By Frank Iannamico
Gordon Ingram conceived his Model 10 submachine gun during 1964 while living in Southern California. Although the Model 10 would be the most successful of all Ingramโs weapons, he had a difficult time finding a company interested in producing it. He had written to every U.S. firearms manufacturer listing all the attributes of his new gun. Unfortunately for Mr. Ingram his Model 10 was rejected by all of those companies who even bothered to respond. The day of the submachine gun as a military weapon had passed, replaced by assault rifles like the AK-47 and M16. It seemed that Mr. Ingramโs Model 10 was destined to only exist as a footnote in firearms history, however his luck changed when he met Mitch Wer-Bell III.
Mitch Wer-Bell III was an OSS officer during World War II. After the war he started a Georgia based company called SIONICS, specializing in suppling equipment for โspecialโ government operations. Sound suppressors were his primary product. When Wer-Bell met Gordon Ingram, and was able to closely examine the Model 10 submachine gun, he envisioned it as the perfect covert weapon for mounting one of his SIONICs sound suppressors. Soon, with the assistance of Wall Street financers, the Military Armament Corporation was formed. During 1971, Ingramโs submachine was placed in series production, most with threaded barrels for mounting a suppressor. Like the drum magazine in a Thompson submachine gun, the sound suppressor became a part of the Model 10โs image. Most foreign and domestic government sales of Ingramโs weapon, becoming known as the MAC-10, included a sound suppressor. The suppressors could even be ordered with the same serial number as its host submachine gun, except for the serial number prefix which identified the caliber: S-1 for .45, S-2 for 9mm and S-3 for the .380 caliber Model 11.
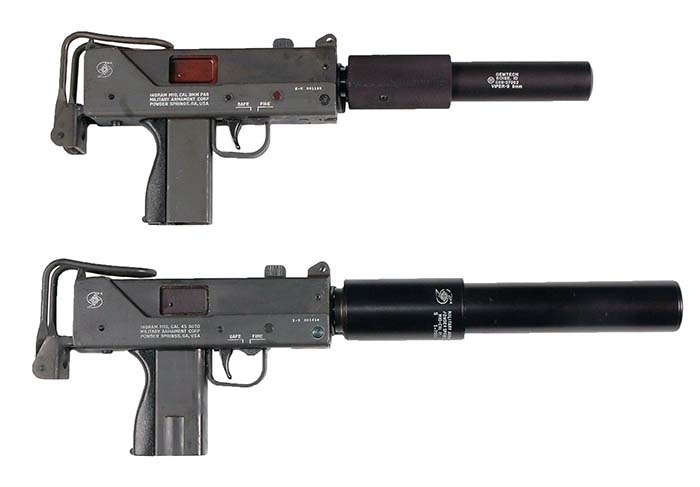
The Military Armament Corporation sold the M10 and M11 submachine guns and suppressors to over fifty foreign countries. The U.S. officials felt that any weapon that was fitted with a suppressor was an assassinโs tool, and didnโt want any U.S. firms offering such weapons commercially to overseas customers. During 1974, the United States Department of State placed an embargo on the export of sound suppressor devices to Latin America and other developing area and ordered a review be made of the situation. A study was undertaken, and a policy decision was released on Thursday 2 May 1974, resulting in the suspension of all munitions export license applications to developing nations involving suppressors, and automatic weapons designed to be equipped with suppressors. The rational for the decision was in part attributed to the concern โThat the widespread dissemination of suppressor equipped automatic weapons in the Latin American region represented an undue threat to the safety of United States Government and host country officials. This would be especially true in the event that such weapons fell into the hands of terrorist groups or were used for unlawful purposes.โ To illustrate just what an essential part the suppressor was to the MAC submachine gun, foreign sales virtually dried up after the ruling.
To prevent fitting a suppressor, all subsequent MAC submachine guns that were exported were fitted with permanently attached barrel extensions that covered the threads; an attempt to remove the extensions would destroy the threads. Later production guns lacked the barrel threads required for attaching a suppressor. The suppressor was what attracted many buyers to the M10 and M11 weapons, without it the MACs were just another submachine gun, competing with many more practical designs like the Israeli UZI, Italian Berettas and the popular German weapons of Walther and Heckler & Koch.
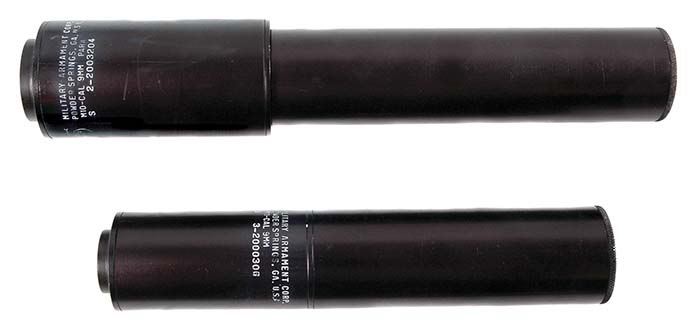
Mitch Wer-Bellโs suppressors for the Ingram Model 10 were a two stage design for both the 9mm and .45 caliber Model 10. The sound suppressor consisted of a primary tube that was 3.75-inches in length and 2.125-inch in diameter. The tube served as the gas expansion chamber, and was filled with aluminum or brass eyelets to provide maximum heat absorption. The secondary tube was 7-inches long and 1.625-inches in diameter. The front tube had a conical baffle to trap gases and absorb heat and direct the gases rearward, delaying movement into the next component. After the gases passed through the baffles, they encountered a helical diffuser that absorbed additional heat, and caused the gas to swirl around its left-hand twist design. The next component was another helical but, with a right-hand twist, that also absorbed heat, and slowed down the escaping gases, by reversing their direction. In the secondary tube was an encapsulator, which was threaded onto the tube used to secure the components in place. Positioned at the end of the tube was a replaceable module that contained several neoprene wiper discs and spacers. The neoprene wipe discs provided a gas seal as the bullet passed through them further delaying the exit of the propellantโs gas to the atmosphere. The service life of the wipes was relatively short, eroded away as the bullets passed through them, replacement wipes were available from the factory.
Although the MAC-10 suppressors were considered state of the art during the 1970s, they had quite a few shortcomings. One of the most glaring problems was the coarse barrel threads used to mount the suppressor, 7/8-10 threads per inch for the .45 caliber guns, ยพ-10 TPI for the 9mm model and 5/8-11 TPI for the .380 caliber M11. The problem with the choice of threads was that the suppressor would loosen because of the heat and vibration generated by the rapid cyclic rate of the MAC submachine gun. This usually resulted in misalignment and baffle strikes, damaging the suppressor. The reason for choice of threads is unknown, but a plausible explanation could be that the coarse muzzle threads were not easily damaged when the suppressor wasnโt attached. Thus a thread protector was not required, nor was one available from the factory. Another possible reason for the threads was that the suppressor could be mounted or dismounted quickly. One fact that is known, the Model 10โs designer Gordon Ingram, disagreed with the choice of threads.
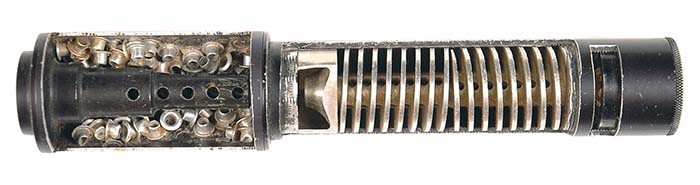
One of the standard operating procedures to prevent MAC suppressors from coming loose during firing, was for operators to place their weak hand on the device to keep it from rotating. To protect their hands from being burned by the suppressor, the early MAC suppressors were sold covered with a foam rubber sleeve. However, when the suppressor got hot, the sleeve would expand, become loose and slide off. During sustained fire, the rubber cover would begin to melt, and leave a sticky mess on the suppressorโs outer tube. Later suppressor covers were made of a heat and flame resistant material developed and manufactured by DuPont called Nomex. The Nomex covers were manufactured by Southern Textile of Atlanta. A spring was sewn inside the fabric to secure it to the suppressorโs tube. The Nomex covers eventually replaced the problematic foam rubber sleeves.
Another problem with the MAC suppressors was the neoprene wipes. The wipes would need replaced after firing approximately 200 rounds. Not only did they require periodic replacement, but they greatly affected accuracy. While not generally a concern while engaging targets at 10-15 feet, at distances over 50 feet accuracy was dismal. However, accuracy would improve slightly as firing would cause the center of the wipes to enlarge, but at the same time the report would get noticeably louder.
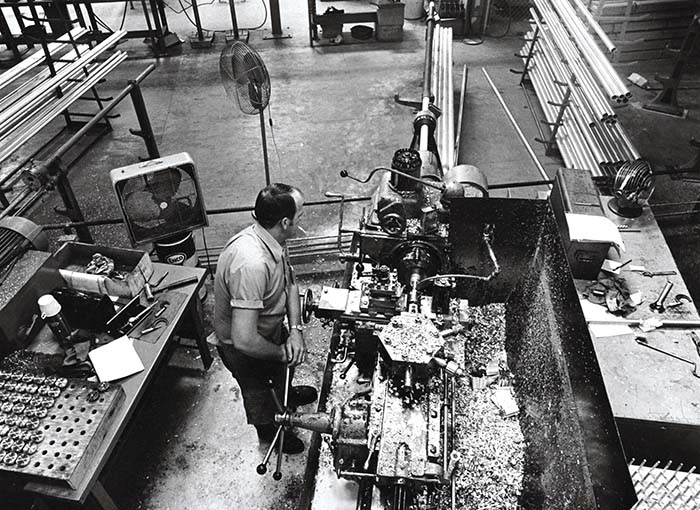
The Gemtech Viper
One of the founders of Gemtech, Phil Dater, procured his first Ingram submachine gun and suppressor, a .380 caliber Model 11 during 1976. After disassembling and studying the MAC suppressor, and Mitch Wer-Bellโs patents, Dr. Dater began to think of ways to improve its performance. The first problem he wanted to address was the inefficiency of the two helicals in the secondary tube. He replaced the helicals with a series of aluminum spacers and stainless steel washers formed into baffles. To address the problem of the wipes, he fabricating a wipe-less replacement end cap with a conical baffle profile. The upgrades significantly reduced the decibel level, while eliminating periodic replacement of the wipes. Much to the delight of MAC suppressor owners, โDocโ Dater began to market his wipeless endcap as the MAC-END. A few years later a complete upgrade kit consisting of baffles, spacers and the wipeless end cap were offered. The ATF ruling that made possession of suppressor parts a felony ended the availability of the kits.
While Ingramโs Model 10 and 11 submachine guns came from the factory suppressor ready, the weapons have been largely ignored by modern suppressor manufacturers. One of the first non-MAC factory suppressors was designed by Phil Dater and Lynn McWilliams during 1986. Designated as the M10A3 suppressor, they were manufactured by AWC of Houston, Texas. Basically, they followed the original MAC design, but improved it by replacing the eyelets in the primary tube with steel mesh, and the helicals in the secondary tube with stainless steel baffles. The module containing the rubber wipes was replaced by a wipe-less MAC-END. The M10A3 was approximately 2-inches longer than the original MAC cans. The M10A3 was available in 9mm or .45 caliber. There was also a .380 caliber model designated as the M11A3. However, the problem of the suppressor coming loose because of the coarse barrel threads remained. The M10A3 suppressor was superseded by the legendary MK-9 suppressor configured for the MACs.

During 1999 Gemtech began to offer a modern suppressor specifically designed for the MAC submachine guns and SWDโs M11/Nine, the Viper. The Viper was designed to address all of the shortcomings of the 1970 era MAC suppressors, and at the same time retain the classic look of the original. The Viper features precision CNC machined aluminum baffles and a domed front end cap. This wipeless design provides excellent performance in terms of both sound suppression and operational life. To mimic the appearance of the original MAC two-stage design there is an oversize knurled heat shield at the muzzle end of the suppressor. But the spring-loaded shield isnโt just for appearance, it serves as a non-slip grip surface, and is part of the system used to secure the suppressor on the weapon.
To address the loosening problem a unique locking system was designed. The system features a collar that is designed to slide over the narrow shelf, just aft of the barrel threads. The collar is secured in place by three set screws. The front of the collar has angled ratchet-type teeth are designed to mesh with similar teeth on the rear of the grip tube. When engaged, the system keeps the suppressor from working loose during firing. To remove the suppressor from the submachine gun, simply slide the heat shield forward to disengage the locking mechanism and unscrew the suppressor from the barrel threads.
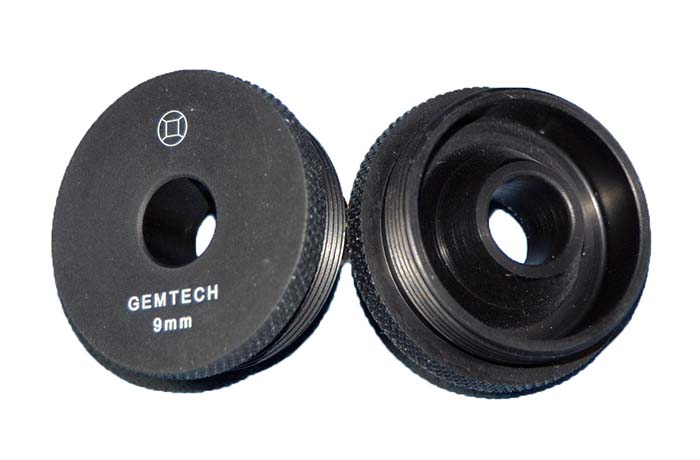
The Gemtech Viper is available for all of the MAC-10 submachine guns in 9mm and .45 caliber and its clones, including SWDโs M11/Nine that has the same muzzle threads as the 9mm MAC-10. There is also a limited production Viper for the .380 caliber MAC-11. The only difference is the physical dimensions and weight. The .45 caliber Viper has an overall length of 9.3-inches the outside diameter of the heat shield is 1.9-inches; the diameter of the suppressor tube is 1.5-inches; weight is 12-ounces. The 9mm Viper has an overall length of 9.0-inches. The diameter of the heat shield is 1.8-inches; the suppressor tube is 1.4-inches in diameter; the 9mm Viper weight is also 12-ounces. The overall length of the .380 caliber Viper is 8.7-inches, the heat shield measures 1.7-inches, the outside diameter of the suppressor is 1.2-inches, weight is 11-ounces. The tubes are fabricated from 7075 aluminum and finished in a non-reflective flat black color. All of the Viper suppressor are rated for full-auto fire. The Gemtech Viper series are made to close tolerances, not possible during the 1970s. The suppressors are constructed of modern materials and are smaller, lighter, more efficient and safer than the original MAC suppressors.
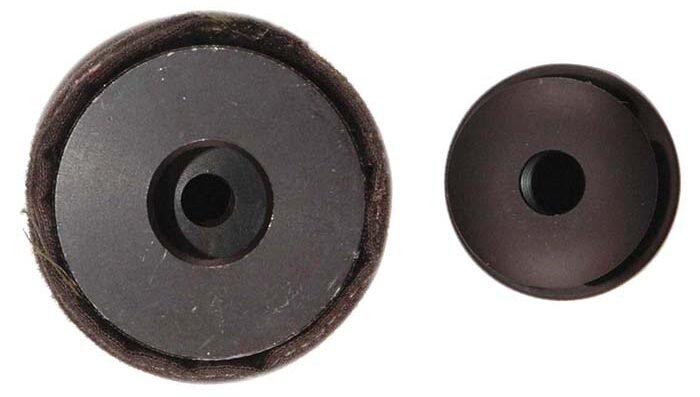
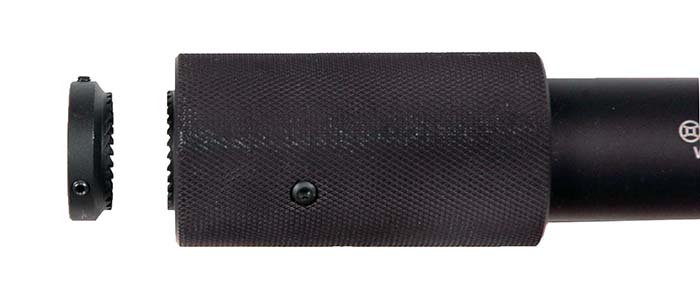
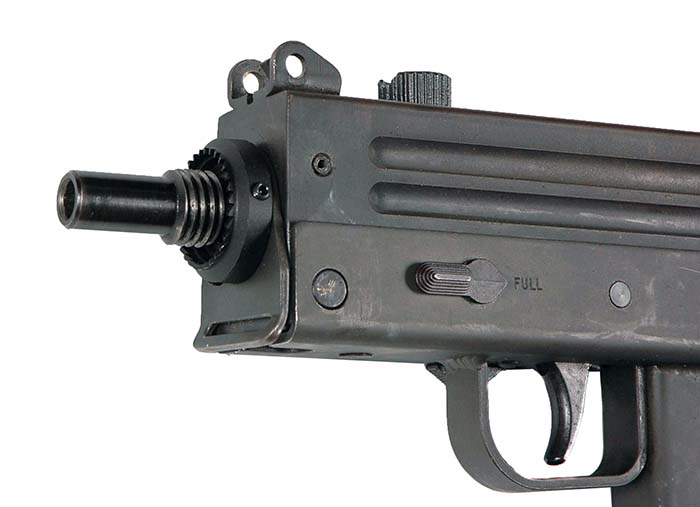
This article first appeared in Small Arms Review V20N5 (June 2016) |