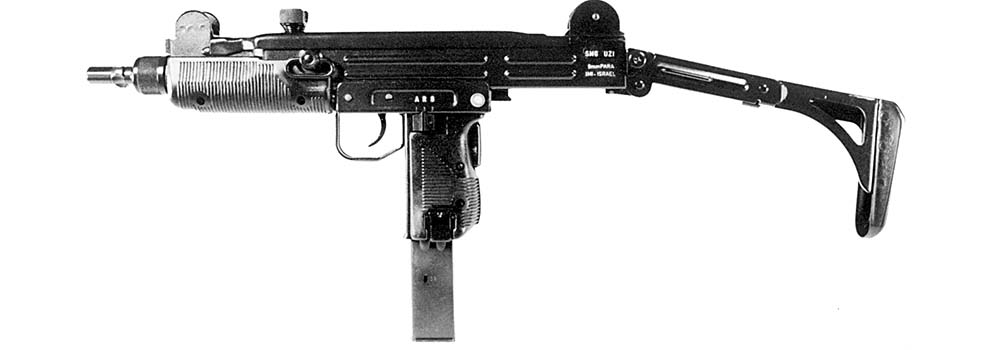
By William R. “Bob” Bishop
One of the most popular firearms to convert to full automatic is without any doubt the Uzi carbine. Simple, reliable, widespread parts availability and an excellent pedigree all come into this popularity. Having recently completed a tour in Bosnia courtesy of Uncle Sam, I had been in the unique position of storing my Beretta M9 9mm pistol and having access to an Uzi. This was my first real long-term examination of the Uzi and I liked what I saw. So much so, that upon my return to the US I wanted a full automatic Uzi for my own personal collection! This article will describe in detail the process I went through to select and convert a semi-auto Uzi into a “factory correct” full auto version. The final goal was to possess an Uzi submachine gun that was both cosmetically and mechanically perfect. In other words, it had to look beautiful and run even better. You be the judge whether I succeeded or not. Time to get to work!
Uzi Selection
Upon returning from Bosnia my wife decided her “reward” for enduring my nine-month absence would be a new kitchen. This meant the money to buy a relatively expensive registered receiver Uzi would not be available. I would have to buy a semiauto model and gradually convert it via the registered bolt route. Yes, this meant it would ultimately cost a little more but the benefit of doing it in bite-sized chunks was much easier on family relations. To do this incremental approach I divided the project into three steps: 1) selecting a base semi-auto Uzi; 2) external modifications; and, 3) internal modifications.
There are several different semi-auto Uzi’s which can be selected as the base weapon. As the Uzi is traditionally associated with Israeli Military Industries (IMI) I felt this was the best place to start. I knew that Group Industries and Norinco have sold semi-auto models in America, but it was just not the same as starting out with a real IMI model. IMI got the nod for supplying the Uzi. But which version?
Over the period 1980-89 IMI had imported two semi-auto Uzi models into America. One was the Model A and the other was the Model B. The Model A has several distinct differences versus the Model B when it comes to a full auto conversion effort. The Model A sights are the same as the SMG version and regulated for a 10.2” barrel. The Model B sights are different and designed for the 16” carbine barrel. Also, the Model A ejector is functionally the same as the SMG version. The Model B ejector is shorter and must be replaced with a taller one. This involves punching out the B ejector and riveting a new one of the proper height back into place. That was really all the differences between the A and B: sights and ejector. Yes, I know the Model B has a slightly different bolt than the A but this was going to be replaced with a registered bolt anyway.
Though the differences were minimal I decided on the Model A as it was visually a clone of the Uzi SMG when compared to the Model B. Contacting Kevin at Gulf State Firearms I purchased a 98% Model A. Now that the first part of this project was completed it was time to start step 2 – the external modifications.
External Modifications
The external modifications would allow me to start the conversion and still be able to shoot the Uzi in a semi-auto mode while I saved additional money. These mods included:
Installing an A-R-S full auto grip frame Installing a full auto ratcheting top cover assembly Modify the barrel nut to clear a three-lug barrel (optional) Totally refinish/restamp the Uzi to look exactly like a factory SMG
NOTE: As this article was being submitted, the best story you will ever read on all the variances of Uzi parts/conversions was published in SAR. Tom Hoel is clearly a master at Uzi’s and his literary work is absolutely required reading for anyone doing an Uzi conversion. Get a back copy of SAR and memorize his words. With his article as a reference, combined with this article on techniques and sequence, you will have a successful conversion. Thanks Tom!
Before doing anything I got a good manual (and Tom’s article!) which shows the complete takedown of an Uzi as the owner’s manual is woefully inadequate for this. Delta Press had an excellent one for sale and it cost less than $10. The “secret” on how to take apart the rear sight is worth this price alone! Get it and you will not be disappointed.
Next, I contacted Class Three Supply and ordered an IMI full auto grip frame. This is exactly what factory SMG’s use and has the correct “A-R-S” selector switch markings. Also ordered was the IMI ratcheting top cover assembly. While the semi-auto Uzi shoots from a closed bolt, the full auto fires from an open bolt. Without a ratcheting top cover assembly it is a potential safety hazard when charging a full auto Uzi as your hand could slip off the charging knob and let the bolt accidentally slam home. It will then fire unintentionally. This new top cover will prevent accidental misfires, as you must pull the charging handle fully rearward to clear the ratchet before it will release. It is worth every cent.
With the acquisition of these parts it was now time to send them out for some machine work. John Norrell, who is well known for his Ruger 10/22 and AR15 conversions, agreed to do it.
The full auto (FA) grip frame is exactly like the semi-auto (SA) frame except for two key differences – the FA split bushing (aka “push” or “axis” pin) hole is smaller and there is no selector switch blocking piece. For FA you do not want a blocking piece so it is a benefit this is absent. However, the split bushing holes are another story. Federal regulations prohibits certain modifications of the SA receiver for full auto so the grip frame must be changed. The 8mm holes in the FA grip frame must be enlarged to 9mm to mate with the SA receiver. John carefully drilled out the FA grip frame holes on a bench press to the necessary 9mm diameter. Being a perfectionist he then chamfered the new holes so the split bushing would easily slide through and lock in place.
Next came the step of restamping the receiver to match a factory SMG. Many enthusiasts do not know it, but John is one of the few people in the business who owns and knows how to properly use a carbide-tipped rotary engraving machine. He also had a post-May dealer sample Uzi at his shop and used it to provide an example of correct factory markings. First, he TIG welded over the “Semiautomatic” and “Model A” inscriptions and milled this area flush with the receiver. Then he stoned the area and rounded the edges to match the sheet metal bends. When finished it appeared exactly like the original sheet metal – absent the unwanted markings. At no time did the original serial number get touched per federal reg 18 USC 922(k).
After loading the correct font set into the engraver and making a few test cuts he skillfully engraved the new markings in. The “Model A” identification no longer existed and the receiver markings were now an exact duplicate of a factory SMG. The “SA” letters in front of the untouched serial number were the only indication it had started life as a semi-auto. Most impressive!
One final modification which I had John do was something which was not “factory” at all but would sure help me. I own Gemtech’s beautiful Raptor 9mm suppressor and use it on my MP5 and Colt CAR15 9mm. I also wanted to use it on my Uzi but needed a three-lug barrel. Uzi barrels can be easily “lugged” but then will not pass through the barrel nut as the diameter of the lugs are a bit too large. John reamed out the nut to clear the lugged barrel while leaving enough lip to properly retain it. Although this is not an IMI option it is something everyone owning a suppressor which mounts to barrel lugs should consider.
The next step was to send the Uzi out for proper refinishing. After extensive talks with Jim Gravitt of Pro-Tech Engineering I decided to have him parkerize all the parts in a rich gray-green zinc phospate. The IMI factory does it this way and after 40 years of production they must know what is right! Mine would be refinished the same way and as Jim learned his trade at Vollmer’s his skills were clearly up to the task.
Jim glass beaded the parts with a fine 55-mesh grit and then air hosed them off to remove any dust. After that he buffed out several small nicks, cleaned up screw heads and returned to “as new” condition all surfaces which would detract from an otherwise perfect finish. Then, he placed everything into the parkerizing tank and let the chemicals do their work. After removing them and neutralizing the chemicals he dried everything off and very thoroughly examined them for any imperfections. If they were not absolutely correct they went back for Round 2. If you want correct parkerizing then Jim is the man to do it.
When Jim returned everything to me I was ready for the final bit of “polishing the apple”. The IMI factory finish is a black paint which is not the most durable or beautiful. Indifferent overspray, uneven coverage and a general air of low quality has always bothered me. The answer is two words: Moly Resin. John Norrell custom mixes several different types of “moly”. One of them is the same shade of black that some notable manufacturers – such as H&K, FN and IMI – are using. I had previously sprayed several other firearms with moly and am totally convinced it is about as close to a perfect military finish as you can get. This Uzi was going to become a true gem.
I first cleaned everything with acetone and carefully masked off those sections which would remain parkerized. The parts were then warmed to 150F in that new oven. A tip: use a newspaper mask whenever possible as most tapes will leave an oily residue on the metal when heated. The parkerizing will then wick this oil about 1/16” onto the area to be sprayed. Moly will not easily stick to this oily area and you may have some slight flaking after limited use. An alternate method for smaller parts such as trigger pins is to warm them first and then quickly mask with 3M Post-it note stickers before spraying.
Using a Paasche Model H airbrush and air compressor at 30 psi it was an easy job to mask off and perfectly coat everything in several hours. As a rule of thumb, for every minute you spend spraying about 3-5 minutes will be spent in masking and preparation. Furthermore, no reducing agent is necessary for moly as you use it straight from the bottle. For this reason the “fine” spray tip which many times comes with the Paasche airbrush is more than adequate. Thermally curing the coated parts at 250F for two hours, followed by an oil quenching, completed the process. After wiping them off it was a beautiful sight which awaited me. Finally, I repainted the A-R-S selector and 100/200 meter rear sight markings with a white lacquer stick from Brownell’s. Clean the target area with acetone, rub the stick in, wipe off, and let cure for a few hours. Immaculate!
To complete the external phase I installed all the parts back into the receiver and FA grip frame. This was where the technical manual was really important, especially with the parts comprising the trigger mechanism. One point to bring out is the SA sear must be used. Do not buy a FA sear as it is too large to fit through the sear clearance holes in the SA receiver. Further, ATF will not allow the opening up of these holes for the FA sear as it is considered a receiver modification – and this Uzi would have a registered bolt not married to the receiver. No problem. The SA sear works perfectly fine and is robust enough to handle many thousands of cycles. Everything fell into place and my Uzi (other than the 16” barrel) looked exactly like an immaculate IMI factory full auto.
While waiting for the registered bolt transfer to clear there is one minor concession you must make to fire in semiautomatic mode. The ratcheting top cover assembly will not release during cocking due to the SA bolt/striker assembly being a bit too long for correct operation. To solve this simply remove the ratchet pawl and it will work fine; or, temporarily use your existing SA top cover.
Internal Modifications
The Uzi was now at the most critical part of the conversion and required these parts: Registered full auto bolt IMI SMG recoil spring/buffer assembly IMI SMG extractor and pin IMI SMG barrel (NOTE: do not get this until you have the registered bolt!) IMI three-detent selector level (optional: depends on Model A you have)
The registered bolt was a B-G Machine product via Tom Denall. I now understand that a very good C3 dealer named Edward Thomas Brady has taken over Tom’s supply and is the man to call. All other parts came from Class Three Supply with the exception of the barrel. It came from Blue Grass Armory for reasons explained later.
The SMG recoil spring/buffer assembly is required since the SA spring does not function with the registered bolt. Furthermore, as the Uzi receiver still had the blocking rail the SMG buffer must be “notched” for clearance. However, why would you want to purchase a SMG barrel and extractor? Why can’t you use the SA parts in the conversion and save some money? Here’s why they can be used….but should not be.
The extractor which comes with the SA bolt can be used in the registered bolt but has been identified as the cause of many jams due to its small “lip”. The SMG extractor has a noticeably larger lip which really locks onto the case rim and grips it throughout the violent ejection cycle. The SA extractor cannot perform this quite as well and is the source of problems if left intact. Aftermarket “SMG” extractors are available but many people I have talked to throughout this conversion have consistently said to stay with IMI parts. Nothing else functions as good as IMI.
The same goes for the barrel. The SA barrel is chambered tighter than a SMG barrel and results in an increased number of feeding mishaps if used in full auto fire. While one can save some money by having the 16” barrel cut down to size, the chambering problem will still exist. My original criteria of having the perfect Uzi which was “factory” in all possible respects led to an easy decision: get a correct IMI 10.2” SMG barrel and avoid the chambering hassle. But that was not enough.
As stated earlier, I wanted to use that gorgeous Gemtech 9mm Raptor suppressor with the Uzi. The barrel nut had already been milled out to clear the anticipated mounting lugs. It was now time to lug the barrel – plus one other thing.
The Uzi SMG barrel will not fit into an SA receiver and has to be “contoured” at the barrel trunnion and feed ramp areas to fit correctly. This is because the SMG barrel is deliberately larger at these points by 1mm. Also, the contoured barrel had better not be in your possession until after you have received transfer of the registered bolt. Otherwise, ATF would consider you to possess an unpapered short barreled rifle! This is one time where patience is well worth every day in waiting for the bolt transfer to be completed.
James at Blue Grass Armory contoured an IMI 10.2” SMG barrel and sent it to Dr. Phil Dater at Gemtech for lugging. Phil is world famous for his suppressors and also the absolute quality of his machine work. Furthermore, he will warranty the critical mounting of his suppressors when they are used on German H&K barrels or ones which Gemtech has lugged. Not wanting to blast a hole through the baffle stack of my Raptor I had Doc do the luggings honors. As an added touch he engraved my Uzi’s serial number into the barrel and then beautifully refinished it with black oxide. To avoid any suspicion of having a unpapered short barreled rifle he sent the lugged barrel to my local C3 dealer and I had it held there until the bolt transfer came through.
Oh yeah… to clear the lugged barrel Doc went ahead and machined out a second barrel nut I had sent him. Unlike John’s method of reaming out the full circumference of the nut, Doc precision milled an actual three-lug area. Both nuts do the job correctly – it is simply a matter of which one you like the “looks” of best.
NOTE: It was found out after the fact (Tom’s article) that I could have had the barrel trunnion align bored out by 1mm and milled off the restrictor ring encircling the feed ramp. This would permit an easy drop-in installation of a standard SMG barrel without the need for contouring.
My Model A was an early import and came with a three-detent selector lever. This gave me the ability to flick the lever to safe, semi and full auto positions without having to purchase a new one. If your SA Uzi comes with a two-detent selector lever you could order a three-detent model or mill a third detent position into your existing one. This is not mandatory as the two-detent selector will work fine, just that it will slide about 1.5mm past the “A” and look slightly offset when it comes to its limit of travel.
The registered bolt started life as an 8620 investment casting made by B-G Machine of Bardstown, KY. In late 1985 through May of 1986 there were 950 of them manufactured. Of this number, 300 were registered in .45 cal and 650 as 9mm. None of these bolts were ever made for Mini or Micro Uzi’s and if you come across one it means someone has cut it down to fit. The full size carbine bolts were then case hardened and parkerized. They normally are ready to drop in and fire.
Should you happen to be using an IMI factory SMG bolt which has been slotted there is a bit more work which must be done for use in a SA receiver. First, the bolt’s central tunnel which telescopes over the barrel must be enlarged from the existing .755” to .805-.815” if you retain the feed ramp barrel ring. One solution is to get a tool and die shop to EDM it out and give you a beautifully straight tunnel. If this is done make darn sure you sit there while the work is performed or else transfer it to a SOT licensee for them to do it. The second thing which must be done is to mill a very slight relief undercut into the bolt’s sear notch. The exact angle is not so important as is removing about .005-.010” of material. This will allow the SA sear – which has a slightly different angle/bolt relationship than a FA sear – to properly operate with the FA bolt. Your Uzi will now exhibit a positive disconnector functioning while shooting in the SA mode.
Once these mods are completed you will have a fine IMI factory SMG bolt which will truly drop in. For academic interest, an IMI bolt has a Rockwell hardness of 48 which is very close to the B-G Machine bolt at 50.
Moment of Truth
Function checks of the ratcheting top cover (the pawl and FA recoil spring/buffer assembly had now been put back in), selector switch and grip safety indicated the bolt was releasing correctly and all safety mechanisms were working. Inserting an IMI 32-round magazine – containing one round – into the mag well and charging the bolt brought everything to the moment of truth. I squeezed the trigger and…and…nothing happened. An embarrassed glance told me I had forgot to take it off safe. Thumbing the selector from “S” to “R” and squeezing the trigger resulted in a round being fired and the brass case properly ejecting. Reloading the magazine with five rounds, I charged the Uzi and placed it on “R” again. Firing two quick semi auto shots, I thumbed it to “A” and pressed the trigger. All three rounds fired as expected/prayed for and three casings kicked off to the side. Breathing a very large sigh of relief I loaded up the magazine and proceeded to run out several hundred rounds in various length bursts. The Uzi never once had a stoppage or exhibited any unusual tendencies. After collecting all the brass for reloading, and quietly remembering all the planning and time invested into this Uzi, a smile came over my face. The factory Uzi I had first handled in Bosnia was now duplicated in my hands. Now, you can create one too!
Class Three Supply
PO Box 1119
Hermitage, PA 16148-1119
(412) 962-1890
John Norrell Arms Inc.
2608 Gristmill Road
Little Rock, AR 72207
(501) 225-7864
Pro-Tech Engineering
706 Bainbridge
Barry, IL 62312
(217) 335-2727
Delta Press
El Dorado, AR
(870) 863-6700
Edward Thomas Brady
325 Green Street
Fayetteville, NC 28301
(910) 485-8000
Blue Grass Armory
PO Box 17089
2507 Preston Highway
Louisville, KY 40217
(502) 634-5856
Gemtech
PO Box 3538
Boise, ID 83703
(208) 939-7222
This article first appeared in Small Arms Review V2N9 (June 1999) |