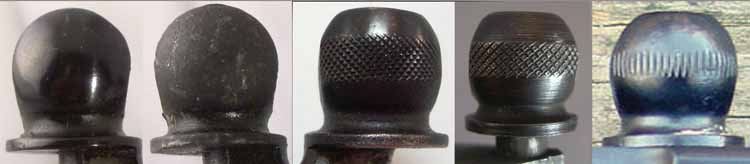
Barrel: This is a commonly found WH part with several known variations. The fins on many of the early WH barrels are very sharp. Sharp edges and corners are characteristics of many WH parts. However, later production WH barrels can be found with radius fins. Most WH barrels are known to have head spacing or chamber issues. If all WH internal parts have been replaced with GI parts and functioning problems continue, a WH barrel may be the cause of the problem. Cosmetic issues aside, this part may be used if brought back into proper specification.
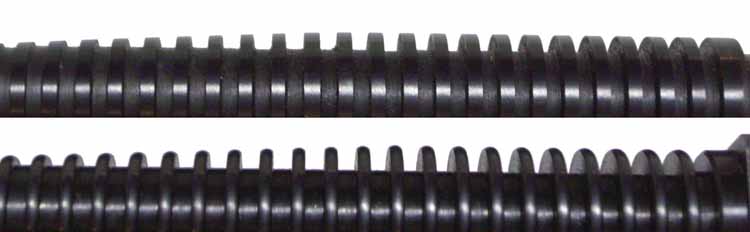
Bolt: As supplies of GI M1A1 bolts became exhausted, AOC subcontracted the manufacture of M1A1 bolts. WH bolts do not have a manufacturer code as found on the WWII GI bolts. The quality of the WH bolts has been reported as both good and bad. Given the large number of inexpensive GI M1 and M1A1 bolts now available on the market, this part is a good candidate for replacement. AOC did not manufacture bolts for the 1928 WH Thompson.
Breech Oiler: AOC used GI oilers until the supply was exhausted and then simply omitted this part with new production guns. AOC included a notification to this effect on many of the later WH Thompsons. Research has uncovered an inexpensive oiler that has been found is several WH Thompsons, including a new in the box WH Thompson purchased in 1981. It is very possible AOC purchased and used some aftermarket oilers at some point during the production run. Irrespective of how these oilers ended up in WH Thompson’s, this oiler type is a good candidate for replacement.
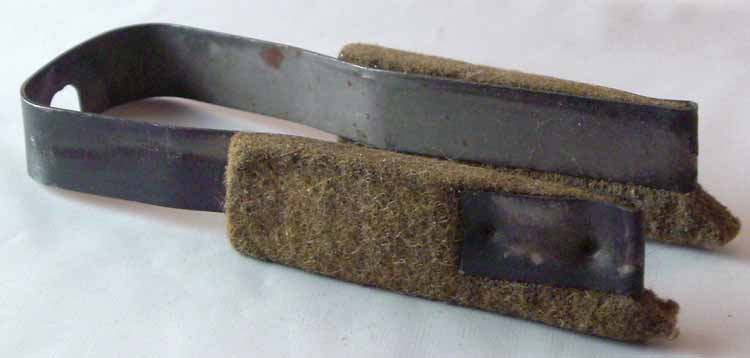
Buffer Pilot (Model of 1928 only): This is a commonly found WH part with three known variations. The two-piece WH buffer pilots must be replaced – see above. It is dangerous to use this part in a Thompson submachine gun. One of the two-piece WH pilots has the flange press fit on the rod; the other has a cut out in the flange that locks on to the rod. AOC did manufacture a one piece pilot; however, like most WH parts it is not manufactured to GI specifications and should be replaced.
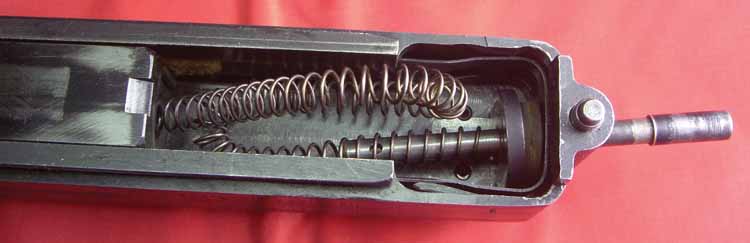
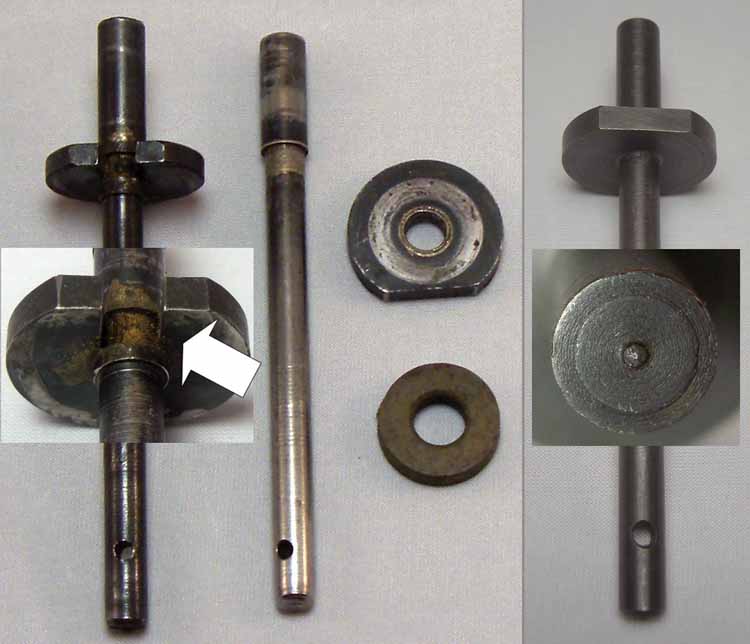
If there is any doubt as to the buffer pilot being a one or two piece unit, replace the pilot with a GI part (that will be marked with “S” or “AOC” (at Bridgeport) on the flat part of the flange). Don’t take a chance with this part!
Butt Stock Slide Group (Model of 1928 only): When the inventory of steel GI stock slides ran out, AOC purchased from MGC an aluminum butt stock slide group. There are two variations of the MGC slide. MGC assemblies are not manufactured to the exterior dimensions of the GI or Colt assembly and are easy to identify because the top of the rear mounting screw is visible. MGC slides also have a separate catch button. AOC soon learned the MGC slide was not meeting expectations and began production of a GI style stock slide cast off aluminum (or a light weight alloy). As with the MGC slide, the fit of the WH stock slide to the lower frame is generally very loose and the painted finish is quickly worn off. While serviceable, aluminum stock slides are good candidates for replacement.
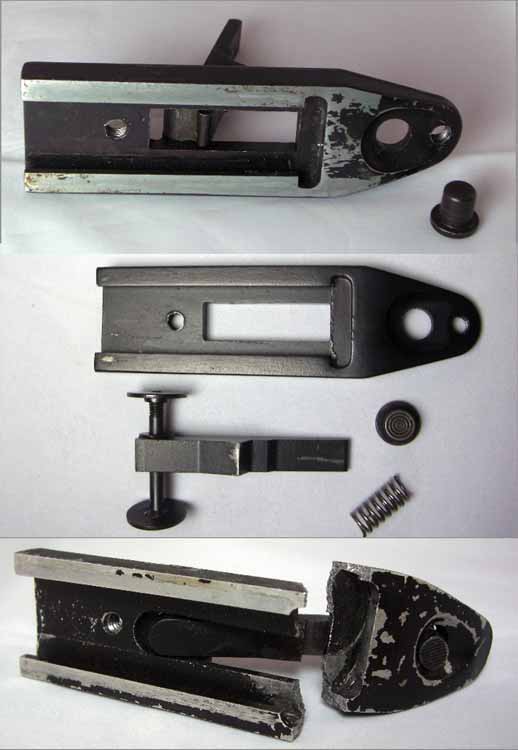
Compensator (Model of 1928 only): This is a commonly found WH part with two known variations. It is easily distinguished from the Colt and WWII counterparts. The only marking is the trademark Thompson Bullet Logo displayed on the top of the compensator in front of the slots. The slots are usually sharp. WH compensators were not pinned from the factory and usually installed with a good dose of adhesive (as were the barrels). This WH part is quite functional and generally only replaced because the owner prefers the look of an original GI part.
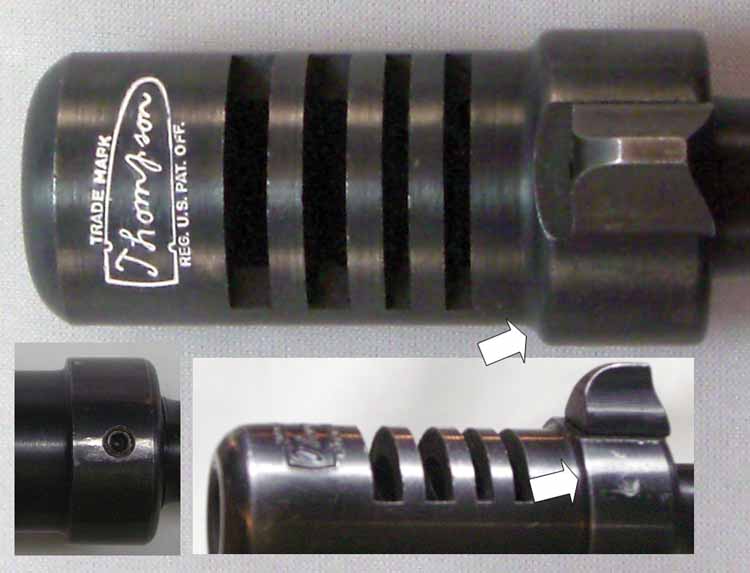
Drum magazines: Most WH L and C drum magazines need work to run properly. WH drums were bringing a premium price during the 10 year assault rifle and high capacity magazine ban; this has passed. Avoid these drums unless you factor in the cost of an overhaul. Lower cost alternatives now exist. WH drums are easy to identify because the center hub is solid. In addition to the L and C drums, AOC also marketed an XL and X drum.
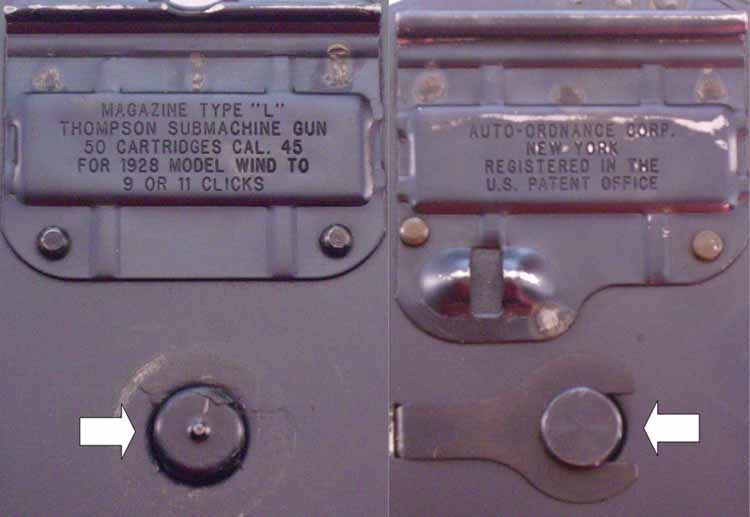
Frame: These have sharp edges and are often found to be not manufactured to exact GI specifications. However, this part is normally serviceable and can often be brought into GI specifications. Frames were not serial numbered by AOC.
Grip Mount: Grip mounts used on WH guns include the following variations:
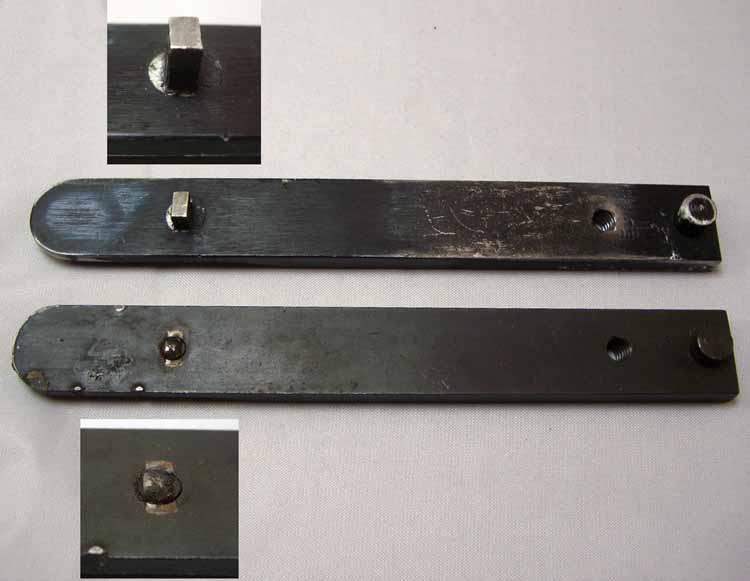
- GI milled (solid stock), 1/2 inch
- GI riveted, early (retaining stud is a separate part), 1/2 inch
- GI riveted, late (retaining and barrel rest studs are separate parts), 1/2 inch
- WH riveted, steel, 3/4 inch
- WH riveted, aluminum, 3/4 inch The 3/4 inch grip mount is the most commonly found. While most are serviceable for sporting use, the WH 3/4 inch aluminum parts are particularly prone to breakage. The milled steel (solid stock) grip mount is the best for every purpose.
Magazine Catch: This is a commonly found WH part with several known variations. Some have holes and a cast diamond pattern on the end; some have a dimple instead of a hole. Many are purple in color or have a purplish hue. This part can be a source of trouble and should be replaced with an original GI part.
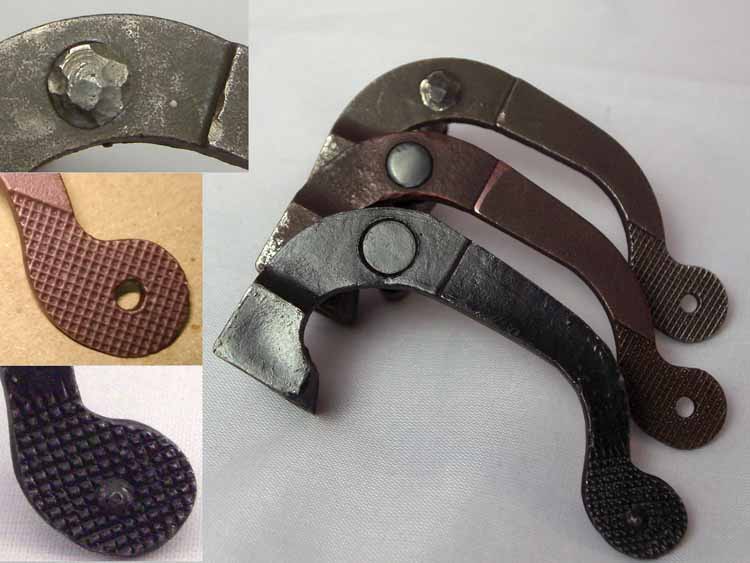
Rear Sight (adjustable) (Model of 1928 only): The serviceability of the WH rear sight is not as good as the original Lyman. Various parts were used to make up sights, including the following combinations:
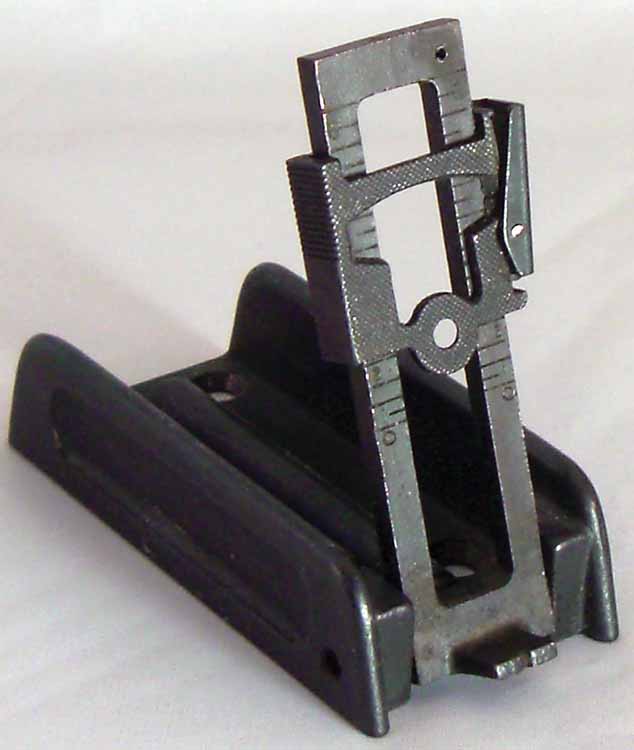
- Original Lyman sight assemblies
- Lyman bases with Enfield Leaf assemblies
- WH steel bases with Lyman leaf assemblies
- WH steel or light alloy bases with Enfield leaf assemblies
- WH steel or light alloy bases with WH leaf assemblies
Rocker Pivot (fire control lever) and Safety: These are commonly found WH parts. Careful examination will show a casting line down the middle. Most have a purplish hue. Functioning problems can occur if the pivot and safety move up and down while the Thompson is being fired. These parts should be replaced with original GI parts.
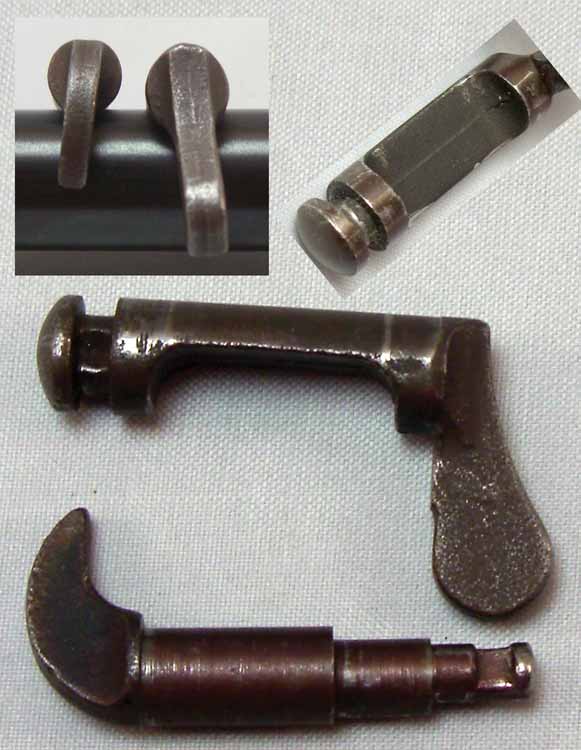
Sear, Sear lever and Trip: These are commonly found WH parts and can be a source of many functioning problems. Most have a purplish hue. These WH parts should be replaced with original GI parts.
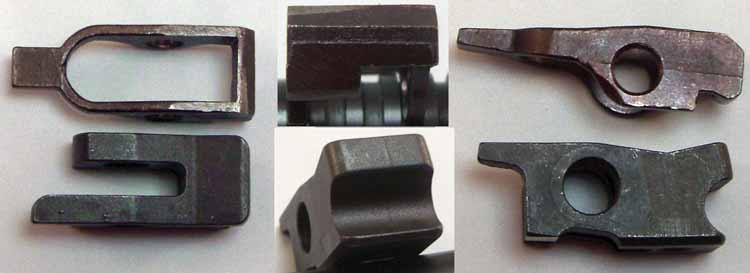

Vertical fore grip & pistol grip: While WH wood is not known for its beauty, it is very serviceable and only replaced for cosmetic reasons – or if a change in the grip mount dictates a different size fore grip. Butt stocks and horizontal fore grips are normally new or refinished GI production. Vertical fore grips are AOC production and known for their flat or slab sides. The pistol grips can either be new or refinished GI or AOC slab side production. When the 3/4 inch grip mount was introduced, the GI horizontal fore grips were re-inletted for the wider part. There is a great deal of variation in the wood found on WH Thompson’s during the 11 year production run.
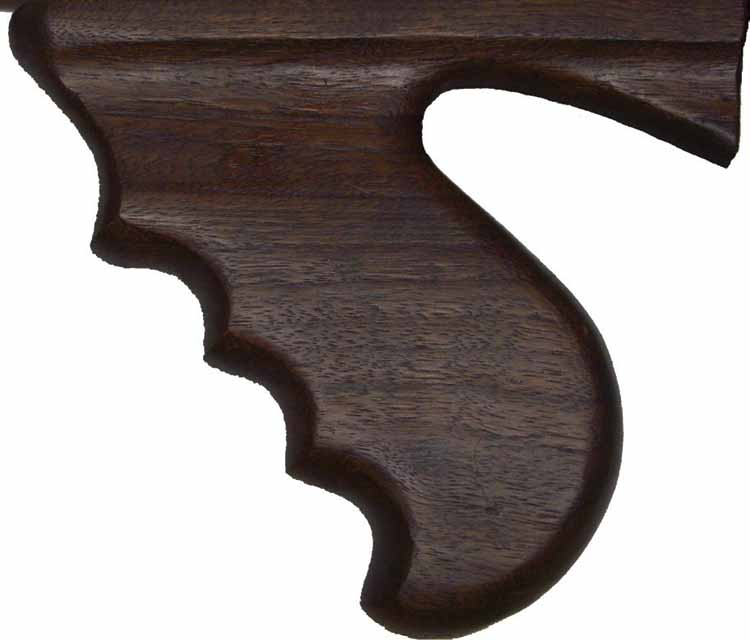
Epilogue
When compared to a Thompson manufactured to original ordnance or GI specifications, most everything about the WH Thompson can be problematic. However, they do run with some work and replacement of most of the WH parts. When WH Thompsons were in production, the vast quantities of original Thompson parts kits as found on the market today were not available.
Mr. Trast said if complete Thompson parts kits had been readily available from 1975 to 1986, it is quite likely AOC would have only manufactured the receiver and vertical fore grip. West Hurley’s are generally an entry level Thompson because of the lower price. Is it possible to take a WH Thompson and have it completely overhauled, refurbished and brought into proper specifications? Yes. And the end product will run perfectly and look just about as good as anything that came out of Hartford, Connecticut in the early 1920s.
(Author’s note: The story of West Hurley Thompson parts is a work in progress. This is the first attempt at trying to catalog all the different Thompson submachine gun parts manufactured and used by AOC in West Hurley, New York. The author encourages anyone who has seen, owns or knows about any different parts or part variations to contact him via Small Arms Review. Additional information may be compiled into an updated story in the future in an effort to make all of us more knowledgeable with the West Hurley Thompsons. This story would not have been possible without the support of all the great members of www.MachineGunBoards.com, many of whom are WH owners that replaced most of the parts you see pictured in this story.)
This article first appeared in Small Arms Review V15N2 (November 2011) |