By George E. Kontis, PE
In 1917 an unusual device was trialed that gave the soldier a means to quickly convert his slow firing bolt action M1903 Springfield rifle into a higher rate-of-fire semiautomatic weapon. The bolt action mode was proven to be effective at long ranges, whereas the semiautomatic conversion was intended to improve his effectiveness in close combat. The Pedersen device, as it was known, was classified “Secret” and generated tremendous interest from the military, but was never used in combat. The inventor of this device was a Danish immigrant from Wyoming named John Douglas Pedersen.
Before introduction of this conversion kit to the Army, Pedersen was enjoying a very successful career at Remington Arms. He already had several successful designs under his belt, and had gotten to know John Browning when they worked together on the Remington Model 17 shotgun. Browning was so impressed with Pedersen he called him, “the greatest gun designer in the world;” potentially the definitive case where “it takes one to know one.”
More than his design prowess, it was Pedersen’s vast knowledge of mass production and the resolution of production problems that had impressed Browning. After World War I, the Army lured Pedersen away from Remington with a lucrative contract. The Army never revealed their reasoning, but it is likely they had more in mind than just bringing a clever gun designer into their fold. His eventual contribution was something so significant we might not have won World War II without him.
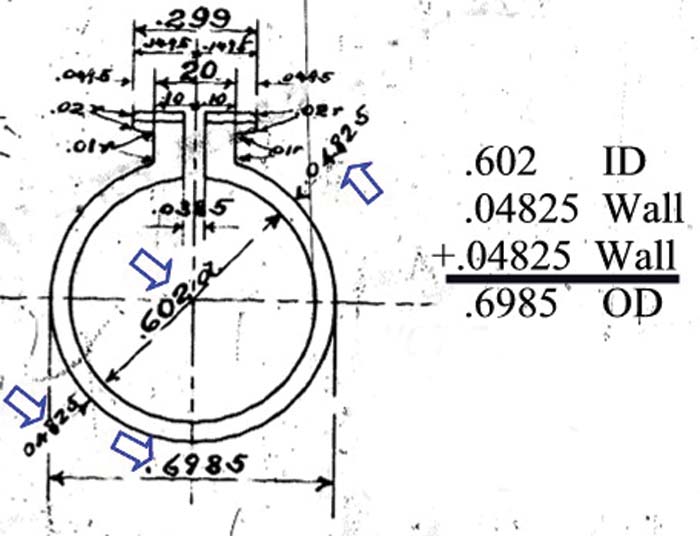
Mass production of firearms and other mechanical devices had been well underway since the Civil War. Henry Ford pioneered this technology in the automobile industry and other industries, like the country’s armories, were trying to turn out guns and other ordnance the same way.
In a typical gun factory, huge ceiling mounted shafts rotated leather belts that reached nearly to the floor. These belts rotated pulleys to power the milling machines and lathes that made the parts. As each part was removed from the machine, its configuration was checked by a set of gauges. If it passed the gauging, it was considered “good” and went on for further processing.
In the early years of the 20th century, the learning curve for mass production was still in its infancy. Problems on the production line were numerous and difficult to solve. When parts were finished and sent to the assembly line, some of them assembled perfectly, while others required rework. Other parts assembled well enough but it was later found they would not function in the firearm.
The problem parts caused engineers and machinists to question if the components had been specified correctly. When John Pedersen encountered these problems he knew what had caused them and lamented, “The sins of faulty production design now overtake us.”
Pedersen explained what happened next:
We now begin to realize the import of the word “trouble.” A detachment of “trouble shooters” is hastily organized, many suggestions considered, some adopted, and changes to equipment are started. The production schedule has already been “badly bent” but hope lingers that by extra effort we can yet swing in with the final quota. The necessity of frequent “explaining” to the head office does not add to our peace of mind or ability to secure results. Yet important decisions must be made, for – to continue machining may accumulate a mass of useless component – to stop will result in no components for the assembling department to practice upon.
Pedersen went on to explain that after design and manufacturing changes were made, production was restarted and parts with the newly adopted changes came to assembly. Generally the old problems were solved, but it wasn’t long before new ones would crop up.
There were cases where more than one factory was producing the same product. But instead of sharing solutions to production problems, each factory tended to resolve its own issues, with their own unique solutions. Very often this killed any chance of parts interchangeability between production lines. Production problems were so commonplace that everyone involved in the production from the engineers to the assemblers believed they were unavoidable. Except, that is, for John Pedersen, who not only understood the problems, he presented logical and workable solutions to fix them.
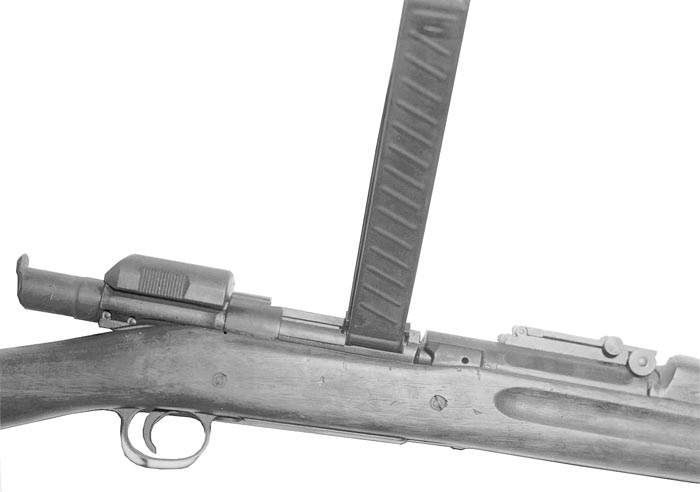
Pedersen’s solution began with the dimensioning of the parts. He insisted that the upper and lower size limitation, or “tolerance,” of every dimension on each part be specified. This was a practice started by French military engineers in the late 1700s, yet well into the early 1900s tolerances were specified on only a few dimensions on U.S. military ordnance components.
Pedersen studied the machining methods of the day and determined the accuracy of every machine tool. He presented this data in a table designed to serve as a reference guide for production supervisors and machinists. Pedersen even realized that in wartime it would be necessary to enlist machinists of a lesser capability than the bevy of master machinists working in the peacetime arsenal. So to his recommendations he added that the tolerance specified also be achievable by the lowest skill level of machinist expected.
As an example, let’s look at a drawing of the Extractor Collar from the 1903 Springfield rifle. This part fits in a groove on the bolt to retain the extractor and must be in clearance with the receiver so the bolt can be drawn back and forth. First notice there is no indication of the allowable maximum or minimum on any of the dimensions. From the dimensions marked by my arrows, you see where the outside diameter 0.6985 (OD), the inside diameter, 0.602 (ID), and the wall thickness, 0.04825 (given twice) are specified. It’s easy to imagine that if the OD is too big, there could be interference problems moving the bolt, but from the drawing there is no way to know how big is too big. Pedersen’s table tells us there’s no way to achieve any dimension perfectly every time regardless of how we machine it.
Another issue is that the allowable concentricity between the ID and the OD is not specified. If you know this part or understand the application, it’s easy to see how fit or function might be adversely affected if the ID and OD are not in close concentricity.
Specifying too many dimensions, as in our illustration, gives the machinist too many options for manufacturing the part and can cause a wide variation in the uniformity between parts. This situation is known today as “double dimensioning.”
Double dimensioning and lack of dimensional controls, result in another problem called “tolerance stack-up,” and is usually uncovered only after parts are put together. Pedersen recognized that the accumulation of tolerances was detrimental to designs and illustrated the concept with the following example: The result is analogous to that obtained by the amateur workman who, in sawing off boards for a picket fence, uses the most recently sawed picket as a measure for the next, and finds that the final picket has acquired surprising stature.
Pedersen understood that production problems went far deeper than merely specifying maximum and minimum limitations for every dimension. When a part was drawn, rarely did the designer give much thought as to how it was to be manufactured. Pedersen recognized this as a failing and observed that … neither in production of ordnance materiel nor in industry in general, has adequate study been devoted to designing the component parts with the expressed purpose of facilitating their mass production.
The draftsman’s job was to make a dimensioned “picture” of the component and that’s where the problem started. A draftsman rarely considered that the machinist had to have some way to hang on to the part as it was being shaped. Draftsmen might, for example, dimension some features from the left end of the part and others from the right end, never realizing that the left end wouldn’t even exist until the very end of the process when the machinist cut the part away from where it was held while being machined.
Pedersen’s understanding of the complete problem led to his advocating of a new thinking that revolutionized not only the production of small arms but other mass produced items as well. A good machinist would take great pains to set the part up in the machine correctly and tried to maximize the features to be cut on each setup thereby minimizing the number of setups. Machinists and draftsmen worked in the same factory but might just have well been on separate planets. Someone had to get them together if U.S. small arms production were to be successfully mass produced, and John Pedersen had a plan for that too.
Pedersen proposed that experts with production experience would shadow the inventor, making rounds in the drafting room to determine how each part would be made, making sure it would be dimensioned in a way that would allow it to be manufactured accurately and with the fewest setups as possible. Simple tooling would be designed to hold the part on the machines in the workshop and the set of tooling would be duplicated for production lines in other factories. He even came up with a name for the work these experts would do. He called it “Production Design.”
Having a maximum and minimum dimensional study as well as a Production Designer reviewing each drawing would be added cost to the manufacturer but Pedersen stated: … no pains should be spared to reduce the design to the forms best adapted to production and to define precisely what each component shall be.
Once a “production engineered” part made it to the manufacturing floor, Pedersen advocated that every machined dimension would be checked by simple gages. This was to account for wear in cutting tools and possible dimensional variation from one set up to the next.
Following World War I, Pedersen recognized there was a need for great speed in producing weapons with interchangeable and interoperable parts. His lengthy essay on production theory was published in the June 1935 issue of the American Ordnance Magazine. The article received widespread acclaim and was recognized by the prestigious American Society of Mechanical Engineers. Not surprisingly, his paper became the bible for everyone involved in mass production. Someone had finally identified the cause and the cure for production line problems.
In 1935, not even Pedersen realized that only four years later we would need to be successfully producing war materiel at breakneck speed. Without this important contribution by John Douglas Pedersen, “Rosie the Riveter” might have very likely ended up with a file in her hands and today we’d all be speaking German.
This article first appeared in Small Arms Review V13N7 (April 2010) |