By George E. Kontis, PE
It was spring of 1942 and the war was going badly for Allied forces. In March, American, British and Dutch troops surrendered Java to the Japanese. Just one month later the Japanese would capture Bataan in the Philippines and send 75,000 men on a 65 mile death march with only 54,000 to survive. There was no good news coming from the German front. The Germans captured the Greek island of Crete in an impressive vertical envelopment completing their occupation of most of Europe. In each newly conquered country, the Germans started rounding up Jews and began sending them to concentration camps.
Americans were enlisting in record numbers. War refugees from Europe, Africa, and Asia were anxious to join in the fight, and were looking to the Americans to supply them with rifles and equipment. The Government facility at Springfield Armory and privately owned Winchester were producing rifles in record numbers, yet they could not produce them fast enough.
The big bottleneck in rifle production was manufacturing the barrel and of this process cutting the four groove rifling was the largest time consuming element. Running at full speed, the rifling operation alone required between 10 and 15 minutes per barrel. On existing equipment, there wasnโt any way to speed things up.
In those years, there was only one way to manufacture an accurate rifle barrel: a hole was drilled in the barrel blank and then reamed to the exact dimension of the bore. Afterwards each groove was individually and painstakingly cut on a very special rifling machine. In a high volume production environment, rifling only 6 barrels an hour equated to an eternity.
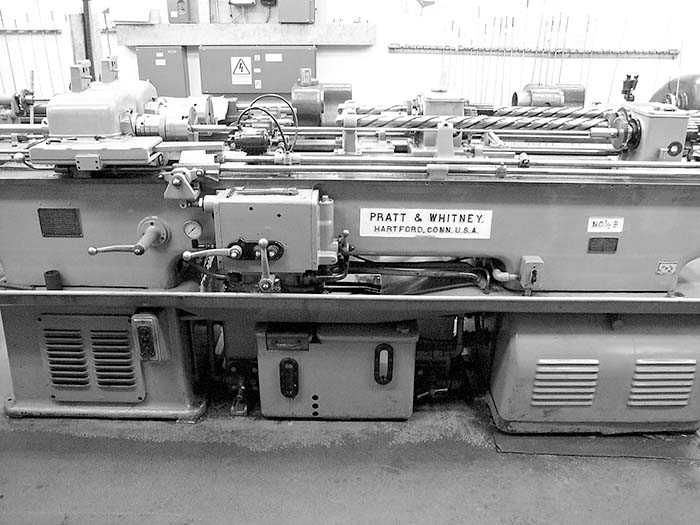
Itโs not that the best, state of the art equipment wasnโt available. Most of the rifling equipment in use at that time were top notch machines, manufactured by Pratt & Whitney โ today a name that is synonymous with high-quality jet engines. There werenโt enough machines and there wasnโt enough time, which always led to the same conclusion: not enough gun barrels to keep up with the production of other rifle components.
As always, the firearms industry worked hand-in-hand with the U.S. Government, making available their finest engineers to support any effort to improve weapons or produce them faster. In the spring of 1942, one idea that surfaced was to eliminate cutting two of the grooves in the barrel. If this could produce an acceptable barrel, the time to cut the rifling would be reduced to almost half. The Industrial Engineers at Remingtonโs Ilion, New York facility and the Ordnance Department from Remingtonโs research division at Bridgeport, Connecticut stood ready to answer the Governmentโs question: would a two groove rifle barrel be as good as the current four-groove barrel?
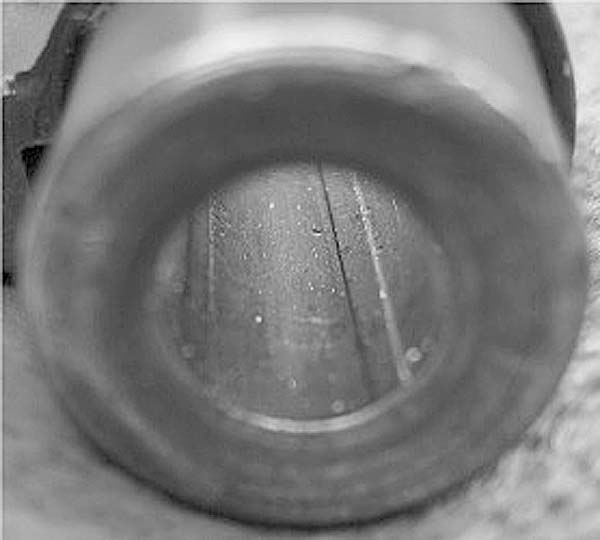
Cutting two groove barrels wasnโt necessarily a new concept. Since the mid-1800s, the British had been using two groove rifle barrels on their percussion rifles. But this was the mid-1900s and there was a more strict demand for accuracy from the military, not to mention smokeless powder and spitzer bullet forms. Before any rifles could be shipped, a U.S. Government inspector would be on hand to check each production lot, inspecting parts and checking records to assure that each one met specification. The performance standard required every rifle be tested for accuracy and that at 100 yards five shots must fall within a three-inch circle. Failure to meet this โextreme spreadโ requirement was cause for rejection.
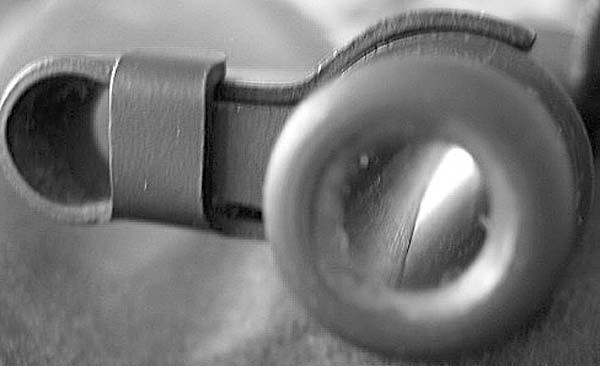
The state of the art rifling machine of that era was the Pratt & Whiney 1/2 B, available in two different models, one capable of producing 30-inch long barrels and the other for barrels up to 50 inches. Two other models of the larger 1 B could produce barrels up to 74 and 98 inches. These Pratt & Whitney 1/2 B and 1 B rifling machines were high precision , well designed machines, each having two spindles that could operate independently of each other. This meant that two different gun barrels could be made on the same machine at the same time.
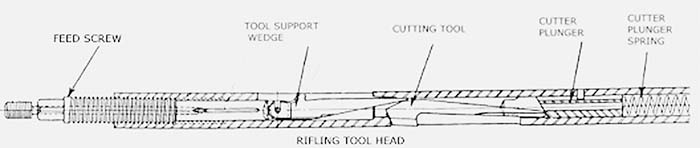
The rifling operation on the P&W is simple, and is essentially the same process that has been used for centuries. The barrel is held stationary while a rifling rod is pulled through the bore, turning as it travels to give the required twist. Protruding from the rifling rod is a cutting tool set to a fixed depth in order to cut one groove on each feed stroke. At the end of the feed stroke, the pressure of the cutter plunger spring on the cutter plunger forces the cutting tool back into the rifling tool head so it no longer protrudes. This allows the rifling rod to make the return stroke without marring the bore or cutting additional material. After one groove is cut and the rifling rod has returned, the barrel is indexed 90ยฐ for cutting the next groove. This process is repeated until all four grooves are cut to the same depth.
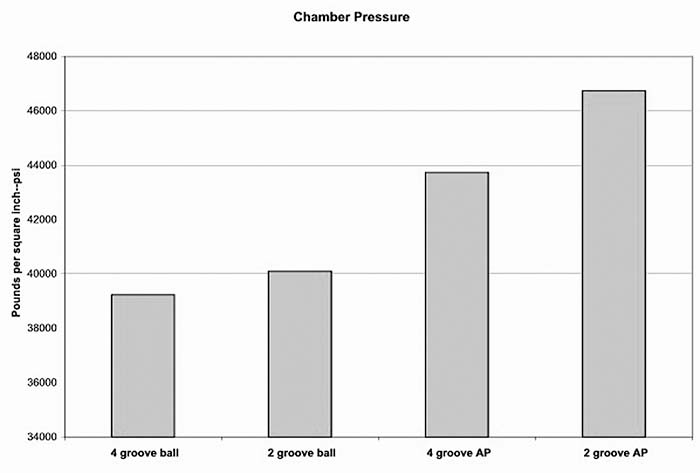

Next in the process is the deepening of the cut. In this stage, the tool support wedge forces the cutting tool to increase its depth of cut. The feed screw, having been previously adjusted to control the depth of cut, advances automatically to the next cutting depth increment. Now the P&W is ready to make another series of cuts. The process repeats making the grooves progressively deeper until all four grooves have been cut to the required depth.
Rifling Tool Head for P&W 1/2 B Rifling Machine
The maximum cutting stroke speed for the 1/2 B is 50 feet per minute and the return stroke maximum is 65 feet per minute. To keep the cutting tool and barrel cool, oil is pumped through the rifling rod and into the rifling head. Keeping the cutter free of chips from the material removed is important. The P&W 1/2 B takes this into account before making a new cutting stroke. A small motorized brush attachment cleans the cutting tool, removing the chips of cut away barrel material. The M1903 barrel drawing specifies a groove depth of .004 inches, or just about the thickness of a normal sheet of notebook paper. With all this speed and sophistication, cutting four grooves, each one only .004 inches in depth doesnโt seem like it would take any time at all, but that wasnโt the case.
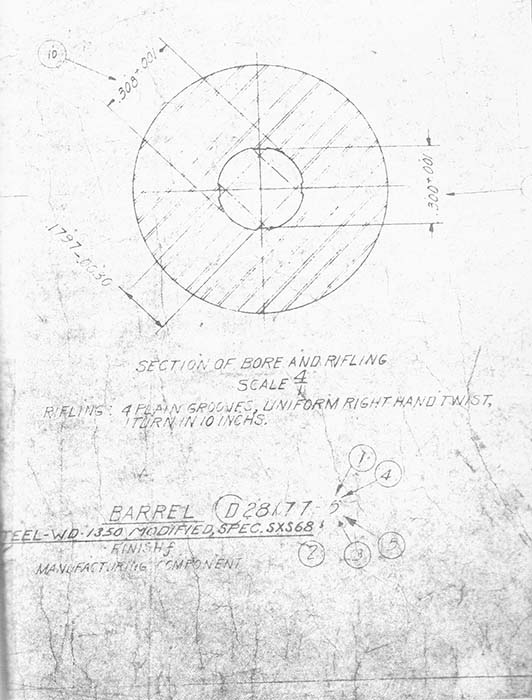
In order to run the P&W efficiently, the deepest single cut that can be made on a barrel of .30 caliber is only .0001 inches. Why? Simply because making a deeper cut creates a larger chip that can potentially clog the cutting surface resulting in a rough surface finish or a broken cutter. This limitation means that cutting a single groove to the specified depth of .004 inches requires 40 complete strokes. Just to make a single 4-groove barrel took 160 cutting strokes and 160 return strokes. In the spring of 1942, there was a lot of incentive in reducing the number of grooves to two.
Springfield Rifle Bore
Dimensions Ref:
RDR-42-12 Remington Arms
Company Report 1942
Remington engineers worried about the potential negative effects on this proposed change. There would no longer be four small lands in the barrel, all four totaling to about 0.2 inches in width that would dig into the projectile jacket to impart spin to the bullet. Now there were two huge ones, each one almost 0.3 inches wide. Would these two wide lands create so much additional bore friction that the projectile would be significantly slowed? Nobody knew for sure. Lower velocity and increased pressure were a concern.
Firearm experts knows that after primer ignition, any delay in getting that projectile moving causes the chamber pressure to rise quickly โ sometimes to dangerous levels. Would the wider lands make a serious increase in chamber pressure? How much additional pressure could be expected? Would the 1350 barrel material be able to withstand the amount of increased pressure?
Accuracy and barrel life were also a consideration. Would the rifle be as accurate with two grooves as it was with four? It would be counter productive to find out the two groove barrel would meet all the performance requirements up front and later learn that barrel life was so greatly reduced that the new barrel would need to be replaced sooner. Again, extensive testing would be required to find the answers to all these questions. Through their years of experience, the Remington engineers knew there was something else to be considered. They knew that if it runs on gunpowder, they could expect the unexpected.
On March 1, 1942, the Remington Arms Company of Ilion, NY was awarded a contract to investigate the two groove barrel. The study was to be a joint effort of the Ilion Industrial Engineers of the Ilion Development section, Remingtonโs Research Division in Bridgeport, CT and the Armyโs Ordnance Department. In their test plan, the Remington engineers proposed there โ barreling of twenty seven Spring field โ03 rifles with the two groove barrel to be used in the test.
Manufacturing a two groove barrel at the Remington facility was accomplished by indexing the barrel by hand, bypassing the automatic indexer so that two grooves and not four would be cut. If the testing turned out to be successful, it became immediately apparent there would need to be a modification of the indexing mechanism for volume production should the two groove barrel be adopted.
The accuracy test was performed at 100, 200, and 600 yards. The 100 yard test was conducted indoors. Each rifle was hand held using a muzzle and elbow rest. Remingtonโs Mr. R.A.A. Hentschel described the test res ults : โTwenty-seven guns have been built with two groove rifling. All have passed the Government inspection standard for accuracy at 100 yards. This standard calls for five shots to be within, or cut the edge of a three inch circle. No difference in accuracy was noted between these guns and regular production.โ
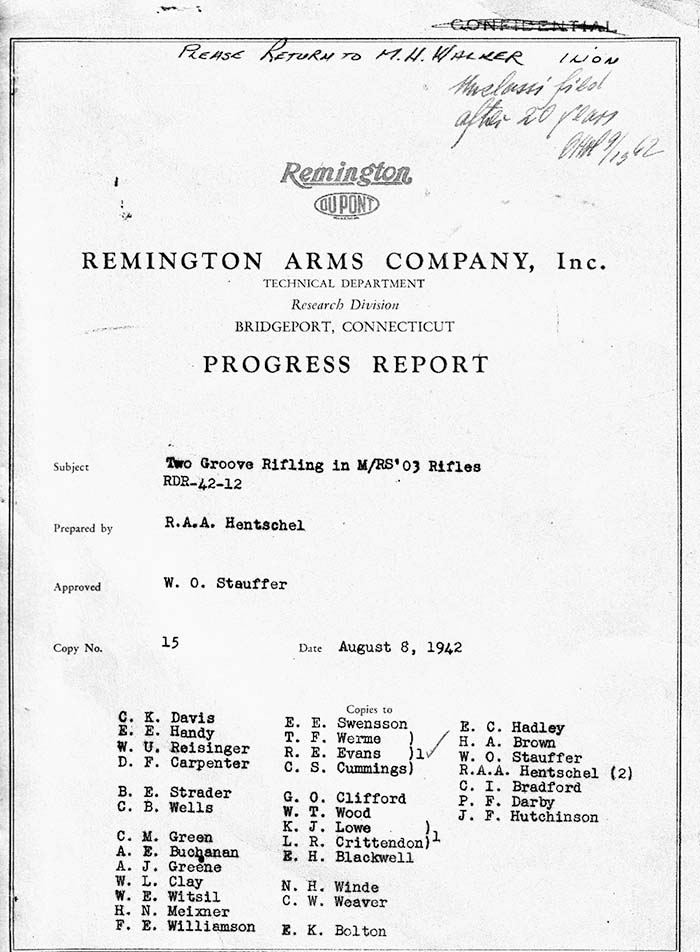
Following those encouraging results, Remington proceeded with the 200 and 600 yard testing. Two of the two groove test rifles were fired along with s/n 1283325, a standard 4-groove barrel used as a control sample for comparison. Again, the rifles were hand held, shooting from the prone position with a rest at the elbow and muzzle. As a baseline, four groups were fired with each rifle at 100 yards with the average group size indicated in the included table.
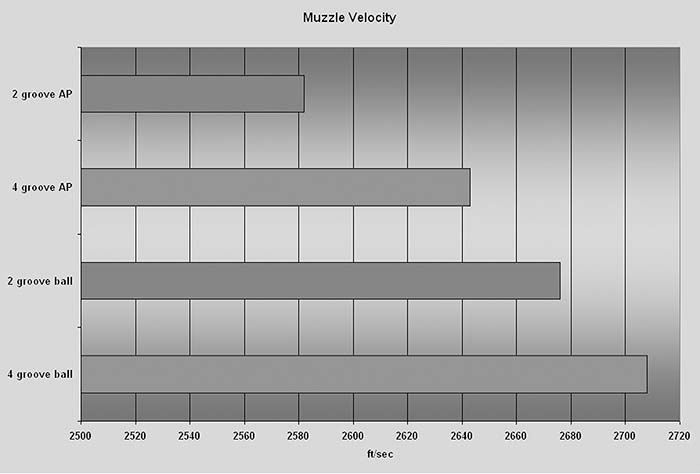
The two groove barrel was performing very well next to the four groove standard. Maybe the endurance test would give some indication why up to this point the service rifle barrels were designed to have four grooves in stead of two. The weapon selected for the endurance testing was Springfield , s/n 3030571. The endurance schedule required the firing of 16,000 rounds with three 5 round groups fired for accuracy after each 1,000 rounds.
The extreme spread was averaged at each 1,000 round interval. Other than an occasional foray slightly outside the 3 inch circle, the results were considered exceptional.
The results so far looked great with only a few tests remaining. Accuracy requirements were equal to or better than the four groove barrel on new guns and the endurance gun. Barrel life indications were also good. The bore of the rifle with 16,000 rounds was measured using sulfur casts. Although this barrel was badly fouled and significant heat checking evident at the breech, there was no measurable wear.
Two tests were left that still might keep the two groove barrels out of military service: pressure and velocity. Pressure testing was performed using the copper crusher method. It was the latest technology in those days but not highly accurate, giving not much more than a good approximation of the actual pressure developed.
Test results showed the expected: The pressure to force the projectile through those huge lands did increase the pressure with the two groove barrel, but fortunately not to a huge extent. The biggest concern was with the armor piercing ammunition that showed chamber pressure was unquestionably higher with this ammunition. Quick calculations showed the current barrel material could withstand the increase provided there was not extended firing with the AP ammunition.
Those two huge lands caused a small drop in muzzle velocity, but again the difference was not of great importance. With all testing complete, Remington concluded: โOn the basis of tests made to date, the two groove rifling equals the standard four groove rifling in performance. Tests show an increase in pressure from 3,000 to 4,000 pounds when using armor piercing ammunition in the two groove barrel. Since armor piercing ammunition is seldom used in the Springfield rifle, this latter result is not particularly significant.โ
On 22 October, 1942 the Ordnance committee met to review the results of the Aberdeen Proving Grounds testing. No one could argue with the performance of the two groove barrel. The recommendation for the two groove barrel was sent to the Ordnance Department for final approval.
When the approval was received, the following rifles were designated to receive the new barrel.
- U.S. Rifle Caliber .30 M1
- U.S. Rifle, Caliber .30 M1903A1
- U.S. Rifle, Caliber .30 M1903A3
- U.S. Rifle, Caliber .30 M1917
The Remington engineers described their testing and disclosed their findings in a concise report, No. RDR42-12. Upon completion, the report was classified โConfidentialโ to keep these results from reaching the enemy. Twenty years after the report was written, the security officer in charge downgraded each copy to โUnclassifiedโ by scratching out the โConfidentialโ stamp and initialing below it.
Just over 300 Pratt & Whitney barrel machines 1 Bโs and 1/2 Bโs were produced, preferred for volume production over the older Pratt & Whitney sine bar model. Many of the 1B and 1/2 B models are still in use today. Most remained in the U.S. while some were sent to Australia and other countries โ including Border Barrels Ltd. in Scotland.
Rifle barrels produced today use a variety of techniques to form the grooves, most being much faster than the single point cut method used by the Pratt & Whitney. But unquestionably the most accurate way to make a barrel is with a single point cut. The P&W 1/2 B is the preferred machine tool for this operation from the time it was introduced up till now. It is for this reason that the Pratt & Whitney 1/2 B and other models are currently used in the production of todayโs competition and military sniper rifles.
The M1 and Springfield rifles with two groove rifling are scattered around the country and the world. Their accuracy, reliability, and durability is enjoyed by shooters everywhere. However, few people recognize the major impact on the war effort that resulted from this minor configuration change to the rifling โ a change that made the two groove barrel one of the unsung heroes of World War II.
This article first appeared in Small Arms Review V11N3 (December 2007) |