BY Paul Evancoe
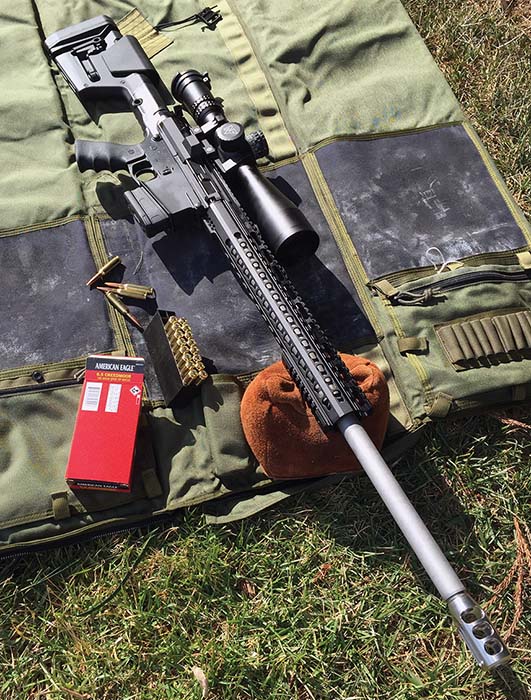
Bohemian Karel Krnka is credited with developing the first gas-operated rifle in the late 19th century. Krnka’s early design, further improved on and perfected by Hiram Maxim and John Browning, led to today’s gas operating systems. Today, there are two gas operating system designs used in self-loading rifles and machine guns: direct impingement and gas piston. Direct impingement disciples assert that gas piston systems are heavy, less accurate and mechanically unsound. Gas piston operating system devotees claim that direct impingement systems foul easily, overheat quickly and jam often. So, exactly what is the functional difference between these two self-loading operating systems, and what are their strengths and weaknesses?
To begin, the review of a few basics might be helpful. A self-loading firearm must mechanically execute a specific set of sequential functions automatically—without user assistance—to be classified as self-loading. The sequence goes like this: The shooter pulls the trigger and the cartridge fires. The operating system needs to automatically extract that spent cartridge case from the chamber, eject it from the firearm and re-cock the hammer/striker. It must then load an unspent (loaded) cartridge from the magazine (or linked belt) into the empty firing chamber. The breech is then locked closed (the bolt is locked) and the gun is “in battery.” At this point, the weapon is ready to fire again. Both direct impingement and gas piston operating systems complete this sequence by using the high gas pressure generated by propellant (gunpowder) combustion to drive mechanical motion that, in turn, automatically cycles the action of the firearm.
What’s the difference between the two systems? For the purpose of familiarity, direct impingement will be exemplified by the AR-15, and we’ll use the AK-47 for the gas piston system.
In the 1950s, American firearms design engineer Eugene Stoner designed the AR-10 (chambered in 7.62 NATO as a competitor to the M14) and, shortly thereafter, the AR-15 (chambered in 5.56 NATO), which both employed Stoner’s unique direct impingement gas operating system. A selective fire semiautomatic/full-auto version of the AR-15, designated by the U.S. Army as the M16, was adapted for military service in the early 1960s during the Vietnam War. Its lightness, ease of handling/carry and ergonomic design later led to the semiautomatic AR-15 civilian variant that has been extensively produced since the early 1980s. Notably, direct impingement is nothing new and has been widely used for both military—in automatic/selective fire M16 variants—and civilian semiautomatic AR-15 versions for over 50 years. The AR-15 is, perhaps, the most multi-caliber adaptable and easily customized gun design in the history of firearms, and that feat begins with its direct impingement gas operating system.
Here’s how the direct impingement gas operating system works. When a cartridge is fired, a small portion of the high-pressure bullet-propelling gas is syphoned off either through a small hole (port) located along the barrel (in what is called a gas block) or from a gas trap located at the muzzle of the barrel. Both pretty much do the same thing. As the bullet passes by, a small portion of the high-pressure gas generated from the combustion of the propellant is redirected rearward to power the direct impingement operating system.
Specifically, as the high-pressure gas is syphoned off (we’re talking gas pressure at thousands of pounds per square inch), it is channeled rearward through a small gas tube. The bolt-end of the tube directly impinges around a slightly smaller diameter tube mounted on the bolt carrier mechanism. The high-pressure gas essentially blows the bolt carrier mechanism rearward, extracting the spent cartridge case from the firing chamber. As the bolt carrier mechanism moves rearward, several other critical processes take place. The spent cartridge is ejected, the gun’s hammer is re-cocked and a recoil buffer spring is compressed.
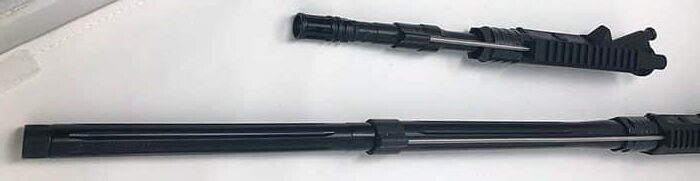
The buffer spring serves two critical purposes. It dampens the rearward impact of the bolt carrier mechanism and stops its backstroke travel. The compressed buffer spring then pushes the bolt carrier mechanism forward by spring-loaded action, stripping an unspent round from either a magazine or linked belt, loading it directly into the firing chamber and forcefully propelling the bolt back into battery (the bolt’s ready firing position known as “lock up”).
Therefore, as the direct impingement operating system cycles, extremely hot, high-pressure gas from the cartridge’s propellant combustion comes into direct contact with the bolt carrier mechanism with each and every shot fired. With it come unburned propellant, carbon residue and other nasty chemical and material contaminants resulting from propellant combustion. The consequence is rapid heating of the bolt carrier mechanism and bolt and partial sinking of that heat into the weapon’s upper frame and barrel. Extreme heat serves to break down most all lubricants necessary for the bolt carrier mechanism to function, which accelerates wear on the mechanism’s moving parts.
Whether founded or unfounded, direct impingement gas operating systems have a reputation for unreliability. While that claim is debatable in today’s ARs, most failure-to-feed malfunctions in direct impingement operating systems result from inadequate or improper lubrication of critical wearing parts, worn out buffer springs, worn out magazine springs (that no longer present the next round at the proper height for the bolt carrier to grab on the forward stroke) or the use of non-MIL-SPEC (undersize/oversize) ammunition. An unclean system is rarely the culprit for malfunction, unless fouling is allowed to accumulate regularly and not dealt with properly.
There are things you can do to reduce direct impingement operating system maintenance and reliability concerns. For example, use an upgraded nickel-boron-coated bolt and carrier set that is precisely machined from high-grade steel alloy. Nickel-boron provides a super-smooth, harder-than-chrome surface. This lubricious surface reduces friction to a minimum and is resistant to corrosion and abrasion. The slick finish also keeps carbon from adhering, which makes cleaning up much faster and easier than with standard steel parts. Another maintenance and reliability boon, in conjunction with the nickel-boron-coated bolt carrier group, is the use of a stainless steel or chrome-moly barrel. High-end ARs and parts, as described above, are readily available from a number of U.S. manufacturers specializing in new AR builds and replacement parts. In general terms, it’s okay to mix and match AR parts and assemblies, because they are built to AR-common MIL-SPEC tolerances (not so for gas piston systems).
As noted above, direct impingement operating systems require cleaning, proper lubrication and preventive maintenance. Parts within the operating system additionally require scheduled lifespan replacement to guarantee weapon system reliability.
There are also some lesser-considered factors that can quickly detract from direct impingement system performance and system reliability. While these factors are somewhat abstract to most, they deserve discussion. As mentioned at the front end of this article, Gene Stoner originally developed the AR-10 as a competitor against the M14. In that configuration, the AR-10 was designed with a 20-inch barrel length. Why 20 inches? There are several factors in play that merit discussion.
The laws of physics dictate that a projectile’s velocity cannot exceed the velocity of its propellant burn, assuming the propellant and projectile can be contained long enough to achieve a full burn. Additionally, propellant burn doesn’t just take place inside the cartridge case, which many might assume. The initial combustion begins inside the cartridge, but the rapidly expanding combustible gases continue to burn and expand right down the barrel, pushing the projectile/bullet up to optimal velocity as it exits the barrel. At the moment of exit, the bullet instantly becomes a ballistic projectile. This means every cartridge volume will ideally be mated to a barrel that has the optimal length for full propellant burn.
Barrel length is directly proportional to projectile velocity and optimal design performance. Because every round has an optimal barrel length, a gun’s barrel length plays several roles. Depending upon the cartridge being fired, the barrel length provides an extended linear combustion chamber necessary for the powder charge to fully burn and expand, so the projectile (bullet) being fired has time to reach its optimal velocity before exiting the barrel. This is to say that a barrel that is too long—one that exceeds the time/length required for a full propellant (powder) burn—serves no purpose other than to add weight to the gun. A barrel that is too short—one that doesn’t allow enough time for a full propellant burn—won’t provide the projectile its full velocity (ballistic potential) in terms of range or impact energy.
This leads us to the M16’s barrel length. Gene Stoner originally designed his AR with a 20-inch barrel to achieve maximum performance. However, since the first Gulf War, close-quarters battle (CQB) has been a common practice throughout the ongoing global war on terrorism. CQB is fought up close and dirty in restricted spaces generally associated with tight urban environments. CQB requires a short-barreled gun that can be easily wielded in tight spaces, and the M16’s 20-inch barrel was considered too cumbersome.
To better meet the new CQB operational environment, the U.S. Military adopted Colt’s M4 variant of the M16 in 1994. There was just one problem with the M4’s shorter 14.5-inch barrel length. The shorter barrel requires the gas port to be positioned further to the rear. The result of moving the gas port rearward is a decreased dwell time, which is the delay between the bullet passing the gas tube hole (the port where the gas is syphoned off for the operating system) and then exiting the barrel. The decrease in distance from the bolt face to the gas port in the M4’s 14.5-inch barrel resulted in a significantly increased port pressure. For example, the M16’s 20-inch barrel port pressure runs at around 10,000 pounds per square inch, while the short-barreled M4 has a port pressure of 17,000 pounds per square inch.
Gene Stoner didn’t design his direct impingement operating system to endure such high pressures and the resulting stresses. Also, 14.5 inches of barrel don’t provide the sufficient opportunity for full burn for the 5.56 NATO cartridge. In summary, changes in barrel length also changed the physics involved, which accounts for several somewhat negative consequences. Additionally, more unburned propellant gases/materials will exit the muzzle of a shorter barrel more quickly. As these hot combustible gases mix and become enriched with the atmospheric oxygen, they instantly ignite. The result is a bright muzzle flash from a short-barreled weapon. Likewise, the gas that is syphoned off through the port (gas block) to power the operating system on a short barrel is full of unburned combustible material and particulate contaminates. So, for direct impingement systems, it can be assumed that the shorter the barrel, the dirtier, hotter and less reliably it will operate.
There are remedies to help mitigate the problems inherent in short-barreled direct impingement gas operating systems, but one cannot beat the laws of physics. Since incomplete propellant burn is the basis for most problems associated with short barrels, a faster, cleaner-burning propellant can be used. This also has its negative consequences, since a faster burn rate always equates to more heat. Ammunition of this type can readily cause firing chamber and barrel throat erosion (permanent damage) not to mention excessive heating in auto-fire or semiautomatic rapid-fire mode. Excess heat can cause round “cook-off,” and that is unacceptable from a safety perspective.
Many short-barreled AR enthusiasts will add an adjustable gas block onto their gun to better control the gas volume syphoned off to the operating system. Adjustable gas blocks can be effective in controlling the cyclic rate of the gun’s operating system, but they will do little to reduce fouling.
Others mount a sound suppressor on their short-barreled AR; this not only suppresses its ferocious report, but also reduces muzzle flash. This solution, while seemingly workable, still doesn’t resolve the dirt and other unburned contaminants being channeled into the direct impingement gas system (and collecting in the suppressor itself). This most often results in reliability degradation of the overall gun by increasing gas system backpressure, which equates to more dirt going into the operating system.
The adage that “death is a small price to pay for looking cool” plays a central role in the way many shooters configure their ARs. Yes, their highly tricked out short-barreled ARs look cool, but they’ll likely die if they rely upon it in a real gunfight. In reality, barrel length directly relates to reliability, and they’ve overlooked that critical component.
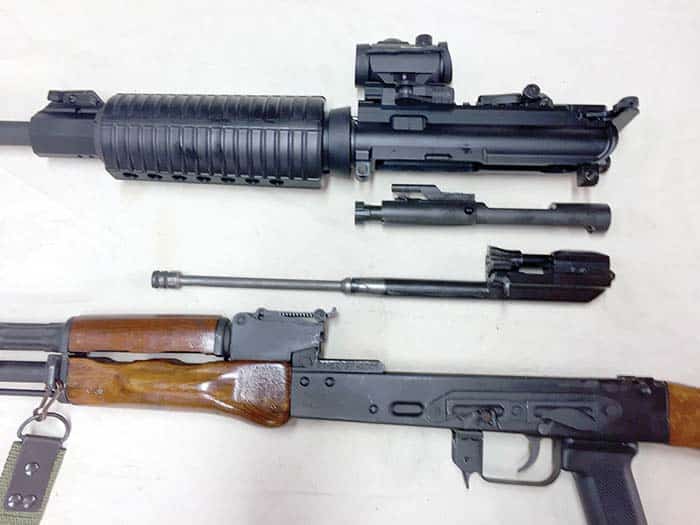
How Does the Gas Piston Operating System Differ?
Russian weapon designer Mikhail Kalashnikov was not the first to employ the gas piston operating system design. However, his unique 1947 adaptation of it in his venerable AK-47 (standing for Avtomat Kalashnikova model 1947) was a game-changer for the Soviet armed forces, their allies and later many developing nations.
How does a gas piston operating system differ from a direct impingement system? While the two operating systems are similar at first glimpse, there are a few key differences in their operation. As a matter of design, gas piston operating systems are heavier (more robust) than direct impingement operating systems, and that’s a necessary design evil.
As with direct impingement systems, the firing process begins with high-pressure propellant gases being syphoned off through a small hole along the gun barrel. Rather than forcing the gas into a tube that channels it rearward into the direct impingement system, the gas is channeled directly into a separate cylinder containing a piston that parallels (above or below) the gun barrel.
A push rod, either directly connected to (as in long-stroke systems) or disconnected from (as in short-stroke/tappet variants) the bolt group, is positioned directly behind the piston. The push rod interfaces with the bolt carrier mechanism contained in the gun’s receiver. The purpose of this push rod/connecting rod is to mechanically transfer the piston’s gas stroke linear energy rearward to cycle the bolt carrier assembly.
Here’s how it works. As the high-pressure gas from the barrel enters the cylinder, it acts directly upon the face of the piston. The rapidly expanding high-pressure gas pushes the piston (and its connecting/push rod) rearward. This, in turn, drives the bolt carrier assembly rearward. Like the direct impingement operating system, this rearward movement extracts and ejects the spent cartridge, cocks the hammer and compresses a recoil spring. The spring powers the bolt carrier assembly forward for the return stroke, chambering a fresh cartridge and putting the bolt back in battery (lock up).
Common to all gas piston operating systems is their reliance on tuning the gas port size for proper critical operating gas volume, along with the physical mass required of the operating parts (including the cylinder, piston, push rod and so on) and recoil spring pressures necessary to power the forward stroke.
Unique to the gas piston operating system, the hot gas used to operate the system never comes into direct contact with the bolt or bolt carrier assembly. This translates to a gun that operates more coolly and cleanly. In fact, on most designs, the bolt carrier can be removed immediately after firing and handled without burn protection. This is advantageous in automatic fire weapons, should emergency takedown be required to make a fix in the field. This is a primary reason that almost all modern machine guns and assault rifles (save the M16 and its variants) employ a version of the gas piston operating system instead of direct impingement systems.
There is a tradeoff, however, for the gas piston system remaining cool and clean, and that is its heavier component mass. Its cylinder, piston and bolt carrier connecting rod (push rod) add weight. As the piston system cycles, the movement of the weighty mass results in snappier recoil, which results in reduced accuracy, especially for quick follow-up shots and full-auto fire bursts.
Heavier recoil also contributes to metal fatigue. That is a primary material design concern regarding assault rifle and machine gun receiver life expectancy. Recoil over thousands of rounds causes receiver stretching and metal fracture from fatigue. Therefore, machine gun receivers are usually made from steel, and they are robust. Knowing that different metals have different expansion coefficients when heated, engineers attempt to use metals with similar coefficient characteristics to produce a gun with an acceptable lifespan (calculated in thousands of rounds fired). The use of exotic metals in gas piston systems is largely avoided because of the cost—both of the metal and the special machining/fabrication processes involved.
Gas piston system parts are not interchangeable between manufacturers, because they all employ their own proprietary pistons and bolt carriers. Since there is no set standard for the gas piston operating system, only brand name manufacturers’ parts can be used, and those usually require professional gunsmith or factory fitting.
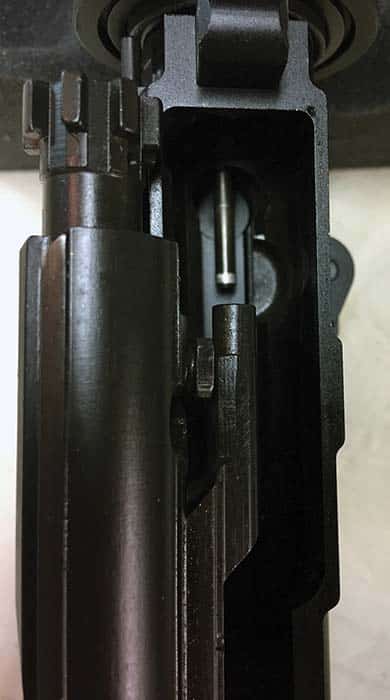
Which System Is Better?
The direct impingement system has arguably proven itself under virtually all battlefield conditions and environments for over half a century on the AR-15/M16 platform with unmatched modularity. Replacement parts are inexpensive, easy to obtain and generally made to a set MIL-SPEC standard. By design, and for the reasons previously discussed, direct impingement system recoil is lighter than gas piston system recoil in the same caliber.
In the long-stroke gas piston system, the piston is mechanically fixed to the bolt group and moves through the entire operating cycle. This means that the combined mass of the piston, piston rod and bolt carrier assembly adds to the entire assembly’s linear momentum, enabling more positive extraction, ejection (on the back stroke) and more reliable chambering and lock up (on the forward stroke). Long-stroke systems can be found in such weapons as the M1 Garand, AK-47, Bren light machine gun, FN MAG, FN FNC, FN Minimi and M249 Squad Automatic Weapon.
The negative consequence of this system is the disruption of the point of aim on the second and following shots in rapid semiautomatic or automatic fire modes. This results from the rapidly changing center of mass during the action cycle, abrupt stops at the beginning and end of bolt carrier travel and the use of the barrel as a fulcrum to help drive the bolt rearward. Also, a higher gas volume is required to operate the heavier gas piston system, which, in turn, requires more massive operating parts—a design Catch-22.
In the short-stroke (or tappet) system, the piston is not connected to the operating system’s bolt group. As in the M1 carbine, it may directly push the bolt group assembly rearward. Or, like in the SKS, Armalite’s AR-18, the FN SCAR and Beretta’s A301-303 shotgun, it may operate the bolt group by pushing a connecting rod. In either design, the gas piston’s linear energy is imparted in a short, abrupt rearward push (short-stroke). The gas piston’s rearward motion is immediately arrested, leaving the bolt carrier assembly to continue through its operating cycle from the piston-generated kinetic energy (rear stroke). Thus, the short-stroke gas piston design has the advantage of reducing the total mass of recoiling parts compared to its big brother, the long-stroke gas piston.
Less recoiling mass equates to better control of the weapon. Less mass means less inertial impact at either stroke end of the bolt carrier travel, and that means less wear on the operating system and receiver. However, there are other dynamic factors in play in short-stroke designs. In many of these designs, the piston sharply impacts the bolt carrier group above the center of gravity, causing long-term wear from peening or accumulative damage to the bolt carrier and the receiver guide rails that champion the bolt carrier assembly’s rearward and forward stroke.
With the preceding in mind, it should be obvious that both direct impingement and gas piston operating systems have strengths and weaknesses unique to their individual design. Some of their weaknesses can be mitigated, but in general terms the operating system’s application should be purposely considered in the gun you choose. The gun’s performance history should additionally play a major role in this selection. Remember, performance is not a matter of belief; it’s a matter of evidence. Understand what you’re buying and choose wisely—your life may depend upon it.
This article first appeared in Small Arms Review V22N8 (October 2018) |