By Frank Iannamico
On October 19, 1960, the U.S. Army announced the testing and evaluation of a new 40mm grenade launcher designated as the “XM79.” The weapon was designed to fire a high explosive (HE) shell at a muzzle velocity of 250 feet per second, at a range out to 400m (410 yards), when launched with a barrel elevation of approximately 35 degrees. Confirmatory testing of the XM79 started at Fort Benning on June 27, 1960. As a result, there were several changes made to the original design.
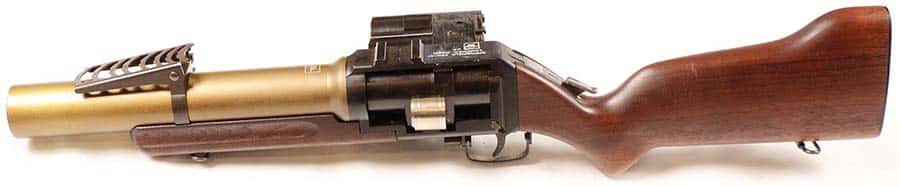
Specifications
The Infantry Board declared the original “ladder”-type rear sight unacceptable. A new rear sight for the M79 launcher had to be designed and fabricated.
The Research and Development Department at the Springfield Armory initiated the design and fabrication of a new rear sight. The (somewhat intricate) new rear sight, part number 7791038, is made up of 22 separate parts. Since high elevations were required, it was graduated to 375m and adjustable both for elevation and windage. The sight design was completed, and production commenced in October 1960. All launchers produced up to June 1960 had to be retrofitted. This new requirement, occurring late in the program, involved additional procurement, rescheduling and overtime in order to meet the Ordnance Readiness Date of March 31, 1961, and the delivery requirement of 2,056 launchers by July 1961. Other recommended changes were made to the barrel locking lug, trigger spring and front sight.
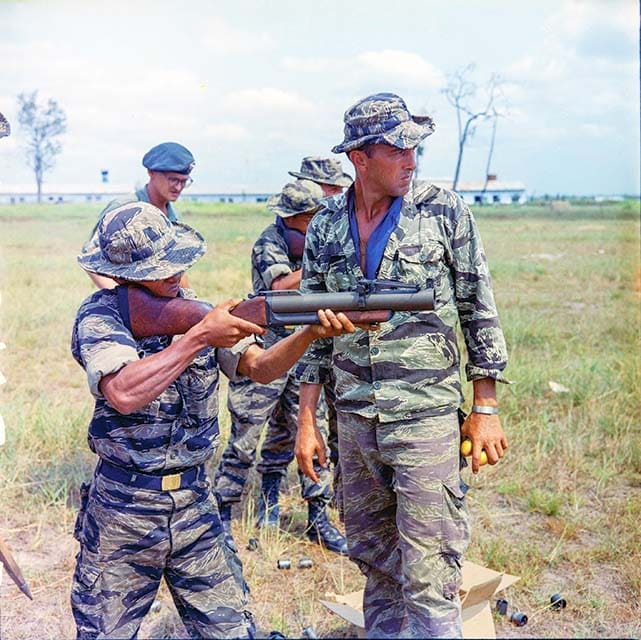
Circa 1967, U.S. Army Special Forces Advisor Staff Sergeant Alvin J. Rouly instructs a Vietnamese Civilian Irregular Defense Group (CIDG) trainee on how to use an M79 grenade launcher. In the Sergeant’s left hand are several 40mm HE (high explosive) grenades.
Early proposed designs for the grenade launcher were identified by a letter “S” representing the Springfield Armory. The Infantry Board at Fort Benning stated a preference for a semiautomatic, multiple-shot grenade launcher. The Springfield Armory designed a three-shot launcher, designated as the “S-6 T148E1” (not to be confused with the XM148 underbarrel launcher), that achieved semiautomatic operation through the use of a magazine made up of three chambers, each long enough for a cartridge 4.5 inches in length. The magazine would move to the left after firing by a constant force of a negator spring. As each round was fired, a latch detected the launching of the projectile and allowed the clip to move over until stopped by the next projectile, lining
up that cartridge with the barrel. Although the basic concept was simple, the mechanism proved to be too complex and was unreliable. Repeated misalignment between the projectile and the bore created gas leakage and a loss of accuracy. Special purpose rounds, such as CS gas or signal flares with a longer overall length, could not be used. A much simpler design, designated as the “S-5,” was a single-shot, break-open type weapon. The S-5 evolved into the XM79 in 1959 after the three-shot S-6 T148E1 project was canceled.
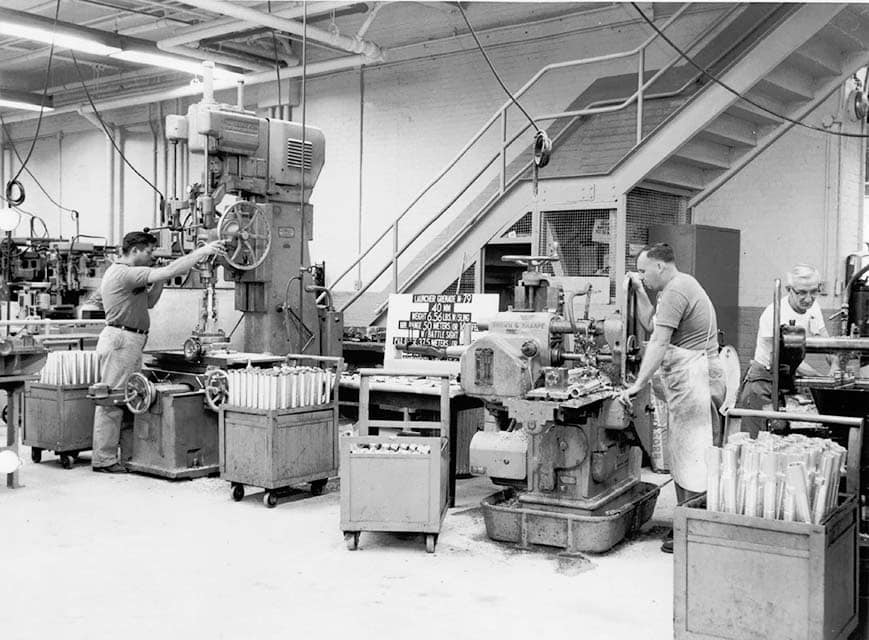
The M79 barrel and receiver production line at the Springfield Armory, Building 201.
The XM79-M79 action is automatically cocked and safety engaged on opening of the breech by a lever under the barrel. Trigger pull is single-stage; the trigger guard can be configured for winter conditions by depressing the front detent plug and pivoting the trigger guard to either side; thus, allowing the launcher to be fired with heavy gloves or mittens. The buttstock and forend are black walnut. A synthetic stock was developed for use in humid tropical climates. A synthetic foregrip was developed but not adopted. The stock is very straight and slightly concave on top, designed to get the recoil in line with the buttplate and to make it easier to fire with high sight elevation settings. To reduce the recoil to the operator, a rubber pad was fitted to the buttstock.
Official Classification and Development
On December 15, 1960, the XM79 became type-classified as: Launcher, Grenade, M79. It was adopted to give the individual soldier a mortar-like capability between the distance the hand grenade can be thrown and the shortest range of the mortar. The XM79 was the successful one of several competitive weapons developed for this requirement. At the time of adoption, it supplemented the M14 rifle and M60 machine gun. A pilot production program was started at the Springfield Armory to develop manufacturing methods, tooling and solve any production problems that may be encountered.
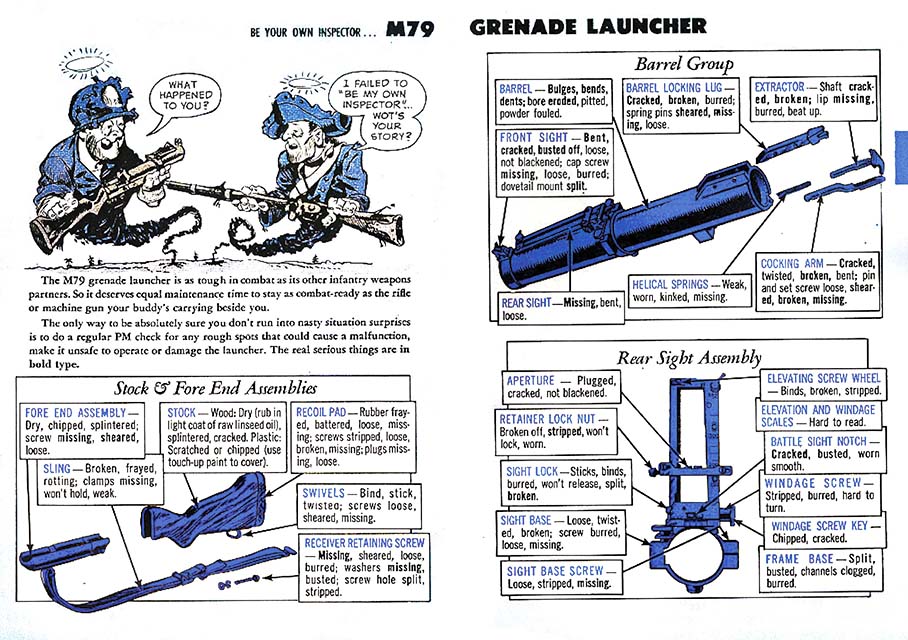
The M79 was developed at the U.S. Government’s Springfield Armory in Massachusetts. Armory engineer Dave Katz, under the direction of Cy Moore, was involved in the development program. Implementing a low-velocity round called for an unusual propellant system called the high–low type. Once ignited by the primer, the propellant’s expanding gases flow into a small high-pressure chamber. The pressure then bleeds through small holes into a larger low-pressure chamber immediately behind the projectile. The pressure in the low-pressure chamber is approximately 3,000 psi compared to 30,000 psi in the high-pressure chamber.
The M79 grenade launcher has 90 parts and is 28.6 inches in length; barrel length is 14 inches. Loaded weight is 6 pounds, 11 ounces; unloaded weight is 6 pounds, 2 ounces, making it light, short and handy. The receiver is made of steel. The barrel is an aluminum alloy finished by hard coat anodizing. Rifling is 6 lands .01-inches high, one turn in 48 inches. Use of an aluminum barrel is possible because of the low velocity and low pressure at which the projectile is fired and keeps the weight of the weapon down. The cost to the government was $318.00 per launcher.
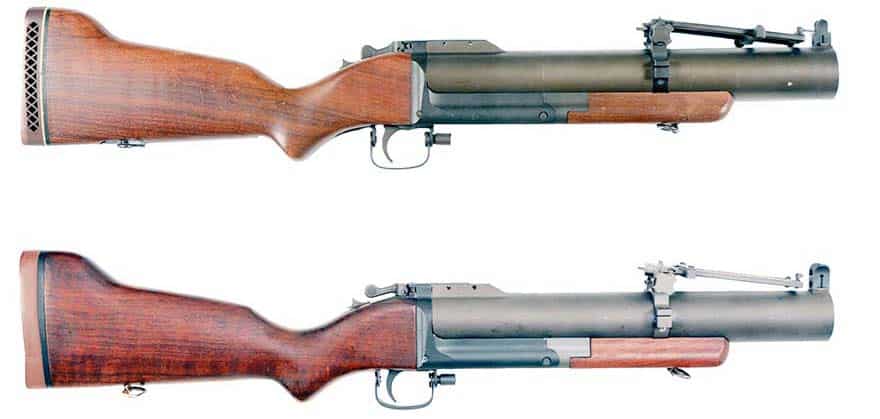
M79 Sights
The front sight is of conventional military pattern with side guards like those on the M14 rifle. The rear sight is a large, folding leaf, mounted on the barrel and is graduated to ranges from 75m to 375m in 25m increments and numbered at 100m, 200m, 300m and 375m. To move the sight carrier, push in the locking knob and slide the sight to the desired position. As the sight carrier is moved up the elevation scale, the rear sight is cammed to the left to compensate for the right-hand drift of the projectile. To lock the sight carrier in position, release pressure on the knob and turn it clockwise. An elevating wheel at the top of the sight frame is used to make fine adjustments. One click will move the impact of the projectile 2.5m at a range of 200m. When the sight is in a downward position, the fixed sight can be used to engage targets out to 100m. A knob on the right side of the sight is used to adjust windage; one click will move the impact of the projectile left or right 28cm (11 inches) at 200m. When raised the sight can be easily damaged. Despite all the features of the somewhat complex rear sight, it was seldom used in combat. Experienced grenadiers could instinctively place the rounds where needed.
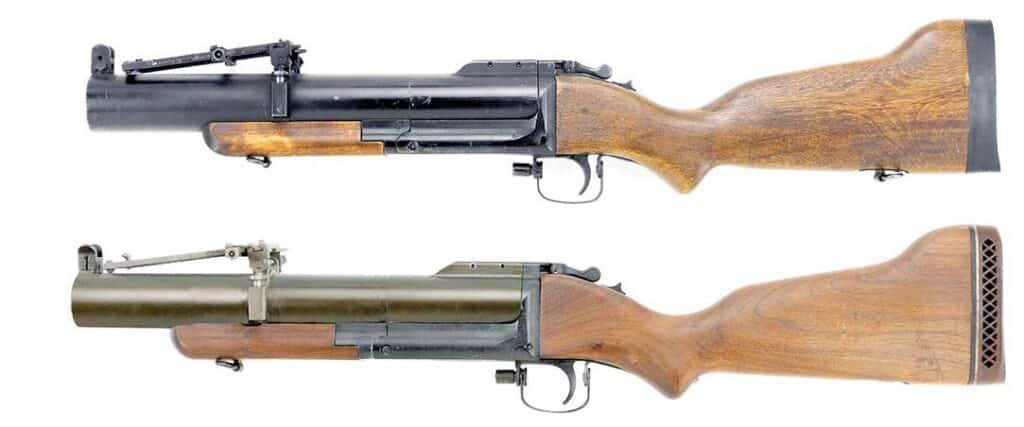
Other civilian companies that were awarded contracts to manufacture the U.S. M79 were Thompson Ramo Woolridge (TRW) and Action Manufacturing. Government records show that a contract was awarded to Exotic Metal Products, but it is unknown if any M79s were produced by that company. The Action Manufacturing M79 has an experimental shortened barrel.
Accessories
The M79 was issued with a small arms accessory case, which included a plastic lube container, combination tool and a pull-through cleaning brush with thong. Early carrying cases for the kit were made of a cotton-duck, which was later changed to mildew-proof vinyl. A sling that was issued for the relatively short M79 was the same one used for the M20 Bazooka (1055-00-714-5320); although an article in PS Magazine specified the small arms sling (1005-654-4508). Bandoleers were designed to carry six-rounds each; each pocket contained a plastic support, often referred to as “egg crates.”
Like the Bell UH-1 Iroquois (Huey) helicopter, the M79 became an icon of the Vietnam War; nicknames like the “blooper” and “thumper” were bestowed on the weapon because of the sound it made upon launching its payload. Another nickname was the “elephant gun,” due to its large 40mm (1.575- inch) bore.
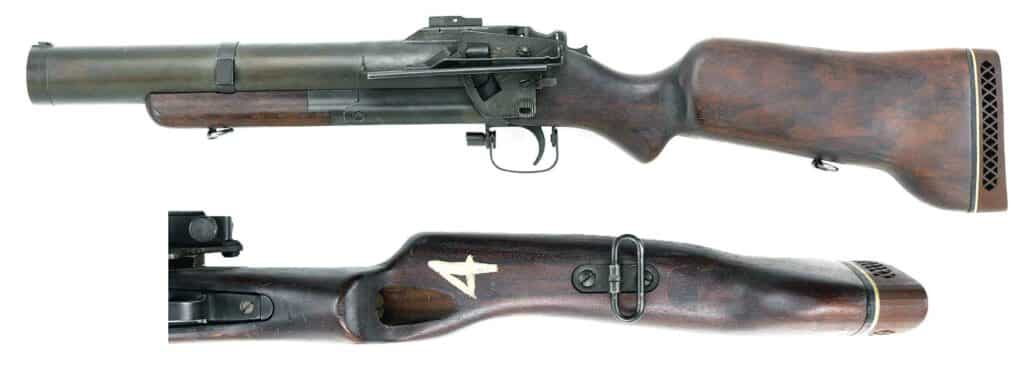
An experimental M79 buttstock designed to form a cheek rest. The launcher is a standard M79 with the sights removed and a tanget-type grenade launching sight attached to the side of the stock.
Contract Issues
As was done with the M14 rifle, the M79 was to be designed and placed in limited production at the Springfield Armory, but most of the production was to be awarded to civilian contractors. This caused a lot of animosity between the employees of the Springfield Armory and the government. During 1961, contracts were awarded to private industry for the manufacture of the M79 grenade launcher: Contract DA-11-1199-ORD-736 went to the Action Manufacturing Company, Bristol, PA; DA-l l-199-AMC-715 went to Kannar Corp., Kingston, PA. The Action Manufacturing Company contract was reportedly terminated in December 1965. Another contract DA-11-199-ORD-730 was awarded to the Exotic Metal Products, Pasadena, CA. Although Exotic Metal Products is listed in government records as a manufacturer, it is unknown if any M79s were produced by that company. During 1966, a new contract for M79 production was awarded to Thompson Ramo Woolridge (TRW).
Other subcontractors involved in the M79 project:
- Twin Cities Army Ammunition Plant for 40mm grenade fuzes.
- The AMRON Corporation for cartridge case metal parts for the M118, M406 and M384 40mm grenades.
- Crosley Avco and the U.S. Picatinny Arsenal for 40mm cartridges.
- General Tire and Rubber Company (GenCorp) for plastic M79 buttstocks.

40mm Ammunition
There were numerous rounds developed for the M79, which included: training and practice rounds, high explosive (HE), high explosive dual-purpose, CS gas, pyrotechnical signal, smoke, buckshot and spotting rounds. The HE 40x46mm rounds used in the M79 are quite complex. The actual grenade, slightly smaller in diameter than a golf ball, inside the 40mm case is smaller than its hand-thrown counterpart, the M26 / M61 grenades. Fragmentation for the M79 HE round is accomplished by internally segmenting the grenade body so that it fragments according to established lines. When detonated, the engraved lines on the steel body create hundreds of small, 2-grain fragments. The fragments travel at an initial velocity of up to 5,000 feet per second from the point of detonation. But the light weight of the fragments causes them to lose velocity quickly. This gives the grenade a limited casualty radius of only 5m (16.4 feet).
There are only 5.6 grains of M9 propellant used as a lift charge. The propelling charge is held in a cavity in the case head which has several small holes through its walls. It confines the powder gases and forces them to pass through the holes, controlling the burning. The design is bore-safe against premature detonation in the launcher. The fuze is armed after the projectile has traveled 14m to 28m. The shell fuze is a percussion type which initiates the burst on impact.
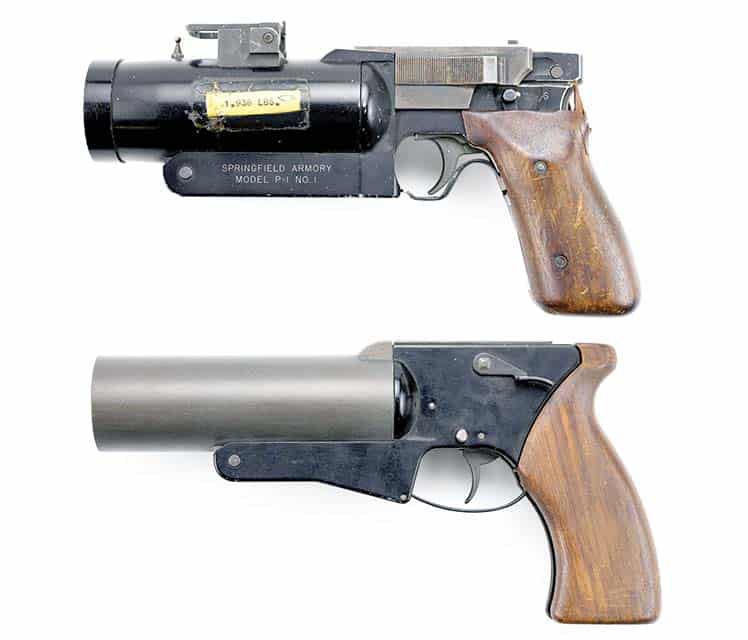
Disadvantages
The soldier or Marine armed with an M79 was at a disadvantage in enemy contact of less than 15m. The minimum arming range of some of the HE grenades, which, combined with its bursting radius, made the round ineffective and dangerous to friendly forces when used close-in during a sudden encounter with the enemy. To solve the problem, an anti-personnel round for the M79 was needed. The first of the close-combat rounds developed for the M79 was a “Beehive” cartridge loaded with 45 finned steel flechettes contained in a plastic sabot. The 10-grain flechettes resembled small nails with stabilizing fins. When fired, the plastic sabot holding the bundle of flechettes would break away soon after the projectile left the muzzle of the weapon, and
the flechettes themselves would spread into a widening pattern. But, as with most of the small arms flechette loads used in Vietnam, the flechettes were not stable at the muzzle of the weapon and usually weren’t flying straight and on point first until they had traveled about 15m to 30m. In close encounters, half the flechettes would hit a target sideways or backward limiting the effectiveness of the round. To make the M79 deadly in close contact with the enemy, a shotgun-type buckshot round was developed for the weapon in the 1965–1966 time period to replace the flechette load. The resulting M576 round was loaded with 20 #4 (0.24-inch) hardened buckshots contained in a small cup designed to keep the shot pattern reasonably close at 20 to 30 yards.
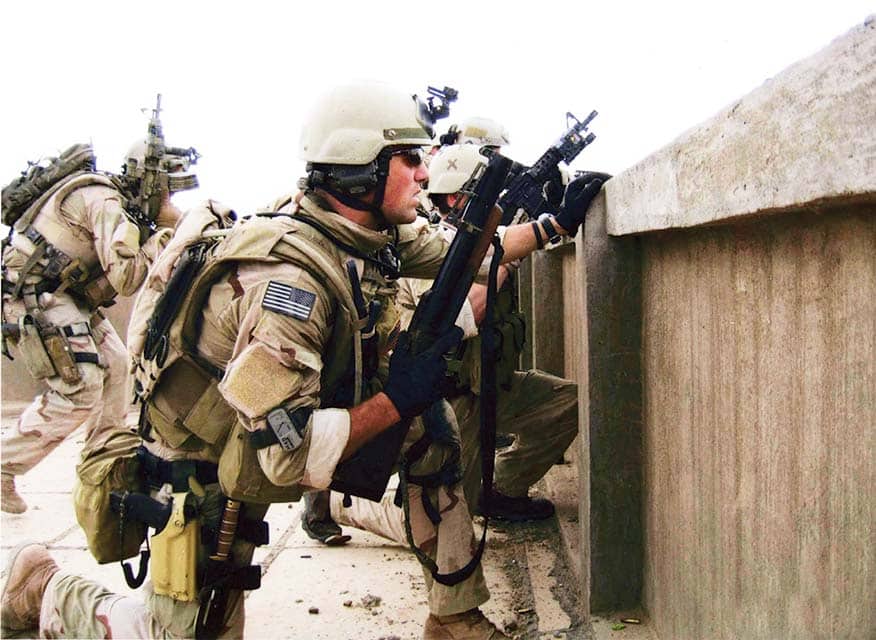
The M79 Grenade Launcher was in U.S. production from 1961 until 1971. Approximately 350,000 were manufactured before being replaced by the M203 launcher that attached under the barrel of the M16 rifle. Licensed production of the M79 by South Korea continued through the 1980s by Daewoo Precision Industries. The Socialist Republic of Vietnam reverse-engineered the M79, designated as the “M79-VN.” Unique features of that weapon include an optical sight and a maroon-color, fiberglass-reinforced plastic buttstock. Vietnam also refurbished and fielded the estimated 10,000 U.S.-made M79 launchers (and 175,000 40mm grenades) abandoned by the U.S. and South Vietnamese Armies. The Milkor M79 is a South African modernization of the M79 by the fitting of the stock, pistol grip and foregrip of the Vektor R4 assault rifle and a telescopic sight.
Although the M79 has been largely replaced by the M203 40mm underbarrel-mounted grenade launcher, U.S. forces recently have used the M79 grenade launcher in Iraq as an answer to neutralizing improvised explosive devices (IEDs). Most IED countermeasures have been high-technology electronic jamming devices sending out radio waves to either detonate or block IED electronic signals. However, not all IEDs are detonated with wireless radio-wave devices. Some are hard-wired to defeat attempts at electronic jamming. The M79 allows the stand-off distance needed to eliminate the threat and keep roads open for convoys.
M79 and M203 40mm grenade launchers are considered “destructive devices” by the ATF. Occasionally, original GI M79s can be found offered for sale, but they can be quite expensive. An unknown number of M203 and M79 MIL-SPEC grenade launcher receivers were made by Randy Shivak.
• • •
Special thanks to Curator Alex MacKenzie Springfield Armory National Historic Site.
This article first appeared in Small Arms Review V23N9 (Nov 2019) |