By David Lake
Steel, Simplified.
Steel is the stuff of which the modern world is made. It is pervasive in history and its presence and application mirrors the rise and fall of man and his kingdoms as well as his proliferation around the globe. Scientists and engineers of the past century have been largely unsuccessful at creating its replacement. Barring the limitations imposed by the basic laws of physics, there are not many problems that cannot be solved by the judicious application of steel in one of its many forms. There is perhaps no better example of Mankind’s technological triumph than when he used steel to create the gun.
The oldest known “gun” by todays definition was developed in China (agree most anthropologists and archaeologists). The first guns created by the ancient Chinese were likely bamboo- or other hollowed out wooden tubes, which may not have been used to fire a projectile. There is some conjecture that these guns were first implemented as “shock and awe” technique- firing off bursts of flame and smoke to intimidate and confound a battlefield foe. It is unclear when exactly the gun would be used to fire a projectile- which was likely an accident the first time it happened. Man’s inherent need and ability to fix and improve things around him would ultimately adapt the simple pyrotechnic display into an implement crafted from steel, and intended to fire a projectile. The rest of the story of the gun follows man through the middle Ages, the time of exploration and conquest, and ultimately the industrialization and modernization of manufacturing and the globalization of commerce. There are marked times, usually times of war that spawned the great advancements in the science of the gun. Mounted cavalry, siege weapons, personal body armor, cannon and naval warfare all demanded that the gun become more potent and precise. Distance and accuracy and power would become requisite qualifications of the gun. Sometime in the last 500 years, the science of the gun seems to have reached a plateau, relatively speaking. Every shooter from a matchlock pistol to a shore gun battery would be made of steel (as they still are). Steel could provide the strength to exploit the power required to inflict the ranged effect we associate with the modern firearm.
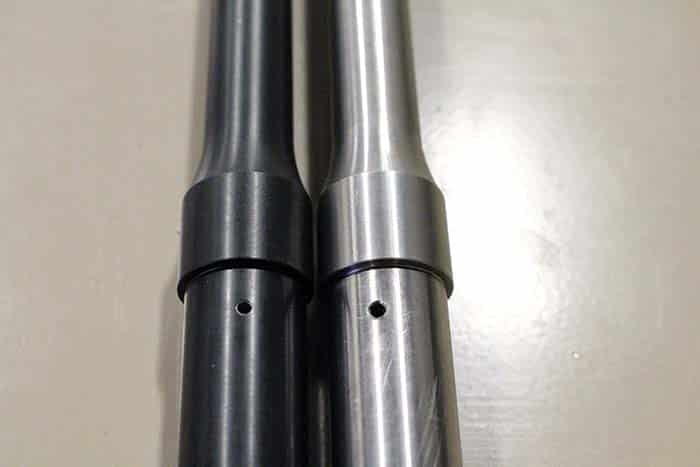
The meter of the modern small arm often and deservedly defers to the “mil spec.” This is an established code of standardization. It envelops a set of rules and requirements for anything claiming to be up to par. It is not necessarily a qualifier of excellence or superiority- unless superiority can indeed be found in uniformity and consistency. The term “mil-spec” has become a generic descriptor, and is often applied to any of the wares and materials purveyed by today’s arms makers. And it is not entirely incorrect to refer to a steel alloy applied or used per an established mil-spec as “ordnance steel.” It is widely agreed that ordnance, or mil-spec steel refers to a specific family of steel alloy; chrome-moly, such as 4140. The enforcement of standards and uniformity is absolutely necessary to ensure any amount of quality and reliability in any system. Today all metal alloys are given a title or numerical designation from one of the authorities on metallurgy and engineering, the SAE, and AISI. These material names and designations describe a recipe or physical and chemical properties. So a steel may be described by what it actually is, as is the case with 4140CM steel, the 4 digit label indicates general type of alloy, and the precise levels of other additive elements to make the steel.
In actual terms, depending on the manufacturer of a gun or its components, the terms Mil spec and Ordnance Steel may be used to describe any of the following (but not limited to); 4130, 4140, 4145, 4150, 4320, or 4340 chrome moly alloys. The truth of the fact is that ANY steel may fall into the category of being “mil-Spec” provided that it satisfies the criteria set forth in the military standard for operating and yield strength for a specific application. There is a tendency for gun manufacturers to use misleading descriptions of their steel and its capabilities in order to promote sales. All steels are not created equal. This sales tactic can put the gun and its user at risk. All steels are not created equal; beware of the fly-by-night startup gun company that professes tactical supremacy but omits the metallurgical details of their operation. That said, modern firearms components from reputable sources (as are most things engineered) are designed with a “safety factor” in mind. Any gun barrel today should be designed with a minimum 1.5 safety factor- which means that barrel is designed to endure 1.5 times its intended operating load before failure or fatigue. The “mil-spec” for a steel structure usually demands a factor of only 1.5. Commercial engineering often requires a safety factor of 2.0 or higher. One should also be wary of the claim of “aerospace” in firearms design. The tolerance, safety factor and quality assurance by aerospace standards all become prohibitively expensive and ultimately restrictive to the end user. Aerospace grade demands a total detailed and documented control and trace of material from creation through use and operation. Nothing about your rifle is aerospace grade.
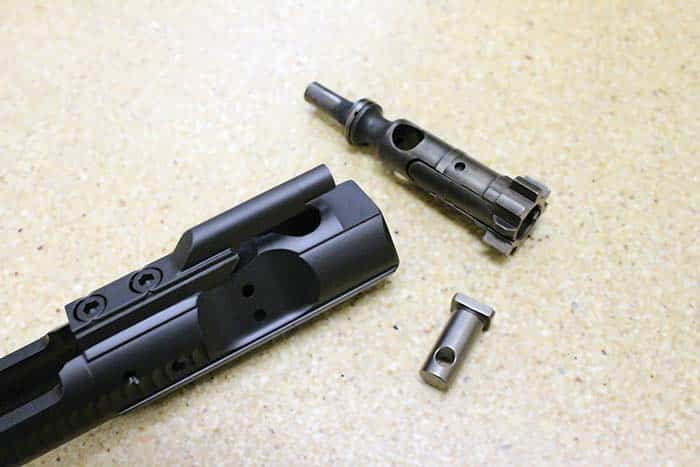
On to the specifics of the steel that may be encountered in the modern small-arm. There are only 4 general types of steel; carbon, tool, alloy, and stainless. All material that can be described as steel is one of these. The creators of steel add various trace elements to iron to achieve desired properties. All steel contains between .25% and 2.5% carbon, which allows the base iron to be chemically or thermally manipulated with or without the addition of other alloying elements. To earn the rank of stainless, the recipe of that steel must contain at least 11% chromium. Chrome moly alloy steel does contain chromium, but not enough to be stainless. And all stainless steel is not totally rust resistant. Some stainless is highly magnetic. It is doubtful that one will encounter a low carbon or plain carbon steel on a gun today; industry lawyers and a general concern for safety have well established a minimum for safety standards. Tool steel is capable of being very hard and tough, but is more difficult to craft. It may be used on guns in small amounts to form items like trigger parts or lock components. One should expect to find all (non-stainless) gun barrels and receivers to be made of an alloy steel; nickel-steel, nickel-chrome, or chrome-moly steel. These types of steel contain trace amounts- usually only up to 3% by mass of these other elements. The presence of nickel imparts extra strength and tremendous resistance to temperature and mechanical stresses. It is interesting to note that iron meteorites are usually an iron-nickel alloy- containing up to 25% nickel. That high nickel content is responsible for the meteorite’s ability to survive entry. The presence of chrome and molybdenum in steel alloy will increase hardness and resilience. Plain carbon steel is too weak and brittle or soft for firearms application. Chrome moly steels are not resistant to oxidation and other surface reactions to include rust and corrosion. Gun parts commercially produced from chrome moly steel are always encountered with a coating or treatment to inhibit surface corrosion. The most common are blueing and parkerizing which form protective oxide barriers on the steel. Chrome moly steel may be coated, clad, or plated in other metals like electroless nickel, hard chrome or newer high performance metal/polymer matrix coatings.
Chrome moly steel is indeed the first choice of the professional market. It is tough. It maintains strength and stability over a wide temperature range. It resists fatigue and failure caused by abrasion, wear and heat. Even in hostile maritime environments, today’s material science offers a host of treatments and coatings to protect the steel from surface attack. Chrome moly used in ordnance is not a “free machining alloy”, that is, it is difficult to machine and form. However, chrome moly does lend itself well to the application of these aforementioned coatings and surface treatments. We are all familiar with “chrome-lined” barrels. Most all gun barrels in general circulation with our armed forces- pistol and rifle alike are chrome lined (M-16 rifle, M9 sidearm). Adding a layer of abrasion and heat resistant hard chrome to the interior surface of a barrel adds longevity. In the case of the M16 or AR-15, if it is respected and not abused, a chrome-lined, chrome-moly steel barrel can expect to serve its owner with good function and acceptable accuracy up to or beyond twenty thousand rounds.
Stainless steel is rapidly becoming the default material used by barrel manufacturers. The most common alloy used in the gun market is known as 416R. This stainless steel makes an attractive barrel to be sure. It’s bright and shiny, and is known for being easy to machine. 416R is a “free machining alloy” which implies that it is created with a molecular structure that makes the material easy to cut. Free machining alloys employ trace amounts of lead and sulfur to improve machinability. While making this steel cost effective to manufacturers, and visually attractive to the consumer, the mechanical properties of free-machining alloy may also make it less desirable to the well-informed. 416R is not nearly as abrasion resistant as chrome-moly steel. And it can only claim 65,000 psi tensile strength (4140CM boasts 98,000psi). 416R does not resist fatigue and erosion from exposure to high heat. At high heat levels- those commonly encountered in military applications, 416 can distort, lose its heat treated state, and even de-alloy—a condition where the additive materials lose their microscopic bonds to the iron/carbon structure. So this material, while in use, could become unsuitable or even unsafe. Not to worry—416R comes with a reliable programmed response to imminent failure. It will split like a banana peel before it fragments. This splitting action is resultant of the “stringers” as they’re called, the areas of sulfur that co-mingle in-between the regions of martensite (crystalline structures) in the metal alloy. There are other grades of stainless one might encounter in barrel making. 410, 420 and 17-4 are less common, though they are found in use. 17-4 is renowned as a super alloy. It is fabled to get stronger from heat exposure. It has been said that it possesses mystical powers to “self-heal” micro fractures and surface defects. Few have ventured to deep-drill and cut rifling into a chunk of 17-4. Many have failed. The name Noveske will forever be remembered as one that succeeded. 17-4 is mainly used in pistol and revolver frames, muzzle devices, or small parts and even receivers and bolts of custom high-end high-power rifles. The last stainless worth mentioning here is 410 alloy. It is the underachiever of the bunch. The yield of this material is actually less than its intended operating threshold- a fact that some in the industry will argue. 30,000 PSI is where 410 can undergo “plastic deformation,” that is, be stressed past its ability to bounce back. Barrel makers still use this stuff knowing that a 5.56 NATO cartridge reaches over 60,000 psi just after ignition. Is this cause for alarm? Not really. Stress is calculated as a constant applied force. The pressure curve inside a gun barrel in not contained for any period of time, nor at a static load, but rather a burst that reaches a peak pressure. The pressure is not contained long enough or focused at a singular point where it could cause damage to the barrel. The barrel is saved by the fact that high pressure gas acts with equal force on all sides of its container (in this case the barrel)- and one side of the container (the bullet) is moving away from this applied force. So the bullet is effectively a valve that allows the pressure to escape. 410 alloy is said to be tougher and more abrasion resistant than 416. It is used by some manufactures to make gun barrels to save cost as it is imminently easy to machine. The more common stainless, 416R does deliver on some promises. Many custom rifle builders who work for the competition market trust 416R. Countless benchrest, palma and F-class records have been claimed by guns fitted with barrels made from 416R. This material does in fact make for a perfect surface finish during machining. This perfect surface lends itself to superb accuracy. A barrel properly ‘smithed from 416R will perform supremely, though not indefinitely. A match-grade stainless barrel fit to a high-powered competition rifle may be expected to have a good service life of 3000 rounds, more or less, depending somewhat on the caliber of the rifle, and largely on how it is cared for.
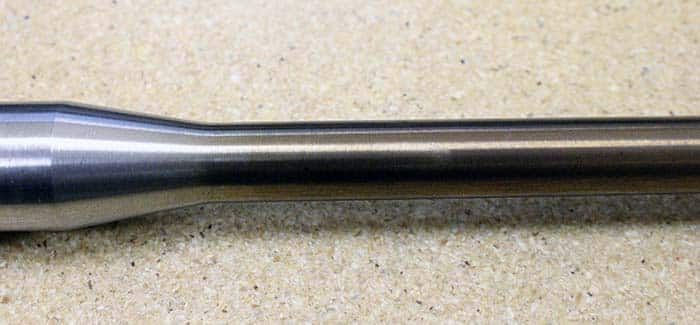
Steel of any alloy may be encountered in a number of “states.” This refers to the condition of heat treatment it may have received. Annealed steel has been softened. This condition does not imply that the steel is mild- only that it has been reduced to a softer state to make it more workable. Hardened steel generally refers to a surface hardening to improve that steel’s wear resistance or reduce its frictional coefficient. This condition may also be called “case” hardened. Heat treated steel is generally hardened throughout, also known as “core” hard. Core hard is a condition commonly employed on high wear or high load components. Certain alloys are better suited to be case hardened. Others are tailored for use in core hard applications. For example, the bolt carrier group in an AR-15 is made of several steel alloys- each selected for it properties as they fulfill the requirements of the BCG’s operation. The bolt itself may be made of something called Carpenter 158 that has been heat treated to a desired surface hardness to resist wear while maintaining internal elasticity, and resistance to fracture of the locking lugs. The bolt carrier body is commonly made of core hard 8620- a nickel-chrome-moly steel used for its superior resistance to heat induced fatigue and mechanical shock. The carrier houses a high-temp expansion chamber that is usually hard chrome plated. The gas key might be made of 4130CM, and specially coated to resist high temperature and impart lubricity so as not to cause abrasion to interacting surfaces. The cam pin receives tremendous abuse, and is formed from a core-hard piece of 4340CM—very high in nickel and chrome. The cam pin will endure severe abuse- repetitive compressive and shear forces and high heat imparted by the M-16’s operating system. These parts are often protected by a hard metal plating or clad in a metal/polymer matrix. Both, designed to kill friction and resist heat’s damaging effects.
So we can conclude that there is no “best” steel for your gun. Lesser materials may be used to great result provided proper engineering and quality assurance to back them up. Super alloys can lose all their attraction when cost and gained advantage are brought into proportion. Long past are the days of Damascus steel when one could be killed by his own gun if the bi-metal structure were to give way. The quality and consistency of steel used in the industry today exceeds the quality of manufacture implemented by the gun makers themselves. Our modern steel industry is nearly flawless. Good steel makes us better.
This article first appeared in Small Arms Review V20N2 (March 2016) |