Sabatti’s rifles are renown for their exceptional accuracy – and the “secret sauce” behind it is a company exclusive, its Multi Radial Rifling pattern. Let’s take a peek at their recipe!
by Pierangelo Tendas –
The Sabatti S.p.A. company of Italy has been well known for decades both in its home country and abroad for its bespoke like of hunting shotguns and rifles. In the mid-2000s, the company shifted its core business towards long-range competition shooting and tactical precision rifles, whose rise of popularity on the international markets has been partially hindered so far essentially only by issues with export and distribution.
And yet, what most hunters and shooters worldwide do not know about Sabatti, is that they may well be the world’s oldest barrel manufacturers in existence today.
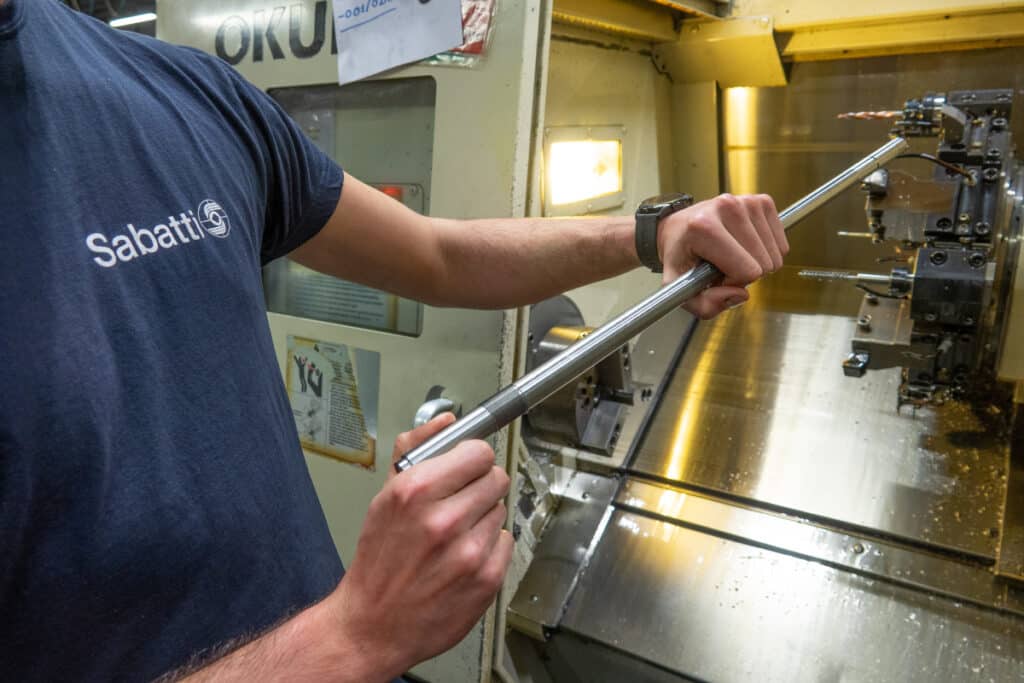
The earliest records of Sabatti’s activity in the Val Trompia region of northern Italy – the “Italian Gun Valley” – date back to the early 1700s, when Lodovico Sabatti was active as a manufacturer of matchlock pistols and most importantly as a “cannoniere” (barrel maker). By the 19th Century, the Sabatti family was known and held in high regard for their barrels and flint locks, which were used by other manufacturers to complete their own guns for commercial sales and for the militaries that fought the battles leading to the unification of Italy.
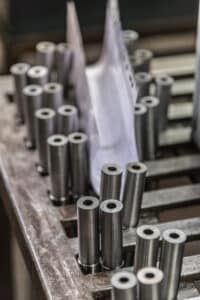
As of today, the manufacture of barrels for third parties still makes up for a substantial portion of Sabatti’s industrial activity. There are so many companies that bought barrels from Sabatti in the past decades that chances are, you may own a bolt-action rifle built with a Sabatti barrel and not even know it. Stocks of Sabatti barrels are well documented to have been used in some lots of Remington 700 and Browning bolt-action rifles, and today they are the sole suppliers of the barrels used on the bolt-action rifles manufactured by Benelli and Franchi (among many others). And that’s not counting shotgun barrels. Unbeknownst to most, Sabatti is what is rightfully called a major barrel supplier in the industry.
A company with such a long history and experience could not hold back for long from taking a huge step in terms of innovation once their core business shifted towards the precision shooting, long-range hunting, and tactical applications market. If the past few centuries had been spent by the Sabatti family mastering the art of making good, long-lasting, accurate barrels, now it was time to make them better, under all points of view: more solid, more accurate, easier to clean and maintain, and with a longer service life.
No Cheap-Out
Right from the very get-go, Sabatti established that the new, improved barrels they set out to conceive had to be easy to manufacture by cold hammer forging. A wise choice, indeed: not only is cold hammer forging a well-regarded, tried, and true barrel manufacturing technique, but is also one that the company had been using for decades and was well equipped for. After all, with such a widely appreciated technology already at hand, already in use to manufacture such widely appreciated products, there was literally no reason for Sabatti to stray from the path from an industrial point of view and set out to design a new barrel that would later require the development of entirely new manufacturing technologies.
This is not a cheap-out by any means. Indeed, more like a rationalization of industrial effort: the new barrels were to be easy to manufacture with the technology the company already had, so they could be put on the market easily and repay the investment just as rapidly, while at the same time not requiring long waiting times to satisfy customer demand.
The research and development phase lasted for years and included both extensive testing and a lengthy study on previous, well-established solutions including conventional rifling, polygon rifling, and 5R, not limited to technical examination of samples but rather reinforced by a thorough investigation of designs and patents dating as far back as the early 1970s, at the very least.
In the mind of Sabatti engineers, it soon became very clear that quality steel and perfectly executed cold hammer forging wouldn’t be enough to achieve the quantum leap they had in mind. They had to go at the heart of the barrel: the rifling.
As mentioned, the research and development phase went thoroughly through the pros and cons of conventional, polygon, and 5R rifling patterns. Sabatti engineers wanted to come out with a new type of barrel that would offer optimal performance with alltypes of ammunition, from factory to reloads, from low-pressure to the hottest loads, from standard to leadless and monolithic. No corners were cut, and no expense spared in the lengthy evaluation and development process.
The Secret Sauce
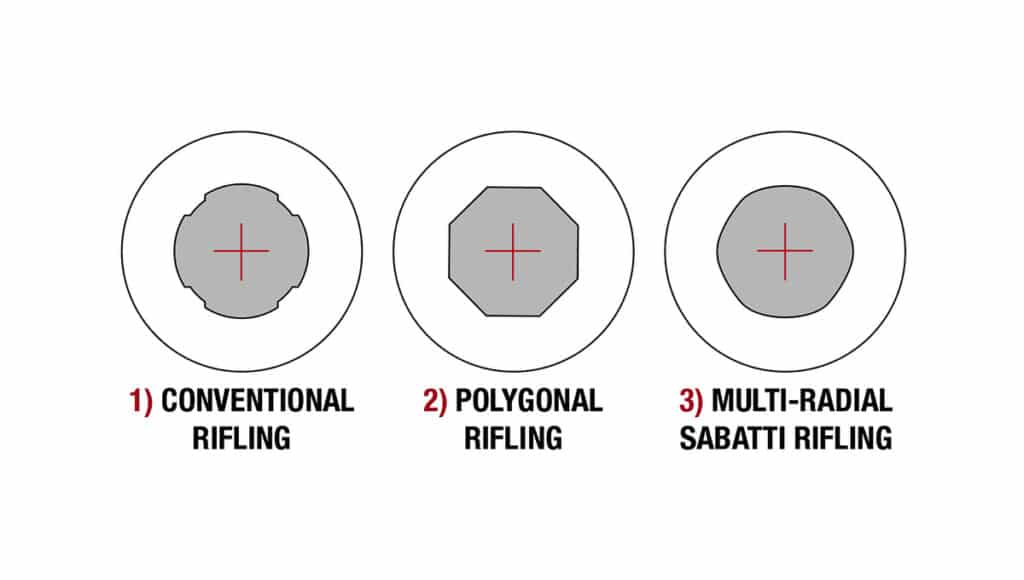
There is a reason why the final product was called “Multi-Radial Rifling”, or MRR for short: the MRR rifling pattern is characterized by two different, alternating rifling radii that go way back to the barrel extension and feature softer edges between the lands and the grooves.
When looking inside an MRR barrel with a borescope, an expert eye may get that old-style impression of the very shallow “microgroove” rifling used by old Marlin rifles and other similar firearms. That feeling would be largely incorrect: microgrooving is an extremely fast, but extremely shallow rifling pattern that doesn’t last long with high pressure loads, aggressive propellants, and, likewise, aggressive cleaning. MRR barrels are everything but.
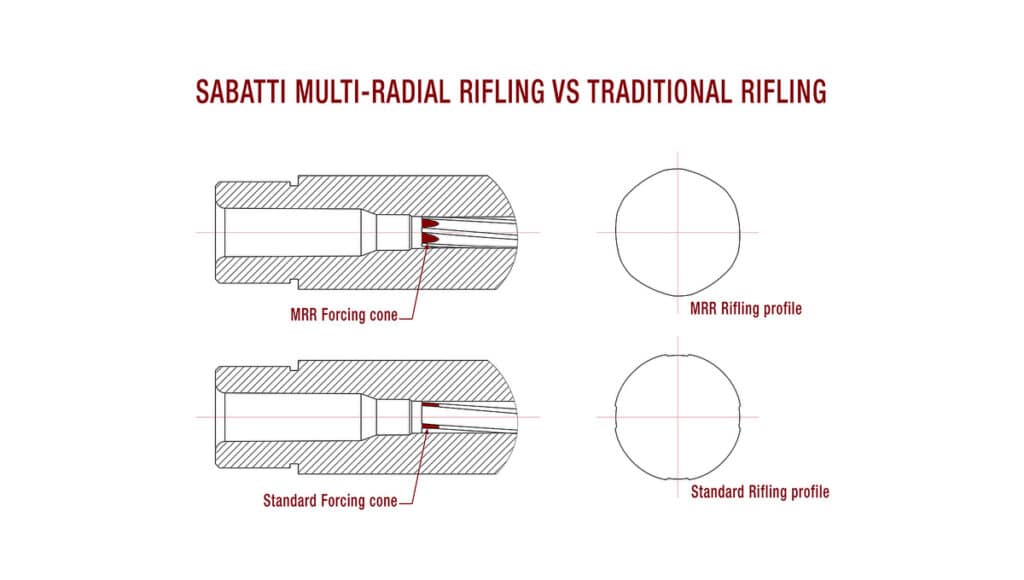
The impression of a shallower grooving is given by the mentioned softer edges between the lands and grooves. As we’ll see, it’s all there for a reason. The alternating radii going back to the barrel extension end up modifying the forcing cone geometry in an optimal way for each given caliber, allowing the bullet to better align with the rifling right from the start. The chamber neck and what little amount of free-bore exists guide the bullet intothe rifling more precisely and with more stability than found with traditional rifling patterns.
It’s worth pointing out that twist rates of MRR barrels have been optimized for each given caliber, but do not depart much from industry standards: we’re talking typically 1:11in instead of 1:12in for 7.62mm/.308/.30-cal. in general, 1.8in for 6.5mm, and 1:8.25in for .260 Remington – for example, that is. It’s not the twist rate that marks the difference between standard, 5R, polygon, and MRR rifling.
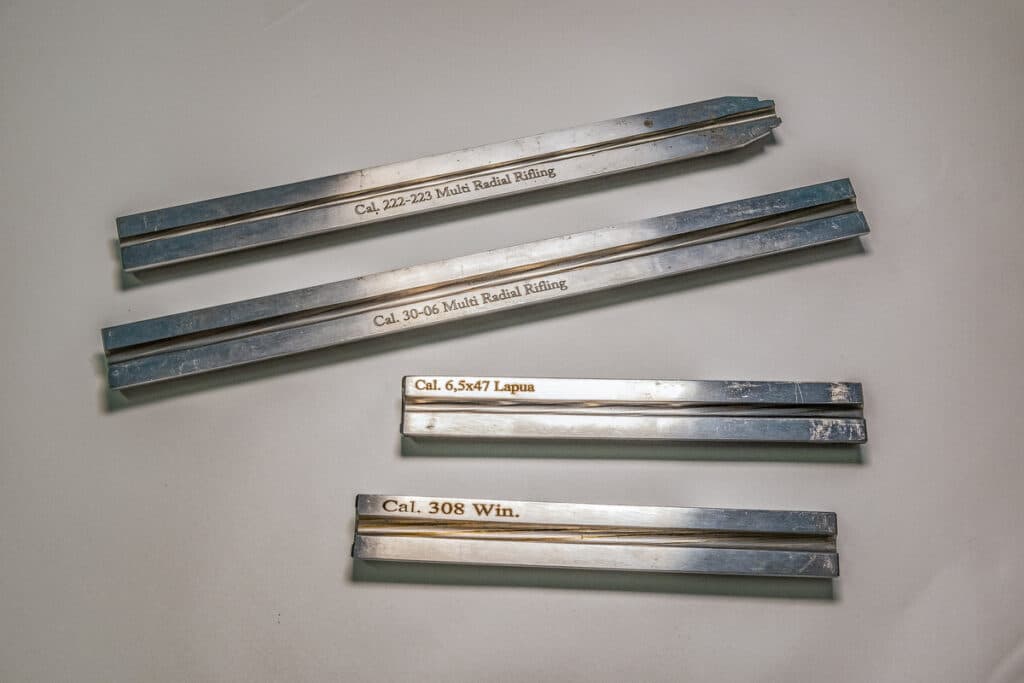
With softer edges between lands and grooves, the bullet traveling through the barrel is deformed and pressure-formed around a circumference, but not cut at the surface like standard or polygon rifling would. The MRR rifling with its softer edges allows the bullet to better fill the lands and grooves, allowing very little, if any, of the gas generated by the detonation of the propellant to escape around the lands. Essentially, in MRR barrels, the bullets seal the barrel as they’re traveling through it, maximizing the propulsion efficiency of the expanding gases.
All the Pros, None of the Cons
The unique features of the MRR barrels make for a long list of pros, which the expert reader may already have guessed. A better bullet-bore alignment provided by a modified forcing cone, optimized twist rate and softer edges allow the bullet to better engage the rifling and thus benefit from better stabilization, which leads to higher accuracy.
At the same time, the “bore seal effect” of a bullet filling the lands and grooves almost completely as it travels down the barrel optimizes propulsion and allows for higher muzzle velocity levels – up to 12% over standard values according to Sabatti in most cases for factory loads, even higher in certain instances with handloads.
Softer land-to-groove edges – which, as we said above, do not cut through the bullet – also eliminate most friction, which is detrimental to both accuracy and barrel service life. Less friction between bullet and rifling also means less fouling, particularly a much lower level of copper or other aggressive metal residues depositing in the lands. Normally, those deposits need to be removed with likewise aggressive chemical cleaners and sometimes scraped away with metal swabs. Nothing of that is good for the barrel’s service life, and indeed nothing like that is actually required on an MRR barrel at any point.

Sabatti’s MRR barrels are overall cleaner, and easier to return to pristine condition: a soft swab with a small amount of CLP is usually enough to remove fouling after even a long shooting session. Abrasive paste or polish pads aren’t necessary to clean the bore, but can be used for lapping, if needed, as they won’t ruin the land-to-groove edges as they would with a traditional rifling.
Accuracy is guaranteed and documented from the factory by Sabatti to be sub-MOA at 100 meters (109.361 yards specifically) with factory ammunition, and to be constant with all MRR barrels, on all Sabatti rifles.
As of today, MRR barrels are a Sabatti exclusive. First introduced in 2017 with the Tactical Syn bolt-action long-range shooting rifle, by 2018 MRR barrels were used on all of Sabatti’s .308/7.62mm and 6.5mm/.284 caliber hunting, long-range shooting, and tactical rifles. As of today, essentially all of Sabatti’s centerfire bolt-action rifles – hunting, sport shooting, tactical – either come standard from factory with an MRR barrel or are available with one as an option. In 2021, Sabatti introduced the SAR Sport semi-automatic rifle – a DMR-style AR-15 variant in 5.56×45mm – which, as of today, is the only non-bolt-action rifle to feature an MRR barrel.
This said, Sabatti can manufacture MRR barrels of all profiles, and for all calibers. Rumors of MRR barrels being manufactured by Sabatti for M4-type select-fire carbines for foreign military contracts have been circulating for a couple of years, but the company, which is otherwise usually pretty talkative, has so far kept tight-lipped about those rumors.
Dedicated Ammo…?
While the MRR rifling pattern has been conceived to perform well with any sort of factory load, handload, and with any type of bullet, the potential exists to improve the performance of MRR barrels even further. In 2021, Sabatti announced the launch of MRR Bullets: a line of dedicated reloading bullets designed to perfectly match the key features of MRR barrels in terms of weight and geometry and help hand-loaders to get the best out of their Sabatti rifles and its multi-radial rifling,
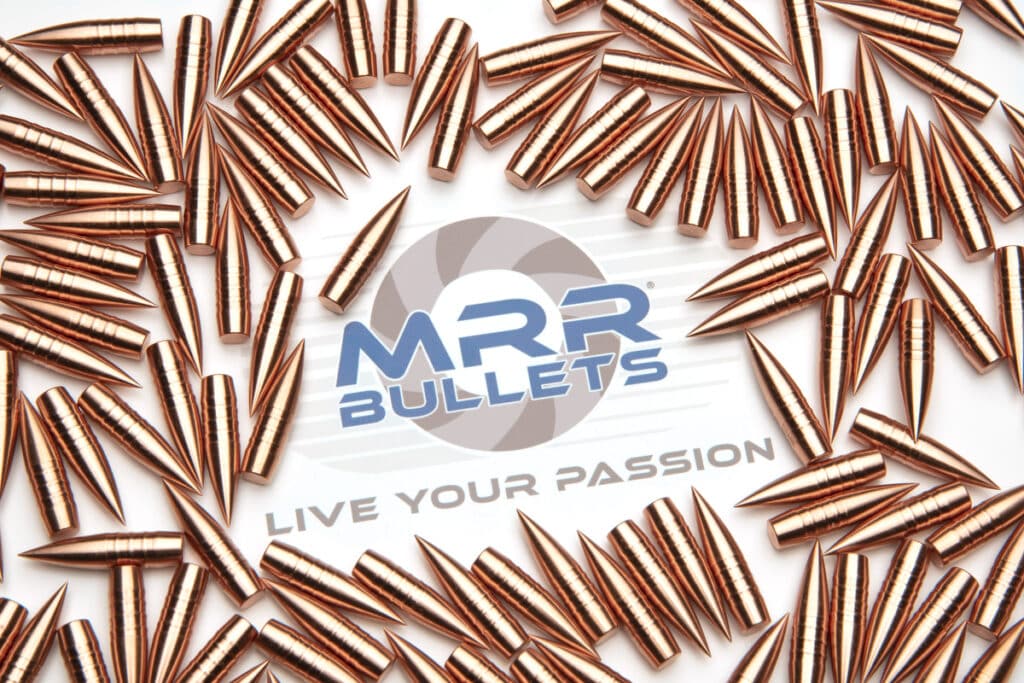
Sabatti’s MRR bullets are all leadless monolithic, and their patented design offers better engagement of the MRR rifling pattern’s typical forcing cone geometry.
Sabatti’s MRR bullets are available in three lines – Green Hunting, Green Sport, and Green Long Range – all manufactured from copper alloy, and all optimized for an intended use: the Green Hunting line bullets feature a polymer tip for better energy transfer and expansion upon impact, while the Green Long Range line bullets are heavier than the “average” Green Sport for better performance at longer distances.
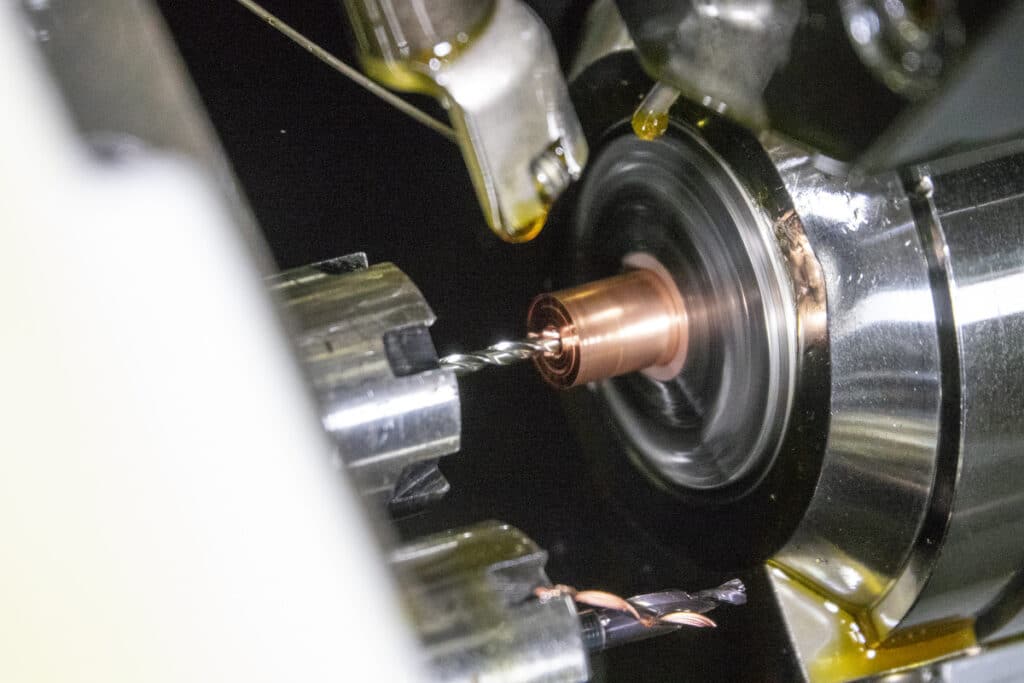
Sabatti MRR reloading bullets are sold in 50-count packages, with calibers and bullet weight availability varying from line to line: the Green Hunting MRR bullets are available in .264 123-grain, .270 120-grain, .284 13-grain, and .30 caliber 152- and 167-grain variants; the Green Sport and Green Long Range MRR bullets are all available in .30-caliber only, respectively in 152-, 158-, 160- and 176-grain options.
The price per box is pretty steep in their homeland of Italy, but one can’t really put a price on quality – particularly if quality comes in the form of patented geometry bullets manufactured out of solid copper alloy billet. As of today, MRR bullets aren’t available on the U.S. market, but a lot of Sabatti rifles with MRR barrels are, and they can definitely give your traditional, polygon, or 5R barrels a run for their money.