By David Lake
Aluminum
Second only to steel, aluminum is one of the most common metals used in construction, architecture, and general industry. The metal was first extracted from its ore in the first quarter of the 19th Century. 70 years would pass before aluminum alloy became economical enough to exploit its tremendous qualities of high strength and low weight. In its pure form, aluminum is soft and ductile- of little to no use as a structural material. It is highly reactive- that is, it easily interacts with and forms bonds with other materials. For this reason it is never found in nature in its pure form. Most commonly, aluminum ore presents as an oxide or silicate. In fact, aluminum is the most prevalent metal in the Earthโs crust. Aluminum can be recycled and repurposed indefinitely. If it can be said that the modern world is built on Steel- it must be said that the world moves forward on aluminum.
Everything that can be made of steel can be made of aluminum- by all modern standards and methods of manufacture and engineering. Aluminum can be formed and machined and otherwise worked as any other ductile metal can. The newest aluminum alloys claim a higher tensile strength than steel. There is even one particular type of aluminum that can best 6AL-4V titanium in most criteria- strength, weight, cost, and machinability. With all its boasting, Aluminum does fall short of other materials in some capacities. For starters, aluminum cannot offer the same resistance to heat as steel. High temp aluminum alloys exist, but they cannot approach steelโs 2500 degree melting temp. Aluminum enjoys only a relatively narrow temperature threshold where its strength and resilience remain useful (at the extremes of cold and hot, it becomes brittle and weak). And aluminum cannot endure the levels of abuse and mechanical stress that steel may take in stride. Aluminum tends to be slightly less forgiving than steel when pushed close to its limits of operational loads. It is indeed very strong per given mass- stronger than the same mass of steel. But while steel is tends to be elastic; aluminum behaves more like a plastic. That is, aluminum can be stressed only so far until it reaches its point of deformation- from where it cannot recover.
Aluminum only became a viable structural material post 1900. The early use of aluminum-copper alloy was seen in the frame construction of airships. Post World War I, heat resistant aluminum-nickel alloy would be utilized in the internal combustion engine and the (relative) high performance frames and engines of airplanes. Following WWII, aluminum alloy would be refined and specialized enough to find its way into jet engines. The aerospace industry would eventually become synonymous with aluminum- the terms โaluminumโ and โaircraft alloyโ would become generic synonyms. While the air and space industries do indeed employ aluminum structures, they clearly do not hold exclusive rights to the discovery or its purveyance. Be not be swayed by marketing strategies that use fancy descriptions like โaircraft aluminumโ to sell a product. It is by common sense and logical conclusion that almost every industry has adopted aluminum to improve just about everything- gun manufacturers included. By 1949 Colt would announce a variant of the 1911 with an aluminum frame. Weight savings was the idea. Smith and Wesson would soon follow suit with semi-auto pistols and a few revolvers. Colt answered back with an aluminum snub-nosed wheel gun. Late in the 1950s, Europe would revisit its staple handgun designs with aluminum variants. While at the same time in America, some inspired aircraft engineers would put their heads together to create the AR-10. Some designs, as is the case with the AR-10 and AR-15, could only be possible with aluminum construction. Aluminum finds its purpose in firearm design right between steel and polymer. It matches the strength and approaches the durability of steel, while shedding much of the weight (lightweight is becoming more than a fad in small arms design). Hence the proliferation of polymer guns today. Aluminum is almost totally resistant to environmental and chemical attack- steel is not. And aluminum wonโt distort or warp at elevated temperatures- which has been known to ruin a polymer-framed pistol.
As to the application of aluminum to the firearms industry, there is only one group of alloys- and within that, 3 โseriesโ that will be encountered. That group is known as heat treatable aluminum. The alloys of direct interest and application to the gun industry will be any of these three series; 2000, 6000, and 7000. Each comes with its own set of benefits and deficits. Proper alloy selection should satisfy physical, chemical, and environmental requirements. Adverse operating forces and environmental factors encountered by a firearm are many. Most obvious would be the extreme pressures and stresses created by firing a cartridge. A gunโs mechanism may apply and divert and share and shed loads across multiple vectors and surfaces and structures within a single momentary stroke of the action. A firearm creates high heat and caustic or otherwise reactive byproducts during the ignition and combustion processes. A firearm requires routine cleaning and lubrication which means regular exposure to chemicals and substances. And a gun may be required to operate in extremes of temperature and humidity and salty or dusty and abrasive environments. One other noteworthy detail is the condition or temper of an alloy. This โTโ designation describes the heat treatment and process a specific alloy has received. As the 4 digit alloy code describes the chemical makeup and suggests the general use, the letter code accurately describes that materialโs specific capability. The most commonly known is T6. This heat treat condition can be applied to almost any 2000, 6000, or 7000 series alloy.
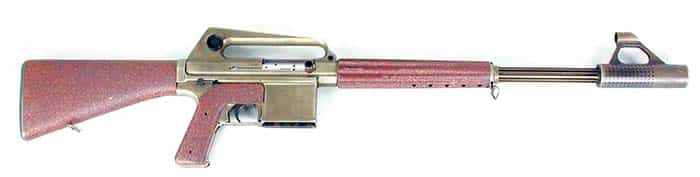
Heat treatable aluminum alloy can be manipulated or โtooledโ by several means. A wrought solid (aka: billet) can be machined or cut into final form, or a final structure may be forged or drawn. A casting may also provide a lump of material that will need to be machined into tolerance. An exciting growing industry of โadditive manufactureโ, also known as 3D printing or (similar) laser sintering can also be used to form aluminum into a finished product. New material science and manufacturing processes are always evolving. Of interest is that one unique company is even using explosive energy (something close enough to RDX) to weld aluminum to steel substrate to create molecularly bonded dissimilar bi-metal pistol frames. One of the newest and greatest aluminum alloys known as Tennalum is stronger than most steels (in annealed state) and lighter than titanium of the same strength. Aluminumโs properties make possible certain structures and mechanisms that would be otherwise impossible. These miracles can be performed at reduced manufacturing expense compared to steel or titanium. Aluminum is easier to work and less taxing on manufacturing tools and equipment. Copper, manganese, silicon, zinc, magnesium, chromium, lithium, zirconium, iron, nickel, titanium and now scandium are all used to make specific aluminum alloys. Strength, hardness, elasticity, ductility, conductivity (both electrical and heat), and density are among the attributes that can be manipulated and prescribed to fulfill specific material requirements. The additive trace elements essentially imbue aluminum alloy with advantages over, and immunities from distinct physical, chemical and environmental influences.
One will likely not find an aluminum slide on a center-fire pistol. A slide contains locking lugs and other highly stressed structures. The receiver of a bolt action rifle should never be encountered in aluminum. A gunโs barrel must assuredly never be made from aluminum. And trigger parts canโt be made from aluminum either. Itโs a great material- but it is a structural material. Aluminum cannot be expected (generally speaking) to repeatedly endure high wear or heavy impact. Aluminum pistol frames and AR-15 receivers house the internal workings and make interface with the locking surfaces and wear components. Pistol frames and AR-15 receivers are usually made from a 7000 series alloy- which can be as strong as some steels. These alloys can endure repeated light impacts, as is seen in the AR-15 buffer. If properly treated on its surface, or coated with a hard or lubricious coating, aluminum can ( to a degree) excel as a wear surface against opposing, moving components, as is seen in the lightweight and long wearing frames of Beretta, Sig, and some 1911 pistols. Alloys of a 2000 series designation match the strength of 7000 series; though the 2ks feature different alloying elements to adjust the metalโs chemical properties to meet more specialized applications.
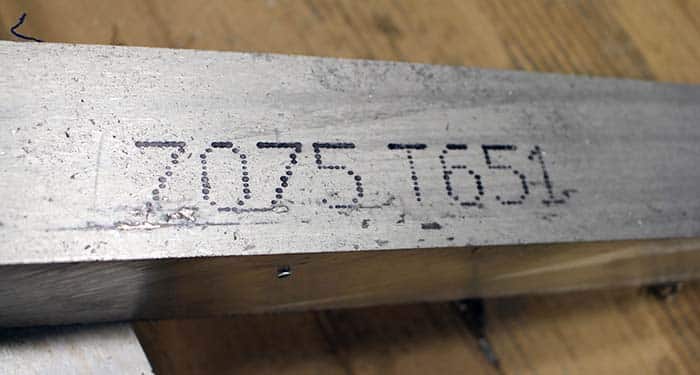
The lesser alloy discussed here, known as 6000 series, are utilized in gun construction also. The fact that the material is not at the top of the list for achievement should not foster skepticism. Trust that any manufacturer has done the homework to make competent and confident decisions as to material selection. The performance of high-grade 7075 can in fact be matched by medium grade structural 6061- simply by the addition of more material. To reiterate, 6061 is not incapable of performing 7075โs job; it just takes more 6061 to do it. That should be acceptable to most of us who recreate with our guns on the weekends. There is only slight risk to accept when choosing a gun that includes 6000 series components. 6000 alloy might scratch, or dent with some entry-level abuse. Again, this should not give pause as most of us spend our own hard-earned dollars on our guns and intend to protect them from damage and abuse. Guns and components made of 6000 alloys might be identifiable by a thicker, heavier profile.
Once upon a time aluminum was in fact worth as much as gold. Today it is relatively cheap, but is used to make anything that must demonstrate a level of excellence. It is used as armor in vehicles and aircraft. It is used to form the structures of spacecraft; and also used as fuel to launch those spacecraft. Aluminum is diamagnetic; a property that makes aluminum the ideal material to be used as the โbulletโ in next wave electro-magnetic artillery- called Railguns. And of course, the modern small arms industry we enjoy is only made possible by the judicious application of aluminum and progressive ideas of how to apply it to effect solutions to engineering problems. There is undoubtedly more new development to come. Years ago, the introduction of aluminum pistols and rifles garnered some enmity from the informed consumer. But science and experience healed that rash for most. Perhaps aluminum will usher in the day when steel is considered a substandard and inferior material from which we used to make guns.
This article first appeared in Small Arms Review V20N3 (April 2016) |