By Matt Smith
SAR had the opportunity recently to sit down with Joe Gaddini and Scott Prince of Southeastern Weaponry Research (SWR) based in Martinez, Georgia, near Augusta. This article has two parts- the interview portion, and a product evaluation portion. The purpose of this article is to provide both the background of this Class II manufacturer and the scientific testing of their unique suppressors.
Part One: The Interview
SAR: How did you get started in this business, Joe?
Joe: It started when I was living in Florida in the early 1990’s, where I had been working for an engineering firm for several years and career-wise getting nowhere. I resigned my position with the firm and moved to Jacksonville at the request of a friend. While first in Jacksonville, I was interviewing with several engineering firms. During this same time period, I met a guy named Joe Moody, who was a long time friend of Reed Knight. After Joe found out I was a mechanical engineer, and knew Reed was looking for one, he arranged an interview for me at Knight’s. I interviewed with Reed and Doug Olson, and they hired me. Reed deemed this initial time of employment as a “dating period” and allowed me to live in the onsite trailer for several months. I worked typically 10 to 14 hours per day at a computer station using an Autocad design program. While at Knight’s, I found the work very interesting and was able to meet and work with many talented people. I was exposed to a variety of special projects that included suppressors such as the KAC QD M-16 can. The redundancy latch on this suppressor is one of my designs. Although very interested in designing items for use in the Spec Ops community, I eventually grew tired of being chained to the computer and decided to go out on my own.
At about the same time I met John Weaver, who was working in his small shop as JRW Sports. He showed me that one guy could make a living doing this. I decided to follow his lead, relocate back to Augusta, GA and thus SWR was born.
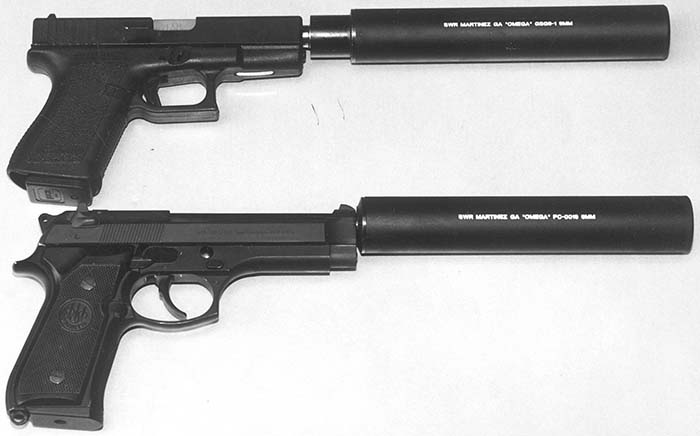
SAR: Do you have formal training as a welder or machinist?
Joe: No, unfortunately these are crafts that are not taught in engineering school. That experience was gained while working for an emergency services engineering company based in Atlanta. During my seven years with the engineering firm, my job was to travel nationally to fossil fuel, nuclear, and chemical plants, where we sealed their on-line leaks. I went on site and designed mechanical band-aids and seals. After design and drafting, I would then take my prints into a machine shop and work with machinists and welders to build what I needed to repair the problems. These were custom made assemblies, and I was able to observe how each one was fabricated. This experience gave me the ability to machine and weld the products we make here at SWR.
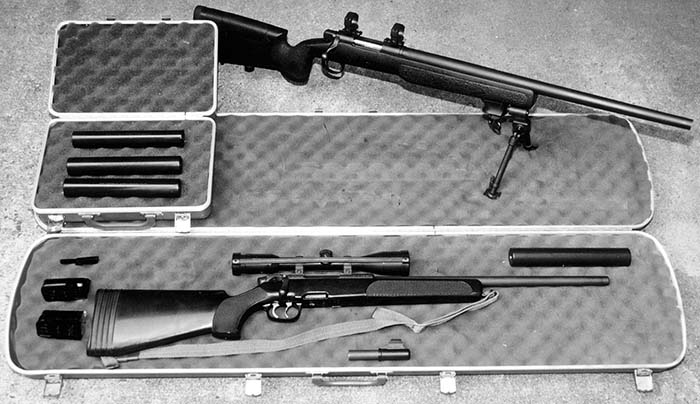
SAR: What were some of the first products that you produced with your new company?
Joe: Poorly built .22 cans (laughing). Honestly, I started out with an old Craftsman lathe donated to me by a friend of mine. We were making cans with stamped steel cone baffles. We did improve rapidly, and gained immediate popularity once we began innovating new ideas into our suppressors. We entered the market at a good time period. When I started SWR, Jonathan Ciener was getting out of the .22 suppressor market and we were there to fill this void. Back then the major players included: AWC Systems Technology, Reed Knight (mostly military sales), and Gemtech, which was just forming. We got into the market at a time that was perfect for us.
I worked together with John Weaver during SWR’s early years. John had been making suppressors for a number of years, and we gave each other a lot of help. We would often bounce ideas off of each other, and in the process became very good friends. We both soon realized that in order to stay competitive we needed to be unique. My main goal after leaving Knight’s Armament was to not replicate anything I’d seen there. I decided to develop completely new baffle designs rather than depend on a variation of what was preexisting. After three to four years of testing and evaluating, we gained a very firm grasp of what would and wouldn’t work in a firearm suppressor. Most of the data that had been gathered up to that point was empirical, at best. It was like voodoo or black magic…. what you thought would work, wouldn’t and vice versa. Not really knowing what else was out there, I had the opportunity to have Kevin Brittingham and Mike Smith from Atlanta visit and bring the Gemtech line of suppressors which Kevin’s company was a distributor for at the time. Up to that point, I thought we were doing pretty well. However, when I heard the Gemtech gear, I was amazed, and knew this was some top-notch stuff. I didn’t know the history of how, why, who, or where it was designed, I just knew that it was quiet. It was recognizably quieter than a lot of what we had done to date. This experience gave me the drive to seek out and act further.
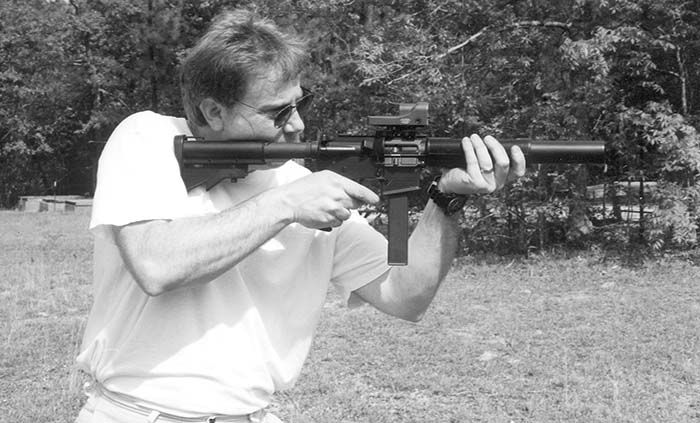
We knew the theory and I knew what the problems were with many of the older suppressor designs. While many people thought the answer was sheer volume, thinking the bigger you made it the more gas it will trap, I realized that a new baffle design was needed. At this time, there was a downsizing trend in the industry. Everyone was looking for smaller, lighter, and quieter. There were limitations at this time to what could be done with existing baffle technology. (Laughing) At that point, I didn’t know the difference between a “K” baffle and a “M” baffle. All the terminology used by the larger manufacturers in the industry was a mystery to me. I had no idea what baffle type Gemtech or any of the other manufacturers used in their cans. All I knew was what I had previously seen at Knight’s Armament. I’ve never been the type of person to get somebody else’s can and open it up to see what was inside. That didn’t interest me. Over the years, after talking with other designers such as Greg Latka, Phil Dater and Doug Olson, I began to comprehend their approach to modern suppressor design. I was finally able to design a new baffle based on this understanding. This is what I consider a new approach to an old design. I’m sure if you go back through all the firearm suppressor patents, there may be something similar, but I am using the right combination of all the other ideas out there, mixed with new. I have described our baffle as the anti-K baffle. It is 180 degrees opposite of what the K baffle is and yet in most applications exceeds the K baffle’s performance.
We designed and built our first prototypes and then began sound meter tests. We soon discovered that we were obtaining decibel reduction results that few of the other manufacturers were getting to at the time. This intrigued me, our new baffle design was showing amazing promise, and in the long run only needed minor refinement for vast improvement. Through trial and error we were able to determine crucial parameters such as baffle orientation, porting depths, porting angles, baffle spacing, and expansion chamber dimensions for various calibers. We succeeded with the optimal baffle design that would work well in almost every caliber we tried it in.
We now have a dry environment suppressor in a relatively small package yielding sound reductions that have never before been achieved by anyone else in the business. We are very proud that we have come up with something that we feel is unique, that in some cases is actually performing ten to fifteen decibels better than what’s previously been available on the market. I’m not trying to take anything away from anybody else, I’m just saying that we did our homework, it paid off, and we built a better mousetrap. Who knows, maybe next week somebody might better what we have done, but in the meantime, we will continue to improve what we are doing.
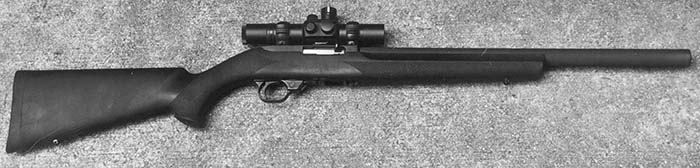
SAR: Scott, what role do you play at SWR?
Scott: I was hired for technical sales. I am the one that greets you with a smiling face and performs physical demonstrations of our suppressors. Secondarily, I assist Joe in the various stages of manufacturing and assembly in the shop when not on the road.
SAR: What sales tools do you utilize on the road?
Scott: My standard sales point is that I will meet you anywhere at anytime and compare our products to what you currently use. And if you don’t like what you see, I will go away.
SAR: Have you ever been taken up on this and asked to leave?
Scott: (Laughing) Let’s put it this way. To date, I have been received like the Good Humor man on a hot summer day. These suppressors speak for themselves.
SAR: What are some of your current models?
Joe: The mainstay of our business has been the integrally suppressed .22 line. These include the Ruger Mark II pistols, 22/45 pistols, and the 10/22 rifles to name a few. These seem to be the most popular because the typical person buying a suppresser is not buying one to put it on a submachine gun. These are individuals who might want to shoot a rodent in their yard, or take their sons or daughters out to the range to shoot a small, inexpensive caliber without a lot of noise. By far, the last four or five years the Rugers have been our mainstay.
We are at the point where we are using a longer barrel and a shorter tube in our integral units than other manufacturers are. We’re using our new baffle design in what we call the Omega series of suppressors. We have gotten some extremely good numbers with this series. While there are others in the market that are building longer cans with shorter barrels that will yield low numbers, we are very satisfied with the fact that we are meeting and beating many of the results obtained at the most recent Suppresser Trials. Our accuracy is better than excellent. We have one target on the wall in our shop from a local SWAT team using our integrally suppressed Mark II’s. This target that was shot with 10 rounds of CCI Mini-Mags at twenty-five yards off of a bag rest resulted in a dime-sized group. These types of results have shown to be typical of our suppressors. Shot groups from another recent testing were incredible.
SAR: Are your integrally suppressed weapons designed to be used with a certain type of ammunition?
Joe: Yes, they are. Most integral suppressors including ours use a ported barrel. The reason for the porting is to reduce bullet velocity to subsonic levels. Our integral units are designed to be used with high velocity .22LR ammunition. We have a preference for CCI Mini-Mags and Remington High Velocity ammunition. Both of these cartridges utilize a copper washed bullet that goes a long way to reduce lead fouling. Using already subsonic ammunition in a ported barrel is simply pointless. We have found that high velocity ammunition in our integral suppressors are performing optimally for both sound suppression and accuracy and at velocities that are more than adequate for any possible scenario.
SAR: What other models are also in the Omega line?
Joe: The Omega line consists of the .22’s, the 9mm pistol cans, a newly designed Glock suppressor, both 9mm and .40 caliber, our submachine gun suppressors, & our .30 caliber can which is attracting a lot of attention by the Spec Ops community. Our entire line is yielding sound reductions never before achieved by anyone in the business. We are currently in development of our new .223 suppressor. As a registered contractor with the Navy at Crane Naval Warfare Center, we are developing this suppressor in support of NAVSEA’s recent request for their SOPMOD program.
The market trend has been to make six or seven inch long .223 cans that yield 28 to 32 decibel sound reductions. What we are looking to put out is a unit that performs that well or better, but it will have excellent accuracy, as to not change the point of impact when the suppresser is mounted. Some suppressors currently available change the bullet point of impact by up to eight inches because of a shift in the barrel harmonics, or because the baffles used cause the bullets to yaw. Current design emphasis is focusing not only on sound reduction, but longevity, durability, and the ability of the weapon to not exceed a predetermined accuracy deviation while deployed with a suppressor. Our current .308 can exceeds these criteria. One example being a local SWAT team marksman deploying our new .308 suppressor on a Savage tactical rifle (with a twenty-four inch barrel) and shooting a smaller group size with our can than without. Shot Groups from a recent testing were incredible.
SAR: Can you give us any specifics on the .223 can you are developing?
Joe: It is six inches in length, with decibel reduction in the mid thirties. We are shooting for 36dB reduction and are very close. Most six inch cans on the market today are yielding reductions from the mid twenties to the low thirties. I want my can to achieve mid thirties performance with the longevity and durability required to withstand full auto fire. With the advent of the Beta C mag and the weekend shooter, we are not really interested in marketing a .223 suppressor to the civilian market. This is not because we don’t want people to have our suppressor, we just don’t want to end up rebuilding a high number of them due to abuse. The Beta C mag is a .223 can killer. The heat and pressure that a .223 round generates will destroy any good can after an appreciable amount of rounds of consecutive full auto fire. Once a suppressor leaves our shop we have no control over its use or misuse. Presently there are several good .223 cans being sold on the civilian market, and we don’t want to compete in that market for the reason already mentioned. We would like to move more into the military market. At that point, we would probably sell contract overruns on the civilian market, as Knight’s Armament has done.
SAR: What kind of mounting system would you use on the .223 can?
Joe: There are currently some quick detach .223 cans on the market. These cans provide good sound suppression, with what appears to be excellent mounting systems. Unfortunately, because of the high-pressure environment, there is a great deal of blow back and carbon build up. After a certain amount of rounds and any type of neglect, the suppressor will seize on the flash hider mount. The down side of the quick mount is that without proper maintenance there will be problems. Of all the quick detach mounts currently available, the Gemtech Bi-Lock unit is our favorite.
When it comes to thread mounts, there has been some talk that left hand threads are superior to right hand threads. This is explained because the gases flowing through a right hand twist barrel tend to unscrew the suppressor from the barrel since the gases are traveling in the same rotational direction as to loosen the suppressor. I do not believe that this is true. It is simply pressure and vibration, and has nothing to do with the fact that the gases are coming out swirling in such a way that it’s imparting a spin on the can or baffle system. That’s just simply bologna! If you’ll look at the Navy SEALs and similar organizations, they do not use a lot of quick detach cans. I’m not sure of the exact reason for this, but even from the days when the Navy first adopted the MP5, they requested that its barrel have a thread mount in front of the three lug. These operators use these weapons everyday in the real world and stake their lives on the reliability of their gear. I have to believe that they would request the best possible mounting system available and if threads are what they require, then you have to pay attention to that. Until something better comes along, other than for pistol caliber suppressors, we are going to stick with the thread mount.
SAR: What’s in the future for SWR.
Joe: Well, as we continue to get attention from the military community as we have recently, our customer base will increase. We’ve met some of the right people in the Spec Ops community, and they’re starting to take notice of what we’ve shown them. We have done several demonstrations for large audiences of SOCOM personnel, and unlike showing up at NDIA or some of the other industry trade shows, we’ve met these people in other areas and performed personal demonstrations for them. What we are doing has convinced them that our products are an improvement over what they currently have at their disposal. Not only a big improvement in sound reductions and durability, but accuracy. Our future hopefully lies in increased military sales and government contracts. As we are designing military products, we are pushing hard to develop new and innovative suppressors for both the military / law enforcement and civilian markets. We’re not going to get to the point one day where we’re going to thumb our nose at the civilian market. The civilians in this country who are legally able to obtain suppressors are the ones who made our company a success. Our message to these customers is thank you very much for your continued support!
There are a lot of new manufacturers popping up who are selling average suppressors for a very low price. We are not out to overcharge for our products, but there are a lot of research and development costs in both time and money behind them. For us to sell a suppressor for $150 and stay in business is impossible. Many of the new manufacturers in this market are able to sell suppressors in this price range because of virtually no overhead and little or no R & D costs. The biggest thing that we want to continue to do is to innovate rather than rehash someone else’s designs. A lot of pride goes into this work, and we want to always maintain integrity in the marketplace. There has been a lot of cloning and copying of existing suppressor designs in recent years, and whether they’re original or not is beside the point. If somebody puts in five or ten years of hard work, we are not the type of company that would copy it and market it under another name and a lower price claiming that it’s better or refined. We are offering what we know to be original, in-house designed suppressors.
SAR: What are some of the custom suppressors that are available from SWR?
Joe: We continue to offer our High Standard HD military replica suppressed pistol. It looks the same on the outside, but it has a fully updated & modern internal baffle stack. We are using all CNC manufactured components in these as in all of our suppressors. We originally started our business as a custom suppressor shop. We are now at the point where we are more of a production suppressor shop. We have a set amount of different models and series of suppressors. We have moved from being solely a small customer oriented business doing strictly custom work to a business geared up for production. We will continue to take in custom work as time permits, but customers need to be patient when requesting this type of work. As my friend, Joe Moody, is fond of saying, “If you go to the best restaurant in town and there’s no waiting line, then you’re not at the best restaurant in town.” Terry Dyer’s HK work is another example of this. He is backed up sometimes two or three years on his work. We are not the biggest, and we’re not saying we’re the best, but we feel that if we’re behind in production, any delay you may experience will soon be forgotten when you receive your new SWR suppressor. We care about our customers and we want them to be happy. We have an unconditional guarantee, “You break it, we fix it.” We don’t say that we have a lifetime guarantee, because nobody really knows what the future may have in store for us, but as long as SWR is in existence all of our suppressors are 100% guaranteed for replacement or rebuilding.
Other custom suppressors that we have manufactured include integrally suppressed Swedish K’s, Smith and Wesson 76’s, integrally suppressed Colt 9mm uppers, HK MP5 SD’s, replacement cans for some of the HK machine guns, Browning take down .22 rifle suppressors, Anschutz rifle suppressors, Browning Buckmark suppressors, and a few Colt .22 suppressors. What we’re trying to concentrate on now is a specific line of suppressors and to build what we know, and know that what we’re building is the best.
SAR: How do you address the size issue of your suppressors, since there are smaller suppressors on the market?
Joe: There’s been a lot of talk about this issue. I’ve heard some of my competitors say, “You might be doing forty decibels of reduction dry, but ours are smaller.” Well, if yours are smaller and doing thirty, and ours is a little bit bigger and doing forty, we respond that we are not in a race to build the world’s smallest suppressors. Our approach is to build the absolute quietest “dry” suppressors possible. We may not have the packaging and marketing emphasis that others do, but I can boldly say we have the quietest suppressors available bar none.
SAR: I have noticed that none of your suppressors are designed to be shot wet. Why is this?
Joe: During the last two years of R & D of our Omega baffle, one of our goals was to design a baffle system that would eliminate the need for an artificial medium. Face it, water and grease equal mess! A suppressor that performs dramatically better using an artificial medium is less than optimized. In fact, using water or grease is nothing more than a crutch! Our baffle design is at the point that water or grease yields little or no improvement in sound reduction.
SAR: How are your products distributed?
Joe: We prefer to distribute our products through a network of dealers. We have quite a following of good, loyal dealers throughout the country. We haven’t covered every state and region, but we have a number of extremely professional dealers that we appreciate greatly. It’s kind of like the Hair Club for Men, these guys not only sell our products, they swear by them. I will always take the time to answer someone’s questions about our products, but I will leave retail pricing issues to an individual’s local dealer. We don’t have specific territories, but we do try to protect the dealers that we have.
SAR: Scott, tell us about your trips to Blackwater.
Scott: Joe and I were both invited up to the Blackwater Training Center in Moyock, North Carolina late last year to do a demonstration. Lt. Colonel Chandler, who owns Iron Brigade Armory, is a retired Marine officer, and builds possibly the finest bolt action sniper precision rifle in the world. Colonel Chandler was especially interested in our new .308 Omega rifle suppressor. All of the instructors at Blackwater are long time military personnel and familiar with many of the suppressors available, having used them on various missions. After the initial introductions, they accepted us as if we were long lost friends. We set up for the demonstration and Colonel Chandler fired the first round, and said, “***Damn!” He was impressed not only with the suppression, but also the fact that there was very little, if any, point of impact shift, with or without the suppressor. Other suppressor manufacturers have demonstrated their suppressors at Blackwater, but according to the instructors we spoke with, they were somewhat disappointed in the shot dispersion with these competitor’s products. Affirmation from a group that builds their own quality product and who have used suppressors in the tactical world made the long hours and the hard work worth the effort.
My most recent visit to Blackwater at the request of some special units brought me once again into a rigorous testing environment. The folks I demonstrated for had all their ducks in a row and had several marksmen available to test our Omega suppressors in a multitude of scenarios. The testing data was recorded on both video and computer medium. All I can say is that the accuracy results amazed everyone present. The sound suppression levels, even in metal-framed tactical shoot houses, had them in awe.
Joe: The basic problem with other manufacturer’s products is that most lack real military design and manufacturing experience. While I was at Knight’s Armament, I gained a lot of this knowledge. I learned from, and worked hand in hand with, those people who had a great understanding of what the real world operators are looking for. I also learned to respect confidentiality and to protect end user identity. That’s the approach we used when we designed our .308 can. We did not design this suppressor with the civilian market in mind. That has given us an advantage in designing and building the tools that our Spec Ops community really wants. What we’re designing are firearm suppressors that can be used with great results in an operational environment. Much of the knowledge we gain designing for the military is then used to better our civilian products.
SAR: What equipment and facilities do you have available at SWR?
Joe: First off, our shop here has gone from a small manufacturing shop to a much larger shop in a short amount of time. We presently own two CNC machines, both of them being turning centers. The first is a Miltronics ML-15 two axis lathe, and the newest machine is a Colchester 60 degree slant bed, live tooling turning center. What we have been doing for the last year is outsourcing a lot of our CNC work to some of the other shops, which are licensed and able to make suppressor components. Although they do an exemplary job in their machining, the cost of not only designing, but also procuring all these parts is immense.
Our machine shop also includes two Bridgeport mills, two Clausing lathes, an Atlas lathe, numerous welding and metal fabrication pieces, bead blasting cabinets and air compressors. Everything is built in house. We still have old world pride in workmanship, but everything is built on modern equipment.
SAR: What materials do you utilize in your suppressor manufacturing?
Joe: The materials we’re working with are primarily stainless steel/Inconel and aerospace grade aluminum. For years, our suppressors were entirely stainless steel or chrome moly. Now we are moving over to a mixture of different alloys and different heat treatments. We do not make titanium cans because of the special tooling required, and the fact that they do not hold up well in a high pressure, high temperature environment. Our high power rifle cans are machined, assembled, structurally welded, and permanently sealed. Although designed primarily for bolt action rifles, our suppressors will survive full auto environments. We have tested one of our suppressors with up to three hundred rounds of continuous firing through an M60 machine gun. The new pistol cans, submachine gun cans, and the new .22 thread mount cans are aluminum other than some stainless steel components, including the threaded end cap. Our suppressors are not designed for customer disassembly and are permanently sealed. The design includes cross-porting and waste porting in our baffles to allow pressure to flow freely through our suppressors. One of the key designs for our new baffle is not to dead end the gas causing carbon deposits, but to expand and cool the gases and allow them to exit freely.
On our Glock can, we have come to the conclusion that the only way we’re going to get a high efficiency suppressor to cycle the weapon is to use a Nielson device. Therefore, on our Browning action handgun suppressors we use an internal recoil booster which can be easily disassembled from the rear for periodic cleaning, and if necessary spring replacement or changes. We call our Glock suppressor the GSG-9, after the West German anti-terrorist group, which helped convince us to incorporate the Nielson device to reliably cycle all variations of Glock pistols. Rumor of our new Glock suppressor with 40 dB reduction dry has more than peaked an interest.
SAR: What are the specifics on your .22 LR muzzle cans?
Joe: We are now offering three versions of a very small thread mount can which is under five inches in length. Materials include aluminum, stainless steel and parkerized chrome moly steel. Our new muzzle cans are 4.85 inches and weigh as little as three ounces. These are all dry environment suppressors with performance that exceeds all .22 suppressors available on the market today.
SAR: The engraving on your suppressors is some of the finest I’ve ever seen. How do you accomplish this?
Joe: We have a small CNC mill, which is run by an IBM Pentium laptop computer. This little powerhouse does a good job for us. It engraves to a depth that exceeds BATF requirements. (Dan’s note: this is critical, because we have observed a number of manufacturers utilizing inexpensive laser engraving techniques that simply work the surface, and while the result is pretty, the legal qualifications are not being met. As of January 1, 2002, ATF will be rigorously examining the products.)
SAR: What did you think of our sound testing results?
Joe: As you know we just completed a rigorous two days of testing using a Bruel and Kjaer model 2209 sound pressure meter in accordance with MIL-STD-1474C . We tested a vast array of not only our suppressors but many of the current offerings from the top suppressor manufacturers in the country. This was the first time I was afforded the opportunity to directly compare our offerings to those of our competitors. Although previous testing on our part has resulted in higher reduction results from our products, we felt that the results of the two days were an accurate reflection of the Omega series. For example, as you witnessed, our 9MM Omega pistol suppressor metered 12 dB’s quieter than our closest competitors. Although we fell short of previously obtained results, we still exceeded the sound level reductions of all of our competitor’s offerings that we tested.
SAR: I agree Joe. The sound meter testing results were very impressive, and they will be tabulated and recorded on charts. Thanks for giving SAR the opportunity to be the first to witness the new Omega series of suppressors.
Joe: You are very welcome. I appreciate the chance to compare my suppressors with many the others out there and show the high level of performance of SWR’s Omega line.
Part Two: Sound Meter Testing Results
The sound testing equipment was provided by SWR. The procedures used follow the specific testing protocol outlined in Al Paulson’s Volume One, Silencer History and Performance. A Bruel and Kjaer Type 2209 Impulse Precision Sound Pressure Meter, set on “A” weighting and peak hold was used with a B&K Type 4136 1/4-inch condenser microphone. The meter was calibrated using a B&K 4230 calibrator prior to the tests. The microphone was placed one meter away from the front of the suppressor or muzzle. The microphone was pointed straight up oriented at a 90-degree angle from the bullet flight path. The weapons were fired 1.6 meters high over grass. Velocity data was obtained using a P.A.C.T Mark 4 chronograph with sky screens set 24 inches apart and the start screen eight feet from the muzzle. These are the same procedures I have followed hundreds of times shooting for SAR at the Suppressor Trials.
The ammunition used is all commercially available and contact data for manufacturers of the subsonic ammunition is provided at the end of this article. Ten shot strings were recorded for each weapon and the average reading obtained is provided in the tables.
The 9mm pistol cans were the most impressive to me of all the suppressors tested. I brought several competitors suppressors to test fire for comparison with the SWR cans. The SWR Omega PC can mounted on a Beretta 92 achieved a net sound reduction dry of 37.7 decibels with Alabama Ammo 147 grain ammunition and 35.5 decibels with A-Zone 147 grain ammunition. The closest competitor’s cans tested achieved a 26.4 decibel reduction dry with the Alabama Ammo and a 25.7 decibel reduction with the A-Zone ammo. The SWR Glock GSG-9 suppressor was even more impressive as it achieved a reduction of 38.4 decibels shot dry with the Alabama Ammo subsonic and 38.2 with the A-Zone subsonic ammunition. The closest competitor’s can was over 12 decibels louder using the same ammunition. This difference is amazing and shows the superiority of the Omega baffle designed by SWR for dry suppression. I even shot the competitor’s cans wet and they still could not match the sound reduction of the SWR cans shot dry. The Omega 3 lug can shot on the HK MP5 performed well in our tests. The can achieved a 32 dB reduction compared to a 25-30 dB reduction by the competitor’s cans evaluated.
The Omega .22 cans performed very well in our tests. The Omega muzzle can mounted on a Beretta 87 achieved a 39.7 dB reduction using Remington subsonic ammunition. The competitor’s cans ranged from 36.1 to 37.9 dB reduction when tested with the same ammunition. The SWR 10/22 integrally suppressed rifle achieved a 30 dB reduction with both CCI Mini-Mag and Remington High Velocity ammunition. The closest competitor’s 10/22 can tested achieved a 28 dB reduction. The SWR integrally suppressed Ruger MK II pistol achieved a net sound reduction of 41.9 dB with Remington High Velocity ammunition and 42.6 dB reduction with CCI Mini-Mag ammunition. The competitor’s cans tested with Remington High Velocity ranged from 31.5 to 40 dB sound reduction and 32.2 to 38.6 dB reduction when shot with CCI Mini-Mag ammunition.
The Omega .308 suppressor was shot using supersonic Black Hills 168 grain match ammunition which yielded a 33.6 dB reduction and EBR subsonic 180 grain ammunition which yielded a 34 dB reduction. Shortly before this article went to press, Joe called and said that his latest .308 can tested at Blackwater yielded a 36 dB reduction using supersonic ammunition.
This article was written to share the history of SWR with our readers and to illustrate how the SWR line of suppressors performs. The accompanying charts provide detailed information for the testing of each SWR suppressor. Through this testing it can be seen that the SWR line achieves maximum suppression for dry technology suppressors. It was not intended to provide detailed information on all the suppressors available on the market today. For an in-depth evaluation of other manufacturer’s offerings, purchase the SAR Suppressor Trials book that is being published in the near future.
Contact Information for Subsonic Ammunition Manufacturers:
A-Zone Ammunition
1340 Deer path Drive
Osteen, FL 32764
(407) 330-7768
www.azoneammo.com
sandrodiaz@mindspring.com
Brad Galloway
(designer of Alabama Ammo Subsonic)
Custom-K
1601-C Highland Ave
Montgomery, AL 36104
bgall@knology.net
Alabama Shooter Supply Inc.
(current loader of AL Ammo Subsonic)
19505 Al Hwy 24
Moulton, AL 35650-7364
(256) 974-3504
Black Hills Ammunition
P. O. Box 3090
Rapid City, SD 57709-3090
(605) 348-5150
www.black-hills.com
Engel Ballistic Research, Inc.
544A Alum Creek Road
Smithville, TX 78957
(512) 360-5327
engelbr@swbell.net
This article first appeared in Small Arms Review V5N2 (November 2001) |