By Jeff W. Zimba
Since early 2006, a few variants from the POF-USA P-416 family have quite steadily become standard equipment when going to the shooting range. After an in-depth article and the initial endurance testing of the 9.25-inch version (Small Arms Review Vol. 9, No. 12, September 2006) this system became a curiosity that people started regularly asking about. As of this writing, the 9.25-inch version has fired well in excess of 20,000 rounds and continues to run excellent to this day. The initial test allowed us to shoot over 9,000 rounds without cleaning or adding any lubrication and we strongly believe that had it not been for a magazine malfunction, the testing could have continued much further.
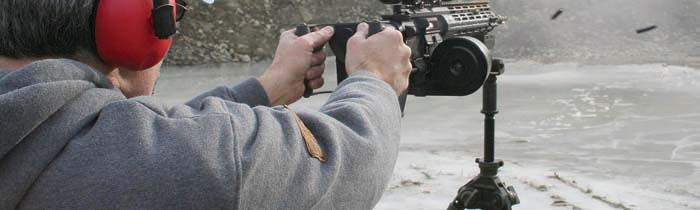
Phase II:
How Hot Does it Run and How Many Continuous Rounds Can We Fire?
It has been almost a year and a half since the original tests, and a review of the data we collected from those outings created a few additional questions that needed to be answered. We noticed that the running temperatures of the P-416 were consistently lower than those taken during the same circumstances with a direct gas impingement system. It makes perfect sense that the absence of the gas tube redirecting hot gasses into the action would relate to lower operating temperatures but we wanted to find out exactly how much of a difference it would actually make, especially during abnormally heavy usage. This allowed us to set up and began phase II.
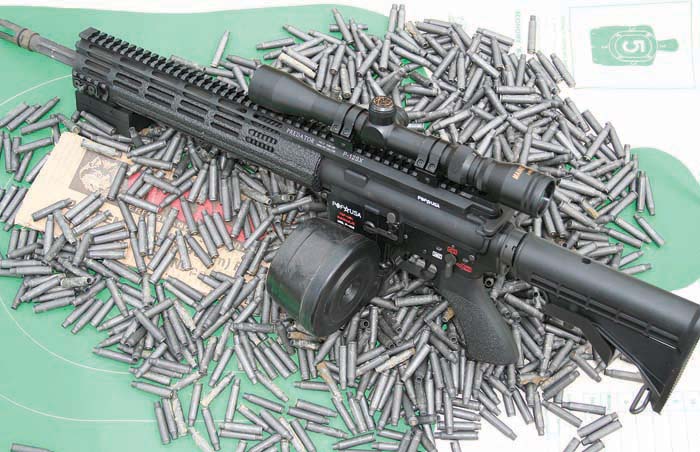
Phase II would be another type of endurance test where large amounts of ammo would be fired, in very long, continuous and uninterrupted bursts, possibly bringing the test rifles to the point of catastrophic failure. Upon reaching the predetermined number of rounds, the temperature of the rifle would be measured in several areas, and the testing would immediately continue, allowing for the residual operating temperatures to continue to increase. No cooling time would be allowed.
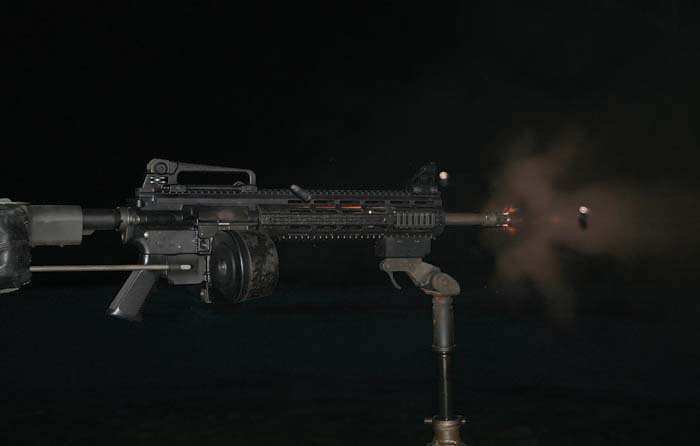
Since BETA C-Mags are readily available and have worked well for us in past testing of this type, we decided to use them as the baseline and go with 100- round continuous mag dumps. We determined that the complete test would consist of 1,000 rounds, barring any type of system failure. After continuously firing each 100-round burst, the surface temperature would be measured on the following parts: the bolt face, the chamber area, the gas block and the muzzle brake. The surface temperature of the barrel would be measured occasionally but was not considered a vital measurement for purposes of these tests. The temperatures would be measured in the Fahrenheit scale with a Geneva Scientific Model TLL950LS Infrared thermometer. This thermometer has a working temperature range from -32° up to +950° and no contact is necessary to slow down the testing or require cumbersome embedded sensors.
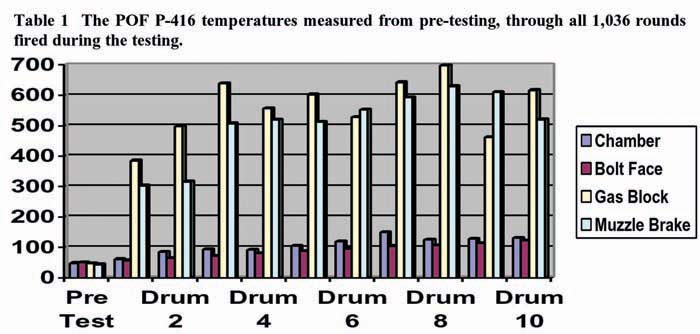
Since we determined that it was going to be possible to reach a catastrophic failure point, for safety purposes, each test rifle was fitted with a KNS precision tripod adapter allowing it to be fired from a standard MG42 anti-aircraft tripod, and both series of tests also employed a set of KNS Precision Spade grips. This combination would allow the shooter to place his body well behind the action of the firearm and not require a cheek weld on the stock only inches from the chamber.
We decided to use Wolf 62-grain, FMJ .223 for several reasons. First, there was an abundance on hand, and if both test rifles reached their maximum number of rounds allotted for the testing, we would need at least 2,000 rounds. Secondly, and most importantly, this was to be one hell of an endurance test and it is almost universally agreed that steel-cased ammunition has the potential to be tougher on chambers than traditional, brass-cased ammo. Contrary to sometimes popular internet and urban legend, we have run tens of thousands of rounds of this ammo during testing firearms of all calibers, types and styles over the years with no adverse effects whatsoever.
Load Up
All available BETA C-Mags were loaded and the remainder of the ammo was loaded onto steel stripper clips for use with a speed loader. We didn’t know really what to expect, but having heard stories about “fire till failure” drills with other rifles, we dressed properly including correct sight and hearing protection. The 16-inch barreled P-416 was mounted on the MG42 anti-aircraft tripod and the baseline temperatures were taken. (It should also be noted that the rifle had been test fired and several magazines were fired in measuring the rate of fire before this round of testing began. Given the high endurance of the original test model we decided not to bother cleaning the rifle before starting this round of testing. Since it was obviously dirty, a quick burst of Rem-Oil was applied through the dust cover prior to beginning this test.) The air temperature was a seasonal 41° above zero with no measurable wind and all parts to be checked were very close to our established “room temperature” this day. (A complete set of charts with all round counts and recorded temperatures are included with this article). After establishing that everything was at a base temperature, it was time for the testing to start.
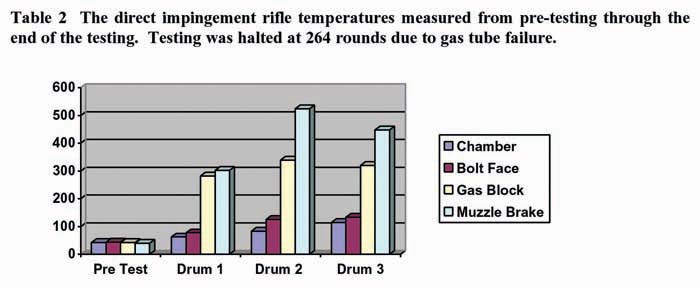
Drum number 1 was loaded and emptied in a single, sub 10-second burst. This was the kind of shooting that we were always warned against because it was potentially destructive and usually pointless in situations where “placing multiple hits on approaching targets was necessary.” It is also precisely the kind of shooting that many serious class III recreational shooters (who have no current approaching enemy targets at the time) really enjoy. The rifle was quickly cleared and temperature measurements were taken in the chamber area, the bolt face, the gas block and the muzzle brake. All were recorded and the next drum was loaded in approximately 90 seconds time.
The bolt was closed on drum number 2 and it was emptied as flawlessly as the first. Measurements were repeated, the next drum was loaded. As the P-416 effortlessly continued to chug along through drums 3, 4, 5, 6, 7 and 8, we wondered if it would indeed make the 1,000-round count we set without a major stoppage.
Drum 9 ran as smooth as the first and it wasn’t until approximately 1/3 into the 10th and final drum that the rhythmic sounds we were getting quite used to screeched to a halt. A quick survey of the situation showed nothing more than a severely cracked magazine feed tower had allowed it to spread and log jam several rounds up inside the action. The loose rounds were quickly cleared and an 11th full magazine was immediately inserted, giving way to another 100-round stream of steel casings, that never ended until the magazine was empty. The final readings were taken and the Phase II portion of the P-416 test was officially over. We didn’t have any reason to believe it would not make it through the whole 1,000 rounds in this harsh manor, but we were still relieved and impressed that it did. A count of the rounds fired through the malfunctioning magazine gave us a total of 1,036 rounds fired throughout the test.
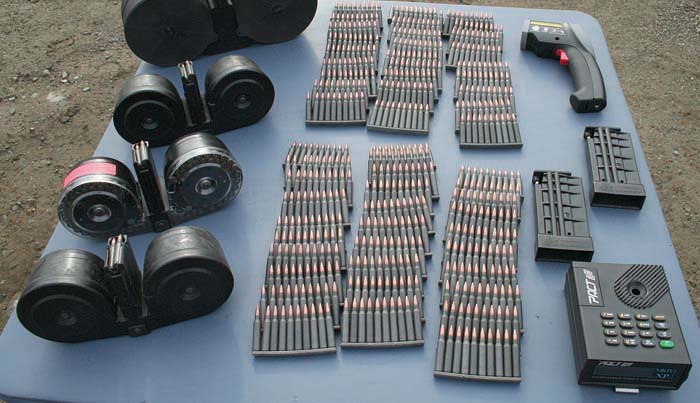
Phase II, Part II
All the data gathered during the P-416 portion was quickly filed, and a second rifle was brought out to duplicate the testing with, and to take direct comparative measurements from, while in exactly the same conditions. This second rifle was a standard direct gas impingement system with an M4 contoured 16-inch barrel, and utilized the same lower receiver and mount setup for continuity.
After taking baseline temperatures the shooting began in the same manor as the first rifle. The first BETA C-Mag was inserted and the first 100-round magazine dump was completed as easily as with the first rifle. It was getting a little darker at this point and the glowing gas tube was highly visible under the rail system. We quickly swooped in with the instrumentation, gathered the necessary numbers and we were onto the second burst.
Drum number 2 was inserted, the bolt was dropped and the range filled again with the same rhythmic beat that had been played since we were set up and started the testing. The gas tube started glowing almost simultaneously with the beginning of the firing, evidenced by the residualheat in it, the barrel and the gas block. The cyclic rate remained smooth and even, and all 100 rounds found their mark in the impact area. The numbers were gathered and drum number 3 was inserted.
As soon as the impact area was in the sights the trigger was engaged and drum 3 was on its way to being rapidly emptied. The gas tube again glowed immediately, and this time the cyclic rate was almost instantly erratic. About 30 rounds into the third drum the cyclic rate started slowing and eventually sputtered to a stop. Pulling the charging handle rearward, anempty chamber was discovered. There had been a gas tube failure and there was not enough pressure to bring the bolt carrier back far enough to pick up a new round and chamber it. Another round was cycled by hand and fired only to have the same result. The magazine was pulled, the gun cleared, and the measurements recorded. Test over. Total rounds fired in rifle number 2 was 264.
Heat Transfer
As discovered through the measurements we recorded, heat was indeed transferred into the action of the firearm through the gas tube at a much faster rate than with the piston gun. The numbers that seemed to indicate the most significant difference were the temperatures of the bolt itself. The bolt face temperature was measured after every magazine was emptied and it reached a higher temperature after firing only 200 rounds with the direct gas impingement gun than it did even after firing over 1,000 rounds through the piston gun. Another factor that plays into the equation is friction, which is greatly reduced in the P-416 by the removal of the gas rings and the silicone nickel coating, which creates an extremely smooth surface. The maximum temperature the bolt face reached in the P-416 was 122° and that was recorded immediately after firing 1036 rounds. The maximum temperature the bolt face reached in the direct gas impingement rifle was 133° but that was only after 264 rounds, the failure point for this system.
Chamber temperatures recorded with the direct gas impingement rifle reached a maximum of 115° and was recorded after 264 rounds, the maximum number of rounds fired. The P-416 reached a similar temperature of 119° after firing 600 rounds. The maximum chamber tempera ture measured in the P-416 was 131° immediately after concluding the testing at 1036 rounds. All temperatures were measured in the rear of the chamber through the barrel extension.
The gas block of the P-416 retained much more heat after firing than the gas block of the direct gas impingement rifle. While the maximum temperature recorded with the direct gas impingement rifle was after only 200 rounds, it only reached a temperature of 339°. After firing 200 rounds in the P-416, the gas block reached a temperature of 498° and spiked at 697° after firing 800 rounds. Gas block temperatures fluctuated greatly throughout the testing but seemed to dissipate much faster in the direct gas impingement rifle. The mass of the gas block is much greater in the P-416 and the free flowing transfer of heat ends there in that particular system as opposed to allowing the flow rearward through means of the gas tube.
Much of the barrel temperature increase is due to the friction of the projectile being forced down the bore. Since the focus of our testing was to check for changes directly related to the differences between the direct gas impingement system and the gas piston systems we did not bother collecting significant data in this area.
Conclusion
We did not really know what to expect when we started this test. The number of rounds fired in the short time allowed was way beyond the normal use of any standard black rifle. The rifle system itself was simply not designed to fire that many rounds without failure. We have all seen enough melted gas tubes and have a good enough understanding of how the system works to know this kind of abuse is well past its intended use. The point of the test was to fire as many rounds as the rifle would withstand, and record the data to that point. Since the P-416 was still functioning at the end of the testing, we still do not know what that end point really is. Maybe a “fire till failure” test is something we should explore in the future. All this writer knows for certain is that the POF-USA P-416 rifle system was designed without the limitations of a standard black rifle and continues to perform in ways quite unrealistic to the original design. There seems to be plenty of active debate about the piston operating system versus the direct gas impingement design and there may never be a “perfect” system for everyone. Just like there are desired barrel lengths, calibers and mounting platforms that some see as mission critical and others see as simple options, the operating system may just be another choice for the end user to determine and remain the topic of another endless debate in the gun world. While there may be valid reasons to stick with a time proven direct gas impingement system in some instances, it is clearly becoming obvious to some that the newly designed piston systems on the market today also have definite advantages. It was not very long ago that the implication of a rifle that could double as a PDW and a SAW would be considered unrealistic at best. Today, thanks to POF-USA, that might not seem quite so far fetched.
Use Your Ears
If you shoot a lot of fully automatic firearms, especially to extremes such as this, your ear can become an important tool. A smooth and even cyclic rate is usually a sign of things working well. When the cyclic rate varies up and down (when shooting the same ammo) or is erratic in any way, it is often a sign of something wrong. A gas leak is an easy one to diagnose as the cyclic rate often slows drastically from start to finish during a long burst. It can be anything from a failing gas tube to a loose gas key but is usually a sign of a gas pressure problem.
During the testing of a new rifle a few years ago, it was decided to do a full BETA C-Mag dump during a lull in the shooting at a well attended private shoot. Since it was a very short barrel (11.5 inches) and had a brake that was quite loud, after 35 or 40 continuous rounds it caught the attention of several participants. The cyclic rate started out in the area of 950 rounds per minute and was slowing at an even pace. By the time the rifle finished the magazine, it was running no faster than 450 rpm. Several people came right over and commented that it sounded like the gun was “running out of gas” and sounded like an outboard boat engine as the tank ran dry. After clearing and cooling, the gun was examined and an improperly staked (and very loose) gas key was found to be the culprit. As usual, your senses, in this case your hearing, can give you more information than you know how to process if you only listen to it.
Sources
P-416 Rifle System
POF-USA
Dept. SAR
23623 N. 67th Ave.
Glendale, AZ 85310
Phone: (623) 561-9572
Fax: (623) 321-1680
E-mail: sales@pof-usa.com
www.pof-usa.com
BETA C-Mags
The BETA Company
Dept: SAR
2137B Flintstone Drive
Tucker, GA 30084
Phone: (770) 270-0773
Fax: (770) 270-0599
E-mail: cmag@betaco.com
www.betaco.com
Spade Grips & Tripod Adapter
KNS Precision, Inc.
Dept: SAR
112 Marschall Creek Road
Fredricksburg, TX 78624
Phone: (830) 997-0000
Fax: (830) 997-1443
E-mail: sales@knsprecisioninc.com
www.knsprecisioninc.com
Wolf Performance Ammunition
Sporting Supplies
Dept: SAR
1125 North Lance Lane
Anaheim, CA 92086
Phone: (888) 757-WOLF
Fax: (714) 632-9232
www.wolfammo.com
This article first appeared in Small Arms Review V11N6 (March 2008) |