By Dan Shea
SADJ has known and covered the products from U.S. Ordnance in Reno, Nevada for many years. Their US MK43 Mod 0 (M60E4) machine gun is state-of-the-art and the M2HB .50 caliber machine gun from their shops is known around the world for its quality. Over the last few years, U.S. Ordnance founder Curtis Debord, Sr. and Sales & Marketing Vice President Steve Helzer have been traveling to more and more countries with their products and, after many customer requests, decided to begin manufacturing the famous MAG 58, with U.S. M240 features incorporated. Wanting an outside observer, U.S. Ordnance asked SADJ to cover a full military specification style testing regimen. After we finished the full M240 testing, we started talking about the upcoming M60E6 machine gun.
Since the Danish Army has now fully adopted the M60E6, we decided it was time to bring this innovative and well thought out machine gun to our readers. We showed up with our woolies and repeated our foray into the cold Reno winter air and put the hammer down on two versions of U.S. Ordnance’s M60E6… and were pleasantly surprised.
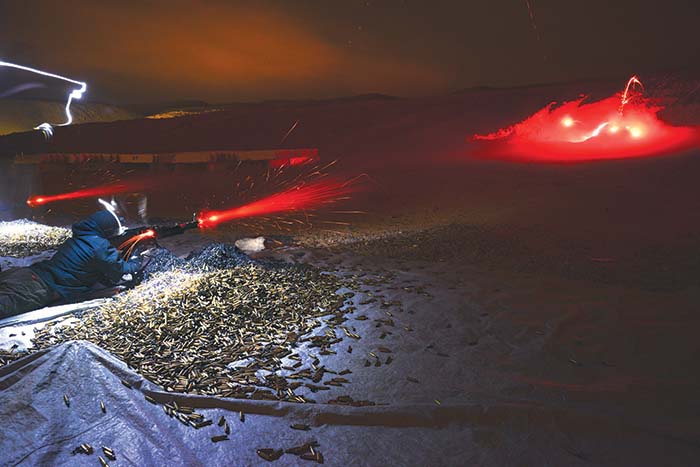
The M60 General Purpose Machine Gun (the “Pig” in ‘Nam talk) was born in the post-World War II era and was actually inspired by the German MG42 machine gun, among other designs. The U.S. government was looking for a replacement for both the M1918A2 BAR and the M1919A4 LMG. Both weapons were very reliable and had served well in training and combat for 30 years. Both the Ordnance Board and Aberdeen Proving Ground had noted the advantages of some of the lighter weight weapons made by the Germans; notably the MG42 and FG42 machine guns, and began experimenting. Students of historical firearms will of course recognize the operating system of the Lewis machine gun as well. The first forebears of the M60 were somewhat odd designs in .30-06 caliber, and by 1951 the M60 GPMG was born as the T161. (Many of the tests, designs, and photos of these early M60s are archived online at www.smallarmsreview.com). Interestingly, there are a small number of these T161 machine guns registered in the civilian community in the U.S. It wasn’t until 1957 that the M60 was adopted into service by the U.S. Army, in caliber 7.62x51mm, as the Squad Automatic Weapon that paralleled the M14 rifle in caliber. Now, the service had maintained a battle rifle and machine gun in the same caliber.
This author has had the pleasure of meeting and interviewing some of the designers of the M60 back in the 1980s, and gained some insight into the thought process and requirement that the designers went through. One engineer explained that the M60 was designed as a modular system in which parts could be easily replaced and the receiver had a life that was specified to be 100,000 rounds. All military firearms have life cycles that are assigned to them, and these are expected replacement points. For example, the M249 receiver has a stated life of 50,000 rounds, and the M240 receiver is 60,000 rounds. The technical specifications on the M60 called for a 60,000 round life, but the designers had targeted 100,000 rounds. There are cases where the robust yet heavier M240 machine guns are known to have fired in excess of 2 million rounds without receiver repair, and the M60 had a receiver stretch gage issued to armorers. During the Vietnam War, U.S. troops gradually integrated the M60 into the fighting units but one tactic evolved that the designers had never foreseen: door gun use on helicopters as daily duty. It was not unusual for an M60 to be used on daily missions where the treelines around perimeters would be pounded for 5-6,000 rounds in a day before landing in an LZ. Clearly, many of these M60s would be facing terminal life at a month’s use, but they soldiered on. Quite a few of these worn out guns were donated to Central American fighters in the 1980s, and this has led to legends about how “Bad” the M60 was. The fact is, the M60 GPMG was a very reliable machine gun, and while it had its problems, it was quite popular and faithful to the machine gunner who kept it clean and properly lubed. Speaking as someone with long experience with the M60, this author can state without hesitation that the M60 was much easier to field. The rounded edges and lighter weight than its predecessor M1919A6, or the M240 that succeeded it, made it far more comfortable to carry, and it was simpler to work on in the field and operate under fire than the M1919A6. Of course, the M1918A2 was an Automatic Rifleman’s weapon in a squad, limited to 20-round magazines, so even though the M60 was to replace it as well as the M1919A6, it truly was used in a different role.
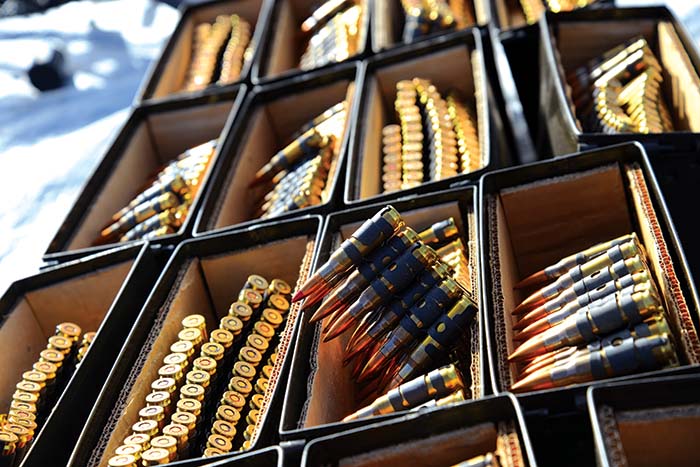
In the 1980s, Saco Defense (manufacturers of the M60 included Springfield Armory and the variations of Maremont Corporation, ending with General Dynamics) was involved in some JSSAP upgrade programs, and the “E3” was born. A lot of reliability changes were made, but one change that was global in effect on the system was moving the bipod from the barrel to the receiver group. It was a nightmare to try to change the barrel on the “Pig” under fire, keeping a low profile, because the weapon had to be supported and moved off of the bipod and a new barrel installed. This is why most operators report that they never changed a barrel in a firefight (although, to be honest, very few operators on a small unit level will EVER change a barrel in a firefight; it’s lost time and not something you think about in the heat of battle). With the advent of the M60E3, this changed. Another important modification was that in the E3 top cover, the feed cam was changed so that the cover could be closed with the bolt forward and then charged. With the old M60, the bolt had to be to the rear in order to close the top cover. Third, the E3 added a two notch operating rod; the second notch was intended to stop the “runaway gun” syndrome with underpowered ammo or when the M60 got very dirty inside.
The E3 was accepted, and upgrade programs began, yet by the 1990s the M240G and M240B were adopted and put into service, with a smaller caliber M249 “SAW” adopted as a belt fed automatic rifle at squad level in the U.S. Army and USMC. The M60E4 was the new competing generation, but it experienced a higher rate of rounds between failures than the M240, thus the services were willing to take the higher weight and length of the M240 series over the M60. (Note that this M60E4 was NOT the same as the M60E4 that is made by U.S. Ordnance today; U.S. Ordnance has a much better design and reliability record on theirs). The M60E4 was adopted in the 1990s by NAVSPECWAR for the Navy SEALS as the MK43 Mod 0, and with its shorter barrel and overall size and weight, has served reliably for over 20 years.
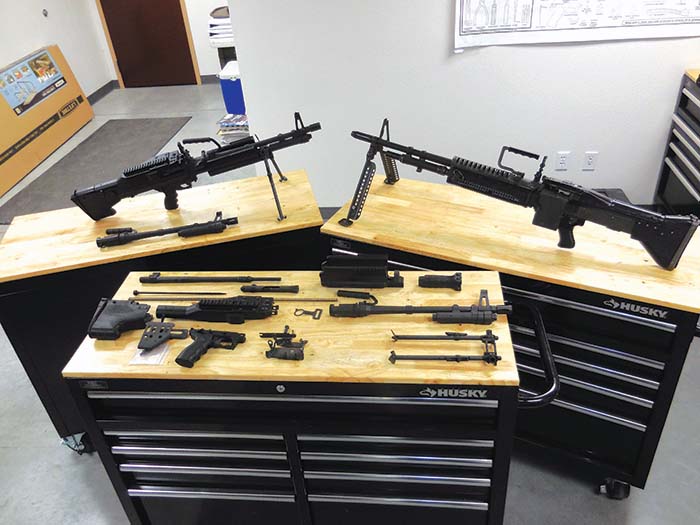
There are literally tens of thousands of M60 GPMG and M60E3 machine guns in service worldwide today. These modular weapon systems are getting tired, and the countries that have them in service are generally looking at replacement programs.
This has driven the duality of our Mil-Spec test design. With the adoption of the M60E6 by the Danish Army, a major Western military has now moved to the newest evolution, so SADJ decided that not only was it time to get this full testing done, but to add the upgraded M60 to the test and run it in parallel. The market for the M60E6 is not just new buyers, it’s complete upgrades to existing inventories in many countries.
As noted, U.S. Ordnance, the subject of this article, has been a military contractor for several decades, and supplies the U.S. M60E4 and U.S. MK43 Mod 0 machine guns, as well as the U.S. M2HB .50 caliber machine gun and a new quick-change barrel M2A2 variant. (We’ll be testing this soon as well). In their new plant in Reno, Nevada, they have the capabilities to manufacture almost any modern weapon system, and the MAG 58/M240 series was a project they recently dove into. That decision was made for them by the many requests from their customers around the world and since the demand was there they would apply their skills to the program and join the market. It was decided not to compete in the U.S. military market as FN Manufacturing and Colt have the longer term contracts; whereas the immediate needs of their foreign customers were an excellent starting point. However, U.S. Ordnance is the manufacturer of the M60 series machine guns and the current counterpart for the U.S. military, so it made economic sense to them to present the E6 upgrade to the U.S. military as well.
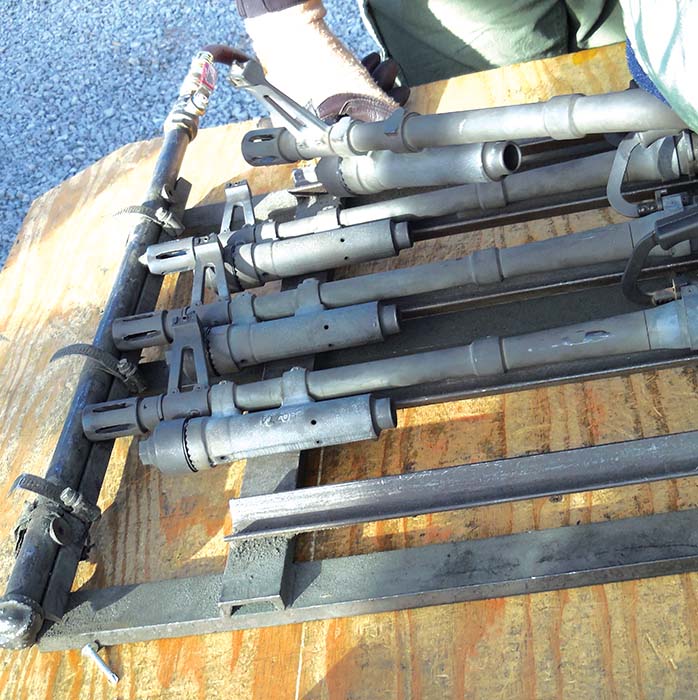
U.S. Ordnance has many strong points in their manufacturing capabilities, and they used them all through the production process. The modern U.S. Ordnance plant in Reno, Nevada has almost any capability from R&D to CNC, to “Cutting Chips,” to barrel making, and one of their strongest points is in their heat treating capabilities. They’ve been able to extend the life of many of their parts because of the deep study and knowledge they’ve put into this subject. For example, their operating rod on the M60E4 and E6 programs has a unique longevity for that part due to this knowledge base, and U.S. Ordnance’s induction heat treatment all the way through these parts has had the effect of reducing this wear point significantly. To be honest, it was this particular part that several of us kept checking – all us old M60 guys. That tower on the op rod just gets hammered, and the ones from U.S. Ordnance’s M60E6 program showed no wear at the end of the test. Very impressive, indeed.
This author has been involved with numerous tests over the years, so it was quickly decided to consult with several military and industry testing professionals to work up a regimen that answered the following questions:
1- Is the M60E6 up to Mil-Spec?
2- Will it perform through a U.S. Mil-Spec test?
3- Are the parts interchangeable for full function testing?
4- What are the Mean Rounds Between Failures compared to the old tests?
5- What is the barrel life and how is the dispersion testing?
6- What is the interchangeability with other M60 variants in existing national inventories? Can they be reliably upgraded to E6?
The tests were designed to answer these questions in a proficient and comprehensive manner. We invite our readers to understand that while this type of test sounds like fun, it is in fact a grueling and demanding task with many hours and many people working to keep the details in order to not invalidate the terms of the test. Since we know that U.S. Ordnance’s 100,000 square foot facility is ISO 9001:2008 certified, and are familiar with the production facility, we just went right to getting answers to the questions about the new M60E6.
One of the best ways to check on a production line’s quality control is to switch out the parts on different units and test them. Interchangeability is critical in a machine gun and it was decided to do this test indoors at the U.S. Ordnance facility instead of on the range. Several weapons were disassembled and interchanged, and function testing was fine. This is what was expected from a combat production weapon – that the parts will interchange and function without fitting or modification. U.S. Ordnance has over 15 years of experience as a company and the management/engineering team has experience going back to the 1970s; so this was no surprise and indicated to customers that they can have confidence in these weapons regarding the supply chain. Parts to U.S. Ordnance guns will work in any of their production weapons. This author has seen parts for machine guns made all over the world, and recommends that the end user gain his supply of spares from the Original Equipment Manufacturer, especially an OEM like U.S. Ordnance with very high quality control.
Perhaps more important to our test, was taking an original Maremont M60 GPMG and stripping it to the receiver, gaging it, and rebuilding it with modern U.S. Ordnance M60E6 parts.
The point of our test was to hammer down on a production E6, and an original “Pig” upgraded to the M60E6 form, and to do this in parallel at the range: Nose to nose, so to speak.
In addition to testing of 100 rounds per minute at intervals and 200 rounds per minute in sustained fire, there is a new test called “Hasty Defense.” This new protocol that USMC and Big Army are planning to implement is 1 minute firing at the cyclic rate of the weapon. In the case of the M60E6, that would be a 650-round continuous burst. Since we were using lightweight barrels, an adjustment had to be made for safety’s sake. We moved Hasty Defense to a 400 round sustained burst.
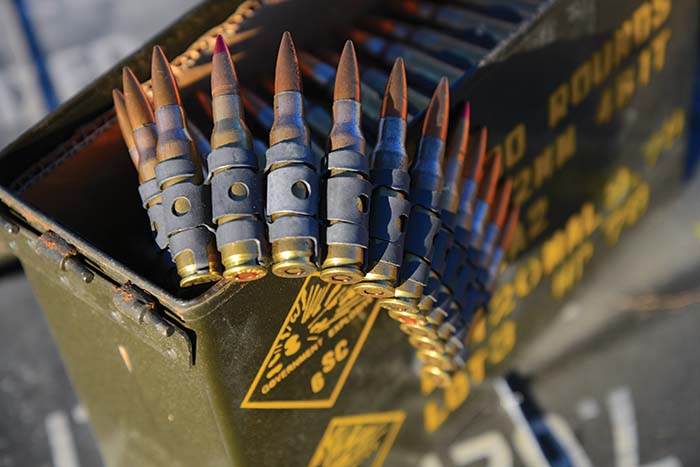
We chose to fire the Hasty Defense test as part of the main test at the very end of the test. Because of their work with the M60 series machine guns and M2HB machine guns, U.S. Ordnance has Stellite lining capability in-house and the E6 barrels were Stellite lined. Thus, before the final accuracy testing, we chose to “put the hammer down” and end with 400-round bursts. We’re trying to beat on these weapons in a methodical, repeatable test, and find out what they can handle.
Army TM9-1005-224-10, the Operator’s Manual for the M60 GPMG, calls for the following rates of fire:
Sustained: 100 RDS/M (4-5 seconds between burst) – Change barrel every 10 minutes.
Rapid: 200 RDS/M (2-3 seconds between burst) – Change barrel every 2 minutes.
What this Operator Manual describes is not a Mil-Spec “Test,” it’s simply the recommendation for the user for his barrel change times. Additionally, there is the “Hasty Defense” test previously mentioned. We chose to intersperse the Sustained and Rapid rates of fire throughout the tests, to achieve a more homogenous result on both weapons and simulate the changing rates of fire found in real use.
The Main Test: 25,000 rounds through each of two U.S. Ordnance M60E6s
The real benchmark to reach for is reliability. In U.S. government test wording: The machine gun shall demonstrate a Mean Round Between Stoppage (MRBS) of 7,500 rounds and a Mean Round Between Failure (MRBF) of 25,000 rounds over a minimum receiver service life of 50,000 rounds. Barrel life shall be 15,000 rounds minimum. This is a pretty aggressive protocol. As an example, while the U.S. Government specifies this, the results of the 1994 competition between the Saco Defense M60E4 and the FN M240 were more realistic: the M60 had 846 Mean Rounds Between Stoppages and 1,669 Mean Rounds Between Failures, while the M240 (which was adopted) had 2,962 Mean Rounds Between Stoppages and 6,442 Mean Rounds Between Failures. Neither weapon achieved this mythical MRBS or MRBF number.
While the M240 appeared about three times as reliable in these early tests, it’s important to remember that these weapons had very different end uses in mind and the M60E4 was a much lighter and smaller weapon and the E4 variant was not fully evolved. The U.S. Ordnance M60E6 was a much better contender in our tests, as the reader will note below.
In order to properly do the testing, a series of firings at set intervals were to be done with the two M60E6 machine guns; one off the combat production line from U.S. Ordnance, the other an upgraded Maremont M60. These machine guns would have to undergo the grueling test until they each reached 25,000 rounds, and the testers would have to rigidly observe firing, cleaning, and parts replacement requirements from the test protocol. Grueling on the testers as well…
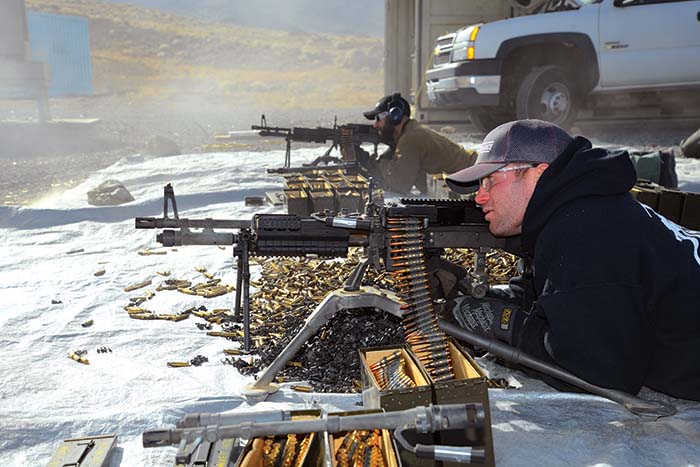
Once the testing started, the protocol had to be observed. Barrel temperature had to be kept within certain ranges, and burst firing had to be kept to the details of the test. We found that the barrels needed to be cooled to about 100 degrees F in order to stay within our barrel change guidelines. Each M60E6 was supplied with three barrels and U.S. Ordnance had designed an air cooling system for forcing air through the barrels to shorten the process between firings. None of the testers like the idea of cooling barrels in water during a test like this.
The test protocol was the same as used by the U.S. military with some modifications due to the weather:
We used Mil-Spec 7.62x51mm NATO M80 ball ammunition linked 4 ball to one tracer (M62), in 200-round belts. This ammunition was Malaysian manufacture in the 1970s and both U.S. Ordnance and this author have used this ammunition extensively and found it to be extremely reliable. Due to recent lack of ammunition from the main U.S. manufacturers and the long delivery times, we opted to use this ammunition. Unfortunately, this ammunition is reaching the end of its life cycle and a number of ammunition related failures were experienced. (Primer and powder have definite lives defined by their chemistry; depending on how it’s stored relates to longevity). Since these failures to extract or fire, and some double feeds were readily identifiable as ammunition related, they do not count towards MRBS and MRBS. As a test matter to prove that theory, at the 12,000 round point, we switched to 2000s manufacture Lake City ammunition for 1,000 rounds and experienced no problems (but did note an increased cyclic rate).
Accuracy testing was performed at rounds 1, 10,000, 20,000, and 25,000. The first tests had a 5.5 inch spread on 8 rounds at 100 meters range. By the end of the testing, one set of barrels showed a 6.5 inch spread, the other set was 8 inches. A very acceptable performance and we were all pleased with this result and did not consider this
a serious degradation.
Many U.S. Ordnance employees are retired or former military. It is a company policy to draw as many veterans into their workforce as possible. This not only works towards their company culture, it is a big “thank you” from U.S. Ordnance to the veterans, and it ensures that the people building the weapons know a lot about those weapons. Jerry Pierson, Retired USMC Infantry Gunnery Sergeant at U.S. Ordnance, and a retired USMC Infantryman, described the production protocol that U.S. Ordnance goes through before shipping machine guns: “In production, accuracy on all raw barrels is checked from a fixture fired 10 rounds, then the barrels go to finish. Then, each barrel is tested on the actual gun for function, 50 rounds per barrel. Then, the gun is tested with 10 lb. belt pull firing 5 rounds simulating lifting a 200 round standard ammo can’s worth. In each shipment of 100-300 guns, one is randomly selected and removed for 1,000 round full test and inspection.” That should explain the quality checks that are being done, and reassure the
customer on that issue.
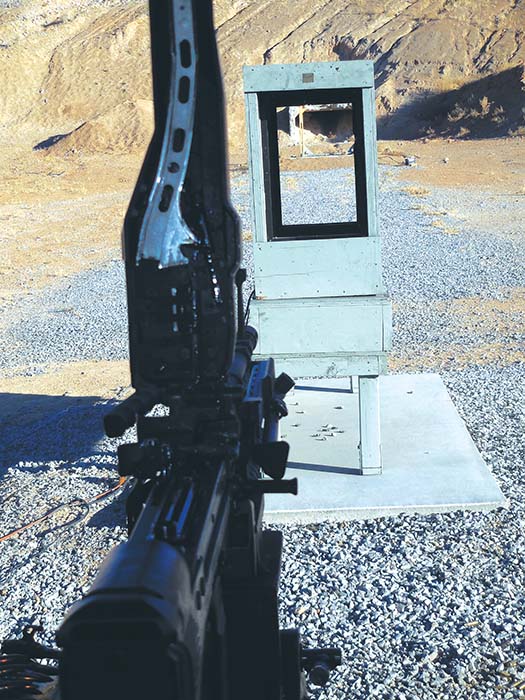
On to the Live Fire
Our firing rates were defined as follows:
200 rounds “slow” was a 7 round burst, then wait 10 seconds and repeat up to 200 rounds then change barrels and move to “Fast.”
200 rounds “Fast” was a 7 round burst, then wait 3 seconds and repeat up to 200 rounds, then change barrels and move to “Slow” again.
We marked the barrels M for the upgraded Maremont gun, O was for the new U.S. Ordnance made gun. This allowed us to keep the test parts with the proper M60E6s.
At 2,500 rounds, each gun was broken down for a quick field strip and general inspection, light cleaning and lube.
At 5,000 rounds, 10,000 rounds, 15,000 rounds, and 20,000 rounds, a full cleaning was done with inspection and minor parts replacement scheduled if needed.
At 10,000 rounds and 20,000 rounds, certain parts were scheduled to be replaced and this was done. These parts were: ejector, extractor, and the firing pin and recoil springs. This is
protocol, and we adhered to it as all testers do.
The U.S. Ordnance manufactured M60E6 experienced a few ammunition related problems; and one instance of an extractor that was replaced with a field extractor which had a problem (not a new extractor). At 20,100 rounds, part of a case broke off and blocked the bolt. Still, that’s an ammunition issue but we called this a Stoppage. In all, we had two stoppages in the U.S. Ordnance manufactured firearm, and no failures.
The Maremont upgraded M60E6 had some problems with the ammunition, until a lubrication schedule was instituted and extractor replaced. At 16,000 rounds, there was a small parts breakage on the right rear tower on the operating rod: the firearm kept running, but the part was replaced at this point. The only real stoppage attributable to the weapon was at 23,801 rounds; the extractor broke and was quickly replaced.
Mean Rounds Between Stoppages (MRBS) is determined by dividing the total number of rounds fired by the total number of stoppages. “A stoppage is defined as any unplanned cessation in firing or the inability to commence or cease firing attributable to the gun. All incidents shall be recorded and any considered as not chargeable to the machine gun shall be substantiated by the contractor.” During testing on the U.S. Ordnance manufactured M60E6, we had 6 total stoppages that were properly attributed to the ammunition. Ammunition issues (failure of ammunition) do not count in this type of test. We had one stoppage attributable to a part failure. The math on that is: 25,000/2=12,500. That’s 12,500 Mean Rounds Between Stoppages. For the upgraded Maremont gun, we had 14 total stoppages that were properly attributed to the ammunition. We had two stoppages attributable to a part failure. The math on that is: 25,000/3=8,334. That’s 8,334 Mean Rounds Between Stoppages.
Result? The U.S. Ordnance manufactured M60E6 system outperformed the U.S. specification of 7,500 Mean Rounds Between Stoppages by a factor of 1.5. The Maremont M60 upgraded to the M60E6 system outperformed the U.S. specification of 7,500 Mean Rounds Between Stoppages by a factor of 1.12. That’s outstanding and beats the old test data from 1994.
Mean Rounds Between Failures (MRBF). MRBF is determined by dividing the total number of rounds fired by the total number of failures. “A failure is defined as any stoppage which involves part replacement or requires in excess of one minute to correct; or involves any failed or damaged part detected during scheduled preventive maintenance, the replacement of which is not authorized at the crew or organizational level of maintenance as prescribed by Source Maintenance Recoverability Code and TM-9-1005-313-23P.” The MRBF numbers are the same as for Stoppages, since we only experienced ammunition related problems.
We’ve already mentioned the capabilities that U.S. Ordnance has at their facility. It’s necessary when supplying military grade firearms to stick to a specification for manufacturing process. However, there will be certain procedures that can be changed to produce a more durable product, as long as the R&D and production teams know what the issues involved downstream are.
U.S. Ordnance wanted to ensure full compatibility with all mounts and accessories, so the M60E6 will mount onto all M60, M60E3, M60E4 mounts, and will accept the M60D spade grip configuration, although if “D-grips” are the plan, it’s best to order M60D to begin with.
MIL-SPEC TESTING AVAILABLE
If you are a manufacturer of military weapons and want to have an unbiased test designed and performed for you, Small Arms Defense Journal can help. Our Editor-in-Chief Dan Shea will assist with this and explain protocols, help design the test system, and evaluate the costs. Contact us at info@sadefensejournal.com for further information.
U.S. ORDNANCE, INC.
300 Sydney Drive
McCarran, NV 89434
United States of America
www.usord.com
Tel: 775.343.1320
Fax: 775.343.1331
Sales: sales@usord.com
Marketing: marketing@usord.com
Support: support@usord.com
Training: training@usord.com
Photos by Shay Swetech
FFECREATIVE.COM
www.smallarmsreview.com
This article first appeared in Small Arms Review V19N8 (October 2015) |