By Paul Evancoe
In today’s age of modern weaponry we tend to forget the historical significance of edged weapons and forged body armor in the evolution of warfare. The days when a fine edged sword made from Damascus steel, and full body armor forged and fitted by a skilled armorer, often meant the difference between a knight’s life and death. While those times are far behind us, the demand for yesteryear’s high quality combat edged weapons and fitted body armor exists today.
A small nondescript factory that authentically produces just such weapons is located in Marriottsvile, Maryland, not far from Baltimore’s busy west side I-695 beltway. Owners, operators and brothers, Matt and Kerry Stagmer, have guided Baltimore Knife and Sword (BKS) into being the predominant name in stage combat weaponry for the past several decades.
BKS’s mainstay is stage combat pieces, but they do accept a limited number of custom orders each year. They also make a handful of original design “one offs” for general sale at their dealers around the U.S. In addition, about once a year they smelt iron from ore and create their own blend of steel for high-end custom swords and knives. They also forge unique pattern-welded and crucible steel works of edged art – more on that in a moment.
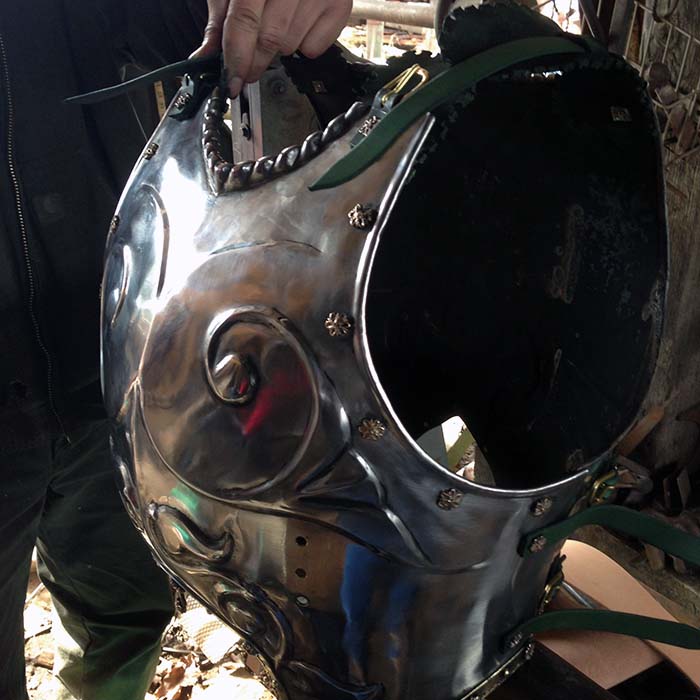
BKS makes every weapon fully functional. “We make a sword first,” Kerry Stagmer asserts, “and then we make it look nice.” Every piece that leaves the shop is a functional durable piece that is built to survive the wear and tear of combat use. The Stagmers guarantee their work. “Our stage combat swords are forged, welded and leather wrapped for a good reason,” Kerry confidently smiles. “Over the past two decades we have found, through trial and error, that our means of construction out performs any other in day-to-day steel-on-steel contact. The handles almost never need repair. We strive to make swords that never break,” he claims, “but eventually all things can break over years of stress so we fully guarantee our work and we’ll fix it for you should it break. You get it back to us and we take care of the rest.”
A unique offering by BKS is edged weaponry made of crucible (Wootz) steel. Wootz steel, as it was originally called, is believed to have originated during the 6th century in South India and Sri Lanka.
Wootz was made by smelting iron ore in a crucible furnace, which yielded wrought iron. The fuel used to fire the forge was mostly composed of charcoal and of sun-dried brattis or cow-chips. After two or three hours smelting, bamboo and leaves from plants such as Av?rai, both native to India and Sri Lanka, were added to the crucible to provide the carbon source that turned the wrought iron into high carbon exceedingly fine quality steel.
The wrought iron was heated to a bright yellow color in an animal skin bellows-driven forge and hammered to rid the iron of slag (impurities). This process was repeated until the slag content was judged minimal. Only then would it be forged into an edged weapon.
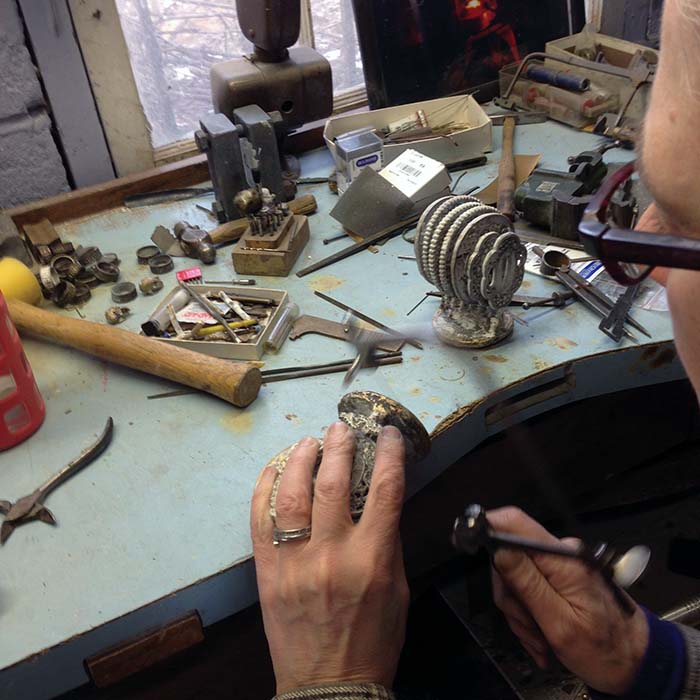
Wootz steel was widely exported and traded throughout ancient Europe and the Arab world, and became particularly famous in the Middle East. The Wootz was exported by Arab traders as cakes of steely iron that came to Damascus where a sword-making industry developed, using this steel to forge uniquely patterned swords and knives known as Damascus steel. Damascus steel is uniquely characterized by a metallic pattern caused by bands of clustered Fe3C particles made of micro-segregation of low levels of carbide forming elements. As the metal is worked, it is hammered into uniformly thin sheets that are then layered like a sandwich one on top of the other. This sandwich is then heated to a bright yellow color and forge-welded together. This forge-welded billet is now folded back upon itself creating even more layers and forge-welded again. Dozens of layers can be achieved using this process. Once a sufficient number of layers are achieved, the billet is hammered into an elongated sword blade or knife. The result when shaped and finished is a blade that exhibits beautifully colorful steely lines with a flexible arm and functional edge-keeping character not found in other types of steel.
Around the 17th Century, Damascus swords made from this legendary steel aroused the curiosity of the European scientific community. The use of high carbon alloys was previously unknown in Europe so the investigation into Wootz steel played an important role in the development of modern English, French and Russian metallurgy – and thus the ordnance of their warfare.
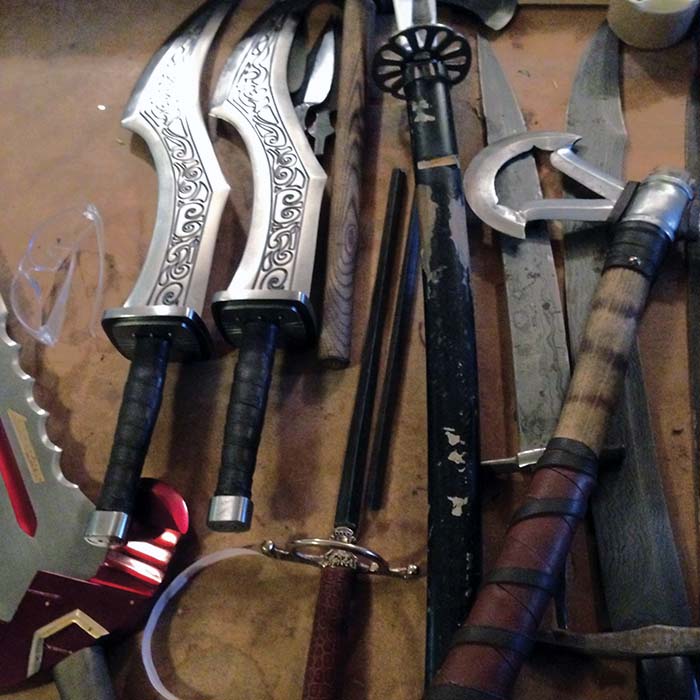
In 1790, Helenus Scott, a physician for the East India Company in Bombay and regular correspondent to his friend Sir Joseph Banks, President of the British Royal society, sent Banks samples of Wootz steel. Banks subjected these samples to expert scientific examination and analysis. The Rajahs of India sent specimens of daggers and other weapons to the International Exhibition of 1851 and 1862 (remember, this is also the timeframe leading up to the American Civil War). Though the arms of the swords were beautifully decorated and jeweled, they were most highly prized for the unique quality of their steel.
The metallurgical analysis of the swords of the Sikhs were reported to “bear bending and crumpling, and yet be fine and sharp. There is a possibility of an abundance of ultrahard metallic carbides in the steel matrix precipitating out in bands.” While not fully understood at the time in today’s metallurgical terms, Wootz steel swords, especially Damascus blades, were renowned for their sharpness and toughness and so the Wootz steel making process was adopted in Europe. Steel manufactured in India’s Kutch district, Scotland’s Glasgow and England’s Sheffield, particularly enjoyed a worldwide reputation that remains today.
BKS can repeat this process. Forge welding is an art requiring extreme attention to detail and years of experience and the Stagmer brothers have perfected forge welding of large Damascus steel billets. For example, when making Viking-era guards and pommels, large billets are required. The alloys they most often forge together in the layering are 15N20, 1018 and 4130, because this exotic steel sandwich provides strength and durability along with artistically distinct color lines and difference in the layers.
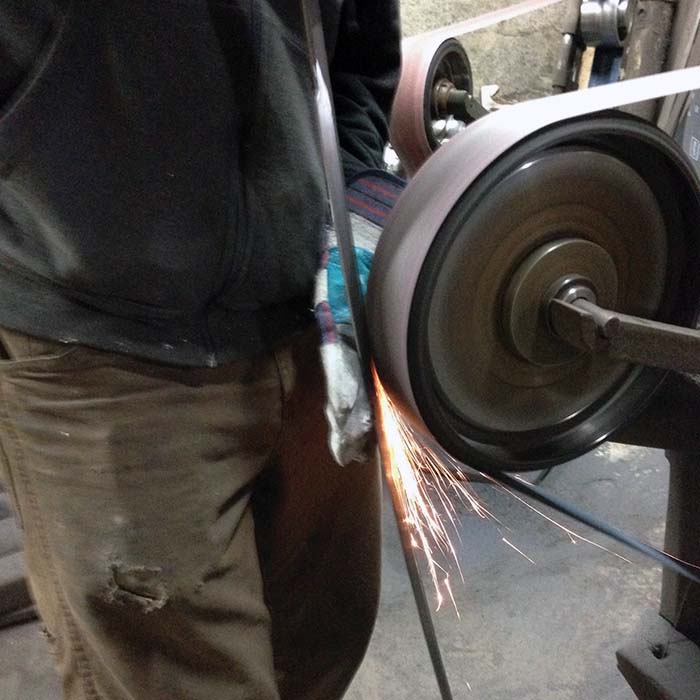
BKS achieves this by first cutting the different pieces of steel the same size. Then, the flat surfaces of all the pieces are sanded to eliminate scale and rust. Cleaning all the plates of the sandwich to bare metal also increases the metal-to-metal seam integrity of the forge-welded billet. As Matt says, “Why go through all the trouble of making a billet and not spend the few minutes clean-sanding the surfaces first to increase the odds of flawless bonding.”
To achieve their uniquely beautiful lines and color variations in the metal, BKS stacks the 1018 and 4130 pieces with 15N20 layered between every piece. 15N20 steel provides defined lines between the layers and acts as a great bonding layer to boot. BKS then arc welds the corners to keep the billet aligned during the forging process. They additionally weld a forging handle made from bar stock on the end of the billet to make it easier to work in the forge and under the hammer when it’s hot. “We tend to work rather large billets and the handle gives us more leverage,” Matt explains. “Once the billet is forged, the handle is cut off and its attachment point weld is sanded off leaving no trace.”
But back to the forging process. After the billet is prepped, the forge is fired. BKS uses an upright blown-foundry set up with an upper chamber made of firebrick. The BKS forge is heated using both propane and a waste oil burn. This duel-fuel forge both heats up fast and efficiently retains its heat, providing the optimum heat consistency necessary for forging exotic steel billets.
The billet is then placed in the forge and preheated until it starts turning a bit red which indicates a temperature of 800 to 900 degrees Fahrenheit. Then, flux is generously applied to prevent oxidation between the dissimilar metal layers and increase weld adhesion of the numerous layers. The billet is put back in the forge where it is turned one quarter turn every minute or so until its temperature reaches even welding temperature of 2,300 degrees Fahrenheit throughout the whole billet. After reaching welding temperature, indicated by a bright yellow color, it’s ready for the power hammer.
The pneumatic forging hammer BKS uses is an Iron Kiss 50 ton air hammer. That’s a 50-ton strike every time the hammer drops. Matt explains, “We use several different flat and drawing dies for welding and straightening. We take the billet by the handle and go straight to the flat dies and hit it hard and even.” After a number of evenly placed hits are made over the whole billet’s surface with the flat dies, the billet is often worked with the drawing dies to elongate it, but maintaining the correct weld forging temperature is critical throughout the entire hammering process.
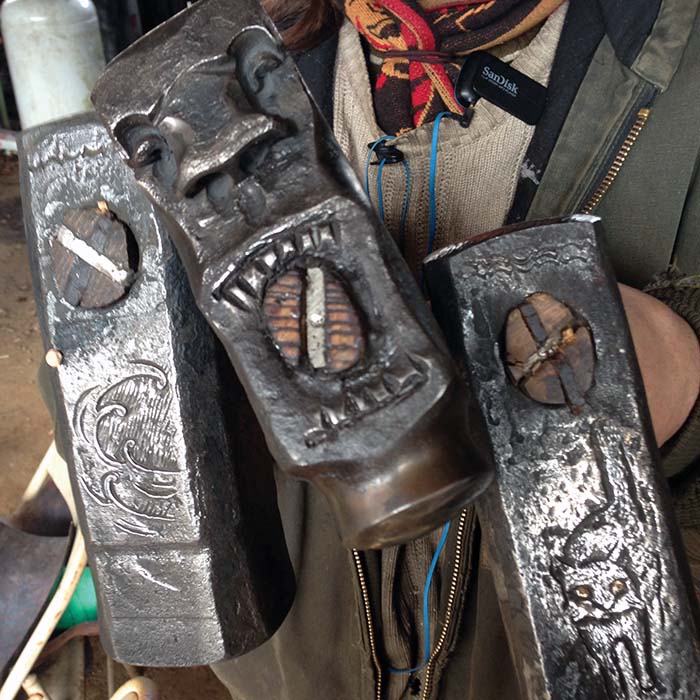
Great attention is paid to the hue of the billet’s heated color. As soon as the yellow fades the billet is wire brushed to remove scale. A copious amount of flux is reapplied and the billet is immediately placed back in the forge for a reheat to its bright glowing yellow color. According to BKS, the first two “heats” need to stay well in the yellow, while the flats are hammered to ensure all the metal layers are solidly welded together. Matt warns, “Only after the second time on the hammer is it safe to turn the billet on its side and true the sides. If you don’t get solid welds between the layers first, trueing it on the sides will separate the layers.”
Once the billet’s multiple layers are solidly welded, there are numerous patterns that can be achieved by further working the metal prior to actually forging the sword. For example, the billet can be forged out (stretched) and elongated which widens the layered lines. It can be folded and rewelded to double the layers, creating beautifully complex lines in the sword metal. Or the billet can be hammered into a semi-round shape and twisted to achieve a particular artistic pattern in the steel. Better still; the sword maker can use a mix of several of these techniques to create a metal pattern so completely unique that it could never be copied. The imagination of the sword maker is the only limiting factor and BKS has no shortage of imagination.
There are a number of additional factors that the sword maker must pay close attention to in order to reduce the risk of ruining the billet during the forging process. Failing to normalize (anneal) the elongated billet before heat-treating it is one of them. When making a large twisted Damascus blade for example, the metal must be properly normalized early on during the sword making process or the blade can untwist during the quench.
Normalization is a metallurgical process involving heating, cooling and quenching that relieves stress between the dissimilar metal welds. As previously described, the metal forge welding process involves three different alloys that are bonded into a single billet. The resulting stress inherent throughout the billet from the differences in the dissimilar expansion coefficients of these metals in the bonded “sandwich” is enormous. In order to relieve that stress and prevent delamination the billet is normalized.
Secondly, working the elongated billet into sword dimensions requires that the sword blank be as close to even thickness as possible. BKS runs it through their rolling mill to get its thickness as perfectly even as they can before actually shaping the sword. Again, maintaining the exact forging and rolling temperature is critical. Even the time of day is important to ensuring perfection. Matt, for example, prefers to forge weld in darkness because he can better see the heat colors glow and fade and maintain them at optimal temperatures to best work the steel.
BKS also hand forges complete custom-fitted suits of armor. Each piece is pounded out and fitted around a body cast (in lieu of the person having to be present for continuous fittings) of the person who will be wearing it. This tedious process of hammering metal sheets into perfectly fitted full armor suits is as unique as making the Damascus steel swords described previously, and it requires just as much metallurgical knowledge and craftsmanship. From shaping, annealing, fitting and tempering to decorative stamping, riveting leather hinges and assembly, this expensive process takes many weeks to complete a single armor suit and it’s all made by hand using a hammer and various shaped anvils.
So why, you might ask, would anyone today want a functional custom-made suit of armor and be willing to pay thousands of dollars for it? The answer is simple. There are organizations that compete against one another as knights once did, both on horseback and on ground, and they use real edged weapons that require a suit of real armor to protect the combatants. The only thing they don’t do is battle to death. Otherwise, it’s the real thing fought with real weapons. And yes, they occasionally lose a finger or two during the battle to an opponent’s misplaced strike.
BKS also makes other swords, knives and edged weapons that are both custom designs and production, with repeatable shapes that are plasma cut from sheets of steel, but nevertheless forged for strength and durability. While still the real deal, these knives, swords, axes, spears, etc. are primarily made for Hollywood stage use and are not sharpened to a razor’s edge for obvious safety purposes.
The Stagmer brothers are sincerely gracious men but BKS is not open for public tours so don’t bother trying. They do have a website and it’s worthy of your review, but otherwise they’re too busy forging works of art for a niche market to worry about public relations. It is probably fair to say BKS exists because they do. And they truly do produce unique edged weapons along with the armor to protect the combatant.
This article first appeared in Small Arms Review V20N5 (June 2016) |