By Michael Heidler
Shortly before World War II, interest in a semi-automatic rifle to strengthen the armed forces reawakened in Sweden, but (luckily) the feared case of defence did not occur. After the War, the Automatgevär m/42 remained in active service for many years, was even manufactured in Egypt and is still popular with sports shooters today.
During World War I, Sweden had already tested French and Russian semi-automatic rifles, but this half-hearted venture soon came to nothing. Eric Wallberg of the Kungliga Armétygförvaltningen (Royal Army Administration) tried in 1938 to convert the already-introduced m/39 bolt-action rifle to automatic fire. However, it soon became clear that this project would have little chance of success. This was followed by a call to various weapon designers to develop a semi-automatic rifle.
Towards the end of the trials and comparison shooting, only two gas-operated models were still in the game. One designed by the Finnish officer Carl Pelo and one by Erik Eklund, the owner of the company AB C.J. Ljungmans Verkstäder in Malmö. His company had nothing to do with weapons but produced pumps and fuel dispensers for gas stations. In August 1941, the board of examiners finally chose Eklund’s rifle because it was lighter and consisted of fewer parts. The official introduction to standard armament was on December 5, 1941, as “Automatgevär m/42,” or in short, “Ag m/42.” That was not even 1 year after the completion of the prototype. The Swedish nomenclature does not distinguish between semi-automatic and fully automatic rifles, but only between Kulsprutegevär (light machine gun) and Kulsprutepistol (submachine gun). The production of the new gun was taken over by the state-owned arms factory Carl Gustafs Stads Gevärsfaktori in Eskilstuna.
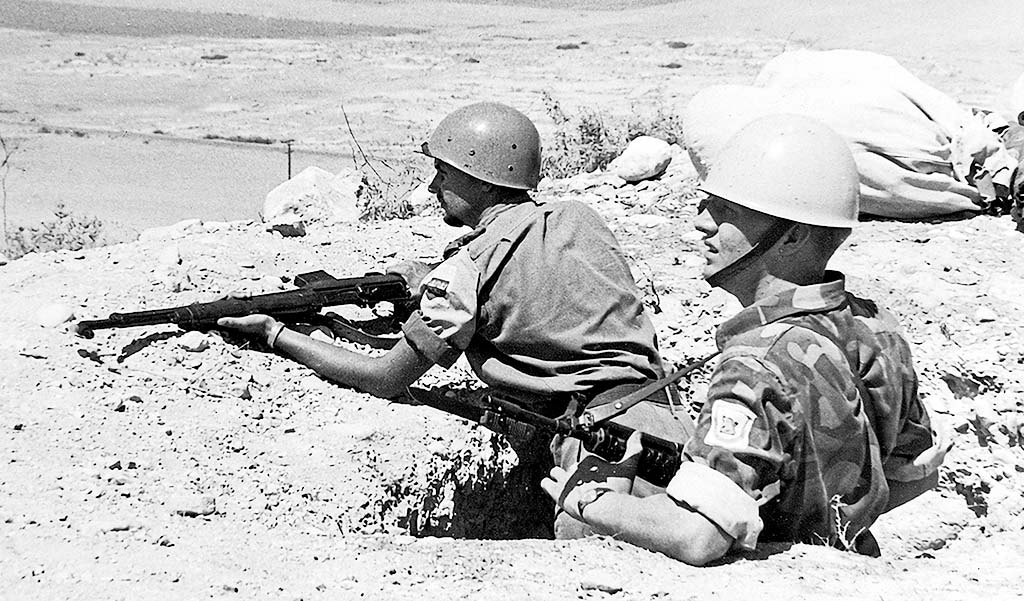
Erik Eklund had from the very beginning attached importance to a mechanically simple construction. Therefore, his rifle is operated by means of a direct-impingement gas system that directs gas from a fired cartridge directly to the bolt carrier. In its forward position, a cup attached to the bolt carrier slips over the end of the gas tube and prevents the gas pressure from escaping. Such systems are simple, but hot gases and powder residues get directly into the weapon and can cause malfunctions due to deposits if not cleaned properly.
The Ag m/42 uses a tilting breech block that drops down into a receiver recess for locking. This tilting allows gas pressure in the barrel to lower to safe levels before the cartridge case is ejected. After the last shot the bolt carrier remains in the rear position, and the shooter can reload. The Swedish military, however, did not recognize the advantage of an interchangeable magazine and decided that the preferred method was reloading from five-round stripper clips from above into the 10-round box magazine that remains attached to the gun. The Ag m/42 has a wing safety located at the rear of the receiver: right position is safe; left position is fire.
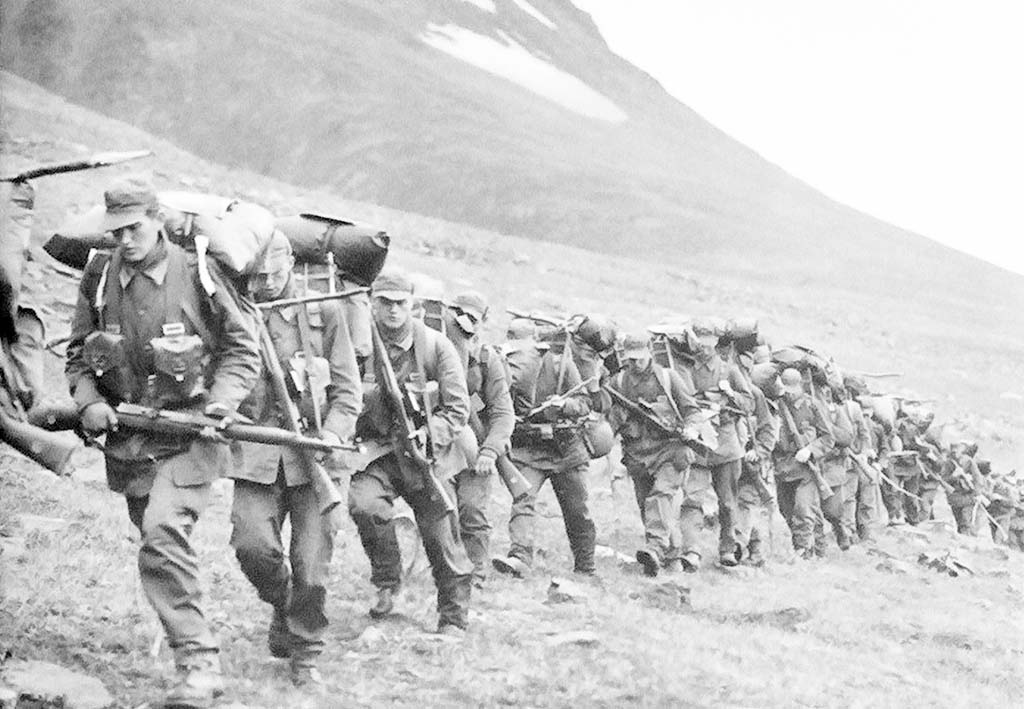
Since 1894, the Swedish Army has used the 6.5x55mm skarp patron m/94 projektil m/94 (live cartridge m/94 projectile m/94) with a round-nosed bullet. A new pointed bullet with a boat tail to reduce aerodynamic drag was developed for civilian weapons before WWII. Its trajectory was very flat, and the accuracy of the shot was therefore high. In 1941, the Army accepted this bullet as “prj m/41” (prj stands for projectile). The adjustment wheel on the Ag 42/m rear sight therefore has a small cut-out through which the distance marks and the contour of one of the two projectiles can be seen. The scale-ring and the contour inside the wheel are exchangeable. This allows the shooter to adjust his sight depending on the ammunition used. The sight can be adjusted for every 100m, from 100m to 600m with round-nosed ammunition or 100m to 700m with pointed ammunition. During the first troop trials, the rifle showed a very variable accuracy. Since the gas tube is located directly above the barrel and is also firmly connected to it, both components cannot expand freely when heated. With hot barrels, the dispersion on 100 meters ranged from 83mm to an alarming 356mm.
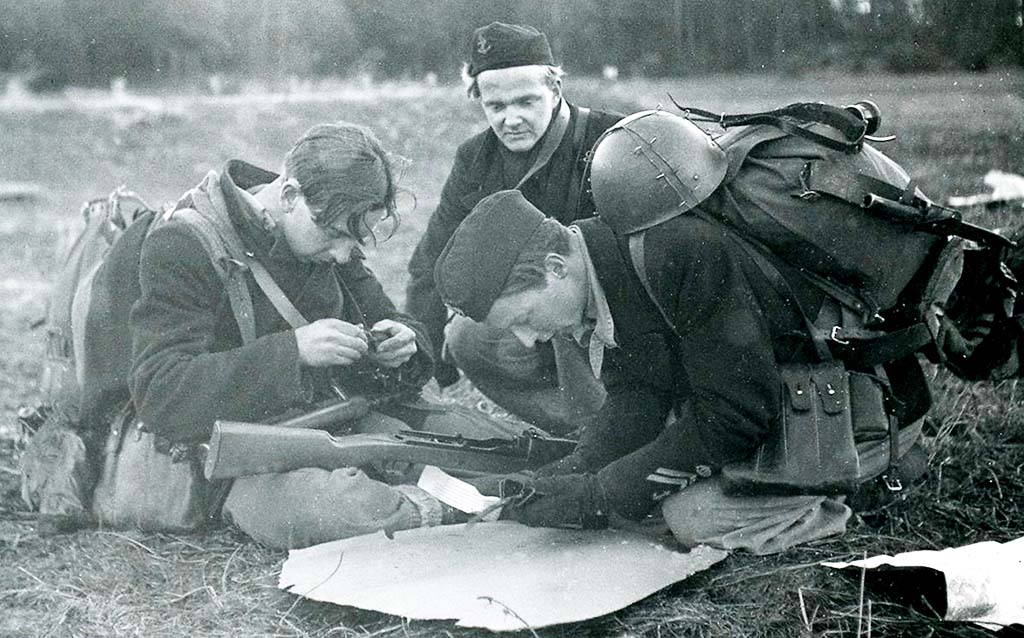
The Ag m/42 did not have a good start in the Swedish Army in other respects as well. During regular shooting exercises the extractors broke constantly. The development department then found out that the carbon content in the steel supplied by Fagersta bruk ironworks varied between 0.15% and 0.40%, which of course had an effect on stability. This was a serious mistake made by a company whose chief engineer at the time was none other than Johan August Brinell, a member of the Royal Swedish Academy of Sciences and inventor of hardness-testing methods. Initially, one extractor only lasted about 4,000 shots. Another problem was the susceptibility of the gas tube to rust, making a change to stainless steel necessary. The magazine release also had to be modified, as the magazines fell out easily when handling the weapon.
In 1953, a program to upgrade the entire stock of weapons to the latest state of the art began. After 3 years the work was completed. In addition to the changes mentioned above, the cover of the bolt carrier was fitted with two lateral knobs for better gripping by hand, and the sight got a different adjustment wheel. The case deflector was given a thick rubber jacket so that the empty cases were no longer deformed and could be used for reloading. The new magazines had an additional hook for a better grip, and the multi-piece, screwable cleaning rod was replaced by a one-piece rod. The reworked weapons got the suffix “B” and were now called “Ag m/42B.” The reworking was so thorough that today only a few weapons still exist in their original condition. Most of them had been taken home during the War by Norwegian police units after their training in Sweden and thus escaped the reworking.
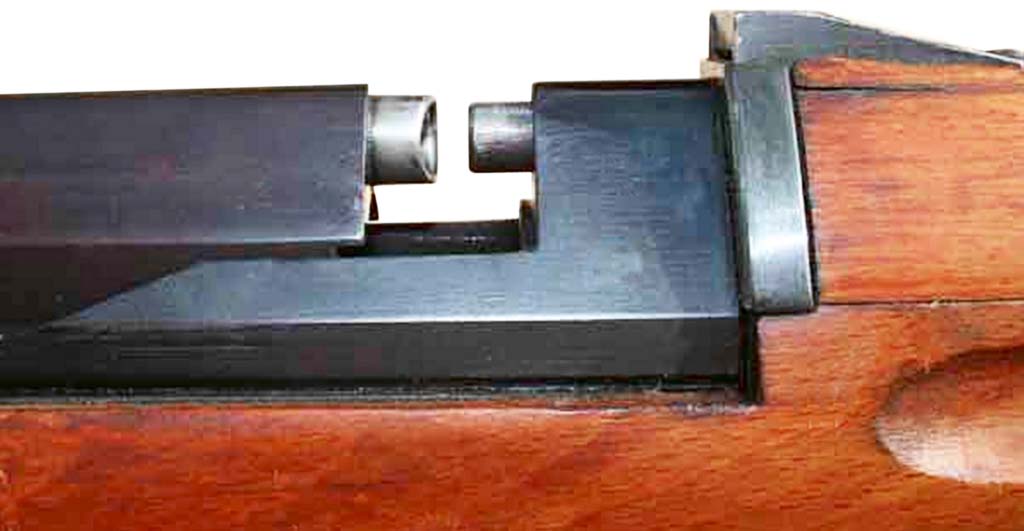
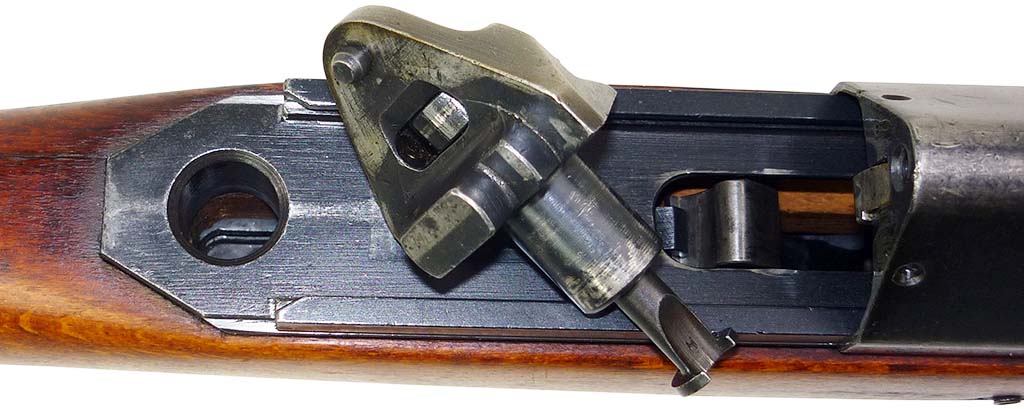
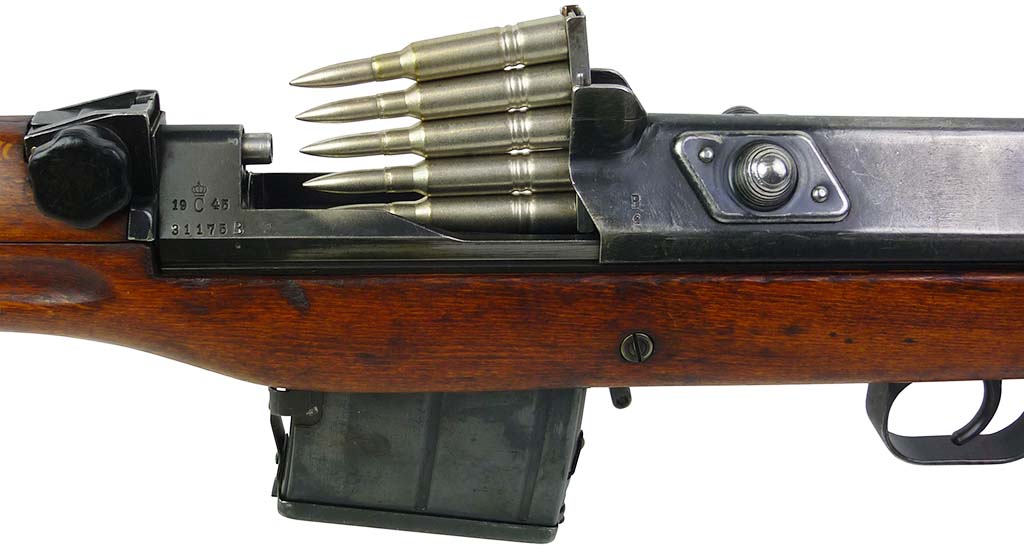
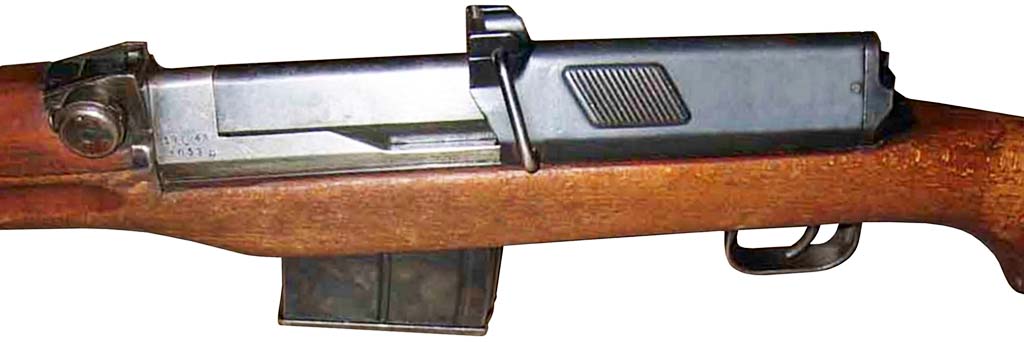
The Carl Gustafs Stads Gevärsfaktori in Eskilstuna produced about 30,000 pieces of the Ag 42/m. The reworking made it a reliable and popular weapon that remained in active service until the 1960s. After an extensive selection process, Sweden chose the assault rifle G3 from Heckler & Koch (HK) as its successor and from 1965 to 1985, a licensed version was produced as the “Ak 4” (Automatkarbin 4) by Husqvarna and Carl Gustaf.
After a conversion to NATO caliber 7.62x51mm, some Ljungman systems served as ranging guns for the 90mm anti-tank gun Pv-1110 under the designation “Inskjutningsgevär 5110.” From 1949 on, Denmark tried to improve the Ag m/42 design, and the company Dansk Industri Syndikat A/S (DISA) produced various weapons in different calibers under the designation “Madsen/Ljungman.” After only about 50 test pieces, the project came to an end in 1955.
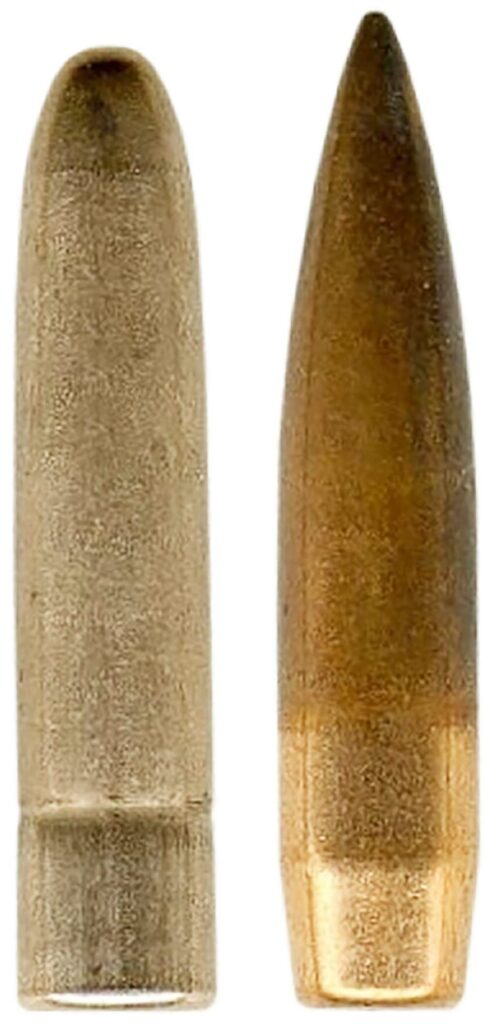
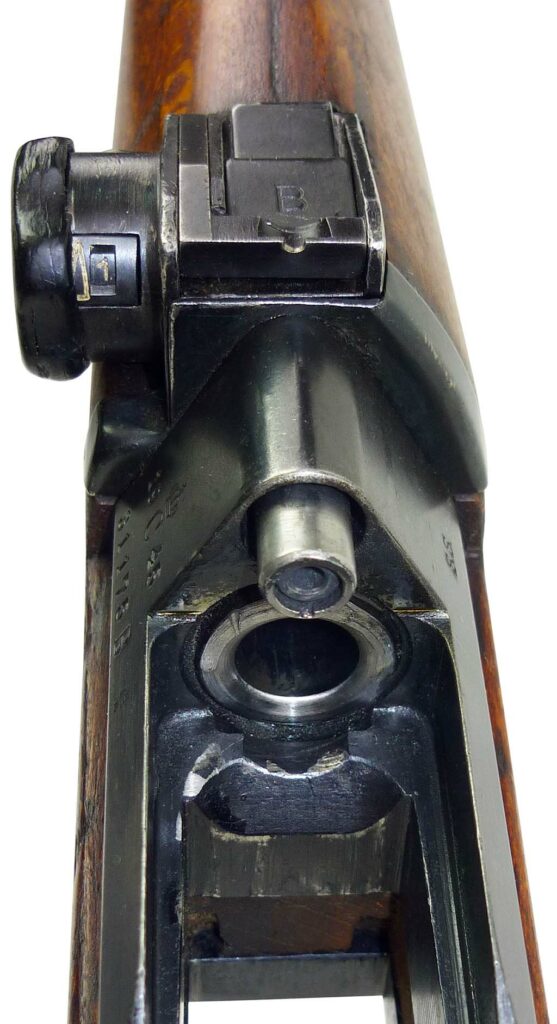
A few years later, Sweden once again made a good deal and sold the manufacturing rights and all the machines no longer needed from its own production (which had long since ceased) to Egypt. The copy was called “Hakim” and differs in some details from the original Ag m/42. Because of the large WWII stocks of cartridges in caliber 7.92x57mm, the rifle was equipped for this stronger caliber and fitted with an improved muzzle brake to reduce the recoil. The fluctuating ammunition quality made a gas-pressure regulation necessary, and so the Egyptians included an adjustable valve screw in the gas port. Some 70,000 Hakims rolled off the assembly line at the Al Maadi Company for Engineering Industries (Factory 54) in Cairo. In addition, about 8,000 pieces of the short version called, “Rasheed” in the Soviet caliber 7.62x39mm and with folding bayonet were made before the licensed production of the Kalashnikov AK-47 went into series production in the mid-1960s.
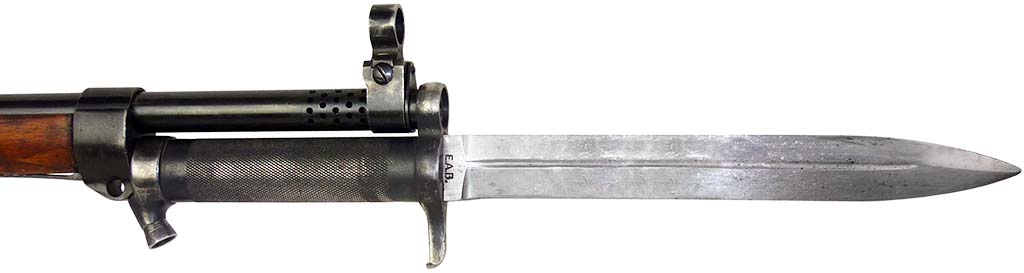
Technical Data of the Ag m/42
Caliber 6.5x55mm
Length 47.8in 1.214mm
Length of barrel 24.5in 622mm
Weight (empty) 10.4lb 4.7kg
Magazine capacity 10 rounds
Rate of fire 40 rounds/minute
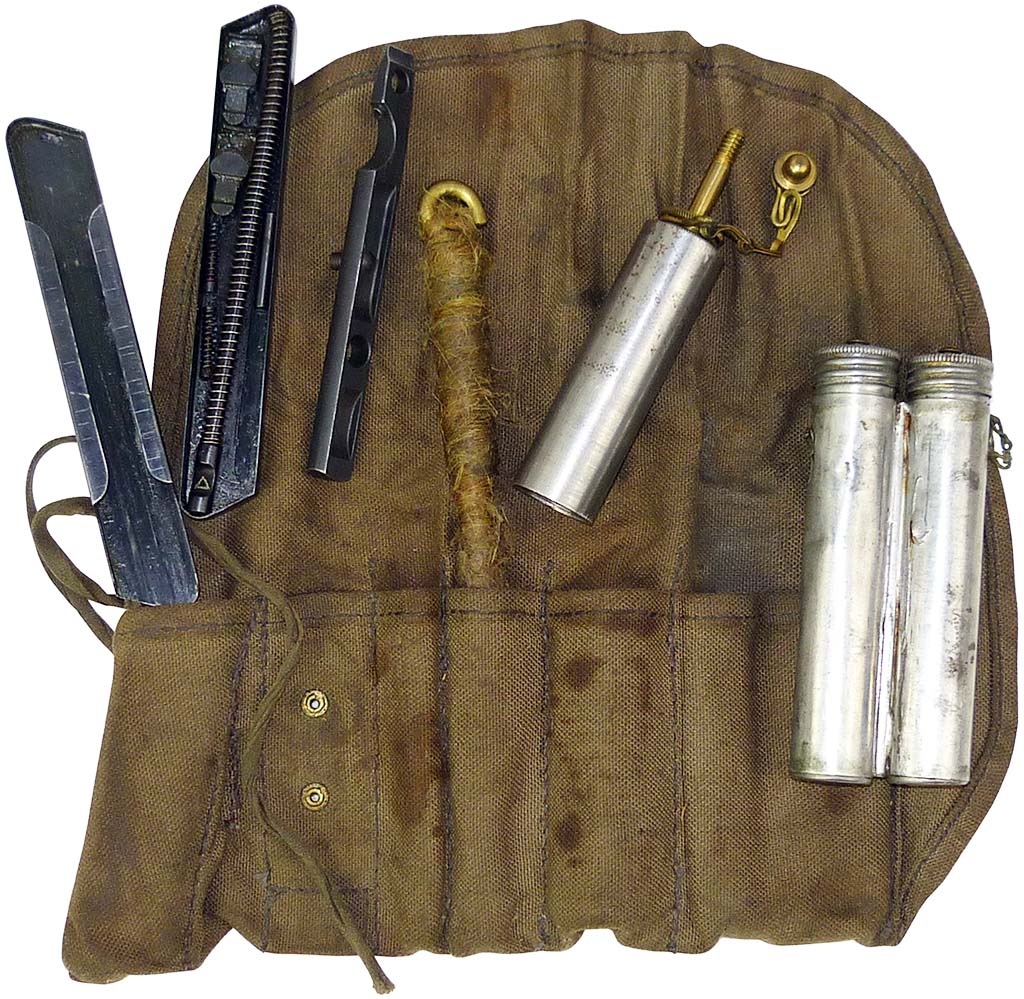
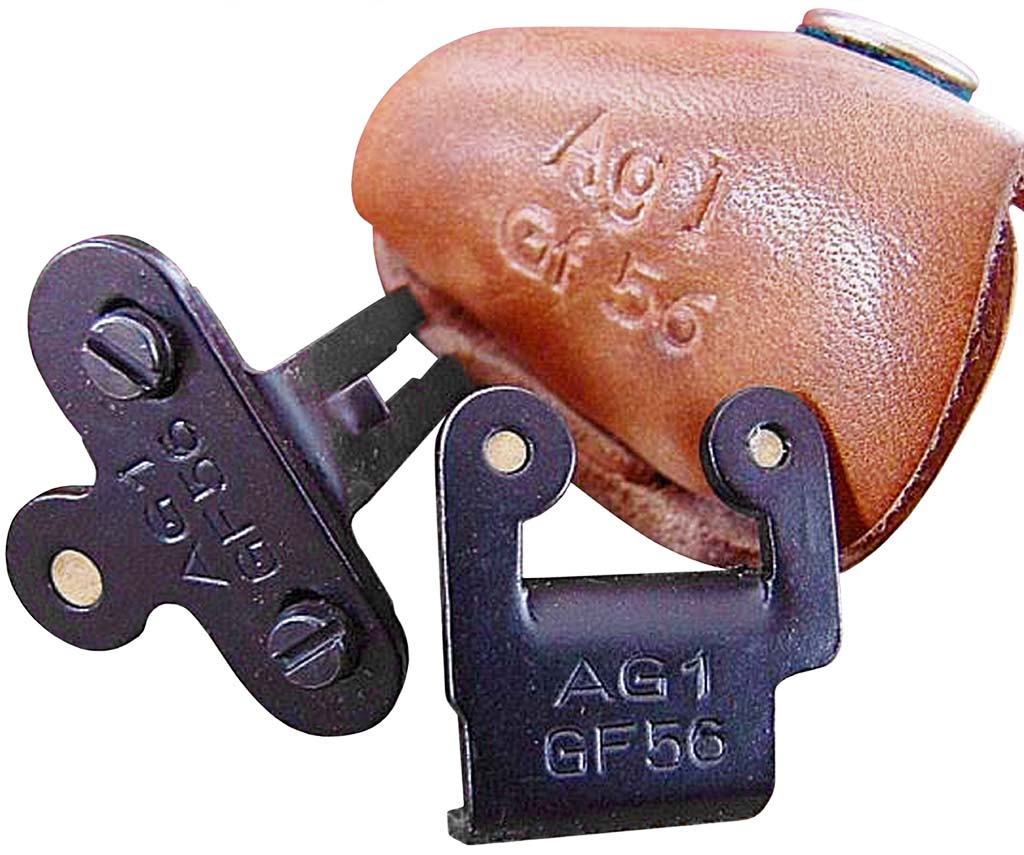

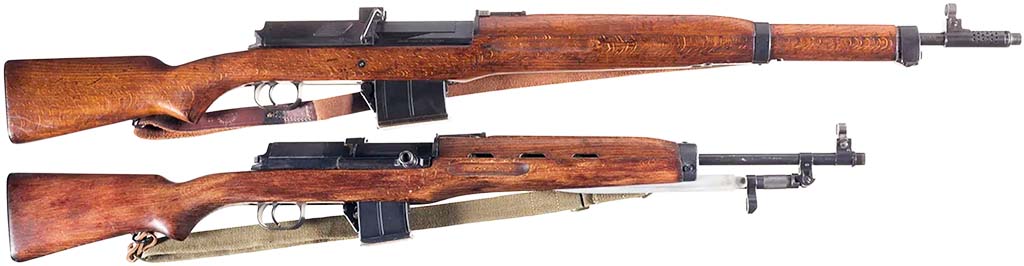
This article first appeared in Small Arms Review V25N3 (March 2021) |