By Matt Smith
PART ONE: THE INTERVIEW
SAR: Doug, please give us a background of yourself and how you got started in the Class 3 business.
Doug: I grew up in Montana and went to school in Bozeman at Montana State where I graduated in 1980 with a Bachelor of Science degree in Chemical Engineering. I worked in California in the chemical industry and gravitated into the machinery manufacturing business. Most of my background is in mechanical engineering. I sold and designed mixing equipment for several years, then moved to Arizona with my own small mixing equipment company. After I was here for a while, I started in the full automatic arms and suppressor business.
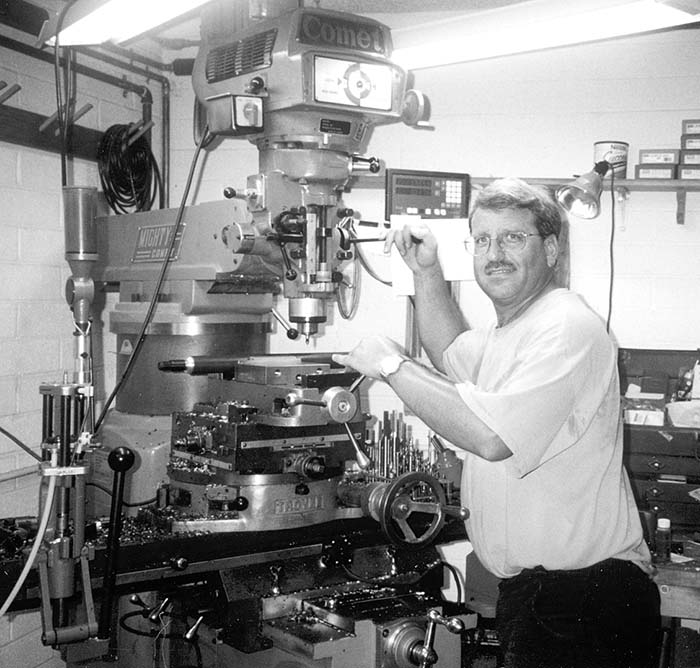
SAR: When did you first become interested in firearms?
Doug: When I was about fourteen years old, I checked out William Helmer’s book from the public library, The Gun That Made the Twenty’s Roar. This was his book about the Thompson submachine gun. That’s when it was decided I wanted my first Thompson, and also peaked my interest in suppressors. I had been thinking about suppressors and mentally designing them since that time. However, it wasn’t until I moved to the free state of Arizona that I was able to pursue my passion for suppressors. The one reason I like suppressors is because I love to shoot but hate the noise associated with it. A lot of people like to make noise, but I don’t. I like to put lead on target as accurately as possible and noise is an unfortunate byproduct of that. I thought that if I could eliminate the noise that it would make shooting more pleasant. This would also be healthier on my hearing, because even with hearing protection your hearing does go away after a while if you do a lot of high volume shooting.
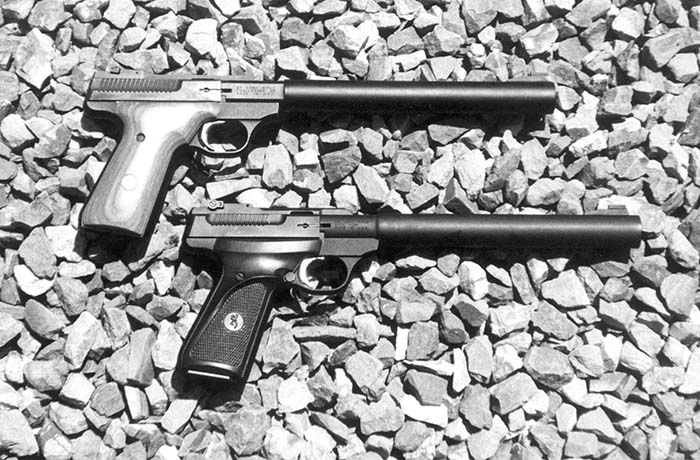
SAR: Did you finally get that Thompson you wanted?
Doug: Yes, it was the first thing I bought after moving here. I had been here just two weeks and found one for sale, paid the seller his money and then the seller held it until I had been a resident long enough to where the local law enforcement would sign off on it.
SAR: Which model Thompson did you buy?
Doug: The first one was a 1928A1 West Hurley gun.
SAR: That makes it sound like you might have more than one.
Doug: You could say I have a passion for Thompson’s! At age fifteen, back in Montana, I wanted my first machine gun, but was too young, plus my mom nixed the idea of my own MG. Then I went to college, and was old enough to own it but couldn’t afford it. Later, after moving to California, I could afford it, but they wouldn’t let me have it. And when I finally got to Arizona, the rest is history.
SAR: Are there any special Thompson’s in your collection that you could tell us about?
Doug: I picked up one of the original Colt guns that sat in the crates at Auto-Ordnance until Numrich Arms bought them in 1951. When they opened the crates, they found 86 unregistered Thompson’s that they promptly stamped serial numbers on and registered with the government. I have one of these Colt guns which is very nice and unusual in that there are no other markings other than the serial number on them. It was apparently a pattern or tool room gun or possibly had some minor quality control issue that prevented them from marking the gun at the time of manufacture.
SAR: Where did you find this gun?
Doug: I got it out of the Champlin Fighter Museum in Mesa, Arizona, when they sold off their assets several years ago. Their collection also included many aircraft guns, a lot of original guns, such a Colt Monitor, early BAR’s, and other rare and unusual pieces.
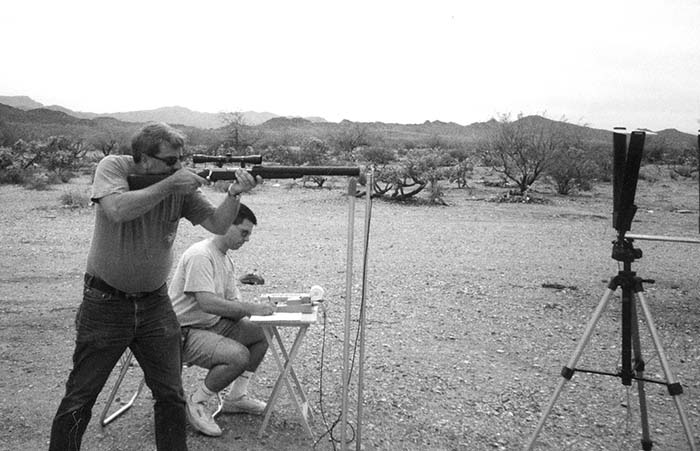
SAR: When did you first get into the business?
Doug: It was three years ago in June 1998 that I received my first FFL. I had built my first suppressor using a Form 1 a year earlier. It was for my Sten and was fairly effective, but quite large. In August of 1998, my first commercial suppressed guns were made available. They turned out fairly good, but they still needed some work. We have improved our work over the years as my learning increased. All of these different ideas had been piling up in my brain for years, that I wanted to try, and that’s what I started doing; trying these ideas. Some worked fabulously and some of them stank! Unfortunately, in the suppressor business, you don’t know what will or won’t work unless you put it in metal and try it.
SAR: What were your first commercial suppressors?
Doug: Our first suppressors were Ruger Mark 2’s followed closely by the Ruger 10/22’s. W have also suppressed a Remington 597, Marlin 7000, which is a great gun to suppress, Browning Buckmark, which is one of the best guns to work with, the Ruger 96/22 lever action, and people have sent me many other oddball guns to suppress, as well. We’ve done a lot of muzzle cans for those that want screw on suppressors. Recently, SRT has started getting into the larger caliber weapons, such as the Ruger 77/44 rifle, the Marlin .45 Camp Carbine, and most recently we finished a first generation 9MM muzzle can.
SAR: What were your impressions of the Suppressor Trials held at Knob Creek?
Doug: It was a very educational experience. It was the first time I really met most of the people in the industry, and it was very good to see what the other people were building. Most of my suppressor experience was just from what I had invented. I haven’t looked at any other cans and hadn’t seen any other manufacturers suppressors until the suppressor trials. Everything I did was pretty much from scratch and what I saw from pictures in Al Paulson’s first silencer book. Going to the Suppressor Trials gave me a lot of ideas as far as different things to try design-wise, how to try to shrink the size of my suppressors down, and improve the cosmetics of them. A lot of the people there were very helpful with ideas and insights. Nobody there actually told me how to build a suppressor, but as I was complaining about running up against one blank wall after another, some of the people in the industry, both manufacturers and those on the sidelines; when they realized that I was actually doing my own original work, and not copying other peoples work; they opened up a little bit and gave me some insight in different directions to pursue when I ran into problems.
SAR: Doug, tell us about your machine shop.
Doug: I have had my own machine shop since 1990. I moved it here from California. I don’t have any CNC equipment yet. Any high volume requirements are subcontracted out to people that do have that capability. We have a three horsepower Bridgeport style mill and a three horsepower gearhead lathe, both with digital readout, that are used extensively. My welding equipment includes those for tig and arc welding. Going into the suppressor business just meant buying more gunsmithing tools. The rest of suppressor building is just moving metal.
SAR: Have you always been interested in manufacturing?
Doug: With my background in chemical and mechanical engineering, I’ve worked extensively with high-pressure gas fluidics and other areas that are closely related to suppressor manufacturing. I started making my own lab equipment and, although self taught, this experience gave me the background I needed to machine metal. I started putting some of these fluidics ideas into suppressor designs, some of which worked great while others didn’t. My suppressor manufacturing business is set up on the research and development end. I would sooner develop the best suppressor out there rather than make a bunch of cheap crap that I could sell to make some easy money. I would rather sell one good piece versus ten cheap, mediocre pieces. That’s the way I care to operate. We will bring our products to market as they are ready. I don’t want to rush out a .223 or .308 suppressor just because everybody else has one. When we bring out a product and make it available for sale, it’s going to be the best one out there or pretty near the best. It will be better in one or more ways than anything else out there, whether this is suppression ability, reduced size, better price or some other advantage not currently available.
SAR: What are your thoughts about suppressor materials and construction methods?
Doug: I prefer to use stainless steel and aluminum. We will use carbon steel in some cases if someone needs a blued gun, but prefer the machineability of aluminum and the corrosion resistance of stainless steel, particularly in the .22 caliber and 9mm subgun cans. As soon as we get into the high-pressure, centerfire rifle, we need to start talking exclusively stainless steel with some Inconel or other exotic metal parts for the heat and corrosion resistance. These exotic materials are expensive and difficult to machine, but that’s the only way to make a suppressor that will last forever. If you’re making a suppressor limited to single shot, centerfire application, you can get by with carbon steel. As soon as you start putting full automatic fire through them, the carbon steel will just melt and go away really quick. I’m not going to fuss with titanium, personally. I think it’s overrated. Yes, it’s strong and light weight, but it can be difficult to machine and I don’t see an advantage to use it for anything I’m building at this time. I have done some research into alternative, nonmetallic materials, such as composites, which hold promise for low-pressure rounds. These would not be good for high-pressure rounds whereas ceramics might succeed. These materials would require serious research and development and would be costly to analyze.
SAR: Do you have a preference for threading versus welding?
Doug: Low-pressure cans can be threaded, but anything that is high pressure should be welded in some form or another, such as tig welding. For assembly purposes, threading often holds it together better with welding used to finish it off and give it added strength.
SAR: How do you think the Internet has affected the firearms industry?
Doug: It’s actually a cheap way to advertise and it’s a good way to learn. I don’t think I would have learned anything useful about suppressors without the Internet. I’m not sure I’d even be doing this without the Internet. One disadvantage, particularly in the gun culture, is that not everyone is connected or Internet savvy. If you rely solely on the Internet, you are missing sixty to seventy percent of the potential market.
SAR: What did you mean when you said that you might not even be doing this without the Internet?
Doug: I don’t think I would have gotten the right contacts or met the right people in this business without the Internet. I would have probably been limited to just people I met here in Arizona. Now, I have contact with Dr. Phil Dater of Gemtech, Joe Gaddini of SWR, both of whom have been very encouraging, even though they are competitors. Tom Hoel, who, like you, writes for Small Arms Review, has given me ideas and direction over the years. There are a couple people who have helped me that wish to remain anonymous who are also in the suppressor industry. I came in contact with all of these people through the Internet.
SAR: What have you learned as a result of your Internet contacts?
Doug: One of the main things has to do with proper barrel porting for suppressors. A lot of manufacturers port their bullet velocities down so low to achieve their suppression, that it won’t cycle most types of ammunition. The bullet is coming out at 700 to 850 feet per second using high velocity ammo, and to me that is pointless. You might as well throw a rock at something, particularly when we are talking about a 38 grain .22 pill. Part of my suppressor design was to provide as high a velocity as I could so I could deliver maximum impact to the target. This allows you to have a greater effective range while providing as good or better suppression than anything else out there, and with very good accuracy. To me, shooting a gun is more than just shooting the dirt at your feet. I’m trying to hit something out at twenty, fifty, seventy-five, or one hundred twenty-five yards. With our guns, I can do that. I can put a drink can out at seventy-five yards and hit it ten out of ten times with one of my Mark 2 pistols from a bench rest. To me, making a gun that works is more important than making a mediocre gun whose only claim to fame is useless flutes on the suppressor tube.
SAR: How and why did you choose the sound testing equipment you have?
Doug: I was talking with Phil Dater and he said that the only way you can really do effective research and development is to have your own meter. I was thinking I could get one from Radio Shack for about $300. Phil told me that a Radio Shack meter just wouldn’t do the job. He sent me a copy of his pamphlet about firearm sound testing, which explained that only two meters were acceptable for accurate sound level testing. These include the B&K 2209 and the Larson Davis 800-B. I started inquiring around in order to purchase one and found out they were several thousand dollars, but knew I needed one if I really wanted to be in the business. I chose the Larson Davis because it is currently in production, and it is made in the United States. If we ever need to have any work done on the meter I know we can send it up to Utah and have it repaired. Fortunately, they had a demo meter that was recently refurbished, and was able to purchase it at a substantial discount. By the time we had the meter, the quarter inch microphone, the calibrator, and a couple other accessories, there was a several thousand dollar investment that we had made. On top of that, you have your chronograph for bullet velocities. Once we had all the equipment, I was able to knock two to three to several, and even as much as a dozen, decibels off all our designs just by tinkering with different parts of the suppressor. You try this and record what you did, recording the decibels, change something else to see if it gets better or worse. Sometimes the gains are small-.2, .3, but other times they’re more. With several changes the dB reduction is significant and you have a new suppressor that’s hopefully as good or better than anything out there.
SAR: Tell us about your work with the large caliber rifles.
Doug: After working mainly with .22 weapons, I ran into some people with some Marlin Camp Carbines in 45 ACP. That really intrigued me because these guns are capable of delivering 230 grains of lead at between 750 and 800 feet per second. This performance is better for animal control and other work related items that you would use a suppressed gun for. The Ruger 77/44 was a natural because of the way it’s made and the bullet characteristics. Others have suppressed these guns but didn’t get the performance I thought they should, and their tube diameter was a little larger than I cared for. I thought we could do a better job. I really like the gun because you have an option of shooting either a supersonic .44 magnum load or a subsonic .44 special load. If you need to, you can send 240 grains out there at 1600 feet per second and do some real work. It’s a little loud with the ballistic crack, but you can download the round or shoot commercial .44 special ammo where you will be subsonic at 840 feet per second at less than 120 decibels. This is right in the suppressed .22 range. Out to 150 yards this is a very accurate shooting gun. If you want super accuracy, then hand loading is the way to go. Anywhere between 210 and 300 grain bullets can be fired at about 950 to 980 feet per second in a .44 magnum case. I designed my gun to achieve maximum practical velocity, which I believe is faster than any other current manufacturer, with as good or better accuracy and sound suppression compared to anything else on the market today, and in a smaller package.
SAR: Do you also suppress the lever action Rugers?
Doug: Yes, we’ve already suppressed a 96/22, which is a nice, compact little gun. I put iron sights on the barrel, which makes it a handy carbine. We are currently building a 96/44, which is a lever action .44, and that will be a super quiet little gun because of the way the barrel is designed. We had to put the tube a little farther forward on the barrel, and this results in two and one half inches of extra baffles, which is good for an extra three dB reduction.
SAR: Other than suppressors, what other products does your company make?
Doug: One of our original products, which we still make, is the Linkmaster Linking Machine. This is a convertible linker that is based on the M7 .50 caliber BMG linking machine available on the surplus market. We take the M7 and drill three holes in it and install an adapter bar on it and cut linking plates for any type of metallic machine gun link. These include 30/06 1919 BMG links, .308 Israeli BMG links, HK metal belts, MG 34 metal belts, .223 links, M60 M13 links, Vickers and Maxim cloth belts, as well as others. The linker, although modified is still perfectly good for the original .50 caliber links as well. If you have your own M7, you can send it to us for conversion and provide one plate at a cost of $200. Additional plates are $100 each. We’ve also built a couple dozen stand-up mounts for the Browning 1919 and M60 machine guns. This is an all aluminum mount which is lightweight at 24 pounds. It is easy to carry and you unfold three legs to use it. You can either order it at a sit down height or stand up height. You stake the mount to the ground, lay an ammo can into the holder, mount the machine gun, and fire it without having to lay on the ground or dirt any more. Prices for these mounts range from $440 to $600 depending on the options you choose. Options include height limiter adjustments and recoil limiters. You have 360 degrees of swing and up to 80 degrees of vertical traverse.
One specialized tool we manufacture is for the Thompson machine gun. It is a pivot plate removal tool which allows you to move the pivot plate spring fingers on the right side of the lower receiver out of the way to release the safety and selector levers. This is necessary to disassemble the lower. The tool is nonmetal, very strong and eliminates scratching the lower, which usually happens when using a screwdriver. The cost is $20 delivered. It will work on any version of the Thompson’s, including both semi and full automatic versions.
SAR: Doug, what is in the future for your company?
Doug: I have plans for finishing up the 9mm suppressor, which we just put together and we tested yesterday in the desert for the first time. It worked really well for a first time design. I would like to get another four or five dB reduction from this can, and next we will start working on a .223 can because I need one for my gun. I’ll build it for myself first, and then work on a prototype to the point where it’s hopefully as good or better than anything out there, and then that will come to market.
SAR: What did you think of our testing results?
Doug: Testing in the desert at 108 degrees is not the optimal place to get the lowest readings. Location and temperature make a big difference. For example, I went up to the mountains recently where it is much cooler and did a couple tests on .22’s. I used a MkII and the 10/22. I ran a string at 7AM when the temp was about 62-65 degrees, and again at noon when the temp was 83-85 degrees. I followed with a third string at 12:30, after the guns and ammo were laying in the sun for about 20 minutes. The 7AM MkII string was about 1.4 db quieter than the noon test (which was lower by another 1.5 db than our hot desert tests). Letting the guns and ammo sit in the sun raised the db level another .8-1.0 db. I suspect that is why we were getting such wild swings, bullet to bullet, the second day. Some of the ammo was in the shade, and some was in the sun, and almost too hot to touch.
The 10/22 was more pronounced having about 2.6 db difference between the 7Am test and noon tests (113.1 db with hi-vel at 7 and 115.7 at noon). If this is linear, I count 2.9-3.9 db difference between 62 degrees F and about 108 degrees F, at least with .22’s. It is also possible extreme temperatures may affect either the meter, or microphone, speeding up the rise time and skewing the results.
As a side note, a few years ago, I went shooting in July, and made the mistake of leaving my .223 ammo in the sun, about every third round ruptured the case, and blew the floor plate out of my M16 mag, leading me to suspect that when ammo is too hot to touch, chamber pressure rises excessively during firing.
SAR: Doug, thanks for giving SAR a chance to check out some of your suppressed weapons and sharing your background with our readers.
Doug: You’re quite welcome!
PART TWO:SOUND METER TESTING RESULTS
The sound testing equipment was provided by SRT. The procedures used follow the specific testing protocol outlined in Phil Dater’s Sound Measurements pamphlet published by ATI Press. A Larson Davis 800-B Sound Pressure Meter, set on “A” weighting and peak hold was used with a 1/4-inch condenser microphone. The meter was calibrated using a calibrator traceable to a primary standard per the National Institute of Standards and Technology prior to the tests. The microphone was placed one meter away from the front of the suppressor or muzzle. The microphone was pointed straight up oriented at a 90-degree angle from the bullet flight path. The weapons were fired 1.6 meters high over the desert floor. Velocity data was obtained using an Oehler Model 35P chronograph with sky screens set 24 inches apart and the start screen eight feet from the muzzle. These are the same procedures I have followed hundreds of times shooting for SAR at the Suppressor Trials.
The ammunition used is all commercially available and contact data for manufacturers of the subsonic ammunition is provided at the end of this article. Ten shot strings were recorded for each weapon and the average reading obtained is provided in the tables.
The large bore suppressed rifles were the most impressive weapons fired during my visit. The Marlin Camp Carbine .45 and the Ruger 77/44 have always been favorite weapons of mine and Doug’s suppressed versions are the quietest ones I have ever encountered. Both of these weapons shoot factory ball ammo flawlessly and deliver a big punch. When you are able to fire 230-240 grains of lead downrange at 800 feet per second and keep the sound signature to 120 decibels, this is quite impressive. Although we didn’t perform any standardized accuracy testing, each weapon was able to pick off small rocks at between 40 and 80 yards consistently.
Doug’s Soundmaster integral Ruger .22 Mark 2 pistol is one of the best available on the market today. I purchased one a couple years ago which has been upgraded to the latest baffle stack. Doug is correct when he states that his sound equipment allows him to make continuous incremental improvements to his products. This pistol’s sound reduction has improved close to ten decibels with the latest upgrade. The pistol cycles with subsonic and standard velocity ammunition and delivers accurate and consistant groupings.
The new 9MM muzzle can is an excellent suppressor delivering a 26 decibel reduction dry and a 37.5 decibel reduction wet. What is amazing with this suppressor is the water retention when fired wet. Even in the desert and with rapid firing, the sound reduction degraded very slowly allowing 3-4 magazines to be fired before the sound signature reduction fell out of the 30 dB range. Doug states that he should be able to greatly improve on this initial design and based on his previous efforts, I believe him.
This article was written to share the history of SRT with our readers and to illustrate how the SRT line of suppressors performs. The accompanying charts provide detailed information for the testing of each suppressor. Through this testing it can be seen that the SRT line achieves some of the highest suppression levels available on the market today. For an in-depth evaluation of other manufacturers offerings, purchase the SAR Suppressor Trials book which is being published in the near future.
Contact Information for Doug Melton: SRT Arms Div., D.H. Melton Co., Inc. 1739 E.Broadway Road, #1-161 Tempe, AZ 85282 Phone (480) 967-6218 E-mail: nac15@sprintmail.com Webpage: www.srtarms.com Contact Information for Subsonic Ammunition: A-Zone Ammunition 1340 Deer path Drive Osteen, FL 32764 Phone: (407) 330-7768 E-mail: sandrodiaz@mindspring.com Webpage: www.a-zoneammo.com
This article first appeared in Small Arms Review V5N3 (December 2001) |