By Christopher R. Bartocci
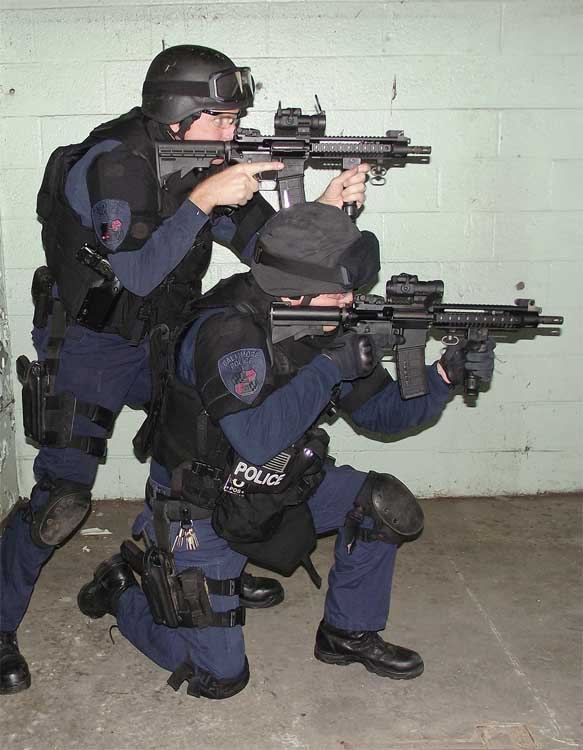
It has been a decade since the war on terror began and from these two wars the infantry equipment was put through the ultimate test, combat in the desert. Around 2004, requirements came out for a new rifle to replace the M4 carbine due to malfunctions in the field. The talcum powder-like sand caused the weapons to malfunction at critical moments. Although there was no official requirement to replace the M4/M16 series weapons from the Army, there was from SOCOM as well as a number of soldiers. Enough so Oklahoma Senator Coburn put pressure on the Army to see if in fact the M4 was the best weapon available to the U.S. soldiers. Due to this pressure the Army conducted Dust Test II where the current M4 carbine was tested against the FN SCAR Light, H&K 416 and the H&K XM8. The test showed the current issue M4 to be the least reliable, by far. The test consisted of 10 each of the rifles and firing 60,000 rounds per model. The end result was the XM8 had 127 stoppages, the FN SCAR Light 226 stoppages, the HK416 233 stoppages and the current issue Colt M4 carbine 882 stoppages. Clearly there is a large gap in stoppages seen between the newer carbines and the standard. The results of this test were questioned by both Colt Defense as well as some in the Army but the results stand. This got congress and the army to initiate two different actions. First was a short term M4 Product Improvement program consisting of three phases. Phase one is procuring 25,000 new M4A1 carbines with heavy barrels, full auto capability and ambidextrous controls. This is to deal with the overheating problems encountered in combat in the desert and the decrease of individual firepower by eliminating the burst setting for fully automatic. Phase II is an open competition for a new and improved bolt carrier group and forward rail. The current OEM of the M4 has not provided this since the rifleโs inception, the only real advancements in the bolt carrier group to increase reliability was a new extractor spring. COTS (Commercial Off The Shelf) manufacturers have developed significant leaps in technology in advancing the bolt carrier group such as the LMT Enhanced bolt carrier group and the Knightโs Armament Company (KAC) E3 system (Enhanced Reliability, durability and maintainability) bolt carrier/barrel extension system. The current KAC M4/M5 RAS is a good system but it is outdated in comparison to many new COTS designs, some of them are from the OEM (Original Equipment Manufacturer) KAC including the URX system. Phase III is an operating system review to see if there is a better more reliable gas system for this weapon platform. This is the major issue. Most of the issues surrounding this debate center on the operating system. Is direct gas impingement as reliable as or less reliable than the standard short and long stroke piston designs.
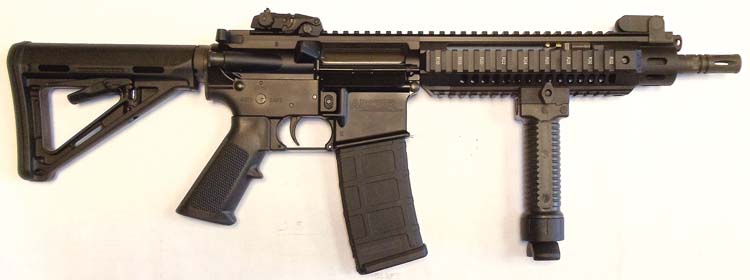
To review the systems, the direct gas or gas impingement system uses a gas tube attached to the front sight block to transfer gas from the gas port, into the tube, back into the bolt carrier where the expansion chamber is made up of the back of the bolt and the back of the bolt carrier. As the pressures increase, the bolt carrier moves rearward until the cam pin is rotated in the cam track of the bolt carrier to unlock the bolt and extract and eject the cartridge case. The benefits of this system is the minimum of moving parts, in-line construction decreasing recoil, little affect on the barrel harmonics increasing accuracy over standard piston designs. The disadvantages include carbon deposits being carried and deposited in the bolt carrier group fouling the bolt carrier group. Due to the hot gasses going into the carrier excessive heat builds up in the receivers. Reliability decreased in the carbine systems, failures to extract due to the bolt unlocking and extraction beginning while the cartridge case is still obturated and maintenance being more frequent than other comparable battle rifles. Also cycle rate increases with gas port erosion.
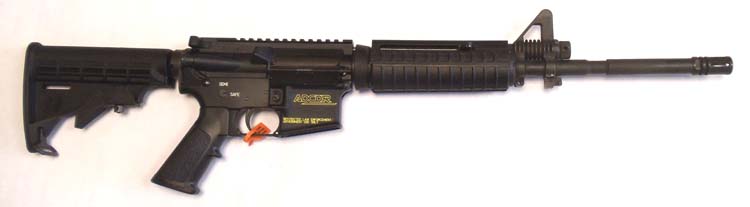
The short stroke tappet piston design is used by most of the major competitors for the new carbine program. There is a gas block attached to the barrel where an operating rod sits whether the end of the rod is the piston or there is a separate piston. Gas tapped from the barrel strikes the piston (operating rod) driving the operating rod rearward striking the face of the bolt carrier (or impact location) driving the bolt carrier to the rear. The operating rod then moves forward by spring tension back into its position in the gas block. The benefits are no heat is transferred back into the receiver, no carbon or debris is blown back into the bolt carrier group causing fouling and the bolt stays significantly cleaner hence will run much longer between cleaning. The negative parts of this system are extra weight, more moving parts, require more gas pressure to operate, carrier tilt/twist, negative effects on accuracy due to the gas block on the barrel and higher cycle rates.
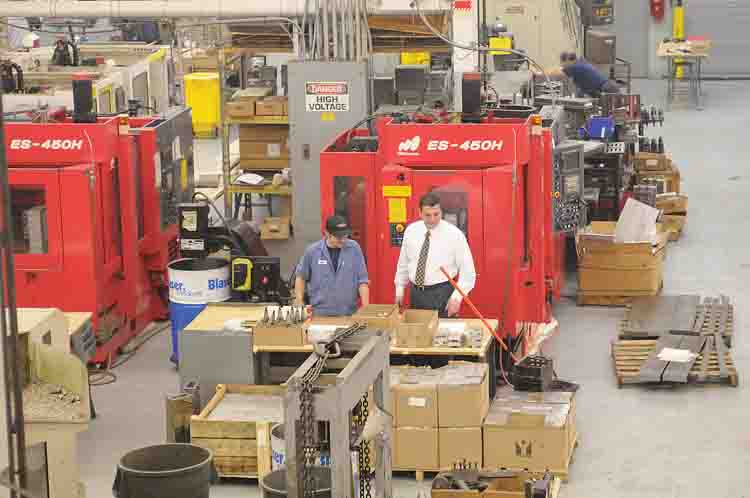
ADCOR Industries goes back to 1966 when Konstantinos Stavrakis, a Greek immigrant, bought his first lathe in Baltimore, Maryland. The struggling business was bought in 1990 when 23 year old Jimmy bought the business from his father and began ADCOR Industries. ADCOR is used to manufacturing high tech aerospace components such as components for the F16 fighter, U.S. Navy ballistic missiles as well as tools for the Hubble telescope. Currently one of ADCORโs leading projects is in the high speed bottling industry, all over the world. These high-speed bottling machines can bottle or can up to 2,000 12 oz cans or bottles per minute ยฑ1/10 grams of precision. These machines have more than 20,000 part numbers. The stack up tolerances must be precise for these machines to work properly. In the bottling business today more than 80% of everything bottled in North and South America is bottled on ADCOR machines. ADCOR employs 160 people in their 65,000 square foot Baltimore plant. ADCOR Industries is a state-of-the-art manufacturing facility with all modern CNC machinery, automated inventory control and a quality control laboratory worth several million dollars. To say ADCOR is brand new to the firearm business is not really correct at all. They manufactured up to 1,000 upper receivers a day for Colt Defense for their M4 carbines and other rifles including their difficult to manufacture 1-piece upper receiver. They began with the raw forgings and machined them to the point of them being shipped to be anodized. They also manufactured the heat sink on the Colt Infantry Automatic Rifle which was submitted and lost to the H&K416. Colt currently sells their IAR to law enforcement and international military. ADCOR Industries is AS9100 certified, which is the highest quality certification in the world. How Jimmy Stavrakis manages his family with four children, ADCOR Industries/ADCOR Defense and two Baltimore restaurants is a mystery; let alone taking on a new venture in the firearms industry.
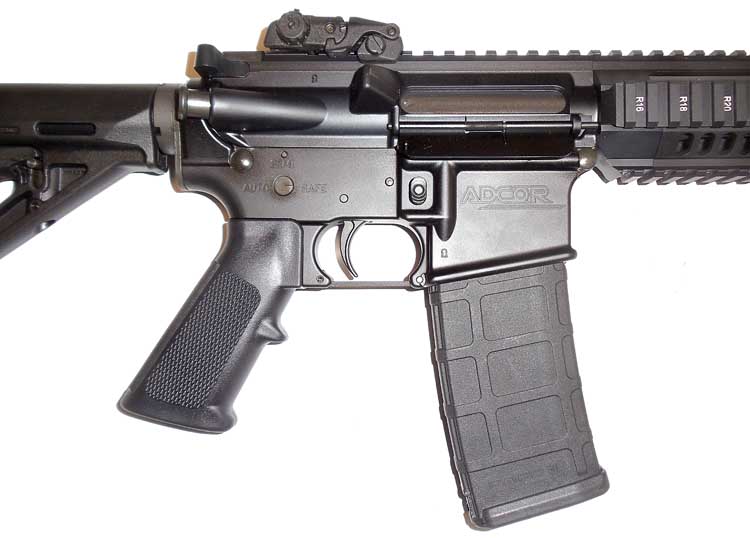
Jimmy and designer Michael Brown heard of the malfunctions with the M4 through the news and internet and saw exactly what the Army was looking for in a more durable and reliable weapon. After speaking with representatives from the Army, they decided to look at the problem and see if they could help the Army and provide the best weapon system to the American warfighter. Brown is an engineer by trade and never worked in the firearms development industry. In but 30 days time, he developed a revolutionary new weapon system which meets and exceeds what he was asked to build. By Brown not being from the firearms industry, he was not poisoned by the way things were always done as many in the industry are. Looking at most of the modern assault rifles they are very similar to each other with very minor changes. Starting with a new sheet of paper and a set of requirements Brown developed the B.E.A.R. (Brown Enhanced Automatic Rifle). The BEAR was shown to the industry for the first time at NSGW in 2010.
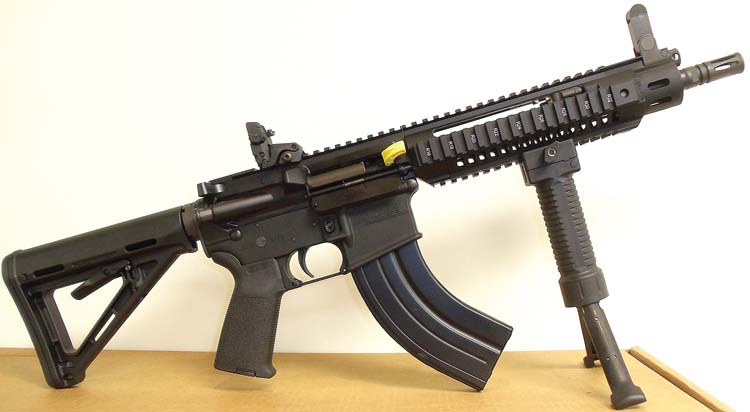
The BEAR upper receiver is unique compared to any previously fielded weapon system. It is very evident that the government is looking for a different operating system than the current direct gas impingement. They were looking at a weapon with the benefits of a piston operated rifle. However the direct gas impingement has some benefits as well. The BEAR takes the best of both worlds. Unlike the standard long and short stroke piston designs there is no large and heavy gas block added and pinned to the barrel causing decrease in accuracy due to the interruption of harmonics caused by the pinned-on block and the functioning of the piston and or operating rod impacting the gas block. Direct gas systems are known recently to have free floating barrels. The gas tube design puts very little stress on the rifle since it just taps the gas off the barrel and leads it to the carrier key. What if you could make a piston system do the same thing? The gas system is not pinned in place on the BEAR. The gas tube is attached by a light gas block to the barrel and the gas tube is horizontal and flat. The piston base is not attached to the barrel but the receiver. As the piston base is slid into the upper receiver the gas tube on the barrel slides into the piston block. The block it held into the receiver by a pin which is locked in place by the hand guard. Contained in the piston block is the piston and spring. ADCOR offers two piston bases. One which has a folding front sight attached and another that is flat for use with lower laying optics. In front of the piston is the gas plug which is held in place by a spring loaded detent pin. The gas plug is a critical part of what makes this system so different from the rest. The amount of gas bled into the system is not based on the gas port diameter in the barrel. On the direct gas impingement platform, the erosion of the gas port in the barrel causes a higher cycle rate and in turn failures to extract as well as parts breakage toward the middle and end of the rifleโs life. The gas plug on the BEAR determines the amount of gas entering the system. There are two gas ports on the plug. Depending on the ammunition it can be set for lower power .223 Rem or to the higher power 5.56mm ammunition. The cycle rate is kept in the 700 to 800 rounds per minute eliminating the need for a special H or H2 buffer. This holds true regardless of the length or thickness of the barrel. For military versions, the gas plugs has two settings as well, one for normal condition and the other for suppressed conditions. Suppressed is a very difficult condition for the conventional gas impingement operated rifle. The suppressor causes an over pressure condition in a system which is already high on the pressure spectrum. The cycle rate is driven up significantly higher when suppressed causing severe wear on the bolt mechanism including the extractor spring and much faster wear on parts as well as severe gas being blown back into the shooters face. The direct gas M4 does not have any adjustment to lessen the gas pressure taken into the system so it will run significantly faster with a suppressor. So no matter the extent of gas port erosion, the amount of gas and the cycle rate remain consistent throughout the life of the rifle. The gas system on the BEAR prevents higher cycle rate from gas port erosion, consistent cycle rate throughout the life of the weapon system, adjustments in the field to pick between using the rifle suppressed or not suppressed, does not transfer heat back into the receiver and does not direct residues from the gas to and deposit them in the bolt carrier group.
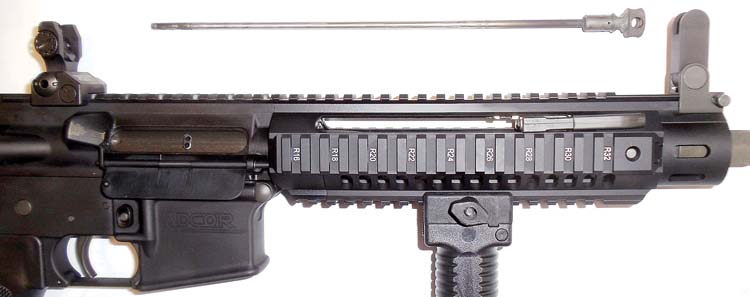
The bolt carrier group on the BEAR is also redesigned to meet and exceed military requirements. The operating rod is attached to the carrier by the location of where the carrier key would normally go. It is held in place with two slots and then screwed into the bolt carrier assembly and the two screws are pinned in place. This corrects another problem found in having piston mechanisms in the M4 platform. On a standard short stroke tappet piston system in an M4, the operating rod strikes the carrier to drive it rearward. Due to the location of the impact point on the carrier the back rear bottom of the carrier tilts downward digging into the receiver extension. This is called carrier tilt. Many manufacturers have inserted skis on the bottom rear of the carrier to deal with this condition. It certainly improves the condition but does not eliminate it. The ADCOR system uses a long stroke design which evenly pushes the carrier to the rear keeping it inline the way the rifle was designed with no tilt. The rod actually guides the carrier to the rear keeping perfect alignment with the receiver extension. Another improvement to the carrier group is what ADCOR calls the Dust Wiper. Reading and hearing about the sand and debris that would enter the M4 through the three gas exhaust ports on the right side of the carrier would cause significant malfunctions if the dust cover was not closed. Also, when firing the rifle dirt can enter the mechanism due to the port cover being open. The engineered high heat resistant polymer dust wiper keeps the ejection port sealed at all times. The only time it is open is when the bolt carrier group is to the rear. When closed there is no way for dust, dirt or sand to enter the mechanism. The BEAR uses a standard M4 bolt, cam pin, firing pin and firing pin retainer pin. The carrier itself is chrome plated for easier cleaning.
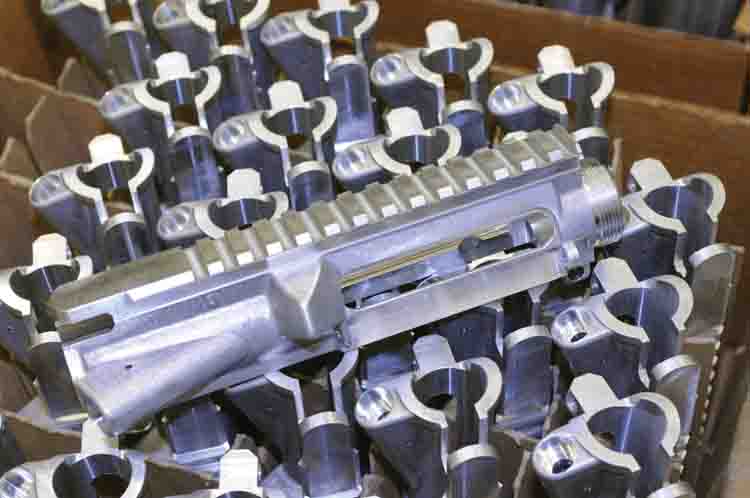
The upper receiver is a standard M4 upper with a modified detent in the fired cartridge case deflector to use the polymer dust cover. The upper has a forward assist. The front handguard locks into the upper giving a continuous top rail. The BEAR has a forward charging handle/forward assist which is reversible to either the right or left side. The bolt carrier can be actuated as well as if need be the forward handle can work as a forward assist.

The barrel is a cold hammer forged 1/7 inch twist manufactured by FN. The barrel is chrome plated and manganese phosphate finished. The FN machine gun barrel will give a longer service life compared to the standard button cut barrel of the current M4 carbine. All barrels are proof tested and magnetic particle tested. ADCOR gets barrels in 10.3, 14.5, 16 and 20 inch lengths. ADCOR has manufactured prototype barrels and will soon release BEAR rifles chambered in 7.62x39mm and 6.8mmSPC calibers. Brown is currently also working on a 7.62x51mm version of his BEAR rifle.
The lower receiver is stock M4-type. ADCOR manufactures their own lower receiver which contains a Magpul MOE pistol grip and stock. The stock has six positions rather than the standard 4 of the M4 carbine. Currently ADCOR is working on making the magazine and bolt catch ambidextrous.
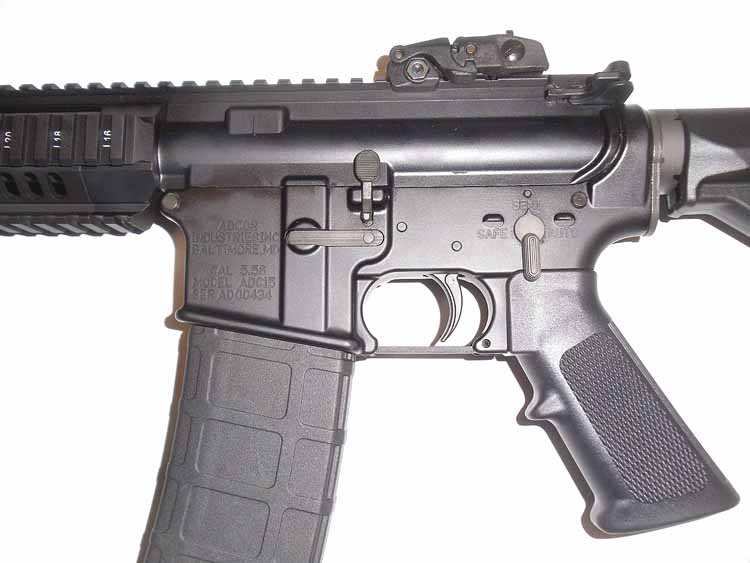
The BEAR has been independently tested at White Laboratory in compliance with portions of the first Article Test Matrix, Carbine, 5.56mm, M4. Two were submitted by ADCOR with a total of 12,000 rounds fired of M855 Ball. Each rifle was fired in 120-round cycles consisting of:
- 30 rounds in automatic mode in bursts of approximately 5 rounds each
- 30 rounds in automatic mode in a single burst
- 30 rounds in semiautomatic mode at a rate of 10 to 30 rounds per minute
- 30 rounds in semiautomatic mode at a rate of 10 to 30 rounds per minute
The rifles were cooled and lubricated every 500 rounds. There were no stoppages of any kind during the testing. Accuracy/dispersion showed an extreme spread of 2.88 inches with M855 and four groups with Federal Match (69gr) ammunition gave a mean extreme spread of .88 inches. Also some adverse firing testing was conducted including the rifle was completely buried in play sand and submerged in five inches of water and fired a magazine of 30 rounds with no malfunctions. This is a significant test due to the fact a direct gas impingement M4 carbine must have the bolt open and the water seal broken and water drain out of the barrel before it can safely be fired. The ADCOR rifle can be removed from the water and fired without having to drain the barrel first.
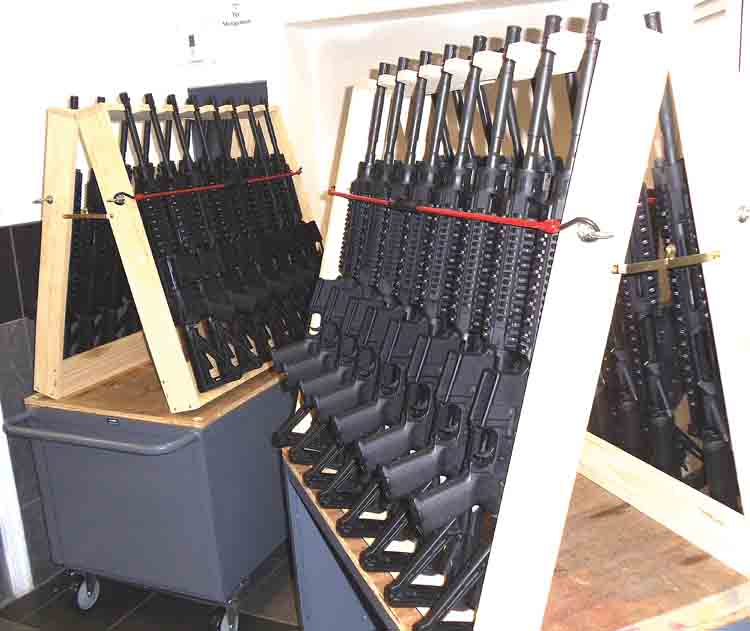
For those who are through and through direct gas impingement fans, ADCOR has a rifle for you. Knowing that there are those who prefer this method of operation ADCOR took their basic design and made some modifications. A straight gas tube is attached to the gas plug. The gas plug can be rotated 360ยฐ for either suppressed or unsuppressed fire. The bolt carrier group has been slightly modified. A carrier key is used which sits slightly higher than the standard M16/M4 key due to the ADCOR receivers. Two gas vent holes were added to the right side of the carrier. These holes are seen through a hole in the dust wiper. Another area Brown dealt with is the issue of carrier keys coming loose, causing gas leakage and eventual short stroking. Not only are the carrier keys torqued and staked, the screws additionally are locked in place with a roll pin on each screw. By the BEAR receiver design you can switch between the piston and direct gas impingement systems using the same barrel. By using the gas plug the gas is regulated so gas port erosion will have no effect on the cycle rate of the rifle. The dust wipers will prevent debris from entering the side of the receiver.
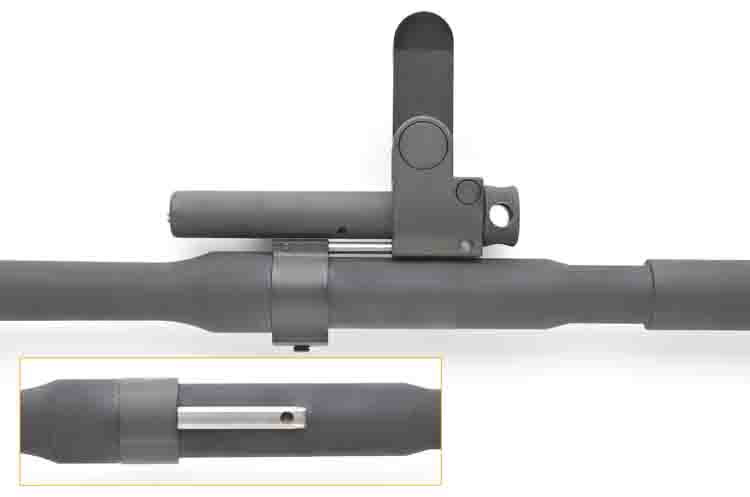
The rifle provided had a 16.1 inch FN produced 1/7 inch twist chrome lined barrel. It came with both front sight piston base as well as a standard piston base. It was provided with two Magpul PMags. It also came with a set of Magpul folding front and rear sights. All that was added to it was a KAC vertical pistol grip, an Insight Tech tactical light, an EOTech sight and Norgon ambidextrous magazine release button.
At the time this rifle arrived I received some of the new Lancer L5-AWM (Advanced Warfighter Magazine) magazines. This author has known these magazines since their early prototype stages they made with Colt Canada. The โgreenโ magazine was to be a joint venture which Colt dropped out of and Lancer continued development of an advanced translucent magazine. Throughout the development different materials, different floor plates and capacities have been introduced. Currently Lancer Systems offers 5, 10, 20, 30 and 48 round magazines. The AWM is the next generation; there is significant change to the metal feed lip inserts. It is now one-piece and it wraps around the rear of the magazine extending to the forward edge of each side. The magazine has a ruff texture on the bottom to aid in handling in adverse conditions. One of the other most significant changes to the AWM is the floor plate. It is not hard plastic, rather it is rubber so it will not snag on clothing and pouches. And finally, you no longer need tools to disassemble and clean. You merely take a cartridge tip or suitable tool and push inward on the lock plate and the magazine disassembles for maintenance. The magazine features Lancers anti-tilt follower as well.
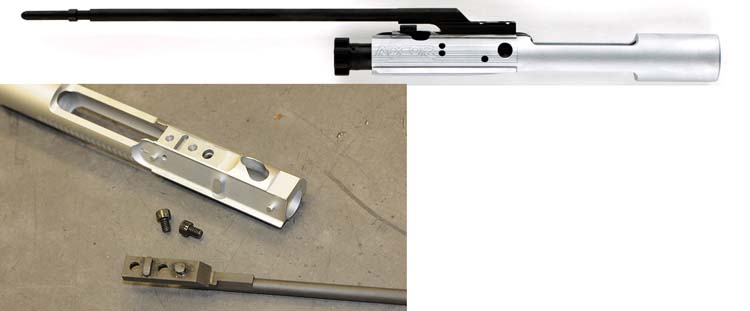
The test rifle has been fired over 1,200 rounds of M193 ball ammunition and 100 rounds of Silver State Armory 5.56mm 69 grain OTM ammunition. All testing was done at 100 yards for accuracy. The groups with the Silver State Armory ammunition ranged between .80 and 1.25 inches. Tactical drills from 10 to 50 meters were quick and accurate.
While visiting ADCOR in their Baltimore office I had the opportunity to fire several other models of the BEAR weapon system. With Mike Brown and Jimmy Stavrakis diligently reloading magazines, I fired more than 300 rounds in a select fire 10.3 inch BEAR rifle. Having extensive trigger time on the MK18, there was a significant difference in controllability between the two. Recoil was much more manageable on the BEAR. Perhaps the lower cycle rate had much to do with it. The impulse felt lighter. The BEAR 14.5 inch rifle was just as pleasant firing nearly 180 rounds through that model. The next and most interesting was a suppressed 16 inch BEAR. This was extremely sweet to shoot. Due to the piston system, far less gas came back to hit me in the face. The only thing this rifle needed was a Precision Reflex Industries Gas Buster charging handle and it would be good to go. More that 600 or so rounds were fired, mostly on fully automatic without a single malfunction. Two members of the City of Baltimore SWAT team were there test firing and picking up their BEAR rifles for their team. In asking them about their testing results they claimed the BEAR rifle was the best of all the rifles they tested and look forward to procuring more in the future. ADCOR Defense has shipped out recent test and evaluation units to the FBI.
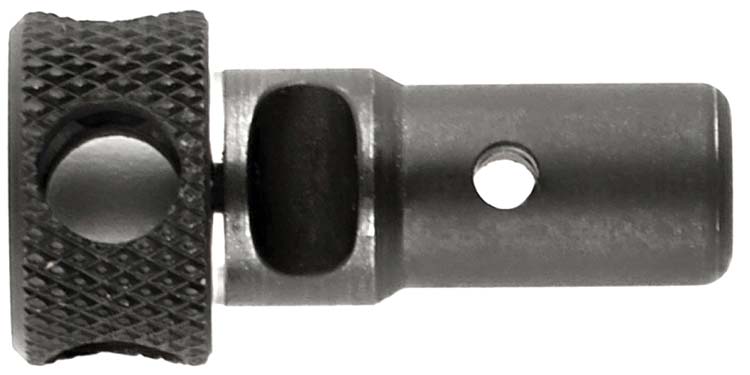
The U.S. military has stated they see no need to replace the M4 carbine unless there is a โsignificant leap in technology.โ Although several of the competition rifles display enhancements in reliability and durability over the M4, there just has not been enough to warrant a change. Significant leap in technology is very open ended and leaves much to interpret. The BEAR rifle will be in the run for the gold this summer. When looking at the BEAR, it has everything the Army has asked for. The accuracy of the direct gas, the cleanliness of a piston, forward charging handle, no carrier tilt, free float barrel, more durable barrel, ability to convert existing weapons, significant number of parts compatibility, easier to maintain, more reliable in adverse conditions and American made. With all the political pressure from those in Congress as well as certain segments of the military there is a very good chance the M4 will be replaced with a better weapon. The question is how long will it take and another important question is do we have the money for such a transition. It only makes sense to go with a better system that can retrofit existing service rifles. We will have to wait and see how it all turns out but the ADCOR BEAR will be a solid contender.
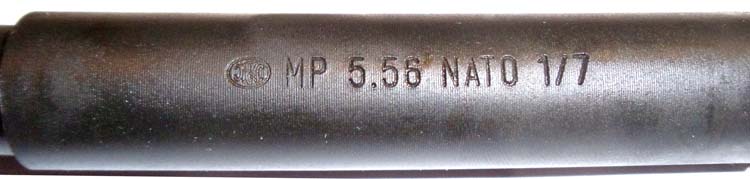
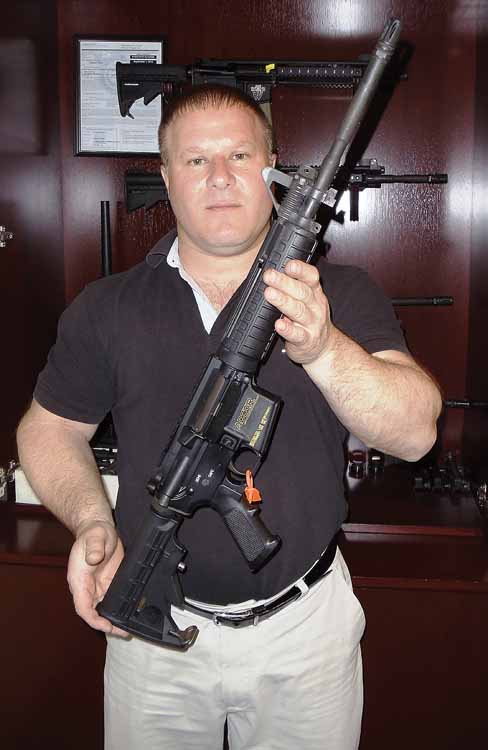
This article first appeared in Small Arms Review V16N1 (March 2012) |