By Frank Iannamico
Just about every military small arms enthusiast is familiar with the U.S. M3 and M3A1 submachine guns, better known by the nickname bestowed upon them by GIs during World War II, the “grease gun.”
The .45 caliber M3 was conceived as a less expensive alternative to the Thompson submachine gun, which at the time the U.S. entered World War II in 1941, the Thompson design was 20 years old. The M3 was patterned after the British Sten and German MP40 sub-machine guns, both constructed from sheet metal stampings—a far cry from the Thompson forged and machined receiver and parts. In addition to being less expensive, weapons stamped from sheet metal can be produced faster, an essential advantage in wartime.
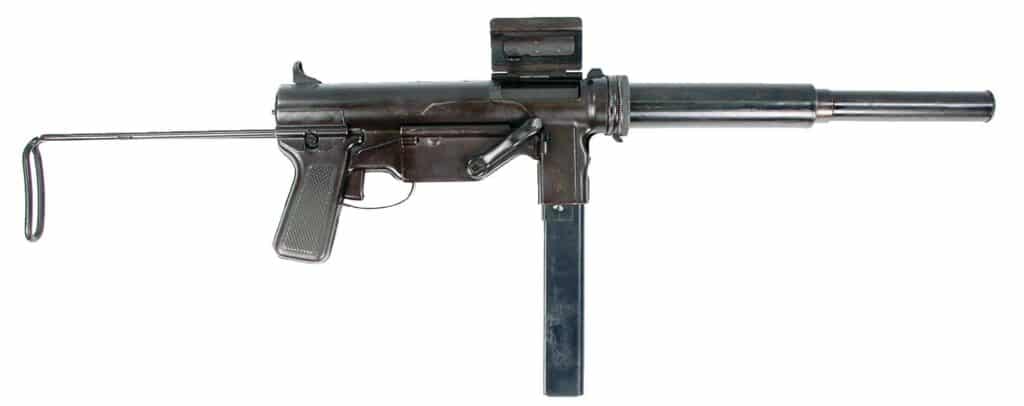
Mk II
The Mk II was the most prolific model of the British Sten. The receiver was fabricated from pre-formed metal tubing. The German MP40 receiver was made from a flat piece of sheet metal that was rolled into a tube. The receiver of the U.S. M3 submachine gun was far more complicated to produce. The M3 receiver and most of its other parts were stamped from cold rolled sheet metal, requiring a factory equipped with a battery of large hydraulic stamping presses. The receiver was made of two separate stamped pieces that were then welded together. When production began, it was discovered that it was difficult to accurately weld the two receiver halves together. In addition, the heat from the gas welding process was warping the thin metal, and it took some time to perfect the process. During production, the time allotted for welding the two receiver halves together was 12.11 minutes. The M3 design had an advantage over other submachine guns of the day, with its ingenious guide rod-bolt system. The bolt of the M3 rode on two guide rods, never touching the inside of the receiver. The unique system made the M3 impervious from malfunctions caused by mud, sand or other debris, making it one of the few weapons to successfully pass all the Ordnance Department’s requirements.
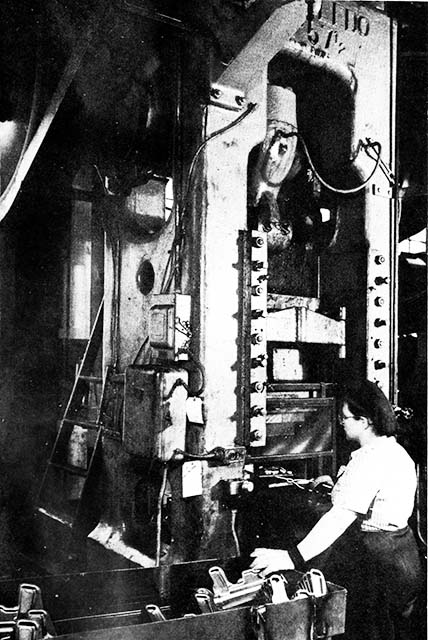
The Guide Lamp Division of General Motors Corporation
The Guide Lamp production plant was located in Anderson, Indiana, and in 1943 it had over half a million square feet of production floor space in 18 separate buildings. The Guide Lamp Division of the General Motors Corporation was a peacetime manufacturer of automobile lamps, headlight buckets, hub-caps and bumper guards. Guide Lamp had a lot of expertise and experience in sheet metal stampings and was an excellent choice for the manufacturing of the M3. By May 1943, the first M3 submachine guns were finally rolling off the assembly lines at Guide. Production had fallen far behind projected figures by the unforeseen welding problems encountered with the receiver. However, by June 1944, 1,000 M3s were being manufactured every 24 hours.
The Guide Lamp contract price for the M3 was $17.92 per unit less the bolt assembly. The initial price was later amended to $18.36 per unit to cover the cost of minor production changes and the packing and shipping of the completed units. The M3 bolt assembly manufacture was subcontracted to the Buffalo Arms Company at a cost of $2.58 per piece.
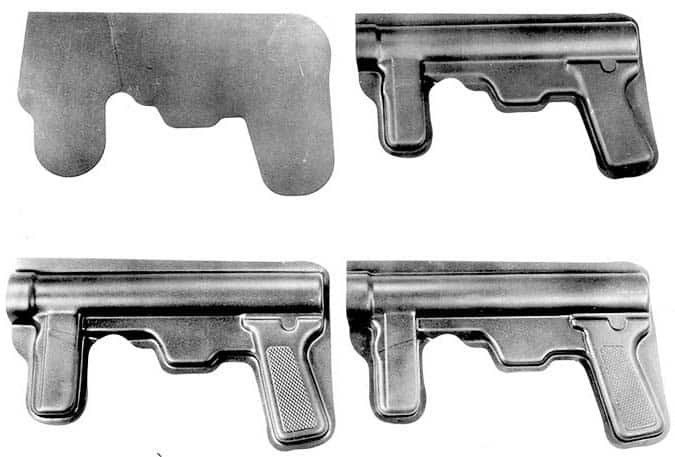
The following quote is from the second summary of the tests at Aberdeen Proving Ground upon adoption of the M3 Submachine Gun. “Although it would be dangerous to state that further improvements and developments are unlikely, the ultimate has been reached in this type of weapon for the time being and production may begin without fear of immediate change.”
The above statement was premature, because as the M3 was pressed into service, problems began to arise. The M3 was not yet “GI Proof.”
One of the primary problems was with the cocking handle and its internal parts. A second problem was magazines were dropping out of the weapon, by the accidental pressing of the exposed magazine catch. Deterioration of the bolt face and barrel chamber was found to be caused by soldiers using the overly long wire butt stock as a cleaning rod. These problems and a few others would be addressed in an upgrade of the weapon.
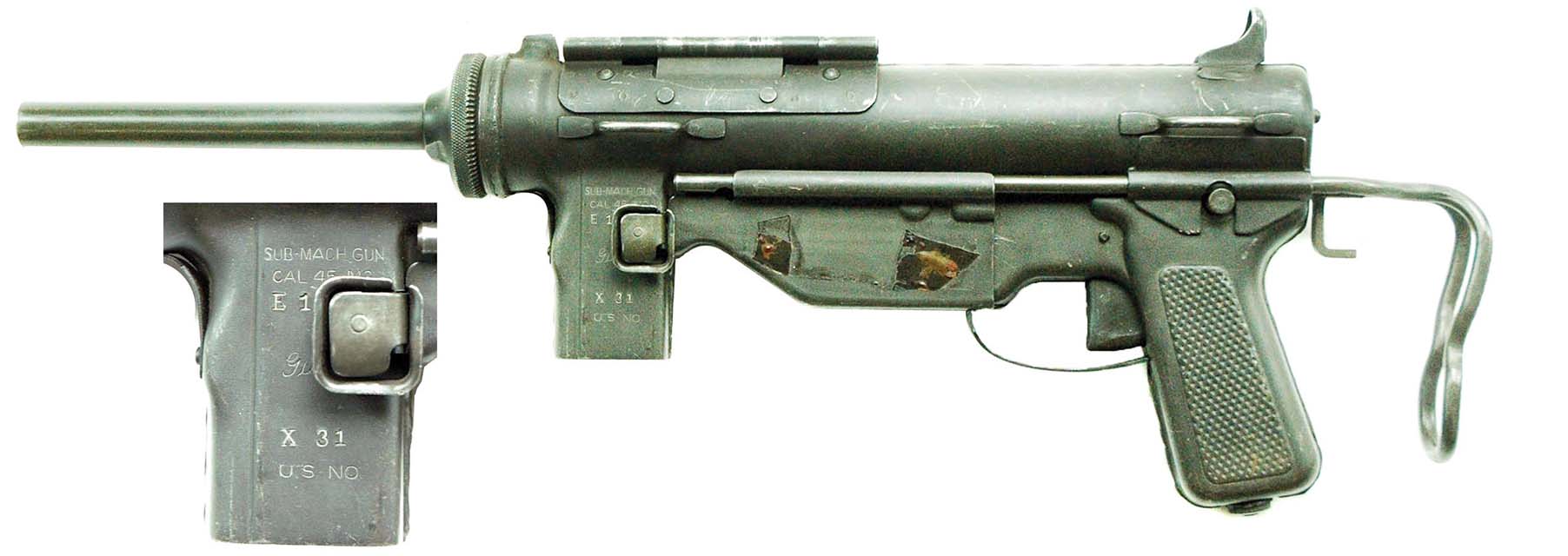
M3E1 Submachine Guns
The M3 was thought to be as simple and reliable as possible; however; the Ordnance Department felt that the weapon could be simplified even further. Six pilot models were built, incorporating several recommended changes that were designated as the M3E1 submachine gun. Two of the completed weapons were sent to the Infantry Board at Fort Benning, Georgia, for informal testing, and two were demonstrated at Aberdeen Proving Ground. Since none of the changes incorporated in the M3E1 design had any adverse effect upon the reliability of the weapons’ functioning, no formal testing was undertaken by the Ordnance Department. Sufficient firing of the new weapons was conducted to satisfy concerned personnel as to the desirability of the changes incorporated. Some of the firing demonstrations were witnessed by representatives of the Army Ground Forces and by the director of the Infantry Board who expressed his approval of the M3E1.
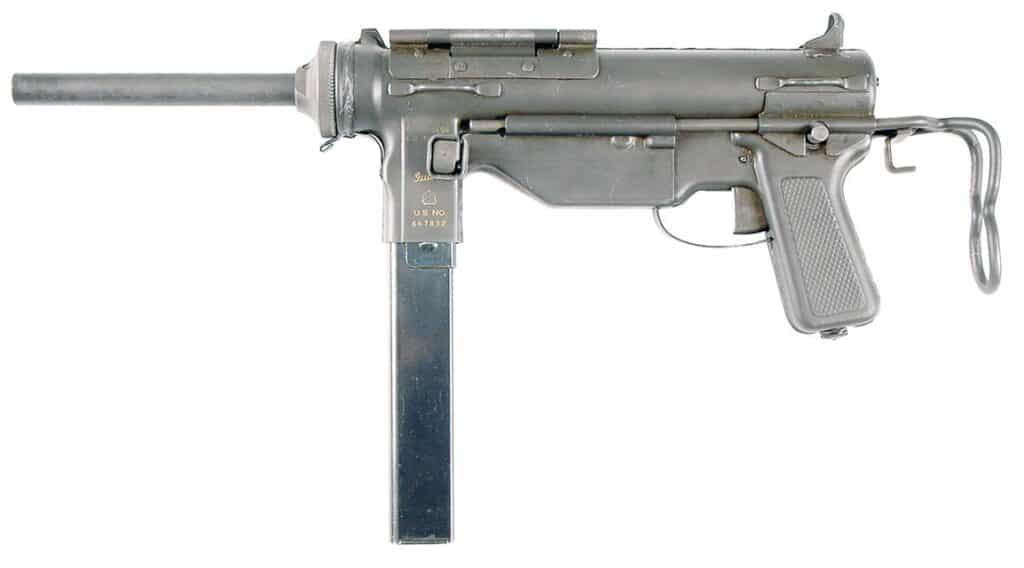
The U.S. M3A1 Submachine Gun
The experimental M3E1 was recommended for adoption on November 2, 1944, by OCM 25593. On December 21, 1944, the M3E1 Sub-machine Gun was approved and officially adopted as: Submachine Gun, Caliber .45 M3A1, thus reclassifying the M3 as Limited Standard.
M3A1 Changes
- Ejection port increased in size
- Cocking handle assembly eliminated, fin-ger hole added to bolt for cocking
- Disassembly groove the length of the bolt
- Stronger cover spring
- Larger oil can located inside the grip
- Stop plate and magazine loader added to the stock
- Guard for the magazine catch
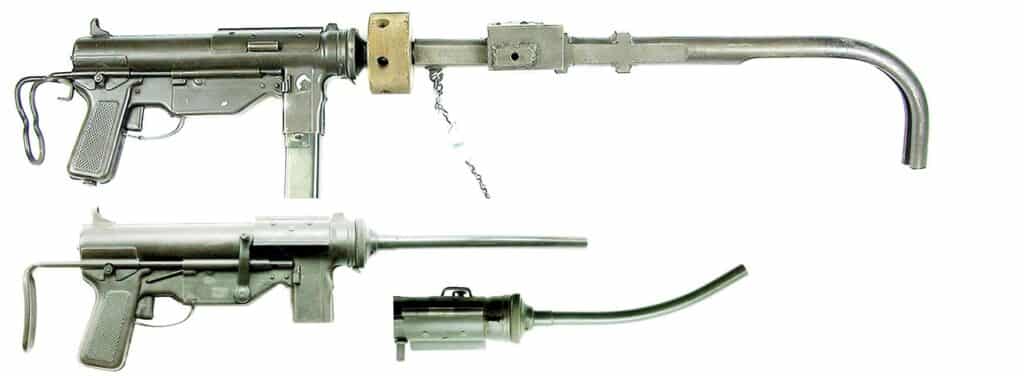
9mm M3 and M3A1 Submachine Guns
Among the original specifications desired in the T-20 (M3) submachine gun was a kit to change the caliber to 9mm. The conversion kits were originally planned for allied use in the European Theater; none were ever issued to U.S. troops. The 9mm cartridge was common in Europe during World War II. It was the standard pistol and submachine gun cartridge of both the British and the Germans. Ammunition would be easier to obtain by resistance groups that the U.S. Office of Strategic Services (OSS) was planning to supply with the M3. The conversion kits could also make the M3 readily adaptable for use by the British especially when using a Sten magazine. The conversion kits consisted of a Bolt assembly C153425, Barrel Assembly C153435 and magazine Adapter C153430. In December 1943, the Ordnance Committee recommended that 500 of the 9mm conversion kits for the M3 be obtained as a limited procurement item. In February 1944, procurement was authorized. The parts were manufactured by the Rock Island Arsenal and Saginaw Steering Gear. The 32-round Sten magazines would be obtained from the British government.
In addition to M3 and M3A1 conversion kits, there were a small number of grease guns produced that were marked 9mm, in place of .45 caliber, on their magazine housings. Those observed were the same configuration as the .45 caliber model but fitted with Sten magazine adapters, 9mm bolts and barrels.
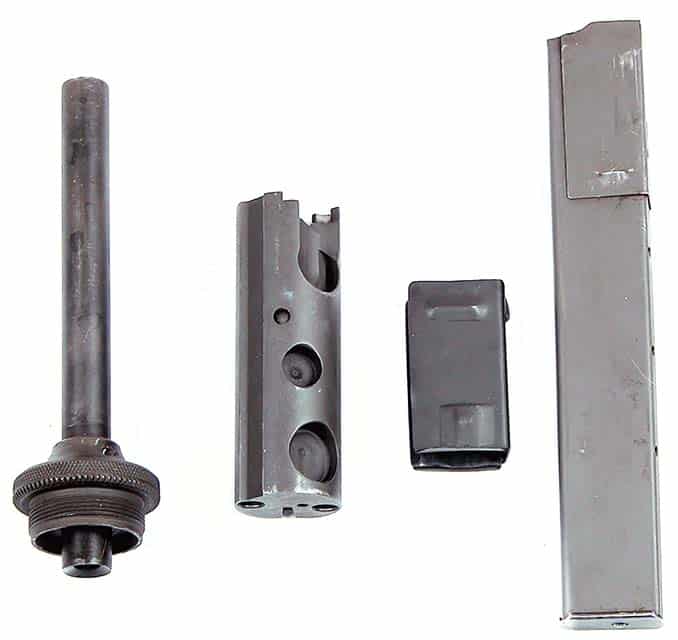
Curved Barrels
Due to its compact size, the M3 submachine gun was ideal for issue as a defensive weapon for armored vehicle crews. The weapons could be easily stored in the cramped space inside a tank. Tanks in the field were usually accompanied by infantry troops for protection from the enemy. Without infantry protection, the enemy could climb onto the tanks and drop grenades or spray machine gun fire into the inside of the hull, killing the trapped crews. To avert such situations, the Ordnance Department engineers came up with several curved barrel designs for the M3. The idea was the crew could extend the curved barrel out of the tank and spray enemy soldiers on their vehicle with fire, without exposing themselves. The issue of the curved barrels was limited. The Germans had also experimented with curved barrels for a number of their small arms.
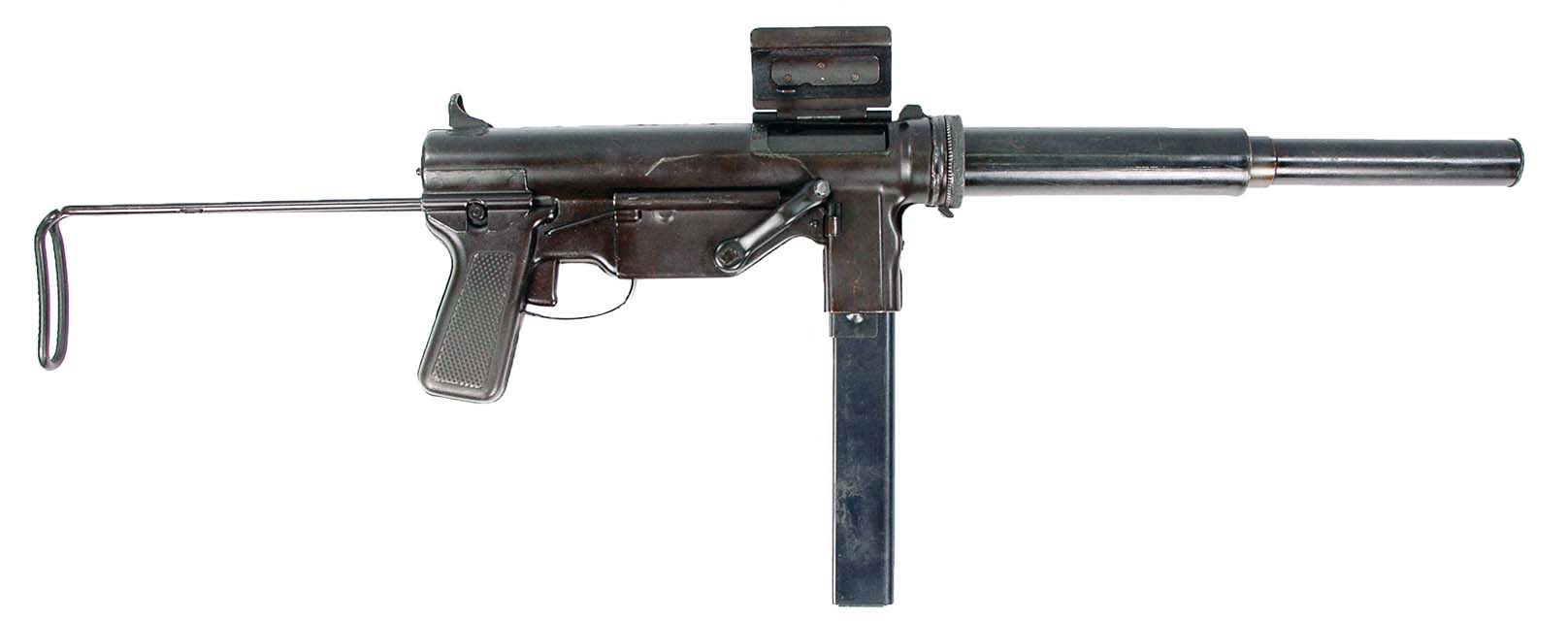
The .30 Caliber T29 Submachine Gun
The German Sturmgewehr mid-range assault rifle was an entirely new concept in World War II. The weapon had the full-au-tomatic capability of the submachine gun but fired a more potent cartridge, giving the enemy far more range. After U.S. troops began to encounter the Sturmgewehr in the field, requests were made for a similar weapon. The most expedient method to get such a weapon to the troops was to modify an existing model. The M3A1 was chosen as the best candidate. The concept was given considerable study by the design section of the Guide Lamp Division of the General Motors Corporation, which was manufacturing the M3A1 submachine gun. There were three M3A1 submachine guns made, designated as the T29, chambered for the .30 caliber carbine round. The weapon was basically an M3A1 with a larger magazine well to accept carbine magazines, a modified bolt, a spring-loaded case ejector and a 14-inch long barrel. Initial testing revealed more development would be required. Development efforts of the T29 ceased with the adoption of the select-fire caliber .30 M2 carbine.
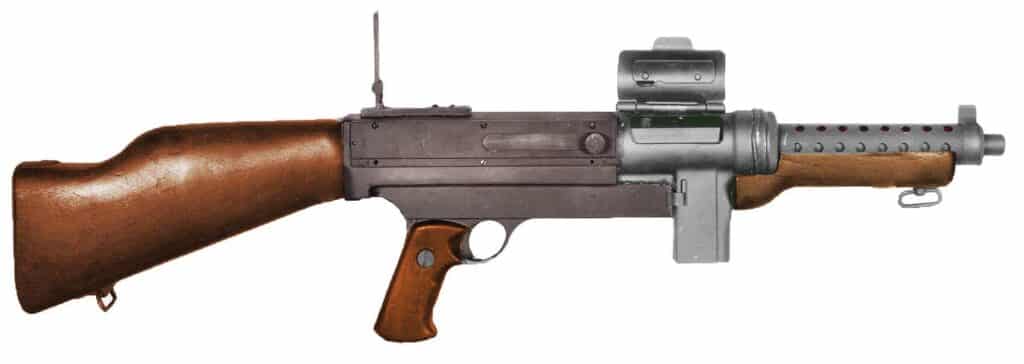
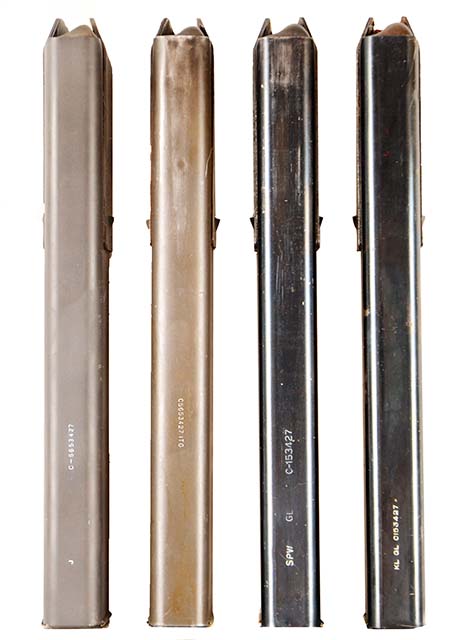
The Suppressed M3
The U.S. Ordnance department developed a special interest in suppressed or silenced weapons after learning of the British Special Operations Executive (also known as the SOE) commandos’ successful use of their silenced Sten Mark II S model. The weapon proved to be an invaluable asset for special operations where surprise and concealment were paramount to a successful mission. The SOE was the British counterpart of the United States’ OSS organization.
It was held that the U.S. M3 submachine gun would be ideally suited for adaptation of a suppressor because of its inherently subsonic .45 ACP cartridge.
The M3 suppressor research was conducted at the Infantry Center at Fort Benning, Georgia. There was an interest in supplying Army Rang-ers and other troops with a silenced weapon for special assignments. The earliest silencers were based on the Hiram Maxim baffle system. These proved to be heavy and cumbersome. None of the Fort Benning designs went past the prototype stage, and the project was canceled.
The Office of Strategic Services (OSS) was established in June 1942. The OSS organization was engaged in various types of covert and unconventional activities during World War II. The OSS had requested from the Army Ord-nance Department suppressed submachine guns for their special mission and operational needs. By late 1943, the OSS was directly supporting resistance groups in Europe and the South Pacific. The U.S. Ordnance Department contracted Bell Laboratories to develop a new suppressor for the M3 submachine gun. Guide Lamp was subcontracted to manufacture drilled barrels and special barrel nuts for the project. The High Standard Company was engaged to produce the components and assemble the unit. The contract called for 1,000 suppressor units to be built. The barrels made by Guide were identical to the standard production barrels except the face of the barrel nut was machined to form a seat for the expansion chamber. The barrel was also a standard item modified by drilling 48 one-quarter-inch diameter holes, arranged in a straight-line pattern of 12 on each quarter section of the length of the barrel. The muzzle end of the barrel was threaded for a length of one-half of an inch to enable the front end of the suppressor can to screw onto it.
The suppressor itself consisted of two sleeves. The rear sleeve is the expansion chamber. It is 7.5 inches long and 1.5 inches in diameter. The front sleeve is the silencer housing and is 7 inches long and 1.125 inches in diameter. The expansion chamber is connected to the silencer housing by a metal connector. External threads on the front portion of the unit were screwed into the connector. The connector was screwed on the muzzle of the barrel and holds the rear part of the suppressor in place by seating on the modified barrel nut. The rear expansion chamber contained a coil of stainless steel mesh. The front section of the suppressor housings contained approximately 230 steel mesh discs. An end cap secured the discs in place. As the bullet travels down the barrel some of the propellant gases escape through the 48 holes drilled into the sides of the barrel.
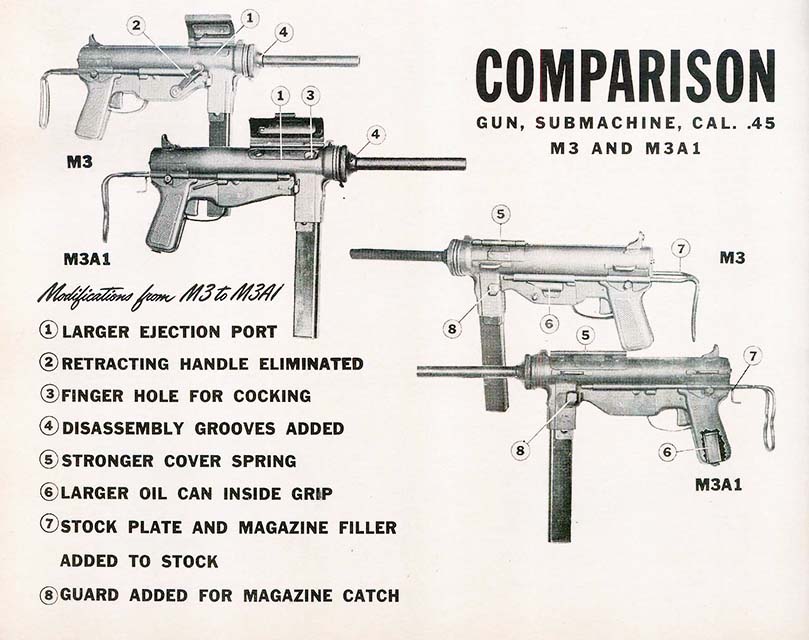
The total of submachine guns manufactured from 1943 to 1945 by Guide Lamp was 606,694 M3 models and 82,281 M3A1 models, for a combined total of 688,975 weapons. The entire World War II production of the M3 and the M3A1 would total only a little more than one-third of the Thompsons produced during the war.
During the Korean War, the Ithaca Gun Company was contracted through the Roch-ester, New York Ordnance District to fabricate 70,000 new M3A1 submachine guns. The manufacturing was authorized under contract number DA 19-058-ORD-7894. Preparation for the manufacturing would be assisted by the data package documented by Guide Lamp during its manufacture of the weapon.
Delays in getting production started resulted in the Ithaca M3A1s being manufactured in 1955–1956 after the war in Korea had ended. The contract was canceled after 33,227 guns were manufactured; primarily due to the Korean conflict ending and the anticipated adoption of the M14 rifle.
The Colonel Hamilton M3 Submachine Gun
Sometime in the post-World War II era, an experimental weapon was constructed by a Lt Colonel Hamilton while he was stationed in Panama. An obvious attempt was to modernize a M3 submachine gun. The front part of an M3 was welded to a steel frame with a removable side plate, secured with machine screws to remove the bolt assembly. Other upgrades include: a wooden buttstock, fore-grip and pistol grip, side cocking handle, adjustable flip-up rear sight and a perforated barrel jacket. The overall length is 30 inches, barrel length is 8-inches, and the weight is 11 pounds. The weapon was procured by the Rock Island Arsenal Museum in 1948 and is currently on display there.
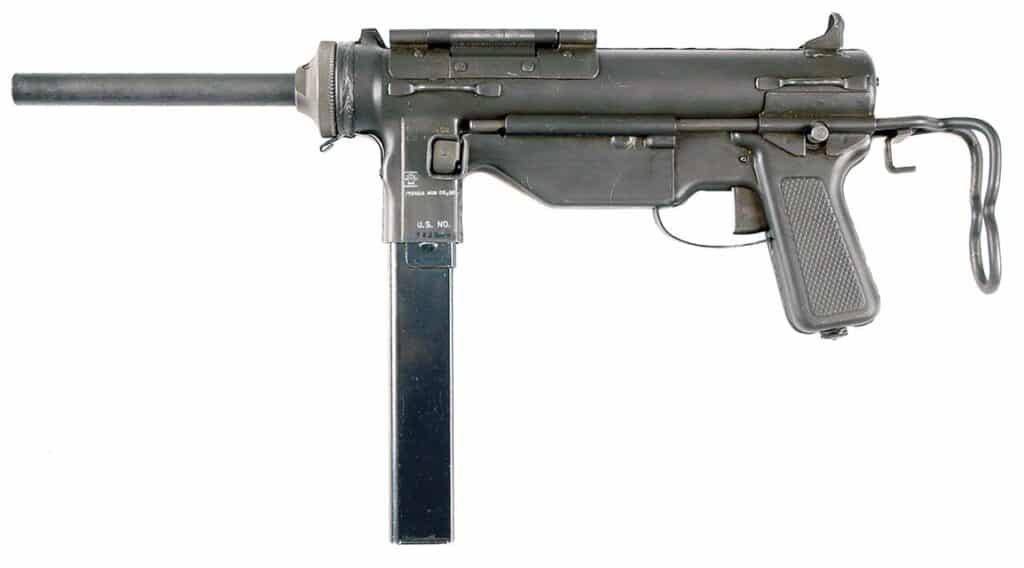
Rare M3A1 Magazines
During World War II, M3 magazines were made by Sparks-Withington (SPW) and Kesler Brass (KL). The magazines made by those companies are still common even today. During subsequent conflicts, in Korea and Vietnam, there were small production runs of magazines for the M3 and M3A1 submachine guns.
In addition to M3A1 submachine guns, Ithaca also made a small number of magazines for the M3A1, marked with a new drawing number C565427 and “ITG.”
Magazines were also produced during the Vietnam conflict by Jahn Manufacturing. These were marked with a letter “J” and drawing number C-565427. OKAY Industries purchased Jahn Manufacturing around 1970.
The Adoption of the U.S. M14 Rifle
Substitute Standard after the adoption of the M14 rifle, which (in theory) was replacing the M1 rifle, the carbine and the submachine gun. M3A1 submachine guns continued to be issued to Army Reserve armored units as late as 1999. Modern mid-range assault rifles like the M16 and M4 have rendered the military use of the submachine gun obsolete.
This article first appeared in Small Arms Review V23N6 (JUNE/JULY 2019) |