By Jay Bell –
In ammunition manufacturing, daring is rare. The ammunition industry in the U.S. is staid. Many popular cartridges and weapon designs are more than 100 years old: look at the .50 BMG, .30-06, and .45 ACP cartridges and the M2 machine gun, Garand rifle, and 1911 pistol. Therefore, when you see something novel, you are taken a little off guard. I had the opportunity to visit with a group of ammunition component-making dynamos at First Breach of Hagerstown, MD. They definitely caught me off guard.
What Makes First Breach Different
First Breach is cupping from brass and copper strip to make their 9mm and 5.56/.223 cartridge cases and bullet jackets. Second, they are molding their lead ingots. Third, they are extruding their lead wire.
For the layman, this means they’re starting with raw materials that are common across all manufacturing industries, so they are not beholden to anyone that is part of the ammunition industry base. In addition, making their own cups allows them to control quality. It also prevents them from being stuck with so-so-quality cups. Multiple times in my days manufacturing brass cartridges, I received cups that did not match the engineering drawing. We had the choice of accepting the product or waiting another six months for a reworked part. Unfortunately, we were often forced to take the poorly made product and fight it all the way through the manufacturing process.
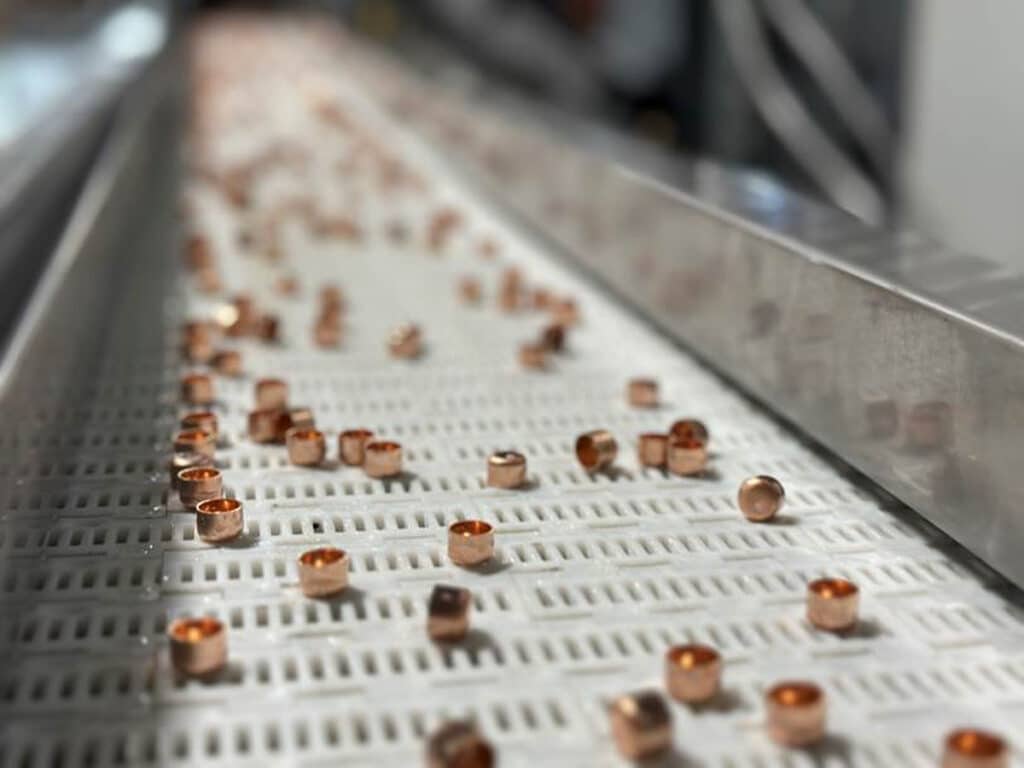
I’m going back in the mental file cabinet to try to remember the last time something so bold was undertaken in ammunition. I can’t think of anything in the last 50 to 60 years. The nearest effort is SIG Sauer’s venture into ammunition in the 2014 timeframe. However, that started as a partnership with another company and expanded slowly. It took around three years to break off into their own facility in Arkansas. On the other hand, this venture getting off the ground and jumping into so many areas at once is quite bold. Cupping is a difficult and challenging operation and makes some of the other manufacturing aspects seem simplistic. One can make a mistake in the cupping process and not understand the full implication of the mistake until it’s on the ammunition testing range days later. The good news is they seem to have the right equipment designs, tooling designs, fabrication equipment, gaging, and support staff to successfully pull off this massive endeavor.
But Wait – There’s More
They are also going to make primers! They will make these from the strip and other basic raw materials. To the best of my knowledge, there has been no one in the last 50 years that has started with this level of commitment or investment in small-caliber ammunition. This facility is so impressive that I’m certain it will be here for decades to come. It’s almost too big to fail. All the other names in the industry that have become industry mainstays (ex. Hornady, Barnes, Sierra) have started much smaller and slowly grew their business over time. I had the opportunity to visit Barnes bullet in the early 1980s when it was a very small operation in an outbuilding on the Brooks family farm. It grew slowly over time. First Breach is trailblazing a path an ammunition manufacturing path in the U.S.
Modern Machines
To make things even more interesting and rare, they are doing it all with brand-new equipment made in Turkey. They have partnered with Atesci, a 20-year-old company with a great reputation and a long history of success. I have been aware of this company for the better part of those 20 years; however, I have never seen their equipment stateside. I can now say that I have seen their equipment firsthand and it is impressive. The equipment appeared to be well-made and designed. The presses are very stout and with excellent fit and finish. First Breach is so new that their cupping, 9mm case, 9mm bullet, lead ingot, and lead wire lines were all set in place but were idle during my visit as they waited on an electrical transformer to power up the machines. Apparently, supply chain issues affecting us at the retail level also have an impact on industrial power transformers, as well. As I am wrapping up this article, my point of contact informs me that the machines are running, and product is flowing.
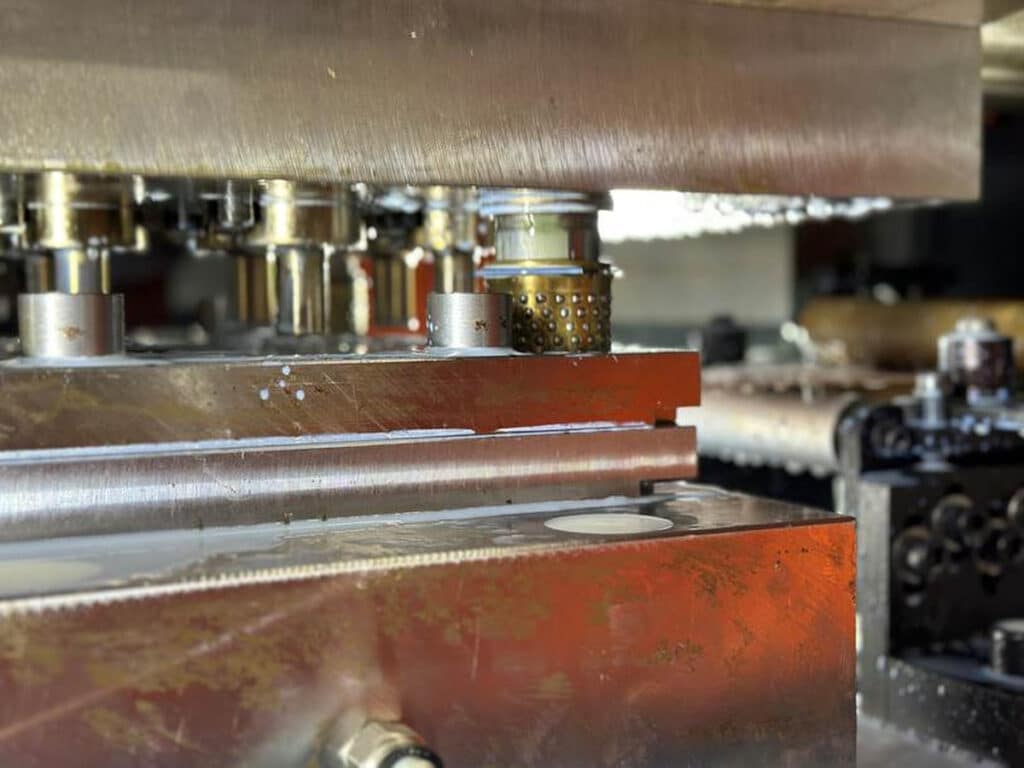
The lines saw many of the modern items one would expect to see in modern manufacturing. They have Siemens LCD touchscreen control panels and individual fault detection sensors on each tooling station on the 9mm case machine to instantly stop the machine should a part not transfer. When a part does not transfer, it means that it most likely is stuck in the die and/or the tooling has broken. If the machine continues to run, it will insert the next part on top of another part and cause even more tooling damage. These types of crashes are typically catastrophic. It’s an important consideration when each of the 16 tooling stations cost over $2000 each.
The equipment stations also had an array of gages to measure the parts coming off the machine. This is also a world class thing First Breach and Atesci are bringing to the table. The operator can inspect parts coming off the machine, as they are built. This will ensure that they will not make scrap. It will also help identify when tooling is wearing or in need of adjustment. When this is done correctly, product quality is assured. They are also planning an underground ballistics lab to test the products in-house, even though finished ammunition is not on the radar at the moment.
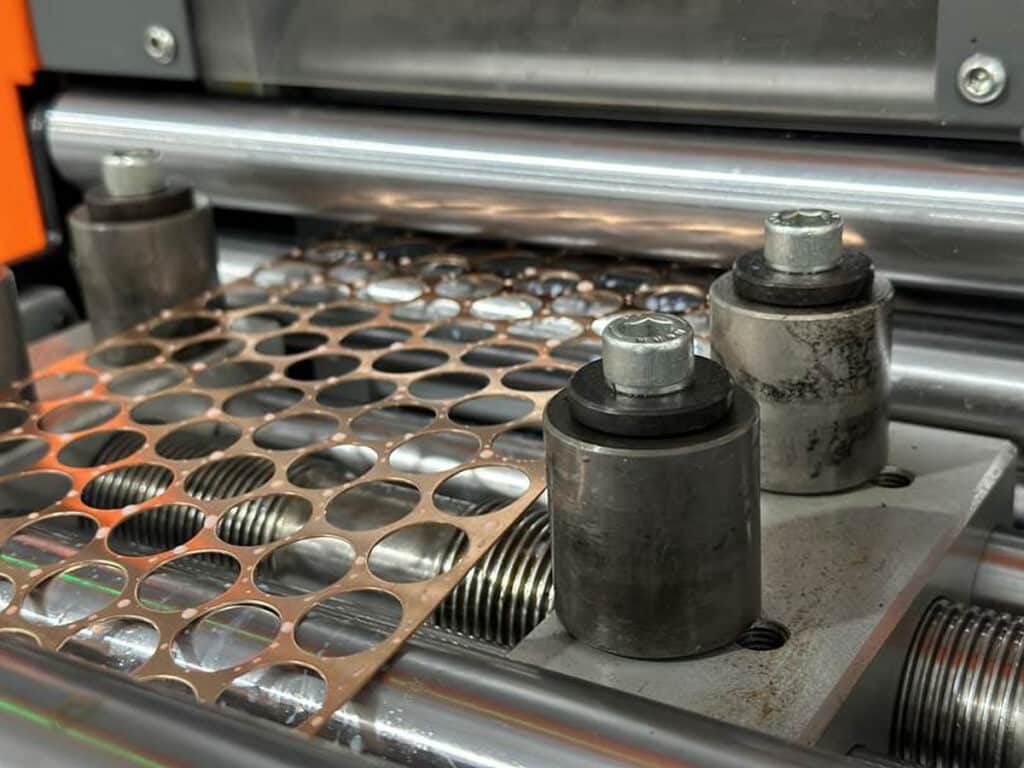
Room to Grow
First Breach is doing nothing small and simple. They are leasing space in an old Fairchild aircraft manufacturing complex. Space is massively abundant the company’s existing lines talking up about a quarter of the building’s total 882,575 available square feet. I believe they used to manufacture the A-10 Warthog in this complex. For a size comparison, the entire building’s comparable to 15 football fields. I don’t think I have ever been in buildings so large in terms of square feet or so tall with an amazing amount of ceiling clearance – 46 ft! Needless to say, the production lines were spaced out and the company has plenty of room to grow.
More to Come
There are many more great things to come from the First Breach team. The team I met with included First Breach CEO Jeffrey Low, COO Jordan Low, Director of Operations Ben Donivan, and Senior VP of Business Development CJ Dugan. All are all professionals that can, and will, do great things. I’m excited about this company’s prospects. Standby for more on First Breach, as I intend to write a follow-up article once their primer lines are running.