Text & Photos by Jeff W. Zimba
The first time this writer ever saw an example of a rifle sporting a DuraCoat camouflage finish, one problem immediately came to mind. Don’t set this gun down in the field and turn your back or you may never find it again.
Steve and Debbie Lauer from Lauer Custom Weaponry (LCW) offer several complete packages for the “do-it-yourselfer” to apply their DuraCoat firearms finishes to existing guns. DuraCoat was introduced at the 2001 SAR Show in Phoenix Arizona, and while listening to a lengthy answer asked by a potential customer, there was a one comment that stuck out more than any other; “You can do it yourself.” That simple phrase has stuck with me in the years since hearing it, and after watching these finishes evolve and adapt to so many new environments it was time to give it a try.
DuraCoat can be applied directly to carbon steel, stainless steel, alloys, synthetic materials and even wood. There is no priming and no etching necessary and unlike other finishes, no baking is necessary to cure. DuraCoat dries to the touch in about 20 minutes and can be handled in about an hour. It is ready for use in just one day but continues to get harder and even more resistant to solvents and abrasion in 3 to 4 weeks. It is extremely resistant to salts and because it retains a light amount of elasticity it does not typically scratch or chip. It can be applied as thin as .25mls and as thick as 1.5mls. It can even be used to build up tolerances when desired.
Starting completely from scratch, it only made sense to order the Level II Starter Kit, the instructional DVD and some of the TruStrip Cleaner/Degreaser. This includes everything you need to get going. For the test, the Urban MirageFlage was chosen for a color and pattern selection, thus receiving the appropriate colors and templates. The colors used in this package are Matte Black, Snow Gray and UM White, but with over 15 different patterns to choose from and over 64 base colors to begin with, the combinations are unlimited.
The Urban MirageFlage is a digital pattern and a series of “Peel ‘n Spray” self-adhesive templates are included to achieve these shapes. It is as simple as peeling these shapes from the backing and sticking them on the firearm where the design is desired. After the color is sprayed the templates are removed by just peeling away. This makes it completely unnecessary to design and create custom masking when finishing your own firearm. In some instances these shapes are even reusable allowing you to finish several firearms with the same set of templates.
Putting DuraCoat To The Test
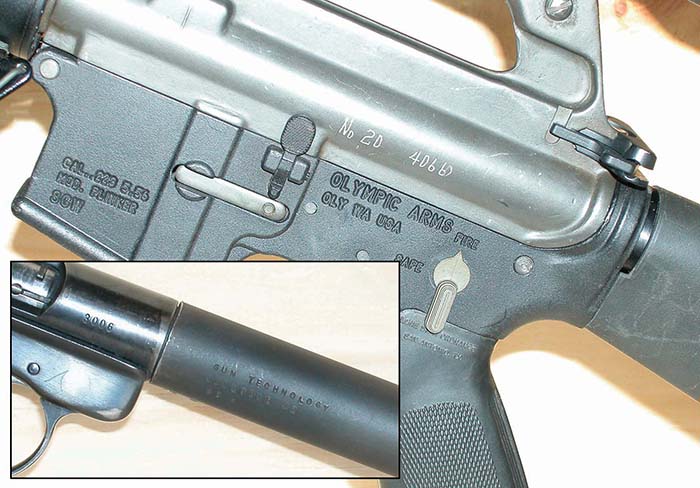
Where this was a project for an admitted novice in the area of refinishing, a couple of firearms that were already in need of some kind of finishing were selected as the initial test subjects. This way a firearm that looked fine to begin with would not have to be sacrificed should things not work out as planned. Two candidates from the depths of the gun safe emerged as the guinea pigs. The first was an old, suppressed MK I Ruger pistol that has lived in the back of the safe for over a decade. It functions great and is quite impressive in its performance but was mismatched with the pistol finish having a very worn and thin bluing while the suppressor portion was parkerized. It did not match at all and looked terrible. The second test subject was an AR-15 variant that was assembled from a collection of spare parts that had been growing for several years. After test firing, it was decided it would be a “keeper” because it was so accurate, but it still looked terrible. The lower was a dark and heavily blast beaded finish. The upper receiver had a shiny, dull and worn finish with a Police Department inventory number carved in it with an electric pencil. A sound suppressor was selected to match the rifle and a few magazines were chosen to complete the package. A few minutes with the Dremel tool and a light sandpaper drum removed the electric pencil marks and it was time to get going.
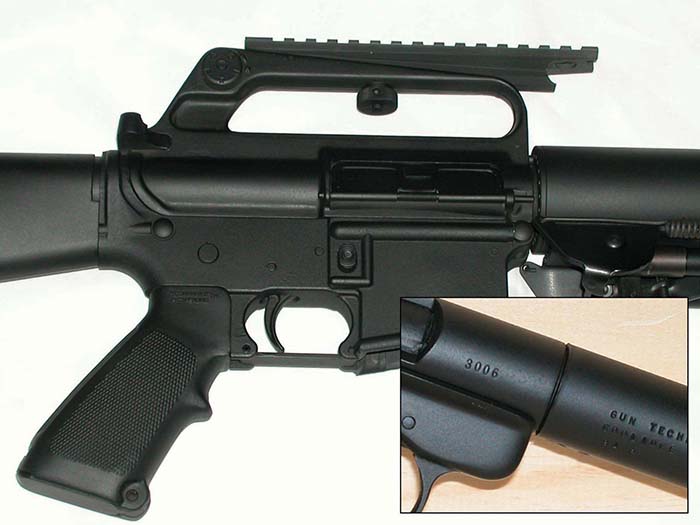
Properly cleaning the parts may be the most important step of the entire process. The finish needs a clean, dry surface to adhere to. In this example, both firearms were finished fully assembled. This would help match the patterns on the final product and would be a much quicker way to begin. While this is an acceptable way to apply the finish, it is very important to completely degrease everything. When parts are assembled it leaves many places for oils and lubricants to hide. The TruStrip Cleaner/Degreaser was used allowing everything to dry. A high-pressure wand from the air compressor to coax any residue out from these hiding places was also utilized. The TruStrip was used again after drying just to be certain all oils were gone.
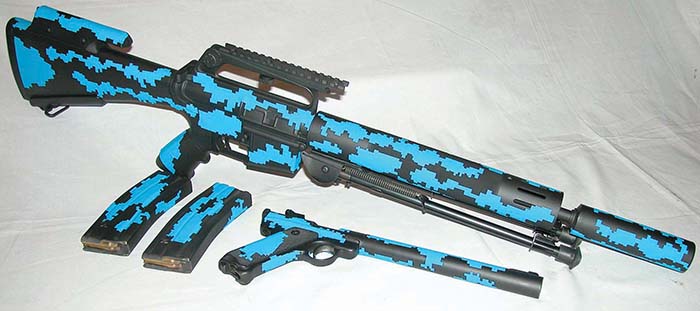
When everything was dry it was time to mask anything not intended to be finished. In this case all that needed masking was the bolt in the MKI Ruger pistol. Everything else was going to be sprayed. A small automotive detail gun was used to apply the finish instead of the airbrush included with the kit so it involved much more masking that typically necessary due to the additional overspray. This would come into play a little later in the process but for the initial base coating everything got a coat of Black. It is important to think ahead a little when spraying and to adjust your finish coverage appropriately. Areas that are “high traffic” and tend to rub on holsters or other surfaces should get a little extra covering. Areas with tight tolerances, like magazine wells, should not be covered so heavy. It is easy to go too light on the base coat because the DuraCoat covers everything so well it immediately looks finished. My advice would be to spray what you think is covering everything, than spray a little more.
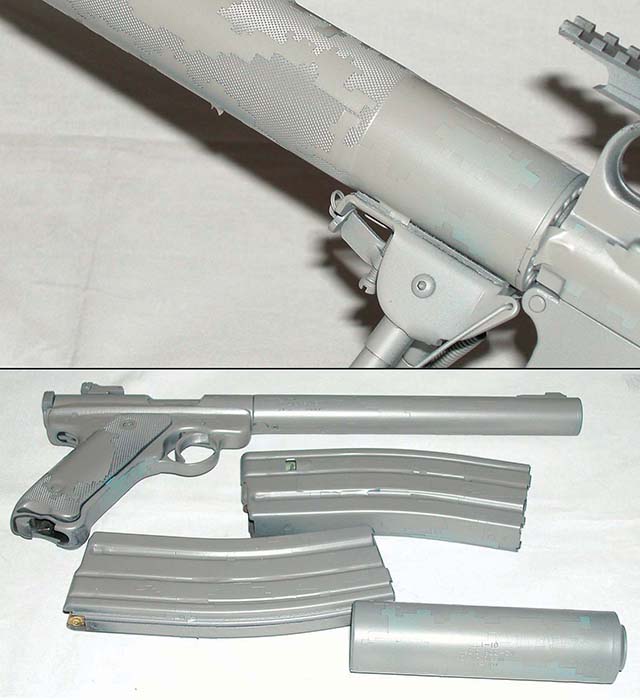
After the initial base coat was allowed to dry a few hours, the first set of templates were applied. These “male” templates should be stuck on every area that you intend the original, base color to remain. In a 3-color system, the second color will be the dominant color and in this case the second color would be the Snow Gray. The templates are all pre-cut and after deciding on the size and shape desired, they only need to be peeled from their backing and stuck right on the area being finished. After applying the templates the next step was spraying the second coat, completely covering everything again. When spraying multiple colors, only enough material needs to be sprayed to cover the previous color completely. It is not necessary to “build up” consecutive colors because it covers so well. After applying the Snow Gray everything was allowed to dry overnight.
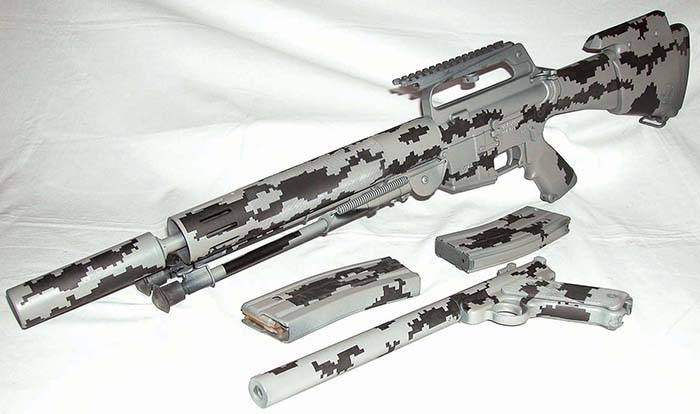
The next step in the Urban MirageFlage pattern is to remove all the templates covering the base color. This is when things started looking drastically different. It was becoming obvious how well this project was actually coming out. After all the templates were removed there was a little excess adhesive remaining from the templates. It was removed by gently rubbing the areas with some mineral spirits on a soft, clean, white cloth.
After allowing all parts to completely dry it was time to apply some “female” templates for the areas where the final (UM White) color would be sprayed. We wanted to cover some larger areas than the provided “female” templates would cover, so we used the knockout areas left over from some of the larger “male” templates to make our own. After masking everything for the final time the last color was sprayed. If the little airbrush had been used to apply the final color, there would have been little masking necessary at all. Usually, the extra masking around the provided “female” templates is all that is necessary for this application. Because of the larger spray gun, with overspray as an issue, everything needed to be masked completely that was not intended to be covered with this final color. In hindsight it would definitely had been advantageous to go the airbrush route on this final layer and save the extra masking time.
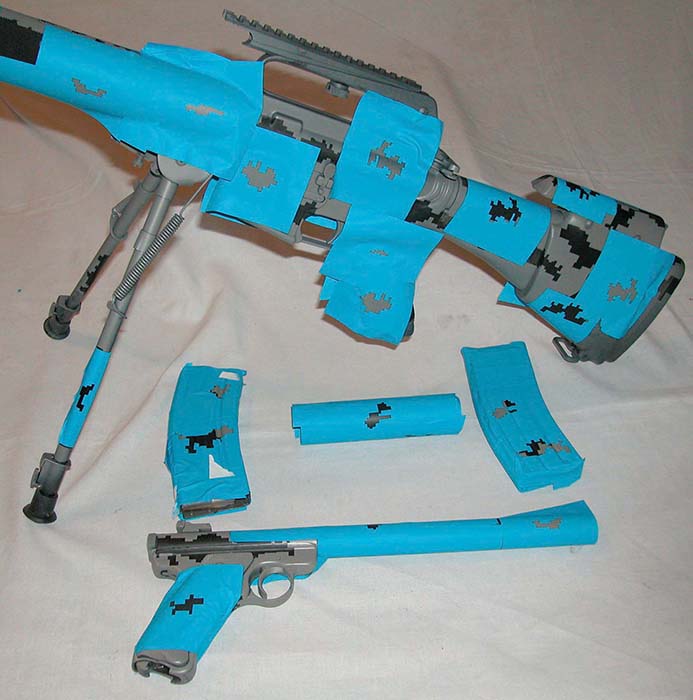
Approximately an hour after spraying this final layer all the templates and masking were removed. Everything was allowed to dry overnight and was rubbed down with a protective layer of DuraLube as a protectant.
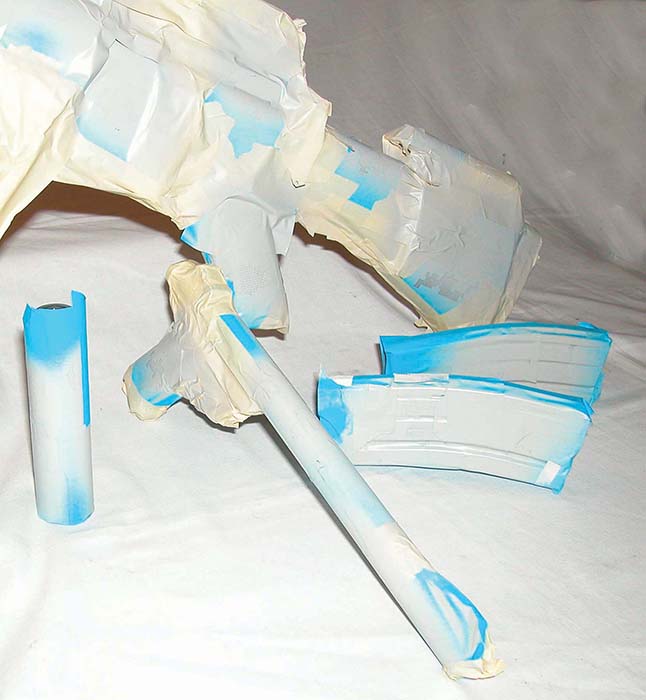
To say that I was delighted with the results would be an understatement. The finish looks great and everything looks far better than imagined. One thing is for sure, and that is the DuraCoat is a complete system that is simple enough for anyone to apply.
After asking Steve Lauer to critique the job, he offered the following advice. He said to pay particular attention to the direction of the lines of the templates when using any of the digital template sets. The rifles, (particularly the AR-15 and M16 family) tend to look their best when the horizontal lines are all parallel to the bore. He reaffirmed the importance of removing all oils and lubricants before beginning. There needs to be a clean, dry surface to start with in order to achieve a good end result.
DuraCoat can be heat cured if timing is critical but it is not necessary. For the purposes of our test application everything was allowed to air dry only. DuraCoat will resist temperatures as high as 600° F and lower than any temperature ever recorded. Those requiring a finish on machine gun parts and suppressors that will reach high temperatures should use the DuraHeat products in place of those above. These high temperature coatings are able to withstand temperatures of up to 1,800° F and even become harder at these high temperatures.
Other LCW Products
There are several finishing products available from Lauer Custom Weaponry. A quick glance at their website or catalog will reveal many items for almost all firearm finishing tasks. Some of these other items include parkerizing solutions, bluing removers, wood stains, drying ovens, solution tanks, bead blasters and much more. Lauer Custom Weaponry is also a Title II Manufacturer who sells their own LCW-15 rifle and several models of sound suppressors. For those who may desire one of the many DuraCoat finishes offered but do not have the time, facilities or even the interest in doing it, LCW will do the work for you. You should contact them directly for pricing on each individual job. Retail pricing for each firearm typically varies from $275 to $575 depending on the colors and patterns. Turn around time is usually 4 to 6 weeks. Classes to become a certified DuraCoat applicator are regularly offered so gunsmiths, manufacturers and refinishers can learn to professionally apply the DuraCoat products.
A few other interesting products in the LCW finishing line include DuraFill and DuraCoat Texturing. DuraFill is applied over areas with imperfections like pitted metal or rough wood and can be built up before being finished with DuraCoat for a smooth finish. DuraCoat Texturing can be used to texture stocks and pistol grips and may be used in conjunction with the other DuraCoat products as well.
Summary
With a starting cost of $49.95 on the LCW EZ Finishing Kit, almost everyone who owns a gun can afford to upgrade or update it without dipping too far into the ammo fund. The number of color and design combinations are endless, and are only limited by the imagination of the applicator. The system is simple and easy to apply and the time necessary to complete a project can be broken into several parts or completed right away if desired. The complete packages are made up of everything necessary from the airbrushes to the templates and the instructions are easy to follow. All the creativity necessary is the desire to have a new look and LCW has thought of the rest. I highly recommend the DuraCoat Gun Finish to anyone who is interested in taking on a small task with the possibility of exceptional results.
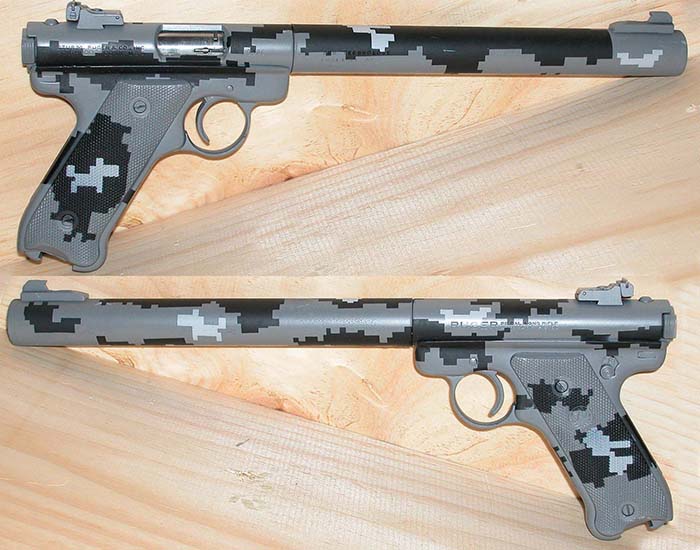
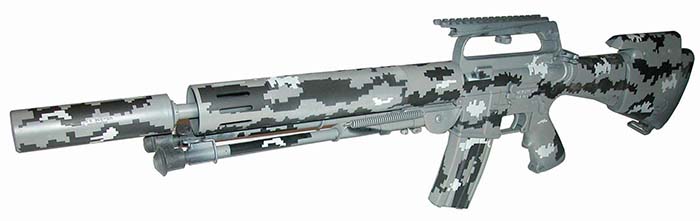
Lauer Custom Weaponry
Dept. SAR 3601 129th Street Chippewa Falls, WI 54729 Phone: (800) 830-6677 Fax: (715) 723-2950 www.lauerweaponry.com
This article first appeared in Small Arms Review V9N10 (July 2006) |